Carbon has introduced a new software that will enhance the way its subscribers design and produce lattices. Named Design Engine™ software, the new tool has served for the design of critical lattice products before this formal announcement.
The truth is, despite AM’s ability to produce latticed parts with better performance than those produced via conventional manufacturing processes, traditional design tools remain limited in their AM support. This lack of traditional design tools is even important when it comes to complex geometries like lattices which does not facilitate the design of functional parts.
To address this issue, Carbon has imagined a software platform that will facilitate collaboration on design projects with customers.
“Traditional CAD tools have not kept pace with the innovation of 3D printers and materials. This lack of progression limits the ‘idea to design’ stage of the product development lifecycle. With the release of Design Engine to all Carbon subscribers, we are helping designers iterate through their design thinking, faster,” said Phil DeSimone, Chief Product and Business Development Officer. “On average it can take 18 – 24 months to bring a consumer product to market. But when we put the best design tools, 3D printers and materials in the hands of designers and manufacturers, we’ve seen our customers accelerate the development of innovative new products – going from idea to finished designs to production in less time.“
Design Engine™ software will enable users to leverage the computational power required to develop complex shapes at a fast pace without requiring local resources and without sacrificing quality. The cloud-based application is equipped with an intuitive user interface and allows for the production of five different types of conformal lattices.
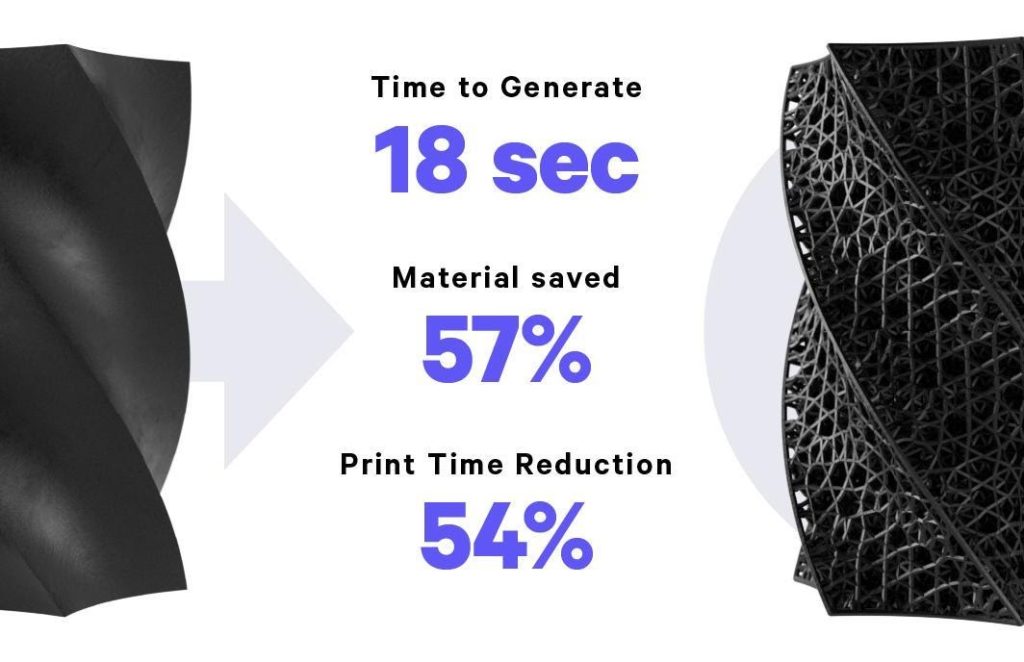
According to the manufacturer of DLS 3D printing processes, Design Engine™ is the ideal software candidate for the development of conformal lattices that robustly populate even the most challenging design surfaces, eliminating the tedious design revisions post-generation.
Furthermore, two other benefits of the platform include the prediction of lattice performance prior to lattice generation, enhancing this way design optimization as well as built-in guidance to help engineers develop successful parts.
Projects that we know that have benefited from Design Engine™ include the Resolution Medical Lattice Swabs developed for COVID-19 testing, Specialized S-Works Power Saddle with Mirror technology, and CCM Super Tacks X helmets.
“Working with Carbon allowed CCM to leverage its innovation pipeline to launch something the industry had never seen before in the Super Tacks X helmet. Carbon technology has evolved, enriched, and accelerated our approach to product design allowing us to go from idea to production at record pace,” said Jeff Dalzell, Vice President of Product Creation at CCM Hockey. “Within days of prototyping with the Design Engine, we gained creative insights into even more applications for performance-oriented lattices in our future product lines.”
Remember, you can post job opportunities in the AM Industry on 3D ADEPT Media free of charge or look for a job via our job board. Make sure to follow us on our social networks and subscribe to our weekly newsletter : Facebook, Twitter, LinkedIn & Instagram ! If you want to be featured in the next issue of our digital magazine or if you hear a story that needs to be heard, make sure to send it to contact@3dadept.com