Avec la contribution de EOS, SOLUKON & RÖSLER
Le post-traitement est en quelque sorte la partie du processus de fabrication qui intrigue le plus les professionnels. L’industrie fait preuve d’un certain manque de compétences et de contrôle tout au long de la chaîne de production d’une pièce finale imprimée 3D – en particulier lorsqu’il s’agit d’une pièce métallique imprimée 3D. Elle montre également un manque de source fiable lorsqu’il s’agit de développer une preuve de concept pour un procédé sûr, fiable, capable d’éliminer et de récupérer la poudre résiduelle.
C’est la raison pour laquelle nous avons décidé d’aborder ce thème. Afin d’analyser dans son ensemble les contours d’un procédé d’enlèvement de poudre nous avons invité les acteurs qui fabriquent des systèmes de fabrication additive, les fabricants de technologies de post-traitement et les prestataires de services d’impression 3D capables d’apporter un point de vue d’utilisateur de ces technologies de post-traitement. Eduardo Alonso, Regional Manager France, EOS ; Vincent Raman, spécialiste de la technologie de finition de masse chez Rösler et Andreas Hartmann, Co-fondateur et directeur technique de Solukon partagent leur expertise respective dans ce dossier. D’autres conversations et analyses de divers experts, dont les laboratoires Lawrence Livermore National, seront présentées tout au long du dossier pour mettre en évidence ou préciser certains points.
Rösler est un fournisseur d’équipements de traitement de surface (finition en série et grenaillage), ainsi que de systèmes de lavage industriel. En raison du fait qu’une pièce imprimée en 3D avec les technologies DMLS, EBM, FDM, PolyJet, SLM et SLS peut présenter des arêtes, des bavures et des aspérités, les technologies de ponçage, lissage et polissage de finition en série sont fournies par Rösler pour obtenir le rendu attendu. L’an dernier, l’entreprise s’est associée à PostProcess,
un autre spécialiste des technologies de post-traitement afin de compléter son portefeuille de produits.
EOS est un fabricant de systèmes d’impression 3D industrielle. Fondée en 1989, l’entreprise propose une large gamme de solutions holistiques dans la fabrication additive. Leur participation à ce dossier est assez atypique dans la mesure où ils discutent souvent de l’élimination des poudres dans le cadre du thème général du procédé de fabrication des poudres ou de la gestion du matériau.
Enfin, Solukon est un fabricant allemand d’équipements périphériques de post-traitement pour les technologies de fabrication additive. L’entreprise met l’accent sur les unités de dépoudrage automatique et les stations de déballage pour les pièces métalliques et plastiques fondues au laser.
L’étape de post-production consiste en une série de procédés de fabrication supplémentaires tels que le traitement thermique pour obtenir les propriétés souhaitées. L’élimination de l’excès de poudre des cavités internes et des géométries complexes des pièces imprimées est un élément crucial de cette étape. Le manque de compétences précises concernant cette étape du processus de FA conduit souvent à externaliser l’étape de post-traitement pour obtenir de meilleurs résultats au niveau de la pièce finie. Cela pourrait donc expliquer le fait que la production de pièces fabriquées de manière additive fonctionnelles et provenant d’une source unique, reste hors de portée de plusieurs fabricants.
En ce qui concerne les technologies de fabrication additive elles-mêmes, un processus d’élimination des poudres est nécessaire pour toutes les technologies qui font fondre une poudre, par exemple la fusion en lit de poudre, le dépôt direct d’énergie à base de poudre,
la projection de liant, etc. Vincent Raman de Rösler et Andreas Hartmann de Solukon précisent que les procédés de fusion en lit de poudre comme la fusion au laser ou le frittage au laser nécessitent principalement un procédé d’élimination de poudre. Ce processus soulève plusieurs défis de post-production que nous allons démystifier.
Défis rencontrés lors d’un processus d’élimination de poudre métallique
Pour rappel, la fusion sur lit de poudre métallique est une technologie de fabrication additive (FA) qui fait fondre des couches de poudre métallique entre elles afin de générer rapidement de nouvelles pièces. Le seul bémol est qu’à la fin du processus de fabrication, on constate que l’excès de poudre recouvre les pièces nouvellement imprimées, ce qui représente un risque non seulement pour les processus de fabrication futurs mais aussi pour la santé des opérateurs.
De plus, l’élimination de cette poudre prend beaucoup de temps puisqu’elle est éliminée manuellement, ce qui crée un goulot d’étranglement pour les productions à grande échelle, d’où le besoin d’un système qui nécessite un minimum d’intervention de l’utilisateur avant la prochaine étape.
Bien que Vincent Raman de Rösler explique que les systèmes de FA sont livrés avec des solutions pour le traitement de surface et l’enlèvement des supports, Eduardo Alonso précise de son côté que « le principal défi est de retirer complètement la poudre de la pièce, en particulier des canaux et des petits espaces où il est plus difficile de le faire. Un autre point important est la sécurité des opérateurs, c’est-à-dire minimiser le contact de la poudre pendant l’enlèvement. »
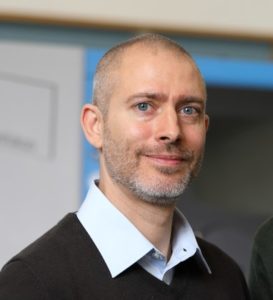
De plus, selon un expert de Lawrence Livermore National Laboratories, « un autre défi est de savoir quand toute la poudre a été enlevée » d’une part, et d’autre part, selon les termes d’Andreas Hartmann, « d’enlever la poudre résiduelle de manière sûre, efficace, économique, avec des résultats de nettoyage reproductibles et sans contamination pour le recyclage ».
La première observation est que ces défis peuvent varier d’un utilisateur ou d’un fabricant à l’autre en raison du type de procédé de post-traitement qu’ils utilisent.
Les processus d’élimination actuels peuvent généralement être divisés en trois catégories : les processus manuels, l’immersion dans un liquide et le nettoyage par ultrasons.
De nos jours, le procédé le plus utilisé reste le procédé manuel, qui nécessite parfois l’utilisation d’air comprimé pour éliminer les cavités. Il consiste à secouer physiquement les pièces à l’aide de brosses, de cure-pipes ou d’une plaque à l’aide d’un maillet pour éliminer la poudre. De plus, il est encadré par une réglementation stricte en raison des exigences de sécurité de la machine. En effet, les risques liés à ce procédé concernent principalement les poudres métalliques non contrôlées et aéroportées.
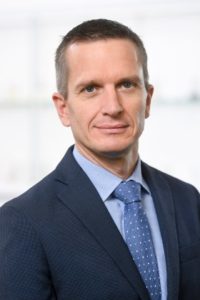
Bien qu’elle soit qualifiée par d’autres comme nécessitant beaucoup de temps, EOS estime que le « processus manuel est généralement totalement flexible, car il peut être réalisé à tout moment sur n’importe quelle machine d’impression 3D ». Ce serait certainement le plus grand avantage de ce processus. Cependant, dans la recherche constante de la rapidité, l’entreprise reconnaît également l’importance de l’automatisation dans le post-traitement. En effet, Eduardo Alonso ajoute que « l’automatisation du processus d’enlèvement de poudre est en cours de test pilote chez EOS et chez certains clients pilotes : l’automatisation afin d’enlever la majeure partie de la poudre par exemple en faisant tourner de 180° l’interchangeable dans le cadre du système d’impression 3D ou par un bras robot avec une buse d’aspiration ».
En ce qui concerne l’immersion liquide, une recherche explique que le succès du processus d’élimination de la poudre par cette technique varie souvent d’une personne à l’autre. Les appareils utilisés dans ce cas sont généralement fabriqués en interne et utilisent généralement un écoulement de fluide pour balayer les débris. Un bon exemple de ce type de solution est le matériau de support soluble récemment dévoilé par XJET, fabricant de la technologie d’impression 3D métal et céramique CARMEL. Uniquement destiné au métal, le fabricant israélien a expliqué qu’il faut quelques secondes pour parfaire l’ensemble du tableau et faciliter la fin du processus de fabrication.
La solution réduit les besoins en main d’œuvre tout en améliorant le processus. Se dissolvant rapidement dans une solution à base d’eau, sans danger, les avantages des matériaux de support solubles peuvent être frappants.
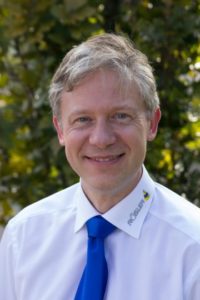
Vincent Raman a déclaré à propos du procédé d’immersion dans le liquide : « L’immersion dans un liquide enlève les structures de support pour différentes techniques d’impression, aussi bien en grandes séries que sur une seule pièce, sans action manuelle». Cependant, pour le spécialiste de
la technologie de finition en série, « beaucoup de clients utilisent un procédé de grenaillage qui nécessite beaucoup de travail manuel la plupart du temps, d’où la fonction d’automa-tisation que Rösler a intégrée pour les petites pièces ».
En ce qui concerne le procédé de nettoyage par ultrasons, il consiste à immerger la pièce dans un bain fluide (eau ou solvant), puis à utiliser un transducteur pour créer des ondes ultrasonores. Ces ondes conduisent à la cavitation et une fois que les bulles formées s’effondrent, elles enlèvent les débris de la pièce. Un inconvénient de ce procédé est que l’immersion d’une pièce dans du liquide rend la poudre retirée inutile alors que pour des raisons économiques, les fabricants ont souvent tendance à réutiliser la poudre retirée.
Andreas Hartmann, le cofondateur et CEO de Solukon donne un aperçu général sur les trois catégories de procédés d’enlèvement de métaux :
« A première vue, les processus manuels ne requièrent pas beaucoup de savoir-faire et peuvent être réalisés à l’aide d’appareils de soufflage ou de brossage. Mais en y regardant de plus près, l’enlèvement manuel de la poudre est très risqué car l’opérateur entre inévitablement en contact avec des particules.
Ce matériau métallique est très fin et assez léger pour être aéroporté dans de nombreux cas. Elle est généralement nocive pour la santé et il existe un risque qu’elle pénètre dans l’organisme par les voies respiratoires ou par la peau. Si la poudre est libérée dans l’air, elle peut créer des nuages de poussière qui peuvent créer une atmosphère dangereusement explosive.
En même temps, l’enlèvement manuel de la poudre prend beaucoup de temps et les résultats de nettoyage sont imprévisibles avec une reproductibilité variable, ce qui compromet la qualité. Tous ces facteurs comportent des risques pour la santé, la sécurité, la qualité et des coûts élevés.
L’immersion liquide fonctionne très bien pour nettoyer les surfaces sans laisser de résidus, mais les pièces doivent être pré-nettoyées avec un procédé à sec sous forme de poudre résiduelle, ce qui soulève souvent des problèmes lorsque les canaux internes sont remplis de poudre.
La poudre se coince et la pièce est endommagée. Les ultrasons peuvent être très utiles, mais des canaux obstrués sont également possibles. En général, lors de l’immersion, la poudre résiduelle ne peut pas être réutilisée et doit être éliminée.
L’immersion avec des solvants chimiques ou des méthodes d’impulsions électrochimiques sont des solutions parfaites car elles permettent d’enlever les structures de support et d’améliorer les surfaces des pièces. Cependant, dans ce cas, il est utile d’enlever la plus grande partie de la poudre dans un procédé à sec car la poudre ne peut pas être réutilisée. »
D’autres dispositifs et méthodes (en instance de brevet) d’élimination de poudre ne sont pas toujours destinés aux technologies de FA. Certains d’entre eux incluent l’utilisation de vibrations tandis que d’autres utilisent des aspirateurs ou des forces magnétiques pour enlever la poudre.
Regard sur les technologies de post-traitement des entreprises participantes
EOS
Comme annoncé précédemment, le fabricant allemand EOS propose tout un système de gestion des poudres. Appelé IPCM M pro, il permet de transporter hors du système de FA des matériaux qui ne sont pas fondus pendant le processus de construction, sans ouvrir la porte de la chambre de traitement et donc sans que l’opérateur entre en contact direct avec le matériau.
« Une pompe à vide transporte la poudre hors du système et dans l’IPCM M pro, où elle est tamisée sous gaz inerte dans le module à un débit de 120 kg de matière en 30 minutes – 50 % plus rapide que les solutions précédentes. La poudre ainsi traitée peut être utilisée pour un nouveau processus de construction, et le cycle de la poudre recommence ainsi. »
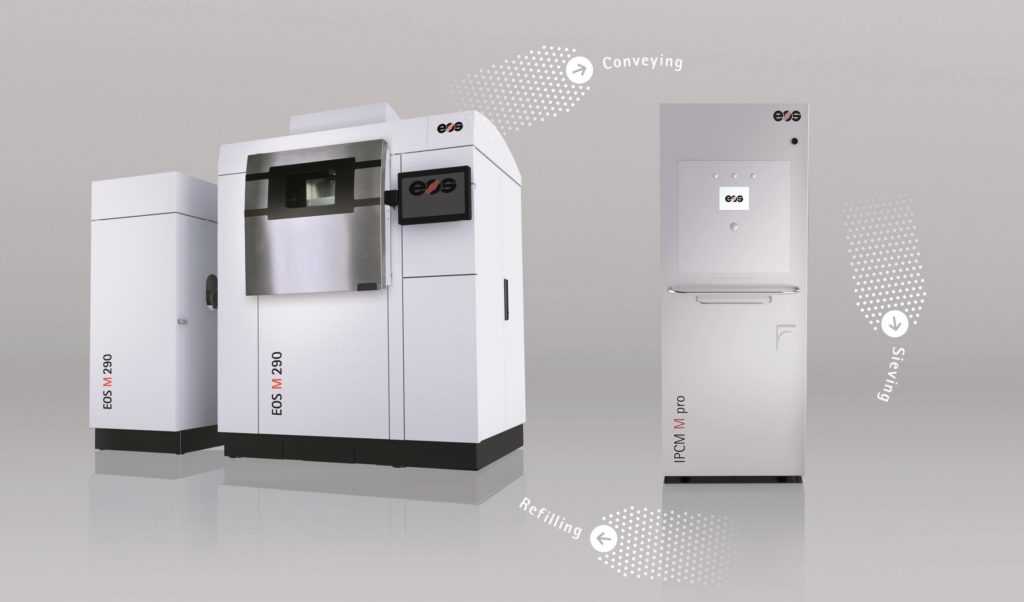
Selon l’entreprise, il s’agit d’un équipement de protection confortable en raison de ses avantages en termes de santé et de sécurité ainsi que d’opérabilité, car le risque de contact avec la poudre est minimisé.
Rösler
Rösler ne fournit pas seulement des technologies de post-traitement pour la fabrication additive métallique. « Nous fournissons des procédés de post-im-pression et de frittage. Ces processus sont définis comme l’enlèvement des structures de support (pour pièces métalliques et plastiques) et l’amélioration de la surface (des pièces métalliques et plastiques). Notre plus grand avantage est l’automatisation ainsi que la longue expérience de l’entreprise en tant que spécialiste des surfaces », explique Vincent Raman.
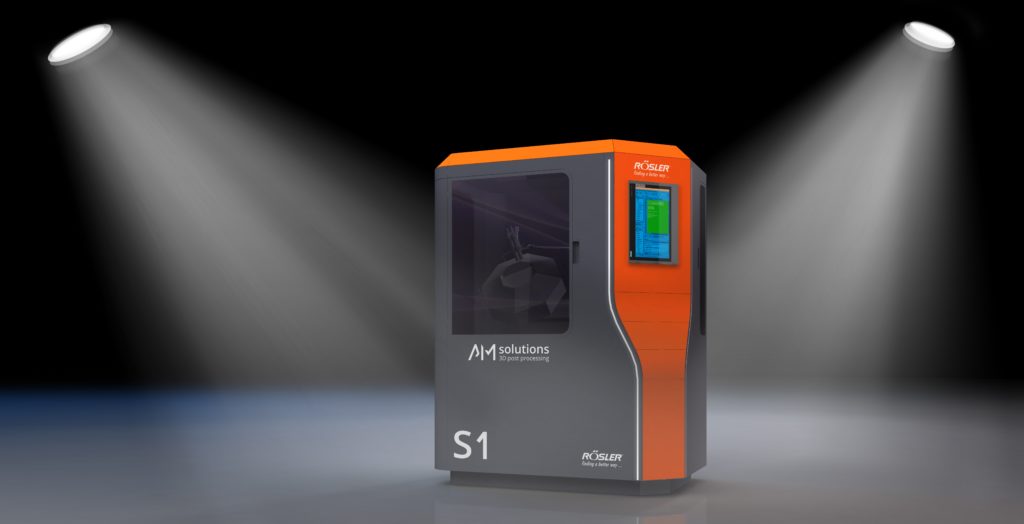
Solukon
Quant à Solukon, l’entreprise a récemment dévoilé son équipement de dépoudrage SFM-AT800-S suivant le à la suite du SFM-AT800.
En parlant de ces équipements, Andreas Hartmann a déclaré que « les unités de dépoudrage automatisées enlèvent et collectent la poudre résiduelle des pièces complexes fondues au laser
avec des vibrations ciblées et une rotation programmable à deux axes dans une atmosphère protégée. La vibration réglable et à haute fréquence rend la poudre fluide de sorte qu’elle peut facilement s’écouler de très petits espaces et de canaux complexes.
L’écoulement de la poudre est soutenu par le déplacement de la pièce automatisée autour de deux axes vers toutes les positions 3D possibles en continu ou vers des positions programmées individuellement.
De plus, les systèmes sont équipés de dispositifs de soufflage manuels ou automatisés.
Pour éviter les atmosphères explosives pour les matériaux réactifs comme le titane et l’aluminium, la chambre de traitement peut être rendue inerte grâce à une infusion de gaz inerte contrôlée par sécurité.
La poudre résiduelle peut être collectée sans contamination pour être recyclée dans des conteneurs spéciaux ou directement recyclée dans un système de tamisage raccordé.
En plus d’atténuer les risques pour la santé et la sécurité, les utilisateurs peuvent réduire considérablement le temps de nettoyage et améliorer la collecte et le recyclage des poudres coûteuses non utilisées.
Certains utilisateurs ont signalé une réduction de la main d’œuvre allant jusqu’à 90% par rapport aux procédés manuels d’enlèvement de poudre. »
L’entreprise ajoute que, « grâce à la vibration réglable, le procédé est très doux et n’influence pas les propriétés mécaniques de la pièce ou de la surface».
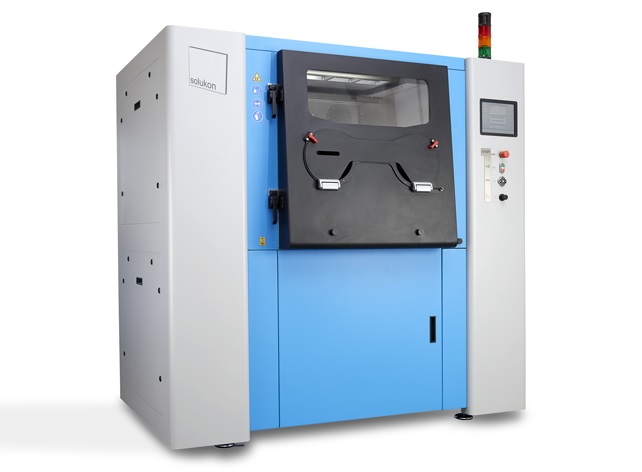
Obtenir la pièce finie désirée
Lors d’un séminaire de GE Additive, l’un des ingénieurs de l’entreprise a déclaré que de toutes les étapes qui sont intégrées dans le coût final d’une pièce – les frais d’exploitation, les coûts d’usinage, les coûts des matériaux des pièces, les déchets solides, les déchets de poudre, etc. – les opérations de post-production représentent souvent presque 30% du coût du post-traitement, ce qui peut représenter un problème pour une entreprise.
Par conséquent, gérer les opérations de post-traitement d’une production de la bonne façon, pourrait se traduire par des avantages significatifs pour les entreprises. La gestion de ces opérations nécessite évidemment de prendre en compte tous les contours de l’idée : l’environnement, l’équipement approprié et même le but final après l’élimination des poudres.