Farsoon will share real-world customer stories on metal AM solutions at Formnext, Hall 11.1 Booth C11
Based on the adoption curve of its customers that specialize in series production, laser powder bed fusion systems manufacturer Farsoon has identified three main trends that are dominating the Additive Manufacturing (AM) market: the need for large-format parts production, the continuous cost comparison between traditional manufacturing and metal AM technology, as well as a growing focus on consumer goods series production.
As Metal AM has enabled various manufacturing applications from prototype toward end-use applications and high-volume series production, the pressure now consists in addressing production yield, cost per unit value, and factory integration challenges. This means, one standard metal AM system can no longer fit all. We are seeing a strong demand for customized metal AM solutions and machines requiring special build size, optic systems, scanning strategies and application-specific processes; running customer-sourced engineering materials.
Farsoon “Open for Industry” philosophy
As an advocate for open, high-quality industrial AM systems, Farsoon has built its reputation in the industry by providing value-added customer-centric solutions.
With this “Open for Industry” philosophy, users of Farsoon systems have access to all key parameter sets (with an integrated, advanced parameter editor) in the machine. The solutions they benefit from are based on specialized applications and material requirements that meet their specific production or development needs.
The company’s core values for customer-centric solutions include:
- Customizable machine solutions: With a comprehensive technology know-how, and a deep understanding of customers’ pain points and demands, Farsoon is open to working closely with industrial partners seeking customizable machine solutions and configurations that best suit their needs.
- Tailored services for your needs: With a customer-centric service and technical support infrastructure, Farsoon offers professional and local support, tailored services, and training experience, to help customers reduce operational costs and achieve business success.
- Best cost-to-performance: Taking great pride in its quality products, Farsoon also strives to provide the industrial market with cost-efficient solutions, and customer-specific applications support that can help achieve a good competitive edge for series production and scalability of future manufacturing.
Real-world customer success stories
- Improving manufacturing efficiency of large-format parts in aerospace:
Being one of the first commercial rocket manufacturers in China to use industrial metal 3D printing for key components engineering, Deep Blue Aerospace invested in Farsoon’s large-format metal system FS621M (build envelope 620 x 620 x 1100 mm) in 2022 to explore innovative manufacturing solutions for rocket engines.
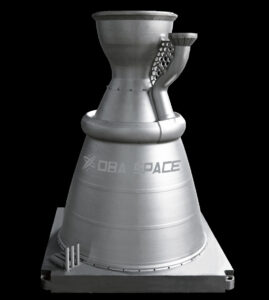
In 2022, Deep Blue Aerospace enhanced their batch production of single-piece, large-sized rocket engine combustion chambers using Farsoon’s FS621M system. The additive-manufactured inconel combustion chamber measures 780mm (30.7 inches) in height and 550mm (21.7 inches) in diameter. Major challenges include the build size, function integration, and detail resolution. The advanced additive manufacturing solution enables several applications including consolidated design, light-weight lattice structures, and complex geometries. As a reminder, complex geometries with many hundreds of internal cooling ribs and channels are likely to promote the combustion efficiency of the rocket engine.
With the FS621M quad laser system, this large-format part production takes 327 hours – a much accelerated cycle compared to the conventional process. In 2023, Farsoon metal AM application team worked together with Deep Blue Aerospace on the “Olympic” project targeting even higher production speed, while ensuring the part’s build quality. Multiple improvement items are tested and verified, including customized machine updates, advanced processing parameter development, scanning strategies, recoating and machine control. With months of joint efforts, the “Olympic” Project achieved an expedite printing time of 96.5 hours – a significant production efficiency improvement of 338%.
- Integration of Metal AM into traditional manufacturing to push for cost reduction
Borton Precision Technology Co., Ltd. specializes in customized vaping molds & tooling solutions by metal 3D printing, offering comprehensive design-to-market services including conformal cooling channel & venting design, mold flow simulation, additive manufacturing, heat treatment, and post-processing.
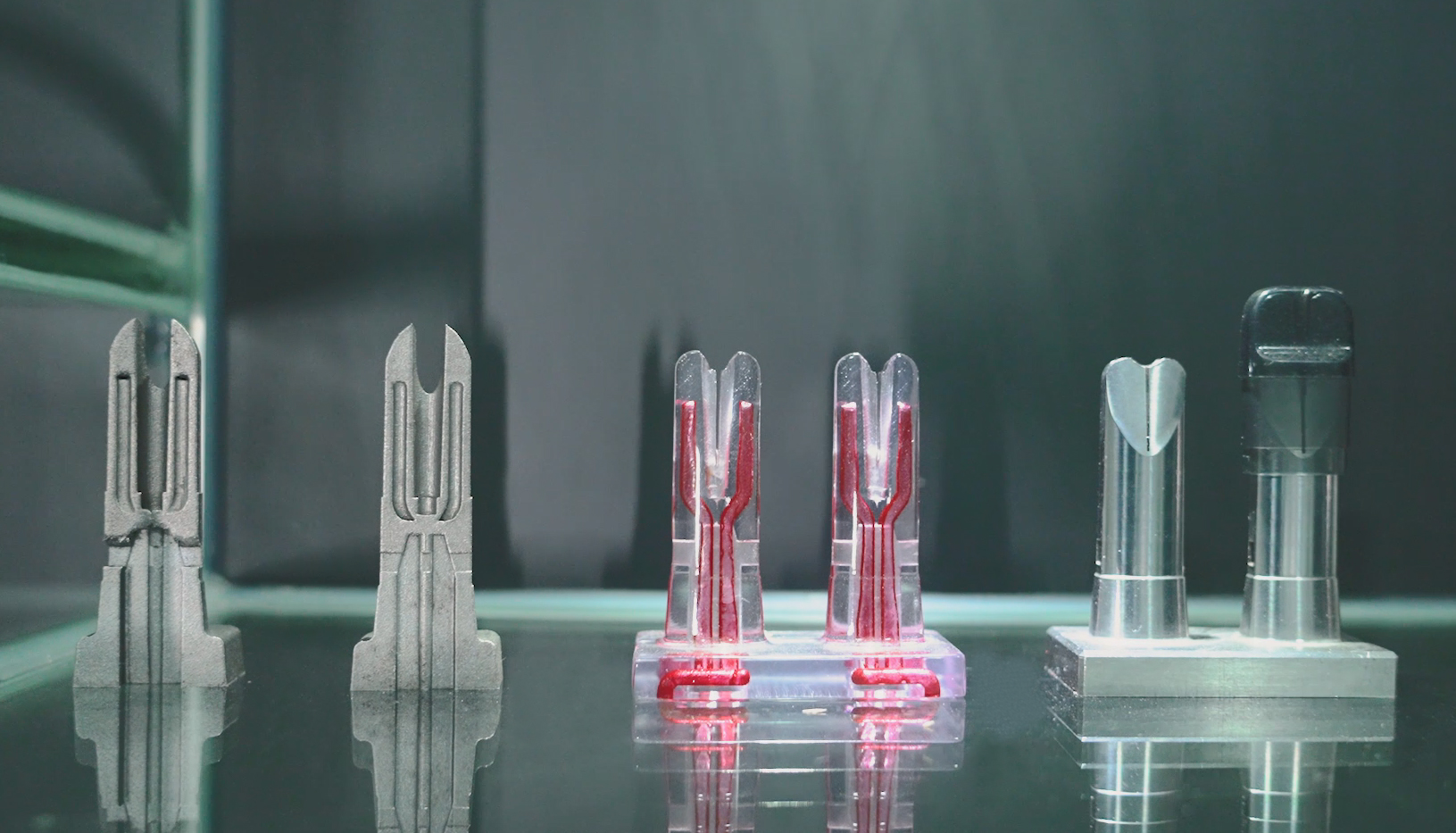
In 2021, after 6 years’ deep dive in metal 3D printing, Borton Precision adopted 5 Farsoon FS273M Dual laser systems for rapid production of highly-complicated tooling, such as injection molding, die-casting, silicone molds, and fixtures. However, when looking at the bigger picture of mold-making, AM is just one step among the multiple processes. The positioning and leveling when transferring between the processes are extremely time-consuming and require high accuracy for alignment. For advanced designs such as conformal cooling channels, for instance, the accuracy tolerance under 0.1mm is required for a functional mold product.
Taking these pain points into account, Farsoon metal AM application team worked closely with the customer to develop the Automatic Alignment Solution that consists in integrating Metal AM into traditional processes. Equipped with high-resolution in-chamber cameras and optimized visual analysis layout, the new alignment system can extract the union outline of the bottom section, as well as the internal channel features for best accurate positioning of the 3D printed section. The whole grafting process takes only 4 minutes, compared to previously hours of laborious manual alignment work; the accuracy tolerance can achieve under 0.05mm which easily meets the industry standards. When it comes to vaping molds for instance, the Automatic Alignment Solution can help improve manufacturing efficiency by 70%, while reducing the powder material cost by 69%.
- The customized Equipment in Sporting & Consumer products
In the realm of consumer goods, the enormous pressure of efficiency and cost keep driving technology innovation in AM. Futai Technology that focuses on R&D and AM of titanium alloy, manufactures sports equipment, for the golf industry in particular. The company incorporated 7 medium-sized Farsoon metal AM systems including FS200M and FS273M, and can now deliver over 15,000 3D printed golf club heads to extended markets such as Japan, Korean, Europe and U.S.
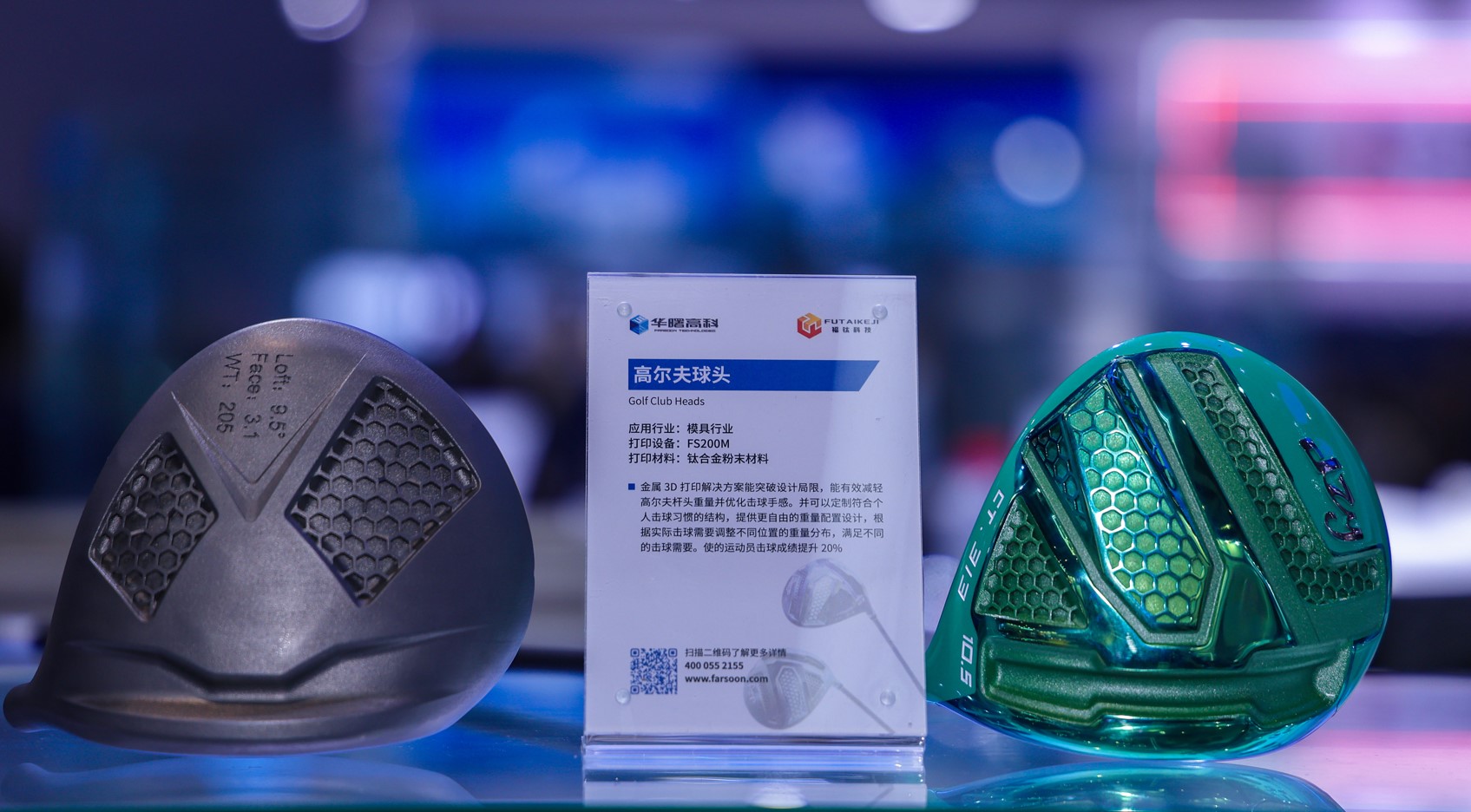
AM applications enable true economy production of customized designs in streamlined forms, light-weighting and personized options. Featuring one-of-a-kind sound window design and lattice structure, the titanium alloy golf heads showcases both durability and improved performance.
One major concern we cannot overlook is the dominating cost-pressure that requires sustainability of materials. Consumer goods companies especially, are pushing for material savings for cost savings, marketing opportunities, and carbon reduction. While AM continues to provide opportunities to reduce energy usage, the material consumption rate remains a key area to take into account here.
Farsoon strives to push the application of metal AM by working with industrial partners to offer high-quality, customer-centric 3D printing solutions. Inquiries and interested customers are welcome to contact wehelpyou@farsoon-eu.com for more information.
This content has been produced in collaboration with Farsoon.