Fondée en 2014, Velo3D développe le Système Sapphire™, un système de fabrication additive métallique par fusion laser basé sur la technologie Intelligent Fusion de l’entreprise. Après de nombreuses années en mode silencieux, Velo3Da commencé à vendre le Sapphire™ au quatrième trimestre 2018 et a réalisé des ventes de 2 millions de dollars à la fin du trimestre. Au cours du premier semestre de cette année, l’entreprise a réalisé un chiffre d’affaires de 15 millions de dollars et prévoit de terminer cette année avec un chiffre d’affaires se situant entre 25 et 30 millions de dollars.
Au milieu de la croissance passionnante de Velo3D, nous avons rencontré le CEO et fondateur pour discuter du moteur du succès de l’entreprise. #OpiniondelaSemaine
Plus tôt dans sa carrière, Benny Buller a travaillé dans l’industrie des semi-conducteurs. En tant qu’ancien vice-président de la technologie de First Solar, un fabricant américain de modules photovoltaïques à couches minces rigides, ou panneaux solaires, il a développé une expertise multidisciplinaire qui a suscité son appétit pour les investissements dans les nouvelles technologies.
En tant qu’investisseur, Buller considérait l’impression 3D comme une technologie révolutionnaire capable d’imprimer n’importe quelle géométrie. En fait, l’une des sociétés dans lesquelles il a investi a tiré à profit de la fabrication additive pour construire des moteurs de fusée. Il a fallu environ 16 semaines à l’équipe pour produire un prototype des pièces les plus simples qui puissent être produites avec FA. Curieux de savoir pourquoi le processus de production était si long, il s’est rendu compte qu’aucune des géométries que cette équipe voulait imprimer n’était réellement fabricable. Ils ont dû modifier leur conception afin de fabriquer en plus les pièces qui vont à l’encontre des principes fondamentaux de la FA : « Invente ce que tu veux. »
Velo3D a donc été créée pour répondre à cette limitation et pour rendre réelle la perception du publique de la FA : être capable de produire toute géométrie.
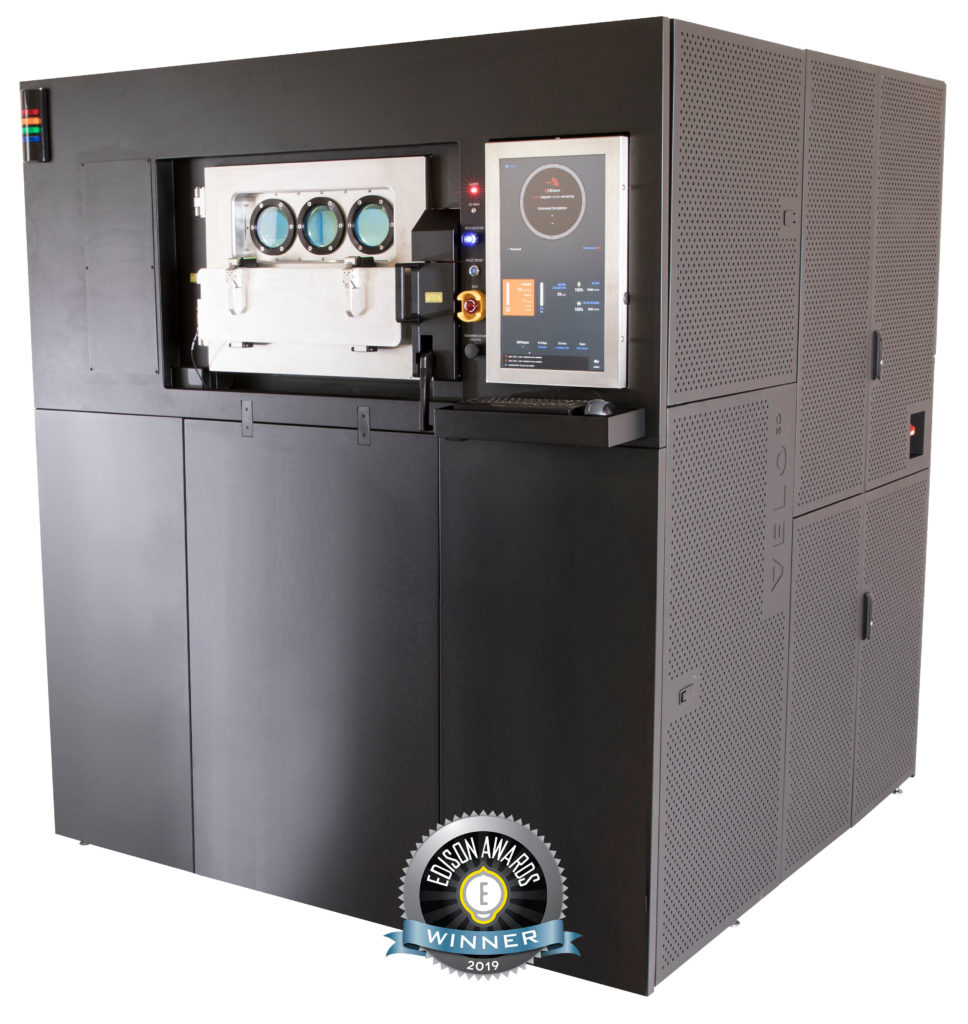
Habituellement, les limites d’une technologie entraînent la création d’une autre. Dans ce cas précis, quelle technologie a mené au développement de la technologie Intelligent Fusion ?
La technologie Intelligent Fusion a été créée à partir de la technologie de fusion sur lit de poudre. Dans l’industrie de la FA métallique, environ 80% des technologies sont basées sur la fusion sur lit de poudre. Je crois sincèrement que c’est une technologie phénoménale, mais elle a aussi ses propres limites que nous voulons aborder.
Que signifie exactement « Impression 3D sans support » ?
En termes simples, nous avons créé une technologie qui permet à un concepteur de décider quel objet il veut imprimer sans avoir à se soucier du support. En d’autres termes, il est libéré de la contrainte du support dans la conception de l’objet.
Il peut y avoir quelques supports qui restent sur la pièce mais ils sont toujours faciles à enlever. Cependant, nous avons découvert que presque tous les objets ou pièces que nous pouvons fabriquer n’ont pas besoin de supports là où nous les voulons habituellement.
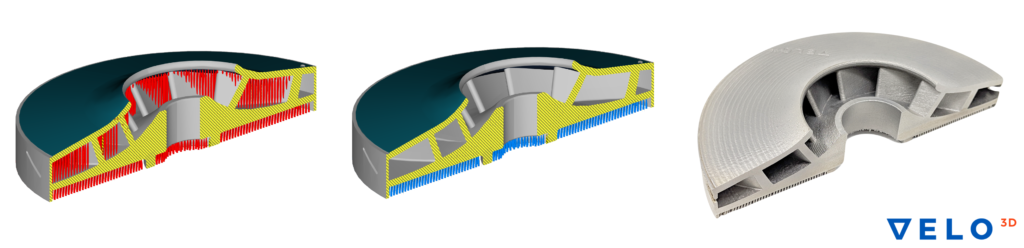
Est-ce la caractéristique principale qui rend Velo3D exceptionnelle ?
Oui, c’est la caractéristique principale. La raison est liée au fait que la FA n’est pas assez fiable pour la fabrication en série.
Pourquoi cela ?
Les grandes entreprises de Fortune 500 communiquent beaucoup sur leurs activités de FA, mais la réalité montre que très peu d’entre elles ont vraiment des développements en cours dans leurs installations. La raison en est simple : il faut des décennies pour développer un nouveau produit. Ce délai peut être encore plus long lorsqu’une nouvelle technique de fabrication est mise à profit.
GE Aviation et Stryker sont les rares sociétés qui se distinguent de la masse parce qu’elles ont pu réaliser une production significative grâce à la FA.
Pourquoi ? nous avons réalisé que le moyen le plus simple d’y arriver est de prendre les pièces qui ne sont pas conçues pour la FA et de résoudre le problème afin qu’elles puissent être fabriquées de façon additive.
Ce problème pourrait être une chaîne d’approvisionnement fragile. Beaucoup d’entreprises sont encore confrontées à des défis parce qu’elles ne font appel qu’à des techniques de fabrication traditionnelles en interne. C’est un véritable obstacle lorsqu’il s’agit, par exemple, de fabriquer une seule pièce. Un tel problème est susceptible de se poser lors du développement de nouveaux produits.
Cependant, faire le pas de géant vers la FA comporte de nombreux avantages, notamment la simplification de la complexité de la chaîne d’approvisionnement et la réduction des stocks.
Chez Velo3D, nous nous concentrons sur le fait de permettre aux entreprises de produire des pièces sans avoir à redessiner la pièce originale. Pour ce faire, notre idée est simplement de faire des répliques parfaites de la pièce. Et cela leur permet de faire leurs premiers pas en FA.
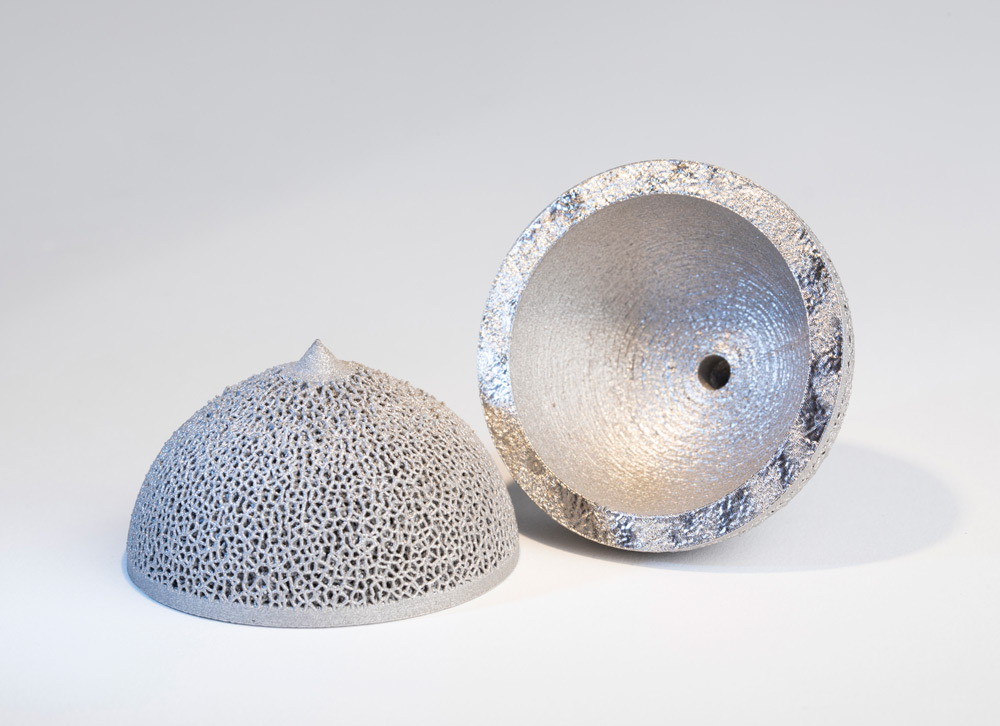
Que faut-il pour que l’impression 3D métal soit viable en production ?
La qualification est l’étape de base qui doit être assurée dans un environnement de fabrication, mais elle demeure l’une des plus grandes limites dans la FA. De plus, la FA a été très lente dans le déploiement du contrôle qualité.
Si vous pensez à la façon dont une pièce est fabriquée par FA, elle comprend des milliers d’étapes, chacune d’entre elles étant contrôlée de façon unique et numérique. La fabrication de semi-conducteurs, par exemple, nécessite des centaines d’étapes de fabrication. L’ensemble du processus peut donc prendre plusieurs mois. Afin d’éviter de se rendre compte à la fin qu’une étape a soulevé un problème, vous devez contrôler la qualité à chaque étape de chaque étape. Le contrôle final n’est que l’étape de validation.
En FA, nous avons travaillé sur un système de gestion de la qualité (SGQ) que nous publierons bientôt. Un programme pilote a été lancé chez certains clients.
Ce SGQ abordera essentiellement deux questions principales :
- Mon système est-il prêt à imprimer des pièces ?
- Le système peut-il valider chaque pièce qu’il produit ?
Grâce à ce SGQ, notre objectif est de fournir aux utilisateurs des informations complètes et précises qui leur permettront de produire des pièces répondant à leurs exigences.
- Le troisième point qui complétera cette liste est la chaîne d’approvisionnement, un processus qui doit être assuré afin de permettre une production réelle.
Il y a beaucoup d’entreprises qui achètent les pièces dont elles ont besoin, mais en raison du manque de contrôle qualité, elles doivent intégrer des capacités de conception et de fabrication en interne afin d’obtenir une production en série, ce qui prend inévitablement du temps.
Notre modèle d’affaires repose donc presque entièrement sur la façon de permettre aux entreprises d’assurer leur chaîne d’approvisionnement.
En travaillant avec les équipementiers, nous avons examiné leur portefeuille de pièces et identifié comment nous pouvons surmonter les différents défis qu’ils ont rencontrés dans leur chaîne d’approvisionnement et où ils envisagent d’exploiter la FA.
Nous les soutenons ensuite en démontrant comment le système de Velo3D est viable pour la production de leurs pièces. Dès lors, l’étape suivante consiste à créer une correspondance entre cet équipementier et un sous-traitant qui achètera notre système afin de fournir des pièces audit équipementier.
En fin de compte, un véritable système de fabrication fiable exige d’intégrer des contrôles de processus capables de produire des pièces de qualité avec moins de post-traitement et surtout d’atteindre les résultats de production souhaités.
Dans cette industrie, les fabricants contractuels sont certainement les acteurs qui sont prêts à avancer vers la production en série.
Votre dernier mot ?
Notre objectif est de passer d’un outil expérimental à un véritable outil de fabrication. Nous ne sommes pas dans le domaine du prototypage, c’est une entreprise qui fait de la production en série depuis le premier jour.
Pour des informations exclusives sur l’impression 3D, abonnez-vous à notre newsletter et suivez-nous sur les réseaux sociaux ! Vous souhaitez-vous abonner à 3D ADEPT Mag ? Ou vous voulez figurer dans le prochain numéro de notre magazine numérique ? Envoyez-nous un email à contact@3dadept.com
https://pagead2.googlesyndication.com/pagead/js/adsbygoogle.js
(adsbygoogle = window.adsbygoogle || []).push({});