Do you remember how in a previous dossier of 3D ADEPT Mag, we explored additive manufacturing candidacy for production applications? One of the frameworks identified to assess if it is was necessary to go down the AM route for series production is the design analysis approach. This approach consists in identifying parts where AM could be applied efficiently, and among the companies that have dedicated their core business to this step of pre-production, there is CASTOR.
For this Opinion of the Week, we sat down with Omer Blaier, Co-Founder & CEO of the Israel-based start-up to learn how their software helps industries achieve part identification for Additive Manufacturing.
Blaier got to know Additive Manufacturing when he was working at Stratasys. Mechanical Engineer by training, he founded CASTOR, in 2017, together with Elad Schiller who currently serves as the CTO of the company. During its stealth mode, the company secured a funding round, backed by several investors across the world including Evonik, that also supported its official launch onto the AM market.
“During my time at Stratasys, I found out that most companies that printed with series production in mind, did not see 3D printing as an option to reduce costs. We have therefore decided to address this issue. We exist to help manufacturers decide where and when they can save time and money in their production environment. To do so, we have been developing three software products that help industries unlock the benefits of industrial 3D printing:
- Castor Light, a cloud-based solution where companies can upload their build of materials, the list of parts they want to explore – whether it is a full product or a large assembly –. Thereafter, they conduct a short assessment to discover where it makes sense to use AM from a technical, economical perspective.
- Castor Enterprise comes next. This is the main product of CASTOR. There is an on premise version that one can be installed on a computer. It has been developed based on the features of Castor Light. However, it distinguishes itself from the previous product in that it recommends the users what design changes they might want to apply on the part. This module can provide part consolidation, which comes with a key advantage: the ability to identify weight reduction opportunities – although we are not a generative design and TO company. The software is also very good at identifying parts that have extra materials, while enabling full customization of calculation structure, as well as ROI calculations for 3D printers. In a nutshell, this software product is about helping engineers explore their DfAM opportunities.
- Thereafter comes Castor White Label, our third product. This is a comprehensive infrastructure designed for large customers in the AM arena. The latter can use it to provide a service to their customers as a “pre-sale tool”. By using this platform, they enable their customers to upload parts and see if it makes sense to use AM. Evonik and Nexa3D are a few examples of companies that currently leverage this platform. The product is powered by CASTOR but is customized at all levels so that each company can use it under their brand”, Blaier states from the outset.
Although one may understand that 3D printer manufacturers, OEMs, parts or material producer are the primary targets that can utilize CASTOR’s products, Blaier also notes that they work with service bureaus as partners. “The end-result is to guide manufacturers towards service bureaus so that they can print the final parts. We are not a marketplace but we have a network of service bureaus. We connect the manufacturer to the service bureau that will get the part eventually to the manufacturer’s factory, which means, CASTOR acts as a traffic provider for service bureaus”, he adds.
Baier’s description of CASTOR’s products also reveals that the company cannot be exclusively categorized as a “design software”, nor a “simulation/workflow software”. It is in-between the “design” and simulation workflow as the software can only redesign where there is an opportunity.
“I think, we should create a new category of software profiles for our products, a category that I would call “parts identification model”. We take the design as it is, as it was designed in the CAD software and give an assessment out of those parts. Our work basically fills the gap between the CAD and the workflow management tools”, the CEO outlines.
So, how does CASTOR help manufacturers identify the right part for AM?
As a reminder, using CASTOR’s platform, engineers have the ability to upload a single file that contains a whole product design or an inventory list. The assessment that follows is based on four pillars: materials, geometry analysis, costs analysis and stress analysis.
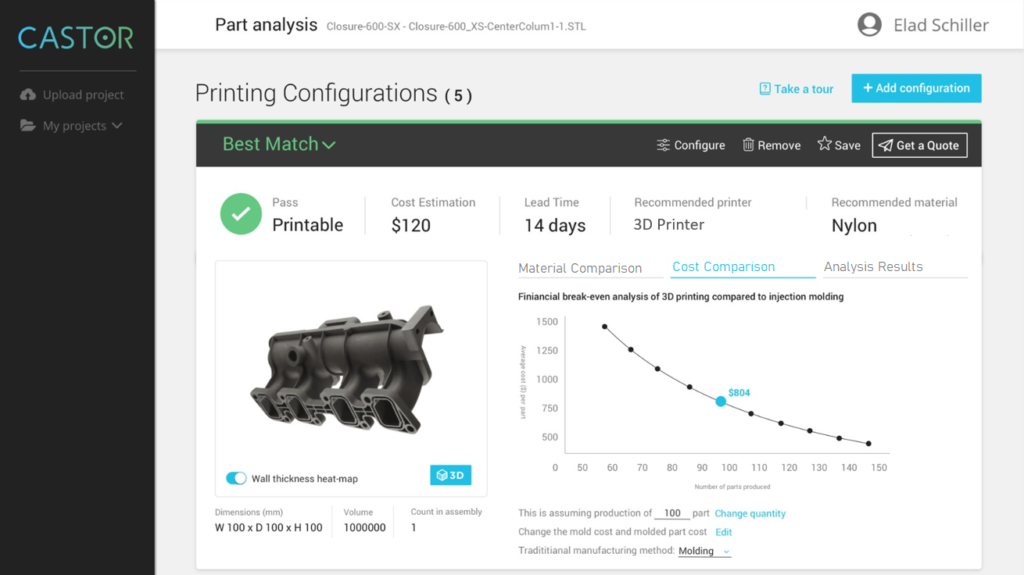
A virtual tour of the platform reveals that the “materials” option helps the user identify the best materials for a given production. As you know, no matter what manufacturing process is utilized, each part should deliver different levels of ductility, density, elasticity and resistance, to achieve the desired functionalities. The goal to achieve these functionalities is to choose the material that will deliver the required mechanical properties. This step is even crucial since switching production from conventional manufacturing to AM, may also result in a change of mechanical properties.
The “geometry analysis” on the other hand, helps the user identify a printer that can print these materials. According to Blaier, beyond the part geometry that needs to be assessed, there is a whole range of limitations that users should consider, hence the importance to perform a tolerance analysis, or to check the minimum wall thickness threshold or the ratio between height, depth and thickness..
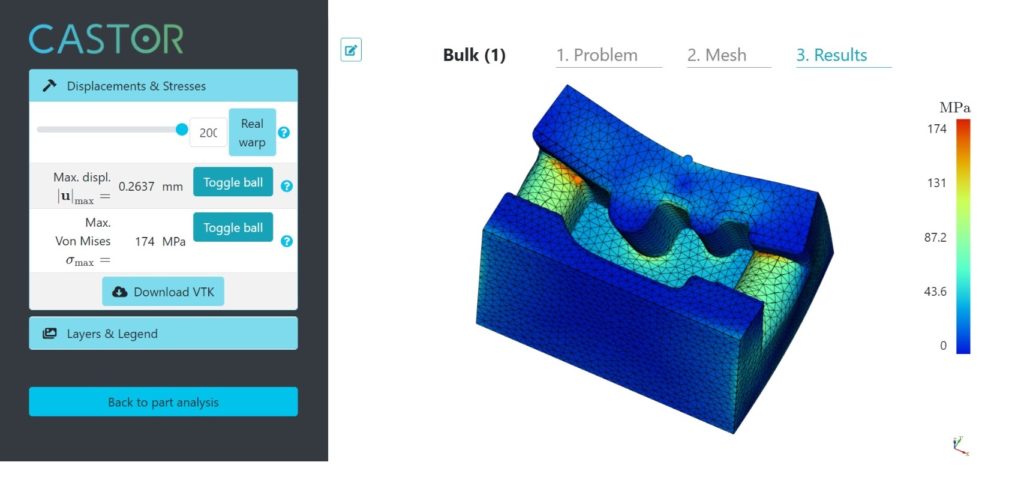
The “cost analysis” comes to respond to the question: “How much I am going to spend for this production?” “It is a great means to assess and compare conventional & AM processes”, Blaier notes. Indeed, in most cases to date, conventional manufacturing processes such as injection moulding make sense for volume production whereas the financial output is more interesting when AM is used for low volumes. This break-even point analysis is marked by a “green V” line on the CASTOR platform that indicates the ideal manufacturing route to follow.
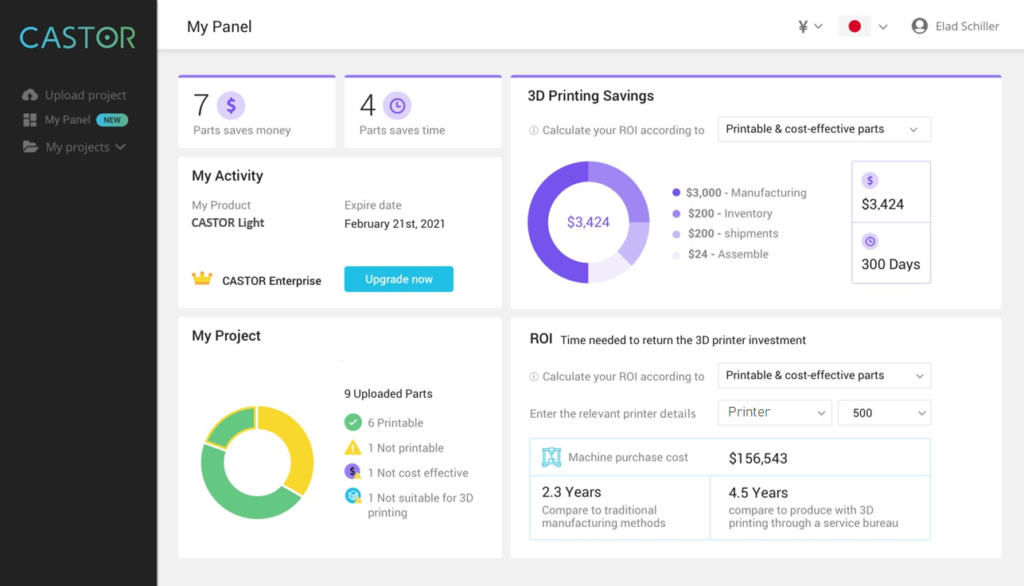
The last step of this assessment is “stress analysis”. “Based on external forces of the parts; it helps to understand how the part will perform in real life”, our guest in this OOW explains.
Speaking of a tangible example, Blaier explains how their team played a pivotal role in the process which led to the integration of a metal 3D printed production part for one of their customers. As part of this project that took 9 days using their automated tools, rather than 9 weeks, by proceeding manually, CASTOR helped the customer achieve a 50% cost saving for a low volume production as compared to the cost of the traditional process.
In the same vein, speaking of areas where 3D printing/AM can make a difference at first glance, the expert recognizes that the current industrial 3D printing world is led by automotive, aerospace, and medical device applications but he finds “ the industrial machinery segment” particularly appealing. This segment includes large infrastructures like food and beverage companies, beer companies that often require a low volume production for their industrial and sometimes complex equipment.
“At CASTOR, our focus area is those non-sexy parts that companies want to produce; the parts that surround the engine itself – the parts that are found in peripheral areas”, he completes.
And the next step…?
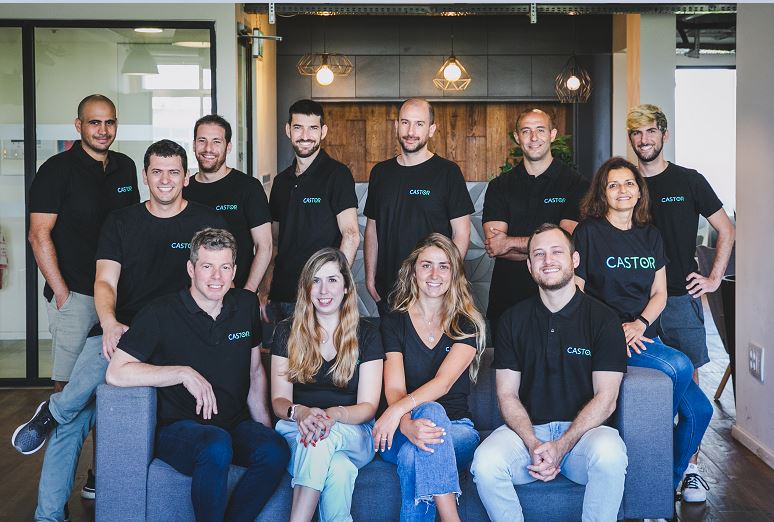
As a young company, there is no doubt, CASTOR still has a long road to go but the company is definitely on the right step. With 15 employees that share the same vision on board, the company is working hard to enhance its existing solutions and to develop new products for the industry. One of their priorities for the short-term is to develop a tool that will help manufacturers identify if metal parts can go the CNC machining route after the printing process. The other one is to enhance interoperability, the integration of their platform within the environment of other software providers. And I have to say, I can’t wait to see who will be the first technology partners of this project.
Remember, you can post job opportunities in the AM Industry on 3D ADEPT Media free of charge or look for a job via our job board. Make sure to follow us on our social networks and subscribe to our weekly newsletter : Facebook, Twitter, LinkedIn & Instagram ! If you want to be featured in the next issue of our digital magazine or if you hear a story that needs to be heard, make sure you send it to contact@3dadept.com