Solutions to industry challenges usually come from unexpected experiences. To eliminate the speed restriction of 25 km/h for electric bikes, Luigi Monaco came up with an ingenious idea: contactless chip tuning.
Developed by Monaco’s company, Badass eBikes, this solution consists in „a hack where a coil induces a magnetic field with which the sensor of the eBike motor is brought to believe that the actual speed is different – lower – than the real speed, [hence the elmination of] speed restriction“.
At the beginning, to manufacture this chip tuning device, Monaco used injection moulding but he rapidly turned to additive manufacturing as it enabled a total control over each production. Furthermore, mass producing these devices using injection moulding became difficult to handle as eBikes manufacturers started changing their sensors, to limit the sale of these chip tuning devices.
At the manufacturing level, choosing among the variety of AM technologies was not an easy task as each technology offers ist advantages and disadvantages for the fabrication of chip tuning devices.
„We compared all the different additive manufacturing methods and we immediately saw that everything requiring a support structure of any kind would not be feasible for our little casings, mainly because of surface finish and the added labour. SLA could have been interesting but a mechanical device fixed on an eBike that would have been exposed to sunlight – not to mention the rough environmental conditions – made it difficult to find available materials that could fit our requirements. So we went to powder based systems and then decided to produce in PA11 (mechanical, chemical properties) and black to save us even another production step (colouring)“, Monaco told us.
Once they began production with their powder-bed based machine, Monaco came to realize how much they struggled to achieve the post-processing steps that enabled them to have the desired finished 3D printed components. Those post-processing stages included depowdering, sand blasting and powder mixing, to name a few of them.
„It had been 8 hard months of 3 time a week 4,5 hours of depowdering, sand blasting, powder mixing etc.“, he recalled. But he was also a reflection time as he was determined to find a solution that would have facilitated these important, time-consuming yet underestimated steps. These are times that led to the creation of PULVERMEISTER.
The people behind PULVERMEIRSTER
Truly self-taught, he mostly learned by himsled what he knows about IT and mechanical engineering. He is backed in the management and development of PULVERMEISTER, by his cofounder & friend Harald Schreck. Schreck is also the founder of a company, Schreck GmbH & Co. KG, that produces machines for the automotive industry.
„The speciality of Schreck is high precision, where the standard deviation in producing parts is 5/1000mm. Him and I we grew up together and when Badass had to place a laser sintering machine with compressor and blasting machinery I asked if he would have some space available. He had, we installed the machines there and he saw the problem. When I asked him if we can finally end this powder pooling malaise he gladly agreed. PULVERMEISTER was born“, Monaco enthused.
PULVERMEISTER: specifications and functioning
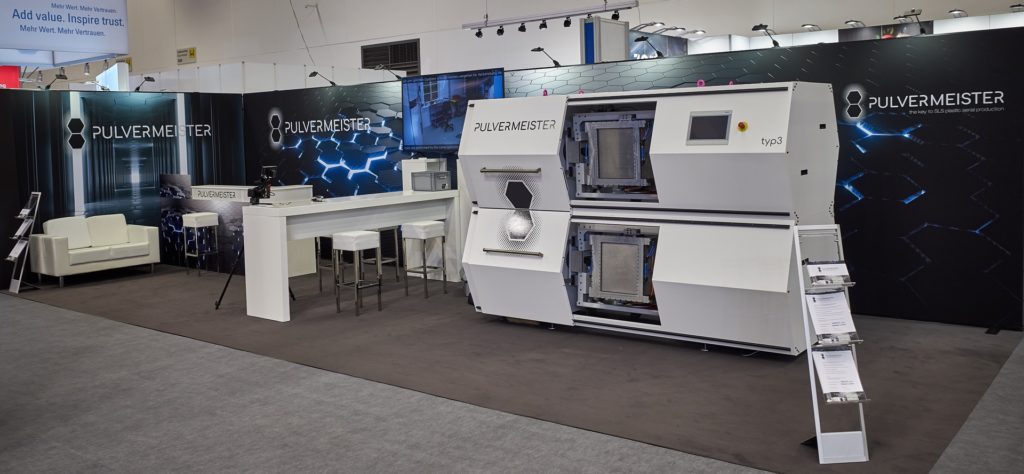
At Formnext 2018, they officially unveiled the first prototype of the 3D print post-processing device that they have been improving during the past two years.
A YouTube Video of the first prototype shows the rapid process of the depowdering machine. In approximately 10 minutes, the upper chamber slowly rotates in different directions and shakes any powder. Removed powder flows back to a recovery bin, but is not exposed during the process.
„We depowder in an air tight under pressure compartment with tumbling and an air jet. The under pressure guarantees that the powder is transported in the storage container. Handover to the second compartment is done by bringing the doors of the containers to each other, opening them and then the parts fall from the upper compartment to the lower one. In there blasting is done. Basically the same device as the upper one, to save cost and to have a modular and reliable – tested – system. Handover is contamination free, the used powder can be taken out of the storage container for refreshing and usage“ Monaco explained, speaking of the post-printing process.
Today, the latest machine of the Germany-based startup is an automated depowdering and blasting solution, designed for every industrial production of bulk plastic parts – in a nutshell, every bulk part that survives a 1 meter drop – . Monaco can pride himself on having Badass eBikes, a company that has become a real proof-of-concept of what is possible to achieve with Additive Manufacturing and PULVERMEISTER‘s depowdering system.
„The growth of Badass eBikes as an international market leader in this brief time would never ever have been possible without AM“, he told us.
Recently there have been some developments in the post-printing space, as the number of companies using industrial AM – and powder-based solutions especially – continues to rise due to price drops and demand. This has created a greater need to automate the traditional manual post-processing steps, and PULVERMEISTER is part of those companies that are willing to bridge this gap.
This interview was originally published in the September-October issue of 3D ADEPT Mag.
Remember, you can post AM job opportunities for free on 3D ADEPT Media or look for a job via our job board. Make sure to follow us on our social networks and subscribe to our weekly newsletter: Facebook, Twitter, LinkedIn & Instagram! If you want to be featured in the next issue of our digital magazine or if you hear a story that needs to be heard, make sure to send it to contact@3dadept.com