Elastomers are materials that are part of the big family of polymers. Generally speaking, they refer to rubbers, i.e. macromolecular, natural or synthetic substances that integrate the elasticity of rubber. They are found in almost all daily objects. They are also widely used across a wide range of industries including the automotive, aeronautics, transport, electrical industry and medicine; sectors that harness additive manufacturing, hence the interest in tackling this topic.
Elastomers are strengthened by the addition of other materials such as metals, textiles, and some plastics. It goes without saying that, a part manufactured with the elastomeric material of company A will not necessarily give the exact same rendering than a part manufactured with the elastomeric material of company B. Moreover, due to intellectual property, some producers do not disclose the chemical composition of their material.
General characteristics of elastomers
Elastomers are unique; their features are different from plastics or plastomers, other materials of the polymers family.
Elastomeric materials that are mechanically recognized as a rubber are:
- Flexible: they integrate low stiffness;
- Soft: parts made of this material can withstand very large deformations without breaking or reach “breaking” elongations;
- Elastics. The parts regain their initial shape when they are no longer requested. In addition, the energy that has been supplied to deform the part is then redistributed quantitatively in the middle of the part.
In the additive manufacturing industry in general, there is currently a limited range of elastomers compatible with 3D printers. Indeed, due to mechanical constraints of 3D printers (melt index viscosity, etc.), many materials integrate formulations that best suit traditional manufacturing processes.
Elastomers that are suitable for additive manufacturing
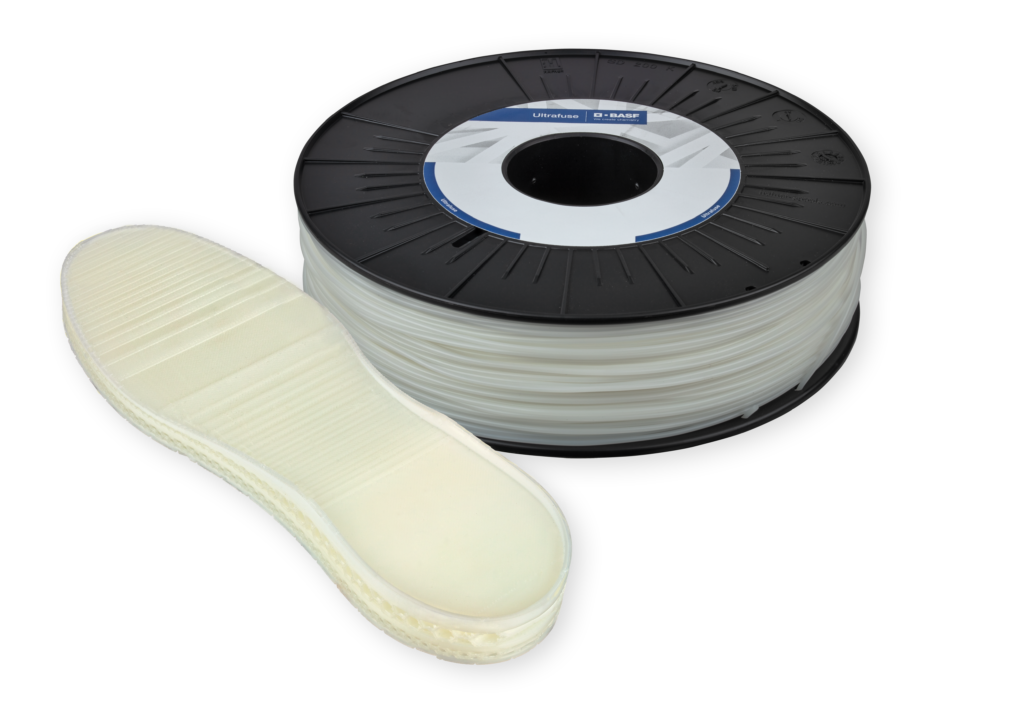
When it comes to elastomers, four materials stand out from the crowd: TPU, flexible PLA and flexible PE for thermoplastics, and acrylic-type photo-elastomers.
When asked what is the widely used elastomer among these four, market players’ answer is definitely not the same. Their prism of analysis often depends on their sector of activity or on the increasing use of one material instead of another in their region. Anyway, that’s exactly what we perceive when we asked this question to Albert de Boer, additive manufacturing engineer at Innofil3D and Franco Cevolini, VP & CTO of CRP Technology.
For those who may not know, Innofil3D – a company that has been acquired by BASF – is a producer of filaments dedicated to FDM/FFF technologies – The company has recently been acquired by BASF. Based in the Netherlands, Innofil3D supplies its filaments throughout Europe.
CRP Technology on the other hand is a company of CRP Group, an industrial group that specializes in additive manufacturing,Rapid Prototyping and high precision machining services in the motorsport sector and in the manufacture of components for F1 racing cars. By creating CRP Technology, the group is opening up to rapid prototyping and additive manufacturing solutions in order to better serve its preferred sectors.
For Albert de Boer: “an elastomer is far more flexible than the more regular used rigid thermoplastic polymers such as PLA for example. The main elastomeric polymers I think, which are used in AM, are TPU materials with different shore grades. TPU stands for Thermoplastic polyurethanes. Consisting of hard and soft segments to control the shore hardness.”
Franco Cevolini states that “the main elastomers used in the AM market belong to TPE and TPU. TPE stands for Thermoplastic elastomers, TPU stands for thermoplastic polyurethane. CRP Technology’s elastomer is Windform® RL, and it is part of TPE family.”
TPUs and TPEs are the most widely used elastomers in the additive manufacturing market.
Which elastomer for which AM technology?
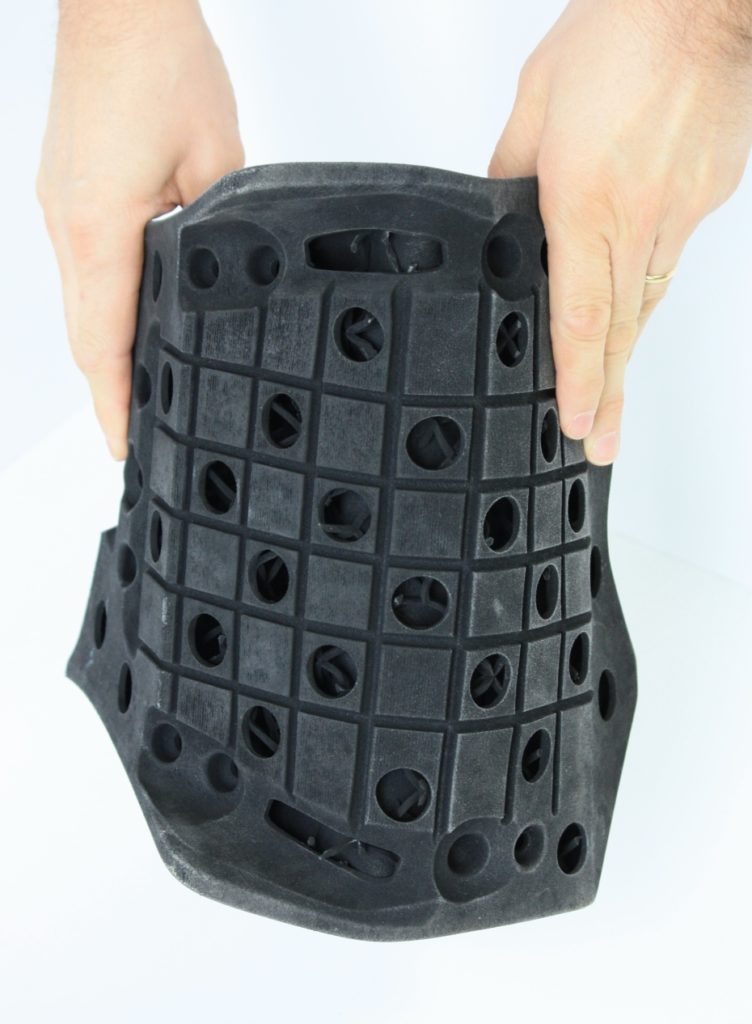
Elastomers are usually used with FDM or FFF technologies. According to Innofil3D, FDM technologies are the AM technologies that best process these materials.
CRP Technology on the other hand, adds that they can also be used with other AM technologies including SLS technology. Despite the fact that most operators increasingly use less expensive technologies (e.g. FDM) for prototyping applications, CRP Technology leverages SLS technology and elastomers to produce parts.
However, it should be noted some AM suppliers have developed materials that can be used to produce functional parts.
Stratasys for instance has recently brought to market advanced elastomers and enhanced materials for its leading FDM and PolyJet machines. The FDM elastomer solution is intended to provide manufacturers with new levels of elasticity, durability with true soluble support – while advanced colors for PolyJet drive enhanced realism to transform legacy design and prototyping processes.
Offered across the F123 3D Printer platform, the Stratasys TPU 92A Elastomer is designed to meet the needs of manufacturers requiring high part elongation, superior toughness, and full design freedom.
“Creating elastomer parts using traditional silicone or CNC molds are extremely costly and time-consuming – while it is our view that other additive techniques just cannot deliver parts with the size and complexity of our elastomer approach,” Zehavit Reisin, Vice President and Head of Solutions and Materials Business, Stratasys. “Manufacturers demand 3D printing solutions that can be put to work in real prototyping and extreme production environments. With reliable and highly resilient parts, our solutions are designed to enable customers to do just that.”
Technical specifications and application of elastomers in EM
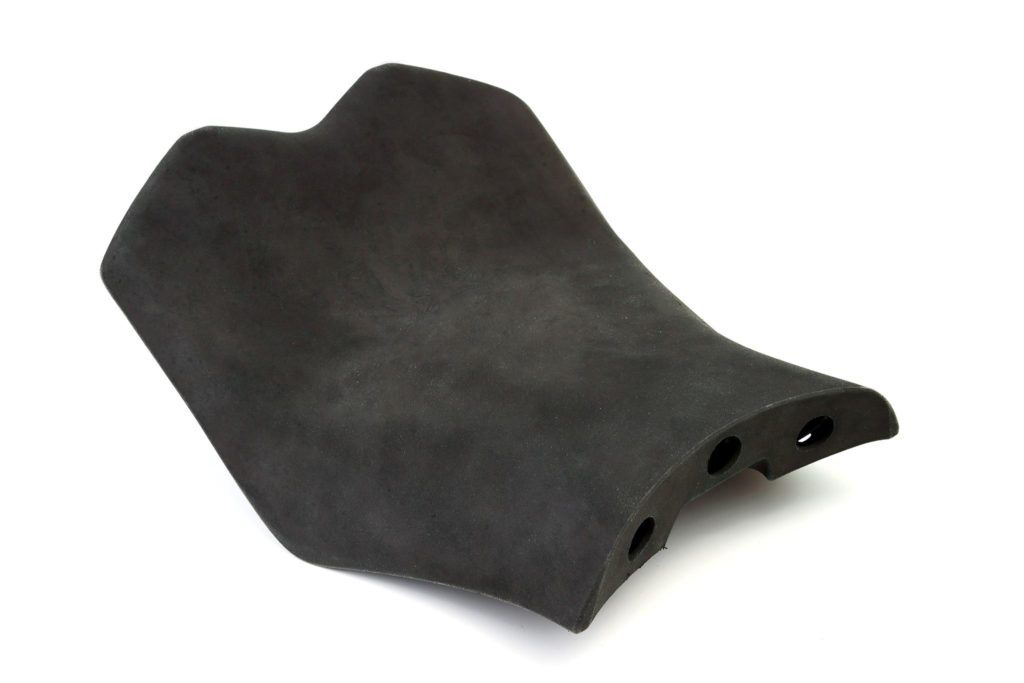
While comparing the technical data sheet of Innofil3D’s material and the information CRP Technology gave us, we realized that the chemical formulation of each TPU material varies from one manufacturer to another.
Speaking of Innofil3D’s Ultrafuse TPU 85A, the TPU material is high resilient, available in its natural white colour and has good wear performance. Furthermore, it has good flexibility at low temperatures and good damping behaviour.
“Its chemical properties (e.g. resistance against particular substances) and tolerance for solvents can be made available, if these factors are relevant for a specific application”, adds the company.
Franco Cevolini on the other side, presents Windform® RL (“RL” stands for rubber like), the first thermoplastic elastomer material within Windform® TOP-LINE family of high-performance composite materials.
“Just like all Windform® TOP-LINE materials, it is designed for laser sintering technology. Windform® RL shows excellent durability and stability. If elastomers lose their properties overtime; it should be noted that it doesn’t happen to Windform® RL. The material accommodates chemicals and heat resistance and combines superior tear resistance with burst strength. Windform® RL withstands repeated bending and deformation. It is also UV resistant. Being a TPE material and thanks to its main properties, it assures high performance sealing power. Since it is a TPE material and thanks to its main properties, Windform® RL be sealed to assure high performance sealing power.”
Some of the mechanical properties of Windform® RL are: “tensile strength: 5,2 Mpa (sintered value) 5,0 Mpa (Value after Windform® RL Seal infiltration). Tensile Modulus: 20,0 Mpa (sintered value) 20,3 Mpa (Value after Windform® RL Seal infiltration). Elongation at break: 397,1 % (sintered value) 383,6 % (Value after Windform® RL Seal infiltration). Shore A Hardness: 84,8 (sintered value) 83,0 (Value after Windform® RL Seal infiltration).”
CRP Technology produced Energica’s motorcycles seat using 3D printing and Windform® materials. At the end of the manufacturing process, the company unveiled a 3D printed front air inlet made with Windform® high performance materials.
Market expectations
To sum up, “due to their low production cost, their flexibility and their ability to be leveraged by several thermoplastic processing techniques, operators increasingly harness thermoplastic elastomers (TPEs). These advantages over conventional rubbers make them very competitive in all applications that do not require high elasticity or high heat resistance,” explain 2 researchers from Paris-Sorbonne and the Ecole supérieure de l’industrie du caoutchouc.
In additive manufacturing especially, a similar situation with other polymer materials can be observed: the lack of qualified materials that can be used on different AM technologies. Stratasys and CRP Technology are part of the few specialists that unveil different applications of AM with elastomer materials. If other applications have been performed with other technologies, they are not yet sufficiently popularized.
From a technical point of view, one thing is certain: as long as elastomers guarantee high performance, the more the market expands, the more applications for mass production will be explored.
Disclaimer: this article has originally been published in 2019 October-November issue of 3D ADEPT Mag
Remember, you can post job opportunities in the AM Industry on 3D ADEPT Media free of charge or look for a job via our job board. Make sure to follow us on our social networks and subscribe to our weekly newsletter : Facebook, Twitter, LinkedIn & Instagram ! If you want to be featured in the next issue of our digital magazine or if you hear a story that needs to be heard, make sure to send it to contact@3dadept.com