Si vous êtes un lecteur régulier de 3D ADEPT Media, vous connaissez peut-être déjà Conflux Technology, une entreprise de la FA spécialisée dans le développement d’applications thermiques et fluidiques.
L’entreprise qui réinvente les échangeurs thermiques haute performance avec la fabrication additive a révélé le dernier ajout à son portefeuille d’applications : un noyau complexe imprimé en 3D qui peut être intégré dans une pièce ou un boîtier fabriqué de manière traditionnelle. Créé à l’aide d’une technologie brevetée de la société – la solution Conflux CoreTM – cet échangeur de chaleur à cartouche Conflux peut être réparé, personnalisé et interchangeable.
La solution Conflux CoreTM est une technologie qui permet de réduire la perte de charge et d’augmenter le transfert de chaleur. « Les structures à petite échelle et les géométries internes uniquement possibles avec l’impression 3D permettent un contrôle précis du ratio de la surface présentée à chaque fluide, optimisant ainsi le transfert de chaleur, la turbulence et la perte de charge.
Les caractéristiques structurelles sont également des surfaces actives, qui minimisent l’espace mort et augmentent les performances par volume », explique l’entreprise.
Cela dit, l’entreprise a été confrontée à deux défis principaux lors de la simulation : le premier consistait à s’assurer que la géométrie du noyau sélectionnée permettait de maximiser le transfert de chaleur tout en minimisant les pertes de charge ; le second nécessitait de prendre en compte l’impact des collecteurs dans le calcul des exigences de pompage.
Pour les résoudre, l’équipe a utilisé des simulations de dynamique des fluides numériques (CFD) pour la performance de la géométrie du noyau et l’impact des collecteurs. L’entreprise détaille ci-dessous le processus utilisé :
Pour les performances de la géométrie de base :
La géométrie initiale a été utilisée pour effectuer des simulations de dynamique des fluides numériques (CFD). Celles-ci ont permis de mieux estimer le taux de transfert de chaleur et les pertes de pression associés au cœur du HX. Ces simulations ont été réalisées à l’aide d’Ansys Fluent sur un cluster de calcul haute performance interne, optimisé spécifiquement pour les simulations CFD.
Le maillage est une étape nécessaire dans le processus de CFD. C’est là que tous les domaines solides et fluides sont décomposés en un grand nombre de domaines plus petits à partir desquels une solution numérique peut être trouvée. Un maillage de bonne qualité est nécessaire pour assurer la stabilité et la précision des résultats. Le maillage a été généré sur la base des pratiques de maillage standard. Des couches de gonflement ont été construites sur les parois sans glissement, et des contrôles de dimensionnement ont assuré une bonne métrique du maillage.
Des conditions aux limites à échelle appropriée ont été utilisées pour la simulation. En outre, divers contours et vecteurs de température, de pression et de vitesse ont été générés pour évaluer les performances du cœur de manière plus détaillée. Ces simulations CFD ont donné un aperçu des performances pour des améliorations supplémentaires qui n’auraient pas pu être obtenues par des calculs sur tableur.
L’impact du collecteur :
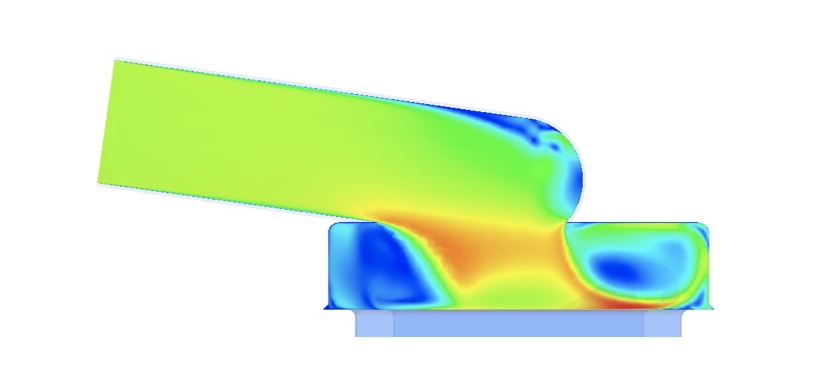
Les collecteurs sont nécessaires pour accepter les flux d’entrée de fluide, puis les diriger à travers le cœur de l’échangeur de chaleur et dans les flux de sortie de fluide. Étant donné que les collecteurs augmentent les pertes de pression du fluide à travers l’échangeur de chaleur, ils doivent être pris en compte lors du calcul des besoins de pompage.
Dans ce cas, une modélisation des milieux poreux a été réalisée pour évaluer les pertes de pression associées aux collecteurs et leurs implications.
Enfin, l’équilibre des performances thermiques et hydrauliques pour les systèmes thermiques complexes grâce à une production évolutive et à faible coût en font un produit idéal pour les petits systèmes énergétiques. En outre, la possibilité de fabriquer l’échangeur de chaleur à cartouche en grandes séries avec des machines industrielles de fusion sur lit de poudre (PBF) permet de maintenir des coûts inférieurs à ceux des options équivalentes fabriquées traditionnellement, note la société.
Une collaboration pour des solutions thermiques imprimées en 3D
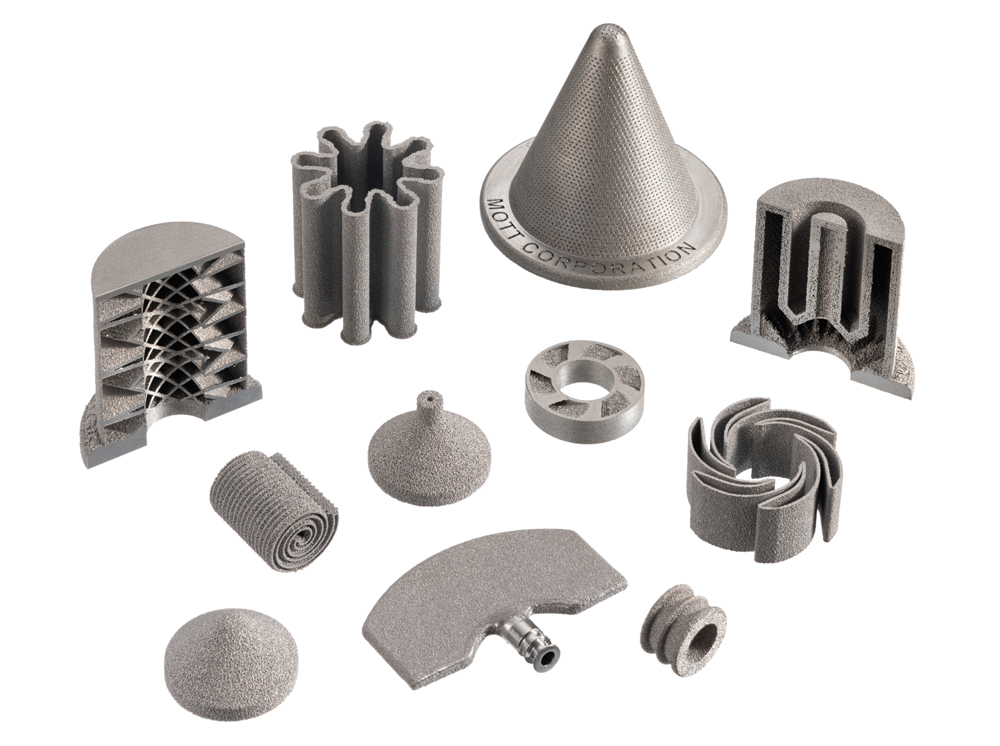
Dans un autre registre, Mott et Conflux s’associent pour introduire les solutions thermiques imprimées en 3D de Conflux sur les marchés nord-américains. Fondée en 1959 et basée à Farmington, Connecticut, Mott est une entreprise de filtration de précision qui opère sur quatre marchés principaux : Médecine, puissance de calcul, énergie propre et exploration spatiale.
L’entreprise produit des composants métalliques poreux imprimés en 3D avec du matériel intégré – une capacité qui améliore les performances dans une fraction de l’enveloppe de conception.
« Travailler avec Conflux accroît notre capacité à résoudre les défis thermiques les plus difficiles de nos clients en une seule solution intégrée « , déclare Sean Kane, vice-président du développement commercial et de la stratégie chez Mott.
N’oubliez pas que vous pouvez poster gratuitement les offres d’emploi de l’industrie de la FA sur 3D ADEPT Media ou rechercher un emploi via notre tableau d’offres d’emploi. N’hésitez pas à nous suivre sur nos réseaux sociaux et à vous inscrire à notre newsletter hebdomadaire : Facebook, Twitter, LinkedIn & Instagram !