Ageing installations are a common issue in many industries. Assets are increasingly used beyond their original design life, which results in parts becoming high-risk for downtime or failure. This can result in significant non-productive time which could cost upwards of hundreds of thousands of euros. Maintaining the integrity of equipment is difficult given that like-for-like replacements of parts are no longer available due to obsolescence of the equipment model or changes in engineering standards.
A few solutions to these issues may come down to envision the (re)design of obsolete parts, the ability to manufacture parts-on-demand to alleviate costs and have a better control of the supply chain and on top of that to leverage an eco-friendly manufacturing process, all of which can be provided by an additive manufacturing service bureau.
As explained in this article on “The Importance of Choosing a Metal Additive Manufacturing Service Provider”, working with a solutions provider must go beyond the “value for money” criterion. It requires to choose a partner that can keep industrial assets operational by overcoming the pain points in today’s supply chain, something Guaranteed has built up expertise in. Headquartered in Belgium, the metal AM service provider can achieve this by producing spare parts on-demand, reproducing obsolete parts, refurbishing damaged components or optimizing existing ones.
“Our unique facilities allow us to provide extra-large scale metal wire and arc (WAAM) additive manufacturing services for customers all around the world. We at Guaranteed, want to contribute to the creation of a more eco-friendly manufacturing future, in which we are recognized for the quality of our service and the innovative spirit of our people. Today, we operate a WAAM manufacturing facility capable of producing parts up to 10 x 6 x 5 meters and weighing up to 20 tons in a broad variety of metals ranging from carbon steels, to stainless steel, Ni-based alloys, titanium and aluminum – to name a few.
Guaranteed’s WAAM services allow such parts to be reproduced at an affordable cost, even for small series, repaired or refurbished. In the latter case, the original part design or material selection is given an upgrade which allows the refurbished part to have an increased performance or life-time as compared to the original OEM part.
For very large parts or failures occurring in remote areas, the costs and logistics involved in dismantling and transporting the damaged part might become prohibitive. To resolve this issue, Guaranteed can propose a “mobile WAAM additive repair service” which allows on-site or even in-situ repair or remanufacturing”, the company notes.
Why the focus on WAAM?
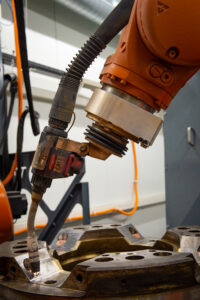
Driven by the demand for increased manufacturing efficiency of engineering structures, Wire-Arc Additive Manufacturing, short for WAAM, which is also known as directed energy deposition-arc (DED-arc), can basically be seen as the integration of an “additive” principle in the wire-arc welding process.
Acknowledged for its ability to produce large scale components, this versatile manufacturing process is often the route to go for manufacturers who are looking to achieve high deposition rate and high mechanical strength of the parts, lighter weight parts and less waste, faster prototype testing while reducing lead times from months to weeks. These advantages are often the most sought-after features across the oil & gas, maritime, steel, mining and aerospace industries – industries where Guaranteed creates value by reducing lead time, ensuring inventory optimization and improving lifetime extension or process performance.
“Our aim is to provide our customers with high quality parts, both on a geometrical and metallurgical level. Our high-quality manufacturing is enabled by data analysis and process monitoring to facilitate qualification and certification. Thanks to our industry leading dimensional capabilities Guaranteed is able to provide a fast, cost-competitive and sustainable alternative to casting or forging as well as hybrid combinations or functionally enhanced cast or forged parts. Our ambition is to grow both in geographical and technological footprint, but never at the cost of the quality of our products and services. Through a high reactivity, structured workflow and project follow-up, we strive to gain and maintain the trust of our customers”, the company states.
To back words with action, Guaranteed has achieved this year the industrialization of a pilot application in the steel industry together with steel producer ArcelorMittal Belgium – which is also one of the service provider’s shareholders. The company explains that they expect to have repetitively well deposited over 3000 individual features by the end of this year. This will demonstrate that WAAM can be a viable production candidate for medium to large series.
“Along the same line, we also notice that several other of our early customers are now ready to move into serial production requests this way successfully securing base-line orders from ArcelorMittal (repeat as well as repair) as well as from third party customers. Within that context, another important achievement this year was that we obtained together with our customer class approval from DNV for a hybrid WAAM produced critical component for use in the maritime industry. We demonstrated that WAAM can not only reduce lead time and costs, but can also significantly reduce material consumption and CO2 emissions. By the end of 2022 this concept will also be industrialized”, the company adds.
That being said, the company is also aware of the fact that, remaining on top of its league requires a continuous monitoring and improvement of one’s processes hence the integration of artificial intelligence (AI) and machine learning (ML) tools within the company’s production environment. Moving forward, to facilitate qualification and certification processes, the company will invest extra miles to advance process monitoring and process control in combination with these tools. A key focus will also be made on improving the manufacturing process (in particular the deposition speed and the ability to perform enhanced in-situ microstructure control during deposition), and on the implementation of guidelines and standards – the standard ISO9001 and the AM specific site certification.
In the meantime, visitors at Formnext could learn more about Guarantee’s expertise in Hall 12.1, D21 and discover fascinating use cases that will highlight several technical, economical and sustainability benefits.
This content has been written in collaboration with Guaranteed.
Remember, you can post job opportunities in the AM Industry on 3D ADEPT Media free of charge or look for a job via our job board. Make sure to follow us on our social networks and subscribe to our weekly newsletter : Facebook, Twitter, LinkedIn & Instagram ! If you want to be featured in the next issue of our digital magazine or if you hear a story that needs to be heard, make sure you send it to contact@3dadept.com