With contributions from the Fraunhofer Additive Manufacturing Alliance, IPC & nScrypt
Contrary to what people conventionally think, Research & Development (R&D) is a very manageable driver of corporate success. If you think for a second, the biggest innovations that are shaking the world of today started with R&D. This stage has been fundamental in any industrial revolution, including additive manufacturing (AM), and today, we want to discover how this technology is driving this sector.
The manufacturer’s ability to innovate and adapt to its customers’ requirements has never been important as it is today. To respond to these industry needs, many manufacturers find themselves investing in their research, design and test capabilities. Manufacturing therefore has to be flexible and with the advancements in additive manufacturing and other technologies, we observe a shift in the paradigm of the R&D industry.
Indeed, the advancements in additive manufacturing and its increasing use in R&D might raise confusion since it is now difficult to perceive if AM drives the R&D industry or if the R&D drives the AM technology advancements.
For Kenneth Church, CEO of nScrypt, the answer is both. “AM is maturing but there is still so much more to learn, to improve and to transition. R&D is the beginning of all great technology but the difference here is that AM provides so many new beginnings. AM is and will make such a broad impact, it is hard to put it into one single category.
Church reminds that AM is not a new technology. The technology has been introduced in the 1980s. Many have proposed reasons why AM has grown so rapidly a number of years ago, but the main one would be tied to patents expiring and enhanced 3D software. The more people can use a software, the more they leverage 3D printing. Speaking of their experience, Church said they were using AM in 1999 on electronics. They printed capacitors using multi-materials and a layer by layer approach.
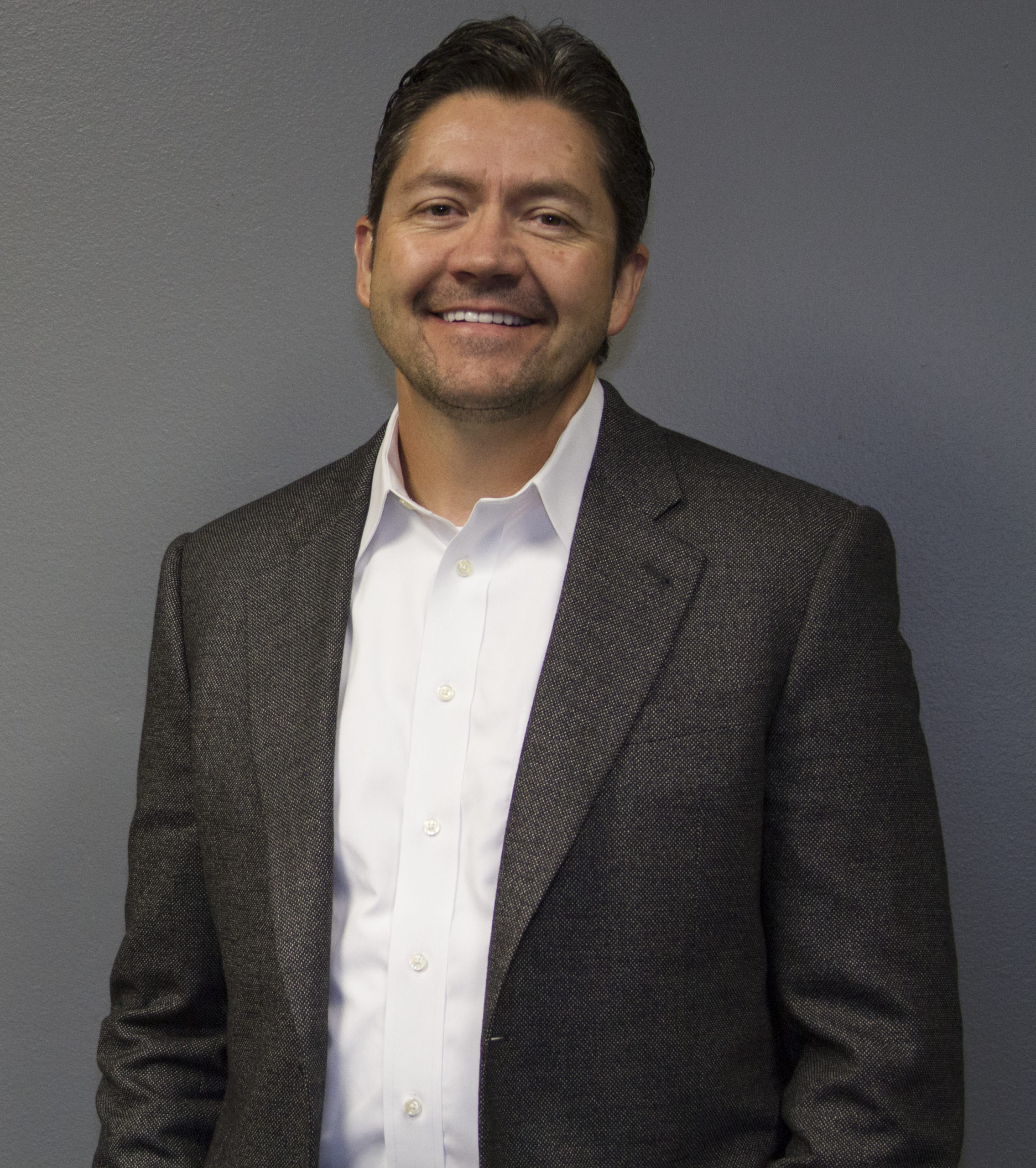
“AM will also and has already, flipped the tables and will change the R&D community. Many look at AM as simple 3D objects or even complex 3D objects that you cannot fabricate any other way, but what most are missing is the intrinsic value that comes from the complex shapes or the melding of materials. Metamaterials [for instance], have been a big buzzword for many years but achieving certain metamaterial designs has been out of reach due to the complexity of the physical object. If you could fabricate the complex metamaterial object, you could discover new electrical, magnetic and even thermal properties that are not possible with material alone.”
What’s that shift in the paradigm of the R&D industry?
R&D may be a crucial means for achieving future growth and maintaining a product in the market but it is a misconception that it is the domain of high-tech technology firms or even pharmaceutical companies.
The truth is, where most other firms may only spend less than 5% of their revenue on research, industries such as pharmaceutical, software or high technology products like additive manufacturing systems, need to attribute a more significant percentage due to the nature of their products. The paradigm appears therefore in the way this R&D activity is led.
Reducing lead times
It does not look like it is but the more we advance; the less R&D projects take time. R&D projects are recognized for their long-term commitment/investment. However, it should be noted that the use of new technologies might reduce the research time in a given project, while opening the door to a more tailor-made solution.
Additive Manufacturing for instance, is known as a technology that enables to reduce lead times.
Companies within the medical device sector for example, invest more and more in 3D printing technology, with industry leaders like Stryker announcing plans to invest €200 million in research, development and innovation at its Cork site. Such an investment in R&D would enable the medical company to produce customized 3D printed implants which can be used where a patient requires a more specific reconstruction, and where off-the-shelf product wouldn’t be suitable.
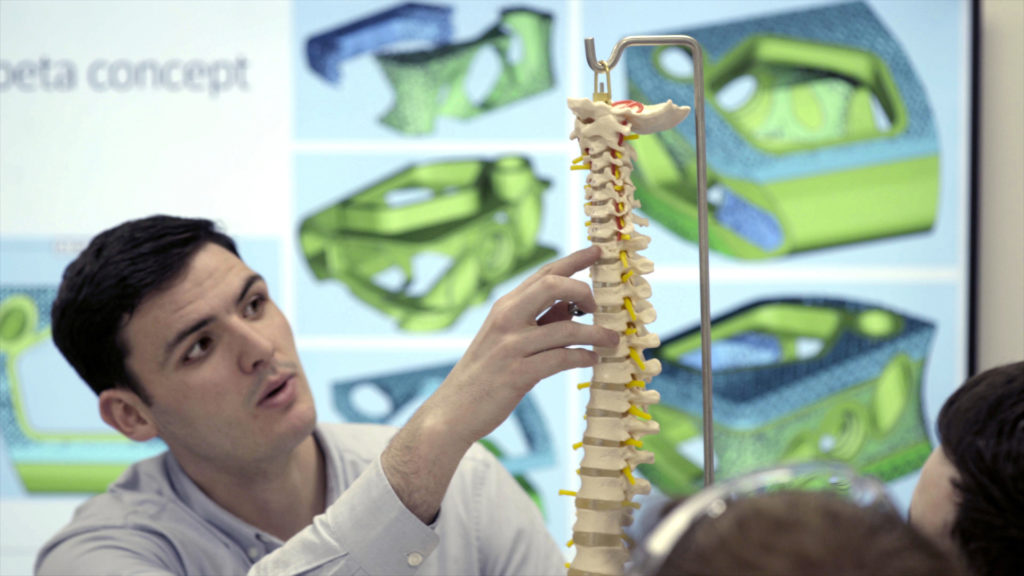
However, despite the benefits announced by this innovation (benefits of bone growth with 3D printed implants), the limitations remain a big hurdle in the adoption of new spinal implants, as the extensive cost of the equipment does not enable yet a majority of people to afford the products made with it.
Proliferation of R&D activities in private sectors
Another interesting observation is that, unlike in the past where R&D was mostly part of the public sphere, private sectors increasingly leverage R&D expertise. However, in this specific case, the R&D activity of industrial projects has recently been restructured with the goal of providing short-term benefits.
According to Dr. Bernhard Mueller, “AM is well-researched in manifold ways and R&D activities have globally exploded. The biggest challenge is to bridge the gap to industrial application, generating more business cases. Only few business cases have so far been proven and industrialized (hip cup implants 3D metal printed via EBM technology, repair of gas turbine burner tips via L-PBF metal AM technology, dental caps via L-PBF metal AM technology, aerospace ducts and hoses via polymer AM).”
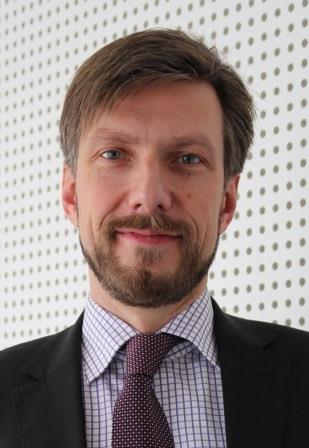
For instance, most of the launches that have recently been made in the additive manufacturing industry are the result of in-house R&D activities of companies.
Dr. Bernhard Mueller affirms for instance, that they use all relevant AM technologies (laser or other beam-based technology, powder bed as well as material deposition, binder jetting, bioprinting etc.) and process all types of materials (metals, polymers, ceramics, biomaterials). “Major applications have been successfully investigated at Fraunhofer including prove of industrial applicability, e.g. AM tooling for hot metal processing technologies, functionally integrated medical implants, several flying parts in aerospace developed at Fraunhofer jointly with industrial aerospace partners” Mueller continues.
To mention other examples, the recent 3D printers that have been launched on the market are the result of extensive R&D activities: HP 5210, XJET Carmel 1400, the 3DGence Industry F420, the da Vinci Color 5D 3D Printer, to name a few of them.
In industries such as the automotive, one can mention the increasing use of additive manufacturing for prototyping parts. Two years ago, car manufacturer Volkswagen sets the goal to fabricate a 3D printed car. To do so, it opened a 3D printing centre in its Toolmaking unit in Wolfsburg. While leveraging several metal AM technologies, the automotive specialist plans to produce complex vehicle components both for prototyping and series production.
“The 3D printing centre takes VW’s additive manufacturing activities to a new level,” Dr. Andreas Tostmann, Volkswagen brand production chief, commented during the opening ceremony. “In two to three years’ time, [3D] printing will also become interesting for the first production parts. In the future, we may be able to use 3D printers directly on the production line for vehicle production.”
The opening of this center brings the company’s activities in AM to a new level. Indeed, the car manufacturer already customizes components such as key rings and exterior-mounted name plates. Using HP’s binder jetting, it will be able to produce quality functional parts with significant structural requirements.

Collaborations, the must?
No matter what anybody says, R&D activities require investments that companies cannot always afford, which is why collaborations often remain a viable alternative. Several types of collaborations therefore exist, collaborations between R&D centres and AM companies, collaborations between companies and universities, or even collaborations between R&D centres.
One interesting form of collaborations that has recently been implemented in order to help SMEs to accelerate the product development of their products onto a given market while leveraging AM is AMable. It is actually a European project whose aim is to foster the development of AM by SMEs. Funded by the European Union’s horizon 2020 Research and Innovation Program, the project aims to support companies in the adoption of AM technologies.
In order to better serve SMEs, the network brings together the main technology centres located across the EU, and supports them in the development of their ideas: from the concept stage, the construct and print stages to post-production phases.
The increasing use of AM as a R&D tool
Beyond this shift of paradigm in the R&D industry, it is interesting to appreciate how exactly AM is used as a tool in R&D. Indeed, while the novelty of a solution may lead to the dismissal of the oldest one, it should be noted that in the R&D sector, the technology remains a tool among other tools.
Nathalie MAILLOL, Additive manufacturing project leader at IPC, comments: “AM is a complementary tool [alongside] other production processes, not a substitute. I think AM changes the R&D industry as people begin to think [of it] as [a] process with a lot of potential, not only a [prototyping tool].”
Indeed, when we look at R&D centres be it private or public, AM is rarely the only technology that is leveraged.
nScrypt for instance, does have traditional machining and electrical prototyping. According to Kenneth Church, these provide fundamental value in research, but to progress to new concepts, [they] have moved to the nScrypt 3Dn Direct Digital Manufacturing tool which has printing, machining, printed electronics and pick and place in a single tool. nScrypt has coined this the Factory in a Tool (FiT). “From this we can fabricate monolithic circuits such as an Active Phase Array Antenna where the active electronics are part of the antenna element”, said the CEO.
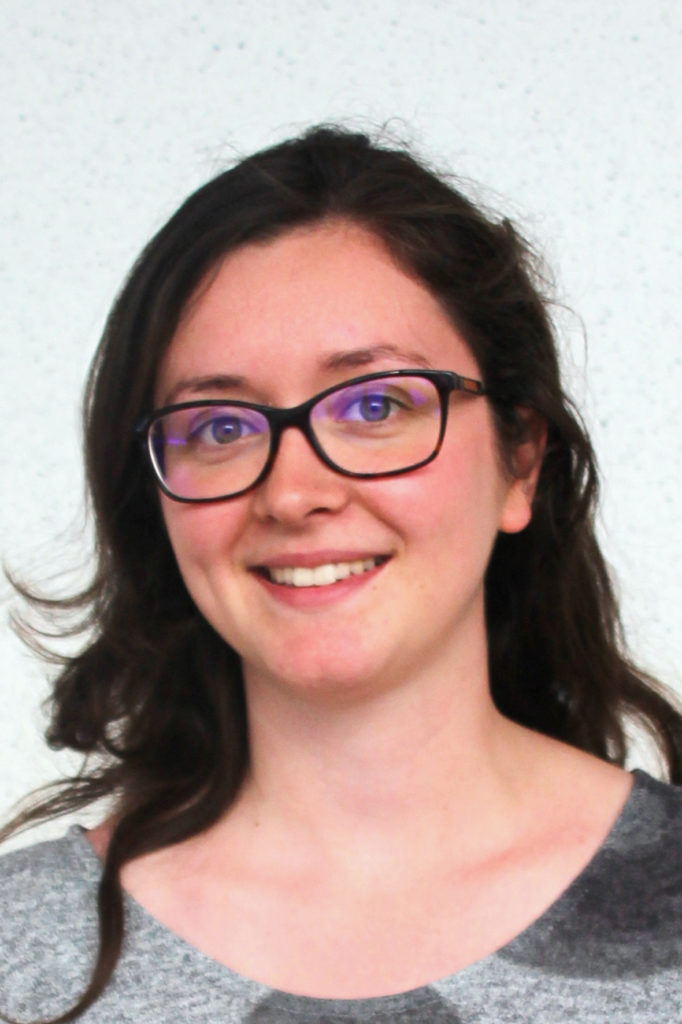
Maillol explained that, from its early beginning, the centre mainly focused on plastic injection. “In 2001, IPC began to work on laser powder bed fusion in order to build mould insert with cooling channels. These channels have a complex geometry that can [only be produced using an] AM process.” This experience has led the AM team to explore the possibilities offered by other types of AM technologies in R&D projects. Today, in addition to metal AM technology, their portfolio includes SLA and different types of FDM 3D Printers (among which large format printers, PEEK or composites-based 3D printers).
Those 3D printers might be a great tool but sometimes, their capabilities need to be enhanced in order to obtain expected results, to reduce costs or simply save time.
“We work with different machine providers to develop exposure parameters or to study powder recyclability. Recently, thanks to a European project, we could have equipped one of our machines, EOS M290, with monitoring systems: OT (Optical Tomography) and MPM (MeltPool Monitoring). They are in-line systems, which means that they watch the production running and collect data to evaluate the quality of the process. The objective is to detect if the melting of a part presents a deviation (like porosity or lack of fusion) during the production. [Such type of] equipment gives a clear advantage as a quality tool and avoid post-production test such as X-ray tomography which is expensive and time consuming”, explained the AM project leader.
The use of AM as a R&D tool might therefore enable researchers to evaluate both the advantages and disadvantages of the technology, and in some cases leads to improvements.
For IPC’s spokesperson, depending on the goal of the research, AM fosters many other developments. These developments can for instance, be observed at the material or the parameters level. “The development of monitoring systems is on the way in order to reach the right first-time manufacturing. The common point is to reduce the cost for parts produced with AM process. So, I expect more projects to investigate if AM is suitable for serial production and I also expect more development to improve the success ratio of AM productions,” concludes Maillol.
The specific use of AM in medical research
When it comes to research, 3D printing is widely used in medical-dedicated researches and several purposes explain the use of the technology: the generation of accurate replicas of a body part, reconstruction and plastic surgeries, customized implants as mentioned earlier. “R&D in AM will continue to increase, providing more and more technological breakthrough developments in terms of cost, multi-material AM, reliable ultra-light-weight structures, process reliability, application-specific technology portfolio widening etc.” said the spokesperson from the Fraunhofer Additive Manufacturing Alliance.
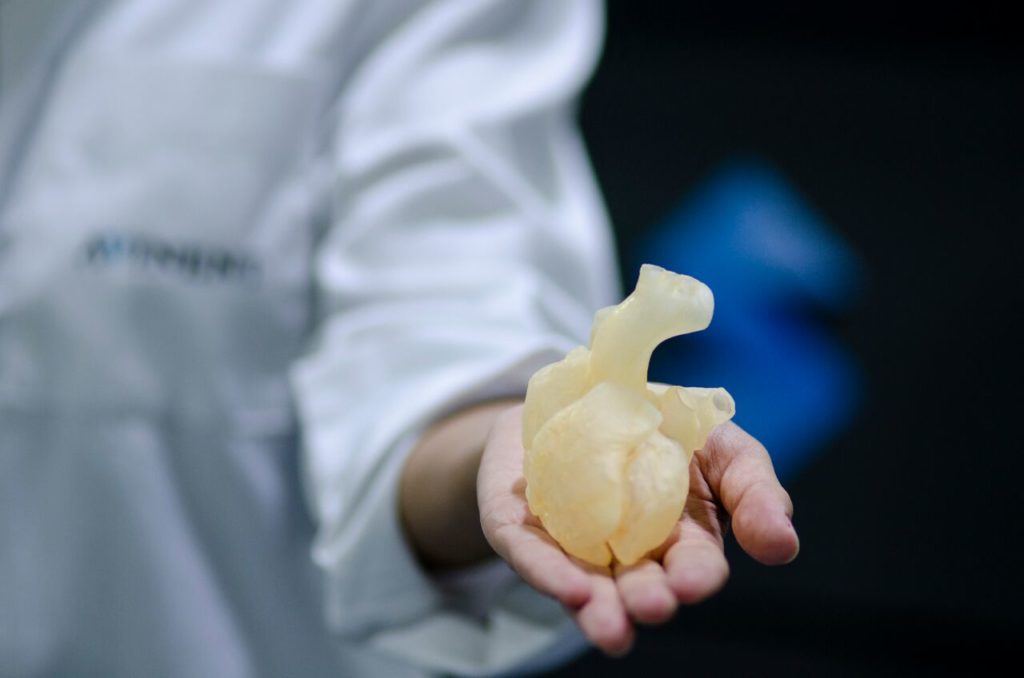
Interestingly, the advancements of the technology have led to the development of a new one: 3D bioprinting. Built on recent advances in 3D printing techniques, this manufacturing process aims to engineer different types of products involving biological components, including human tissue and, more recently, vaccines.
While the concept of bioprinting is not entirely a new one, the increasing advancements in the field raise legal and regulatory questions regarding their effective use on humans.
In a nutshell
Our paper demonstrates that Additive Manufacturing also has a disruptive effect in the R&D industry:
At a structural level, the technology allows the creation of dedicated R&D centres committed to exploring the advancements of the technology, the proliferation of R&D centres in private sectors and a wider collaboration between companies, universities and R&D institutes.
At the internal level, the technology remains a R&D tool used alongside other manufacturing processes, which is a good thing as, the more researchers will depict the areas for improvement of the technology, the more manufacturers might be able to develop high performance machines.
We couldn’t agree more with Kenneth Church when he says: “the task in front of us is daunting, but it is not insurmountable and it is important. We need to continue to push the R&D in AM and this will drive R&D to a whole new place. R&D will be faster due to accessibility to fabricated prototypes with unique properties. AM will also disperse the R&D. Today, labs that have very expensive equipment get to have most of the fun. Tomorrow, your garage will be a lab and you will get to join the fun. Software will improve and what once was only for highly trained CAD users is now in your physical hand, your phone, you will create what highly trained CAD people might not have thought of.”
Last but not least, among all R&D sectors, vital sectors such as the medical industry remain a crucial focal point. Indeed, 3D Printing led to the development of new manufacturing techniques, techniques that might drastically change people’s lives but regulations are not yet ready to cope with this change. Nevertheless, it’s the job of R&D to convert requirements — from consumers, government and others — into specifications.