« Comment puis-je garantir que si j’achète un matériau, j’aurai la même reproductibilité dans douze ans ? ».
Il y a quelques années, au cœur des premières applications d’impression 3D développées par les marques de sport Armour et adidas se trouvait Lehvoss Group, qui a livré des solutions matérielles dédiées pour faire de ces applications une réalité. Lehvoss Group est dirigé par sa société mère, Lehmann&Voss&Co, et comprend plusieurs entreprises chimiques qui développent et commercialisent des matériaux spéciaux pour divers clients industriels.
En près de neuf ans d’activité dans le secteur de la fabrication additive, la société a mené la plupart de ses activités de manière relativement discrète jusqu’à récemment, lorsqu’il a mis en lumière la nécessité de la certification des matériaux pour la fabrication additive. C’est pourquoi nous avons décidé d’inviter Dr Thiago Medeiros Araujo dans cette Opinion de la semaine afin d’en savoir plus sur le parcours de l’entreprise dans le segment de la fabrication additive et sur cette certification.
Ingénieur de matériaux de formation, le premier contact de Medeiros Araujo avec la FA a été pour produire de nouveaux filaments à partir de matériaux biosourcés. Après un passage chez Airbus Group Innovations, il a rejoint Lehvoss Group il y a environ quatre ans, où il est actuellement le chef de produit international de LUVOCOM® 3F.
Vous l’avez peut-être compris, LUVOCOM® 3F est une ligne de produits qui est actuellement développée et commercialisée au sein de l’unité commerciale des matériaux d’impression 3D de Lehvoss Group. Conçue pour les processus basés sur l’extrusion, cette série de filaments haute performance offrirait une expérience d’impression facile aux utilisateurs. Le producteur développe également la ligne LUVOSINT®, une gamme de poudres pour les procédures de frittage laser et autres procédés d’impression 3D basés sur la fusion sur lit de poudre. Toutefois, c’est le filament LUVOCOM® 3F qui est au cœur du processus de certification mentionné ci-dessus.
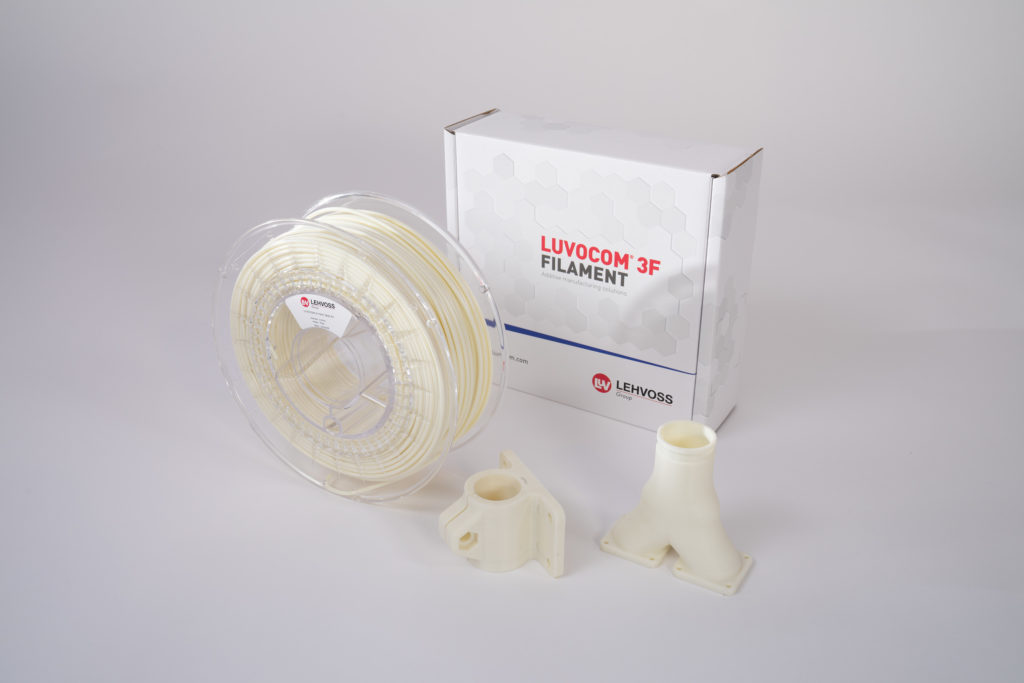
Medeiros Araujo explique que pour introduire un matériau sur un marché, il est crucial pour le producteur de s’assurer de sa viabilité. Dans cette optique, « nous avons commencé à travailler avec plusieurs fabricants d’imprimantes 3D pour garantir la compatibilité de nos matériaux avec leurs machines. Nous nous sommes rendu compte que, malgré cette compatibilité indispensable, l’adoption des matériaux n’était pas aussi rapide que prévu. Afin de fournir aux clients de meilleurs résultats, nous avons décidé d’explorer le problème sous un angle différent, cette fois avec une seule question en tête : Comment puis-je garantir que si j’achète un matériau, j’aurai la même reproductibilité dans douze ans ? Pour explorer cet angle, nous avons dû collaborer avec un fabricant d’imprimantes 3D pour la certification de nos matériaux », ajoute-t-il.
Tout a commencé par un « NON »
La collaboration avec l’équipe d’Ultimaker ne s’est pas déroulée aussi fluidement qu’on aurait pu penser.
« D’abord, ils ont dit ‘Non, ça ne va pas marcher’. Après beaucoup de persévérance et d’explications, nous avons finalement décidé de définir les modules de la certification et la manière dont nous allions tester la qualité des matériaux. Nos filaments ont été testés dans une fabrication spéciale de filaments, et dans le laboratoire Ultimaker pour s’assurer que tous les résultats des tests soient les mêmes. Nous nous sommes ensuite adressés à TÜV SÜD qui a certifié le processus d’impression 3D en utilisant la combinaison du filament LUVOCOM® 3F et de l’imprimante Ultimaker », rappelle Medeiros Araujo.
Lorsqu’on lui demande quels sont les éléments essentiels à évaluer dans un tel processus, le chef de produit fait remarquer : « Dans notre cas, il était crucial d’examiner de plus près la précision géométrique, la résistance aux tests, les produits chimiques et les émissions. En tant que producteur de matériaux, nous devons nous assurer que nos matériaux ne changent pas, afin de garantir qu’il s’agit d’un processus certifié. Cela signifie que le matériau qui a été certifié l’année dernière doit être en mesure de fournir les mêmes résultats en termes de propriétés, de composition et de comportement pendant la production, l’année prochaine ou dans cinq ou six ans. Pour s’en assurer, il est important de se soumettre continuellement à ce processus de certification. D’autre part, l’émission de tests permet de garantir que ceux qui utilisent leur imprimante 3D dans un environnement proche peuvent le faire en toute sécurité. »
Il convient de noter que cette certification n’est pas valable pour toutes les imprimantes 3D. L’équipe commerciale des matériaux d’impression 3D travaille actuellement à l’élargissement de la gamme de matériaux et de machines qu’elle pourrait faire certifier.
Un regard plus attentif sur la fixation directe dans l’impression 3D
Notre conversation avec l’expert de Lehvoss Group met également la lumière sur le concept de fixation directe dans le plastique pour les composants imprimés en 3D.
Que ce soit pour la production de petites séries ou pour des prototypes, les opérateurs doivent souvent s’assurer que les composants en plastique imprimés en 3D sont bien intégrés dans une structure globale, comme c’est le cas pour les produits moulés par injection.
Étant donné que les matériaux choisis lors de la fabrication jouent également un rôle clé dans cette connexion, Medeiros Araujo a expliqué à 3D ADEPT Media qu’ils ont travaillé avec EJOT GmbH & Co. KG, un expert en technologie de fixation.
Les deux équipes ont travaillé sur des bossages de vis imprimés en 3D. Pour faire simple, « le procédé consiste à imprimer directement dans la pièce à fixer et par la suite, on visse pour obtenir la même résistance que ses homologues moulés par injection », précise notre invité dans cette Opinion de la semaine.
« La vis EJOT EVO PT® a été utilisée pour les expériences de jointage. Outre les caractéristiques de positionnement optimisées de ce type de vis, le couple d’installation est presque indépendant de la profondeur d’insertion. Comme un certain niveau d’imprécision dimensionnelle se produit toujours dans l’impression des trous de perçage en raison de la procédure utilisée, le trou pour la vis (trou de guidage) a été recalibré dans chaque cas afin d’observer une norme expérimentale fiable. Tous les bossages pour les essais ont été produits en utilisant la technique FFF. Le calibrage du trou de la vis sur le bossage imprimé a montré que si l’on choisit une géométrie techniquement pratique pour le trou de guidage, on peut obtenir des valeurs de fixation de la vis presque identiques à celles du bossage moulé par injection », peut-on lire dans le rapport de la société.
Perspectives futures
Lehvoss Group dispose désormais d’une solide expertise en matière de polymères à haute performance. Le producteur envisage maintenant d’élargir son portefeuille avec des matériaux ignifuges.
« Nous travaillons également à la certification de matériaux pour l’industrie ferroviaire. Nous avons déjà développé trois matériaux à cette fin ; les produits sont basés sur les polymères PEI, PPS et PA », souligne Medeiros Araujo.
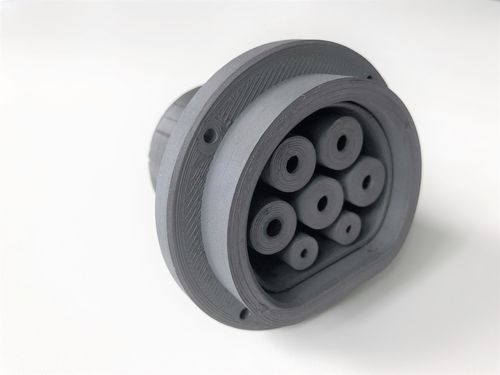
Les composants des véhicules ferroviaires sont soumis à des exigences particulières en termes de comportement au feu. En Europe, la norme applicable est la norme EN 45545, qui contient différents tests simulant le comportement des matériaux en cas d’incendie. Parmi les paramètres déterminés figurent la densité de la fumée et l’indice d’oxygène. Selon le domaine d’application, les exigences sont plus élevées que celles de l’industrie aéronautique. La classification se base sur les niveaux de danger (hazard levels = HL1 – HL3) ainsi que sur les applications et les exigences (classes R = requirements).
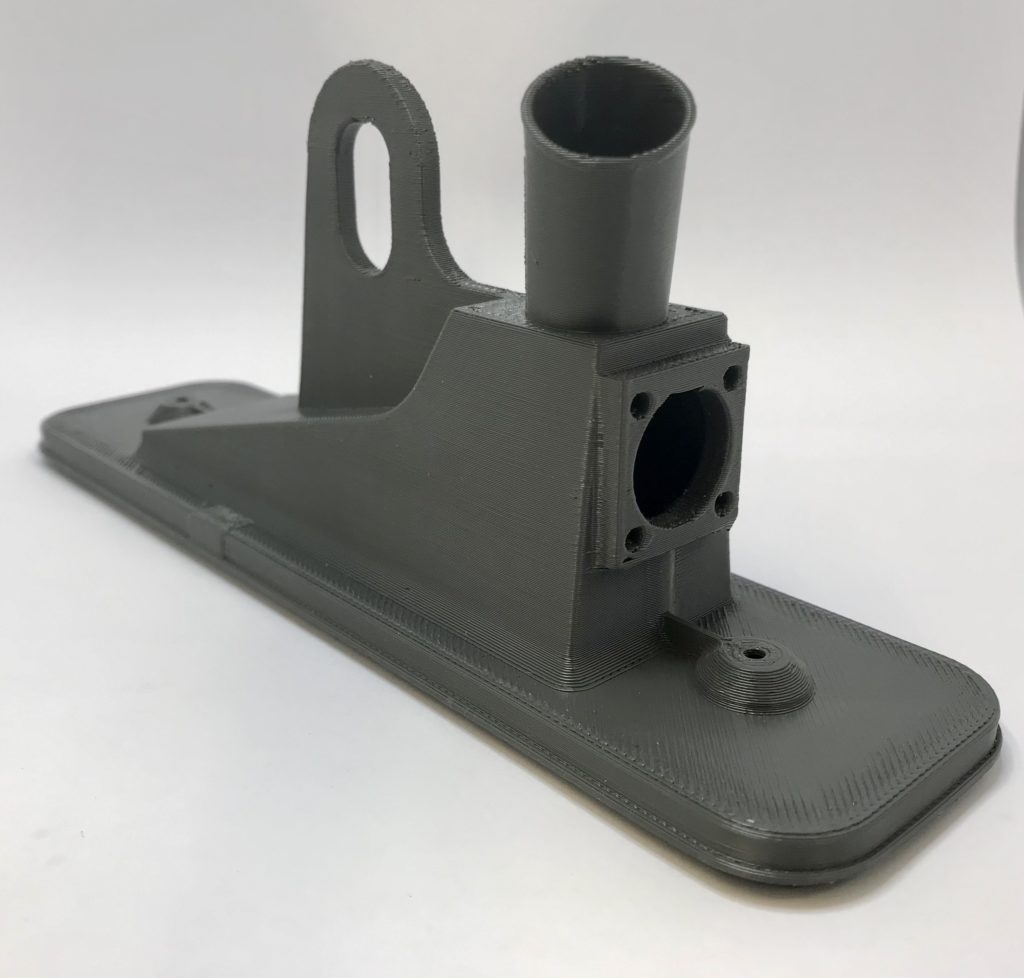
Dans la gamme de produits de l’entreprise, les produits LUVOCOM 3F PEI 50236 GY, LUVOCOM 3F PPS CF 9938 BK et LUVOCOM 3F PAHT KK 50056 BK FR répondent à R22 et R23 dans HL 1, HL 2 et HL3 et conviennent donc à un large éventail d’applications.
Enfin, en tant qu’entreprise de matériaux, la durabilité est également au cœur des principales préoccupations de Lehvoss Group. « Nous travaillons actuellement sur la manière d’aborder cette question. Nous espérons que d’ici le milieu de l’année, nous sortirons des produits qui prennent également en compte une approche d’économie circulaire », conclut Medeiros Araujo.
N’oubliez pas que vous pouvez poster gratuitement les offres d’emploi de l’industrie de la FA sur 3D ADEPT Media ou rechercher un emploi via notre tableau d’offres d’emploi. N’hésitez pas à nous suivre sur nos réseaux sociaux et à vous inscrire à notre newsletter hebdomadaire : Facebook, Twitter, LinkedIn & Instagram !