Joyson Safety Systems a collaboré avec CRP Technology pour la production additive des boîtiers d’airbags.
Cela fait un siècle que Joyson Safety Systems fournit des composants critiques pour la sécurité sur les marchés automobiles et non automobiles. L’entreprise conçoit, fabrique et vend des composants tels que des coussins gonflables, des ceintures de sécurité, des volants et des systèmes électroniques de sécurité.
Dans le cadre d’un projet qui consiste à explorer comment tirer parti de la technologie de FA pour la production de conteneur d’airbag, l’équipe de JSS était à la recherche du matériau composite idéal qui aurait été utilisé pour cette production. Leur objectif était de trouver un matériau dont les propriétés seraient similaires à celles du polyamide avec un renforcement de 40% de fibres de verre, qui était auparavant exploité avec les procédés de fabrication conventionnels pour cette fabrication.
La performance de la partie boîtier de la DAB est extrêmement essentielle, du fait qu’il s’agit d’un composant de sécurité dans le véhicule. Cela signifie que l’airbag se gonflera lors d’un accident soudain dans une période assez courte d’environ 30 à 50 ms (milliseconde) pour éviter que le passager ne soit blessé. Le boîtier DAB maintient l’ensemble du système Airbag en place, il est donc également un composant essentiel de base du système.
Selon Samer Ziadeh et Daniel Alt de l’équipe Core innovations de Joyson Safety Systems, la fonction du boîtier DAB est de résister à une grande quantité de charges dynamiques en plus de maintenir le gonfleur et le coussin d’air fixé en place pendant et après le déploiement du système d’airbag. Cette charge est développée en raison de la pression requise pour gonfler l’airbag, de sorte que les fortes contraintes seront directement appliquées sur le système d’airbag et plus particulièrement sur le boîtier DAB.
Les procédures d’essai sont normalement effectuées dans une plage de températures comprise entre -35°C et +85°C.
Ainsi donné, le matériau utilisé pour la fabrication de la pièce devrait avoir une résistance mécanique, une résistance aux chocs et une stabilité thermique suffisantes pour fonctionner correctement dans différentes conditions d’essai.
Ziadeh et Alt ajoutent : « Les différentes études de marché que nous avons menées pour trouver le matériau et le procédé additif les plus appropriés pour satisfaire les performances exigées, nous ont orienté vers les matériaux composites Windform ® TOP-LINE de CRP Technology et, notamment vers Windform ® SP. »
CRP Technology a développé une gamme précise de matériaux composites et a acquis une solide expérience à travers diverses collaborations dans l’industrie automobile et des motos de sport.
Pour rappel, le Windform® SP est composé de grades de polyamide PA et renforcé par de la fibre de carbone. Disponible sous forme de poudre, une fois traité par le procédé d’impression 3D SLS, il offre les propriétés souhaitées pour produire un prototype fonctionnel du boîtier DAB.
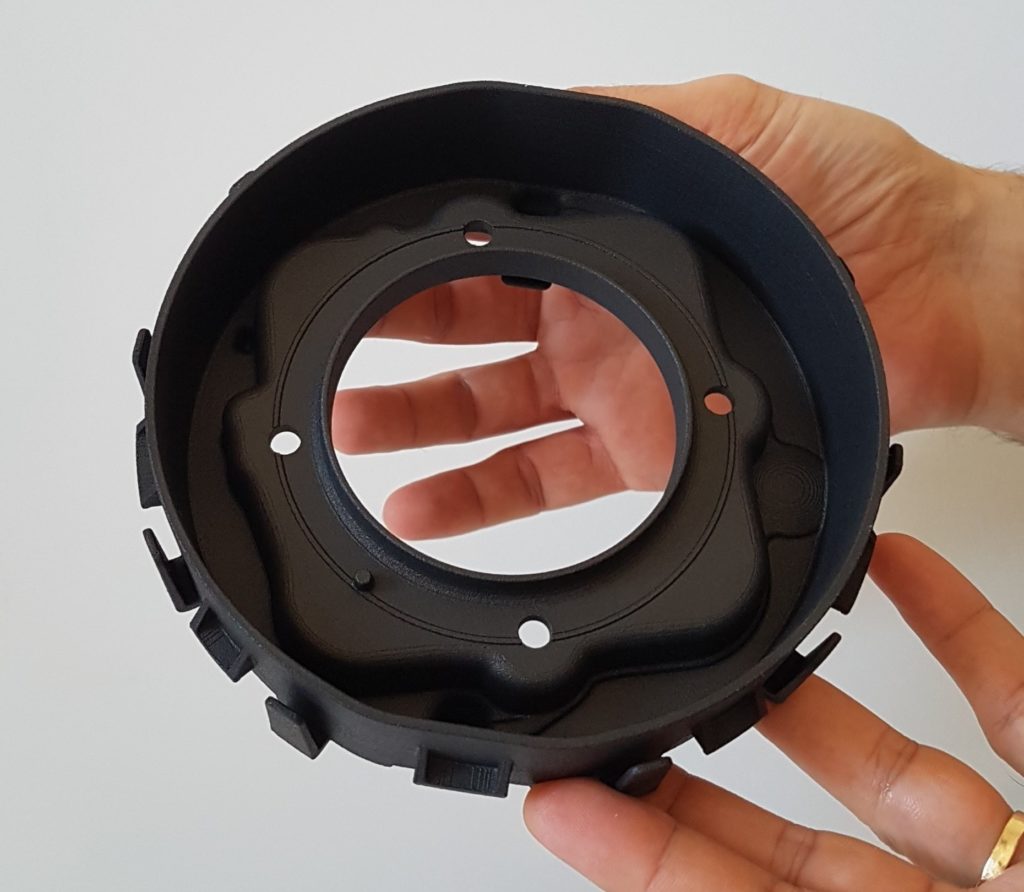
Les tests de la pièce menés par l’équipe montrent de bonnes performances mécaniques en termes de résistance mécanique et de résistance aux chocs ainsi qu’une bonne stabilité thermique entre une gamme de températures basses et élevées (RT ; 23°C, -35°C & 85°C).
Satisfaits des résultats de ce projet, Ziadeh et Alt envisagent déjà une coopération plus poussée avec CRP Technology.
Remember, you can post free of charge job opportunities in the AM Industry on 3D ADEPT Media or look for a job via our job board. Make sure to follow us on our social networks and subscribe to our weekly newsletter : Facebook, Twitter, LinkedIn & Instagram ! If you want to be featured in the next issue of our digital magazine or if you hear a story that needs to be heard, make sure to send it to contact@3dadept.com