Do you remember that feeling you have, when you go out and realize you forgot your phone? Some are willing to go back home/wherever they were, to take their phone. We certainly agree with one thing: mobile devices have changed the way we consume products/information/work, in one word, live. The world has evolved so fast that, almost everything we do today requires the use of mobile devices. Interestingly they have also changed the way, we use technology and design products. What’s that impact in manufacturing?
In the past decade, technological improvements have spurred tremendous changes in the way design professionals work. CAD (Computer-aided Design) technologies that were considered an option ten years ago, are now essential today. However, when it comes to manufacturing, it is no secret that modelling a product using a CAD software is the primary step to go through before the manufacturing itself. Do we achieve the same design by working on a mobile device? Is the quality the same?
First, it should be noted that the most common mobile devices that are used nowadays include: smartphones, tablets, laptop computers, smart watches, e-readers and handheld gaming consoles. In the design world, the primary device used for modelling is the laptop. The following lines will discuss the impact in manufacturing when using tablets as part of this exercise.
According to Sophia Georgiou, Chief Designer and Founder of Morphi, 3D modeling and design software, designing in 3D on tablets is more frequent than phone screens.
Together with her team, Georgiou has been making Morphi for four years. The software is used on iPad and by people of all skill levels in more than 125 countries.
What are therefore the advantages of “CAD on mobile devices”?
The first advantage people are looking at, while leveraging CAD on mobile devices is accessibility. This advantage is more obvious for those who leverage full-cloud CAD. Indeed, they can access their work, anytime and anywhere, even on devices they don’t own.
At the design level itself, the founder of Morphi talks about the possibility to not be limited by creativity.
“Users can design from anywhere inspiration strikes them, like on the subway or while outside, whereas laptops are often not as portable”, she explains. Morphi advocates 3D modelling as an empowering tool. That’s why, the company has developed other 2D and 3D drawing tools to improve the user experience through a touch interface.
To illustrate the capabilities of such type of modeling tools, the Chief Designer mentions the 3D printed Named Dress designed by Sylvia Heisel, a wearables specialist. Unveiled last year, the Names Dress is a compostable couture gown that is on display at the Ferragamo Museum in Italy. Heisel utilized Morphi on iPad to write the names of over 300 women in STEAM fields on the touchscreen. She extruded them in 3D in the app and fusing them together to form one continuous piece.
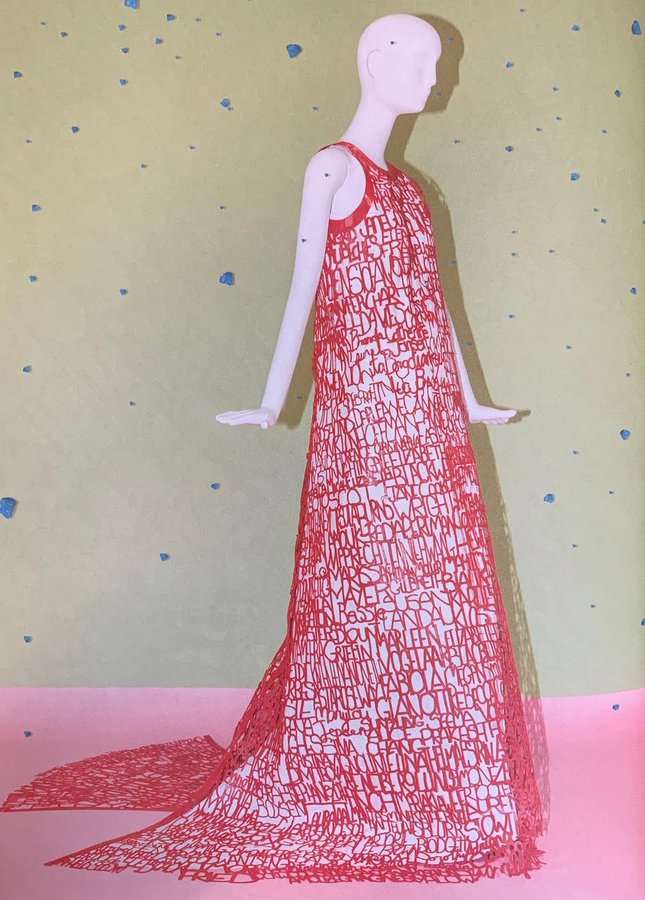
Sophia Georgiou brings out interesting arguments but so far, only gives examples that might give the impression that CAD on mobiles is only useful for artists.
In a more industrial environment, engineers “need to resolve design issues on the GO & stay on schedule”. Imagine an engineer working in a SME. With a myriad of responsibilities, his position might require him to run between different sites (at suppliers and/or customers location) to investigate manufacturing issues.
Those responsibilities are not limited to reviewing drawings and rotating 3D models. They require active modifications to designs. According to Siemens, “there are other prudent reasons to take immediate action. Given the fact that the amount of time they have at the desk is shrinking, engineers can’t afford to let desk-based to-do lists build up while working remotely. Such a backup in design tasks can unnecessarily delay the overall product development process. They need to resolve them immediately, as much as possible, while they are on the go.”
Moreover, as the technology increases, the evolution of CAD on mobile devices has led to the use of AR capabilities that enable a better visualization of 3D models (without 3D printing or manufacturing) and a more immersive experience for users. Georgiou totally agrees with this argument as she relates:
“We started developing our Augmented Reality viewer for Morphi on iPad back in 2016 and released our first feature in 2017 which was a very simple way to open your camera and place your 3D model in your environment. After the release of Apple’s ARKit in various stages, we have been able to create more immersive ways for our users to directly 3D model and visualize their designs in a variety of ways in our iPad apps. We also have a new iPhone app, Morphi AR for iPhone, that will be released next week [from February 17th] where you can import 3D models created in any CAD software and place and edit them in AR using an iPhone.”
This list of benefits shows that CAD on mobile devices enables a certain flexibility in the way a designer works but there is still a big gap with their use on desktop workstations.
Other considerations to take into account
To run smoothly, CAD applications need processing power, memory, hard disk space and high graphics performance.
An engineer will quickly depict that 3D models of complex parts (with hundreds of pars) require several computer resources in each of the aforementioned categories. In this case, the ability to produce properly and fast will depend on the performance of the platform leveraged.
Be it on a desktop workstation or a tablet, without the proper compute resources, simple tasks such as loading, modifying or manipulating can lead to time lags or delays.
Given their high capacity and upgradeability for processing power, and other resources, desktop workstations are usually – and will certainly remain – the best match for the largest 3D models designed in CAD software.
Over time, tablets have managed to meet these performance expectations, and to professionals that complain about smaller physical graphics screen, they are given the possibility to stream the display to a larger screen. Is it enough?
“Processors, screen size. device connectivity, getting used to touch screen as opposed to a mouse and a lack of accuracy in 3D modeling tools are sometimes discussed as limitations to 3D modeling on mobile devices. However, we think the biggest limitation is probably mindset. Mobile devices are powerful computers and impactful designs are created on them every day. Users have even told us that designing in 3D on mobile devices enhances their creativity because they associate it with experimentation and can see things in new and interesting ways”, said Morphi’s founder speaking of limitation of CAD on mobile devices.
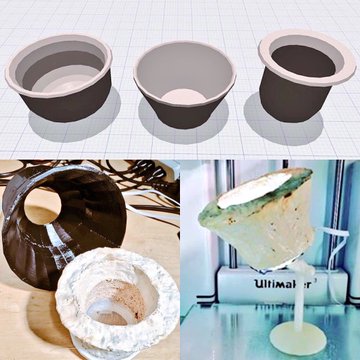
Speaking of these differences with desktop workstations, a research carried out by Siemens explains that finger gestures are another consideration to take into account, and even an advantage for productivity for those who leverage CAD on tablets:
“Finger gestures on a touch sensitive screen and other peripheral-less interactions on tablets present an opportunity for productivity improvements. Instead of plugging in a physical keyboard and mouse, which may not be possible in some use cases, users can enter text or interact with models on the touch screen directly. Besides supporting the software with the right computation resources, some software providers have retooled the interface and interaction of their CAD application to leverage multi-touch interfaces”.
Productivity vs Freedom: is there a balance?
This article does not question the use of CAD on mobile devices. People do really do CAD on mobile devices. That’s an undeniable fact. But who are they? The way CAD is used on mobile devices is not the same from one user to another.
While the use of these tools will strongly influence productivity for enterprises, for individuals, the question will turn around the ability to materialise a 3D model “the way they want”.
For Morphi’s Sophia Georgiou, “people should use whichever tools they feel will help them better visualize, evolve and share their ideas. It is not about choosing to model in 3D on a desktop versus mobile device – they can do both seamlessly now. It’s more about people being empowered to create the things that matter to them and their communities.”
This reflection might not always be the same for organizations. Productivity is the key to release a product on time, be it evolutionary or revolutionary. Finding from Siemens PLM Study (2015) show that on average only 55% of development projects are released on time, a very low score for those who aim to be the “first” on a given market.
Despite the complexity due to the design of some complex parts, CAD on mobile devices aims to resolve issues earlier and to stay on schedule, therefore to improve this percentage. The question is: what is the true reality for these companies?
This dossier has originally been published in the March – April Issue of 3D ADEPT Mag.