If everything we use comes from natural resources and that natural ecosystems are often described as models of sustainability, does that mean that every 3D printed product inspired by nature is de facto a sustainable product? A conversation with Libonati Flavia, researcher and Associate Professor, at Università degli Studi di Genova.
It makes perfect sense to explore how nature can inspire 3D printing companies. As a matter of fact, 3D printing companies that have already gone down this route, have embraced the concept of biomimicry and yes, applications shared so far, revealed some real cool designs inspired by nature. But that’s not enough, not today when we are looking for tangible examples that can support the ‘sustainability’ argument, for examples that show what is possible in industrial production.
So, we caught up with Flavia Libonati, researcher and Associate Professor, at Università degli Studi di Genova – an Italian University – and whose work is at the intersection of nature, materials, 3D printing and engineering. Her research focuses on toughening a n d fa i l u re m e c h a n i s m s of biological structural materials, such as bone and nacre, from molecular to engineering scale and on the design of novel composites. She uses a material-by-design approach, combining Nature and engineering principles including 3D printing to improve the mechanical properties of materials, thus combining them successfully in an optimal way.
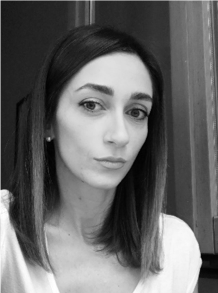
From the outset, Libonati said that “we are dealing with a two-way process. 3D printing can transform biomimicry and vice-versa. On the one hand, 3D printing has revolutionized everything, including the biomimicry design approach. The technology and its principles have opened the design space, broken down several manufacturing barriers and now enable designers to 3D print components with very complex shapes. On the other hand, biomimicry transforms 3D printing to the extent that it opens new perspectives and changes at a functional level. It helps for instance to explore new material possibilities, new material functions as nature does. 4D printing for instance, enables to get new functions within the printed component by adding a new dimension, so it goes beyond the simple manufacture of the part.”
The professor goes even further to explain the principles of nature that are leveraged by engineers: “ Nature uses a few building blocks, such as proteins and minerals; and–through complex hierarchical structures¬¬–it creates a variety of materials, which are multi-functional, efficient, and sustainable. If you think about the basic materials seen in nature –nacre, bamboo, bone, etc.
They have a very complex structure and diversify a lot, and this diversity of structures and functions can also be seen within the same material. Bone for instance, is a material that features many sub-structures, which are made of minerals and proteins, to name a few composition items.
These structures are mixed together at different length scales – from the nanoscale to the macroscale –to yield different complex macrostructures able to perform different functions in the body. Seven levels of hierarchy are actually recognized for this material. Even within our body, the bone tissue differentiates a lot so, a compact tissue will definitely not have the same properties as the spongy one, but both are made from the same building blocks. We can do the same with 3D printing. We start with these building blocks and then we look at nature and how a specific local shape can affect and enhance the performance of a whole part. Thereafter, we try to combine these building blocks and diversify the various substructures to bring out for instance, composites with different properties”.
By understanding how materials function in the nature for instance, by emulating the natural world, engineers can easily find solutions to some of their design challenges.
The example of the way materials work in nature is just one that stands out from the crowd as Libonati notes that every trade of the 3D printing value chain can see their work affected by a biomimicry approach. This includes the designer, the materials expert, or even the parts producer. “ I n the designer’s work, the biomimicry approach will affect the creative part and help provide optimal solutions inspired by nature. It’s easy for designers to take inspiration from solutions found in Nature, not only because they are optimized, but they are not covered by intellectual property. A materials expert on the other hand, will need to understand how these solutions work and how to translate it into synthetic materials, bearing in mind that the latter are not living materials like biological materials.”
However, “the evolution of 3D printing is very related to the evolution of materials”, she said, hence this focus on materials as part of this feature. “The more we open the palette of materials we can print, the more we can develop a diverse range of structures for materials, and therefore, a wide range of material’ formulations and their printability”, she adds.
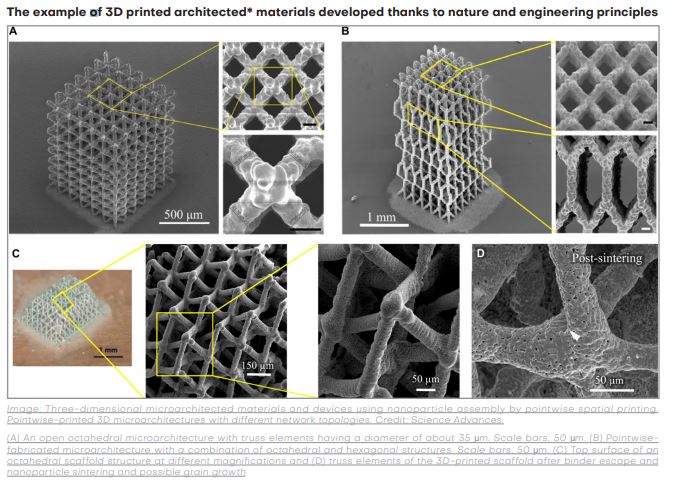
As part of a research project, the Associate Professor, together with a team of researchers, has provided a deeper understanding of the « structure – property » relationship of crystal-lattice-inspired materials. While the study starts with single unit cells inspired by the cubic Bravais crystal lattices, the research team utilized what they learned from Nature on the one hand, and on the other hand, a set of methods which include 3D printing and mechanical testing, to investigate the influence of different printing parameters, and numerical modelling to design lightweight architected materials.
While Nature provides solutions for porous structures , from shock-absorbing hedgehog’s spines to trabecular bone, it should be noted that the shock-absorbing hedgehog, which helps to prevent injuries, is very similar to a foam that fills the central part of a spine, supports the thin outer wall, contrasting local instability and allowing the whole system to bend further without breaking. The trabecular bone on the other hand, is another example of cellular structure at the microscale with energy-absorbing properties.
With an open-cell porous arrangement, apparently random, it is “carefully designed by Nature to bear specific local loadings and to fulfil different functional needs while keeping a low weight”, the research reads.
“Numerical models, validated based on experimental testing carried out on single unit cells and embedding manufacturing-induced defects, are used to derive the scaling laws for each studied topology, thus providing guidelines for materials selection and design, and the basis for future homogenization and optimization studies. We observe no clear effect of the layer thickness on the mechanical properties of both bulk material and lattice structures. Instead, the printing direction effect, negligible in solid samples, becomes relevant in lattice structures, yielding different stiffnesses of struts and nodes. This phenomenon is accounted for in the proposed simulation framework. The numerical models of large arrays used to define the scaling laws suggest that the chosen topologies have a mainly stretching-dominated behaviour, a hallmark of structurally efficient structures where the modulus scales linearly with the relative density.
By looking ahead, mimicking the characteristic microscale structure of crystalline materials will allow replicating the typical behaviour of crystals at a larger scale, combining the hardening traits of metallurgy with the characteristic behaviour of polymers and the advantage of lightweight architected structures, leading to novel materials with multiple functions.” the report says.

What we will keep from Libonati’s explanations is that “nature does everything from the nanoscale on, with a hierarchical organization, and we need to find a way to translate the process into manufacturing, while maintaining a multiscale precision. This way, we will find better ways to develop new high-performance materials.” In addition to 3D printed architected materials, other examples of a biomimicry approach within the 3D printing sphere highlight the use of honeycomb structures in 3D printed parts.
The honeycomb pattern results from the cross-section study of a real honeycomb. In a 3D printed object, this pattern can deliver greater strength while using less material. Since the biomimicry-design approach somehow leads to the fabrication of 3D printed objects with less materials, it’s fair to say this approach may enable the development of more “green products” in the long run. However, without any quantifiable data regarding the complete value chain, it will be hard to confirm how “sustainable” it is for manufacturers.
Reality is, the commercial market for bio-based products or materials is almost non-existent, even though in the meantime a lot is being done at the research level. Therefore, one should recognize the efforts of researchers like Libonati who are leveraging the full capabilities of biomimicry to extend the palette of 3D printing materials, or to advance new manufacturing processes like 4D Printing.
This exclusive feature has first been published in the 2021 September/October edition 3D ADEPT Mag.
Featured image: Credit: Google Earth – Remember, you can post free of charge job opportunities in the AM Industry on 3D ADEPT Media or look for a job via our job board. Make sure to follow us on our social networks and subscribe to our weekly newsletter : Facebook, Twitter, LinkedIn & Instagram ! If you want to be featured in the next issue of our digital magazine or if you hear a story that needs to be heard, make sure to send it to contact@3dadept.com