“Making casting using 3D printed molds.”
It’s probably very cultural but I grew up in an environment where I was taught that our parents are always right – especially moms. They simply know best. Imagine my surprise when at Formnext 2023 I stumbled upon Foundry Lab, a company that was bold enough to state loud and clear “Mom was wrong”. Of course, I had to stop by their booth to tell them they were wrong to state such a thing – no matter what their reason was; but I needed to understand first what led to such a bold statement. It took me a few months and a recent conversation with founder and CEO David Moodie.
We may have discovered Foundry Lab last year when it debuted on the European scene but the company was founded in 2018. It turned out that Moodie was running a design consultancy before founding his company and he was frustrated with their ability to only prototype plastic parts and not metal castings.
“My clients were falling through this huge gap in manufacturing – die-castings are impossible to prototype. I got frustrated with the inability to test our designs in the production material – so I decided to fix the issue myself!”, he said.
It looks simple but it’s truly not. If I was seduced by their marketing tactic, the more I read about them, the more I found subject to debate.
What does Foundry Lab do?
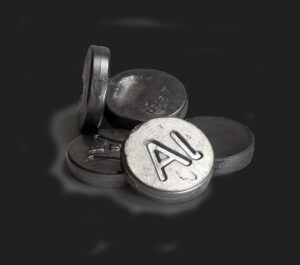
Simply put, the company headquartered in New Zealand leverages the strengths of traditional casting and combines it with Additive Manufacturing and microwave technology to produce metal parts.
If my understanding is correct, the company’s strategic thinking is based on a harsh truth: it’s difficult – sometimes impossible to 3D print a casting. Most importantly, the latter should not be confused with a metal part as there are two different things.
To fill that gap between casting and 3D printing, the team has developed a solution called “Digital Metal Casting”.
Moodie explains how the solution works: “We approach casting a little differently – we 3D print molds in a ceramic powder, insert a slug of metal into the mold and then heat the mold. The slug melts and fills the cavity. The outcome is a casting with the same alloy and geometry as your production casting.”
The controversy might arise when Foundry Lab said “Stop printing prototypes”. Something that the founder clarifies: “Essentially we were saying that “If your parts will be cast in production – they should be cast in prototype.” Printed metal parts share the same color as a casting but that’s about it. You cannot get the data you need from a print.”
How does it work?
Well, the first explanation I received from Hester Tingey (the company’s marketing manager) at Formnext reveals a four-step process that includes: a 3D printer based on binder jetting, a depowdering station, and a microwave furnace – all of this working with a dedicated software solution; all supplied by Foundry lab.
The 3D printer fabricates a tooling in a proprietary ceramic using a proprietary binding agent. That part undergoes a microwave curing process before going to depowdering.
The metal casting process is carried out without the need to pour molten metal. Solid metal, either in the form of a disc-shaped medallion from Foundry Lab or any other solid piece, is placed into the mold, which has a reservoir to hold this raw material. The microwave furnace doesn’t directly melt the metal; instead, it heats the ceramic mold to a temperature that melts the metal. The molten metal flows into the mold, solidifies into a cast part, and then requires the removal of excess material, such as flash, just like any other casting.
The entire process yields 5 main benefits that Moodie lists below:
- Production quality castings without any casting knowledge.
We recognized that the market for casting in the US/EU is booming but foundries are still closing down. The issue is that we have lost the workforce with the technical knowledge to work in the foundry. Foundry Lab’s goal is to digitize casting – to allow an untrained operator to achieve quality castings. - Safety: The mold goes into the furnace cold and comes back out cold. This is hands-off casting. Think of a paradigm shift from a dark foundry with fire and smoke to a clean room environment
- Any geometry: By digitizing the mold making (3D printing) we have complete geometric freedom. The way we cast also allows thin wall – so, essentially we can achieve anything that die-casting could have done – without the pressure, steel molds or casting experts.
- Speed: The system can turn around a part in under 24 hours. Castings tomorrow. (Compared with the 6-18 months that the industry is currently dealing with)
- Cost: This is a complicated one – this system is orders of magnitude cheaper than casting for short runs. There is a crossover when you get into higher quantities. But the initial outlay on tooling is what stops prototype/short-run castings in the first place.
Speaking of areas that could be improved in this process, the founder mentions bigger sizes and higher temperature alloys – both of which are being improved by the company.


Key applications
“We have parts on cars, on the road already! The reason is that the parts are functionally equivalent to production castings. The applications we are seeing at the moment are casting R&D, legacy part production without requalification (supply chain resiliency) and short run/bridging between trials and mass production”, Moodie told 3D ADEPT Media when asked about the key applications that demonstrate their technology potential.
Furthermore, the development of applications is fostered through industry collaborations and Foundry Lab’s development is no exception to this rule. One development effort that is worth mentioning is seen with global power management company Eaton that relies on the Digital Metal Casting System to cast aluminum parts in weeks rather than months. Those parts include stainless steel pins, and are described as “a technological advancement that is not possible with traditional 3D printing.”
“Eaton is often faced with the challenge of applying AM to legacy applications because changing the process and/or material is too big of an engineering hurdle,” says Cameron Peahl, Additive Manufacturing Manager at Eaton’s Additive Manufacturing Center of Excellence, “In this example, Foundry Lab‘s technology provides a solution for us to leverage the speed and agility of Additive while maintaining the conventional casting method and material, even including the cast-in-place steel pin. This is a huge step forward in our AM journey.”
Aware that the goal of most users is to achieve both series and mass production, Moodie confirms that they “don’t want to get stuck where 3D printing is right now.” “We are focused on production – this is what is needed to fix the capacity shortfall in industry today.”
However, in the meantime, the company’s near-term steps are to complete the digitization of the entire casting process and qualify all the key casting alloys to allow the system to fit seamlessly into manufacturing.
This dossier has first been published in the May/June edition of 3D ADEPT Mag.