With over 2 100 employees and a worldwide presence, CHIRON Group is mostly acknowledged for its CNC equipment and automation expertise in the metalworking industry. Given that expertise and background in the metalworking field, it is not a surprise to see the multinational company debut on the additive manufacturing industry with the launch of a metal 3D printer.
However, what draws attention is the type of metal 3D printing technology the company develops and its latest project dedicated to the automotive industry. In this Opinion of the Week, we sat down with Axel Boi, Head of Additive Manufacturing CHIRON Group to discover what to expect from the company within the AM industry.
Adding one string to its bow
Boi has been working for CHIRON for two decades. Aerospace engineer by trade, he held several positions within the company prior to his current role.
“The AM Team is a start-up within the CHIRON Group”, he said from the outset, which enables the team to work with flexibility on the one side & know-how from CHIRON on the other side.
The idea of an AM unit started five years ago. As a machine tool builder, it was important for the CHIRON team to assess the 3D printing market and their chances to penetrate and provide third-party industries with their services.
“We quickly realized that the additive manufacturing market was a dynamic one. However, to debut on such a market, you need to ensure a proof-of-concept of your solution. Most importantly, as a high-tech company, it is crucial to invest extra miles to position as a leader in its field. That was our goal, and to achieve it, our biggest strength was to rely on an existing expertise, hence our choice for the production of metal 3D printed parts”, Boi explained.
2018 therefore saw the launch of the CHIRON Group AM-strategy. The team’s first steps in the AM industry consisted in the production of polymer parts followed by the development of the AM cube in 2019.
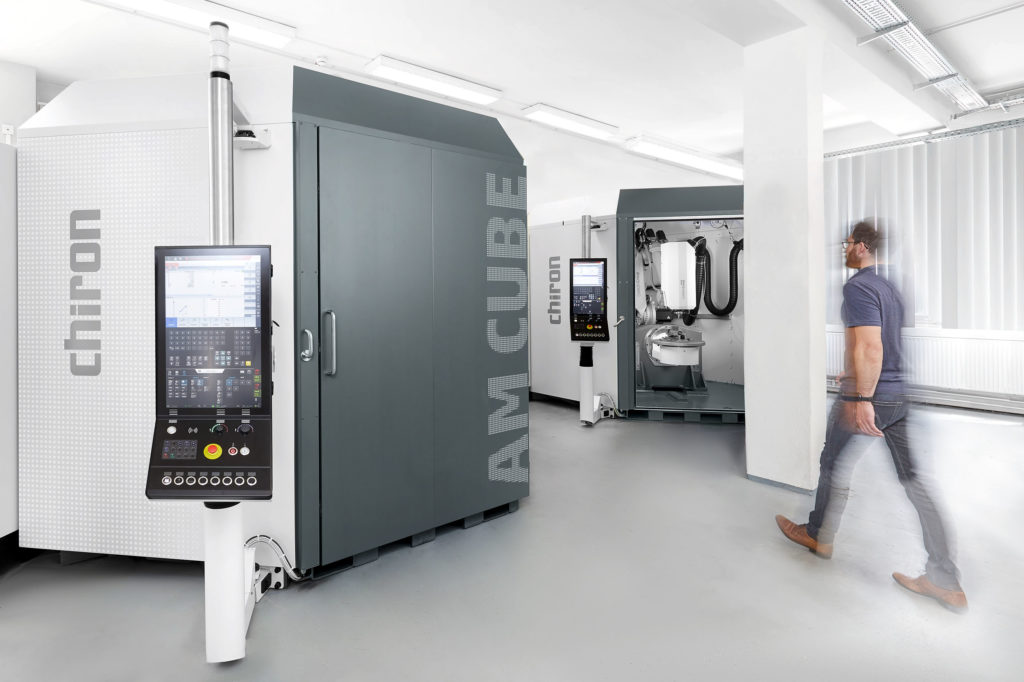
“Today, we implemented a SAP process, allowing designers to use 3D printed semi-finished products in their development process”, the Head of AM CHIRON Group added.
Combining two deposition materials technologies into the AM Cube
With the AM Cube, the CHIRON Group has developed a new form of metal 3D printing technology laser metal deposition welding that combines wire and powder. What makes the AM system stands out from the crowd is that, unlike other industrial 3D printers, the deposition head of the machine can be changed during the additive manufacturing or coating process.
“This means that different materials can be printed (or coated) automatically during the same print job and different print strategies can be applied with the different print heads – for instance, high volume with one deposition head, and good surface quality with the other deposition head”, Boi outlined.
According to the manufacturer’s representative, there has been a bunch of nice developments launched on the AM market, but they do not always focus on challenges encountered during industrial operations. “The customer is looking for an industrial solution on the shop floor, a solution that will maximize uptime and require less repair and maintenance issues”, the representative said while elaborating on what they bring into the development of the AM-Cube.
Needless to remind the increasing importance of data-driven workflow tools for additive manufacturing. If emphasis has not been made on the software tools that enable connectivity across the AM workflow during our conversation, it should be noted that the machine’s capabilities allow for smooth visualization and assessment of parts data.
So far, CHIRON held an Open House to show a select number of prospects the capabilities of the machine. While the manufacturer will provide further feedback on the AM-Cube at the end of a pilot program that is currently in progress at a customer’s facility, Boi revealed an increasing interest from three target groups: those who know welding wire, those who use coating and researchers. Indeed, although researchers would be interested in improving product quality with the machine, the first two groups of prospects are interested in a more automated manufacturing process and the flexibility of the tool head change.
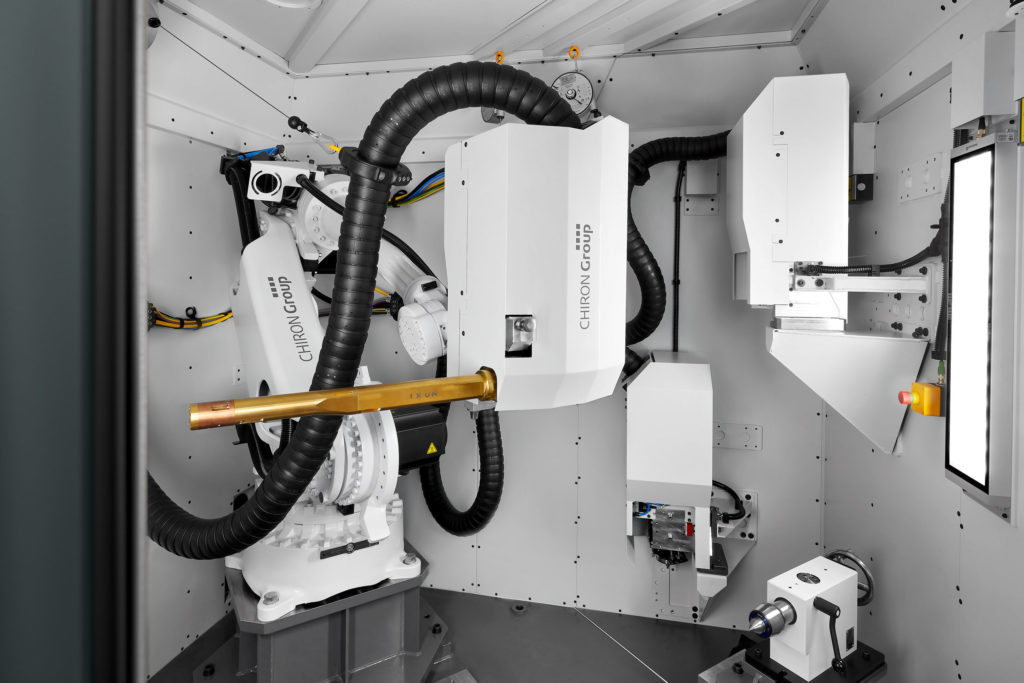
The AM Coating project
During the recent Formnext Connect event, the Germany-based manufacturer has also revealed more about its latest project: a system for coating brake discs. Brake discs, more than other automotive components, are often subject to repeated mechanical loads, hence the fine particulate matter they produce. To protect them, and to a certain extent, to address the substantial environmental issue they raise, the AM team at CHIRON has been working on a solution that will help reduce corrosion and fine dust on brake discs. The solution will therefore measure fine dusts; can be much faster than any conventional manufacturing process available on the market and could better improve brake discs’ protection.
The AM Coating solution could be used as a system for developing process parameters or for series production.
Concluding notes
Despite these challenging times, the AM start-up within CHIRON can pride itself on relying on industry go-to-market capabilities of its parent company to debut on this market. Furthermore, unlike manufacturers that bet on the most-widely used metal AM technology to launch their activities, the company has developed a unique technology that can bring unparalleled advantages in terms of applications, compared to other metal AM processes. Add to that the company’s AM coating solution, these are already two outstanding reasons that deserve the interest of industrials.
Remember, you can post free of charge job opportunities in the AM Industry on 3D ADEPT Media or look for a job via our job board. Make sure to follow us on our social networks and subscribe to our weekly newsletter : Facebook, Twitter, LinkedIn & Instagram ! If you want to be featured in the next issue of our digital magazine or if you hear a story that needs to be heard, make sure to send it to contact@3dadept.com