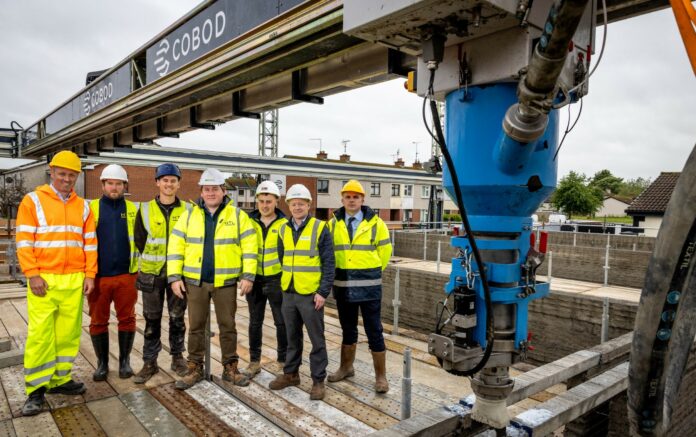
According to HTL, the Dundalk homes will be built three times faster than traditional methods, with completion expected by October.
During the past two weeks, construction company Harcourt Technologies Ltd (HTL) has been building Ireland’s first 3D printed homes. The homes are being built in Dundalk, the county town of County Louth, Ireland. So far, experts in Ireland had decided to fill the gap with the technology by first educating professionals on construction 3D printing.
Before starting the Dundalk project, HTL first built two test houses at their R&D facility in Drogheda. Using a gantry-mounted 3D concrete printer from COBOD, experts from HTL observed how it follows a digital blueprint, and extrudes concrete to create cavity walls without the need for traditional concrete blocks.
“It’s like building a concrete block wall, but the machine lays 50mm layers instead of manual placement,” explained Justin Kinsella, Managing Director of Harcourt Technologies (HTL). “As architects and engineers, we design the building digitally, and the model guides the printer to extrude the material layer by layer,” he said.
As far as labor is concerned, it is “reduced by about a third, and construction speed is tripled compared to manual methods. Overall, the construction process is 25-30% faster, and we expect further optimizations,” Kinsella added.
Currently, it takes the 3D printer about 18 minutes to lay a 50mm layer of concrete around the three-unit block in Dundalk, with hopes to reduce this to 12 minutes next week.
In terms of cost, this method is comparable to traditional concrete block construction. “The real cost benefit lies in the speed of delivery. Costs can drop significantly if construction time is reduced by 25-30%,” Kinsella stated.
With housing remaining the company’s primary focus, training is being offered to prepare for a wider adoption of construction 3D printing.
Remember, you can post job opportunities in the AM Industry on 3D ADEPT Media free of charge or look for a job via our job board. Make sure to follow us on our social networks and subscribe to our weekly newsletter : Facebook, Twitter, LinkedIn & Instagram! If you want to be featured in the next issue of our digital magazine or if you hear a story that needs to be heard, make sure to send it to contact@3dadept.com