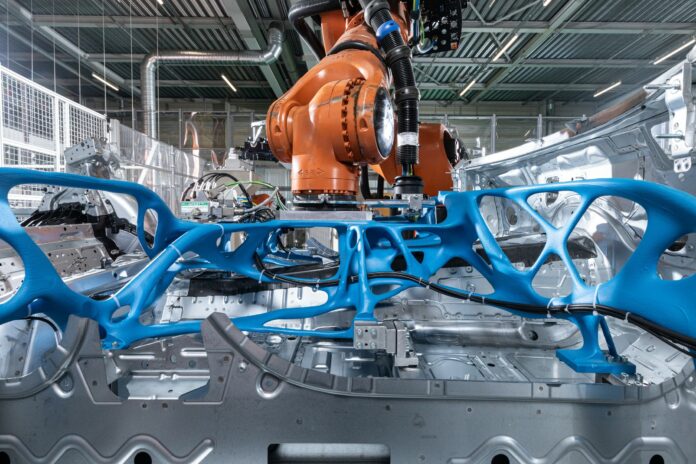
Le constructeur automobile BMW Group fait le point sur l’évolution de son utilisation des technologies de FA. Après trois décennies d’expérience en tant qu’utilisateur de la FA, une chose est sûre : l’entreprise ne cesse d’élargir son champ d’expertise – des orthèses sur mesure pour les employés et des aides à l’enseignement et à la production aux grandes pinces robotisées au poids optimisé, utilisées pour des éléments tels que les toits en PRFC et les assemblages de planchers entiers.
À ce jour, le « Campus de fabrication additive » de BMW Group à Oberschleißheim a fait état de la production de 300 000 pièces en 2023 ; cela ne tient pas compte des 100 000 pièces imprimées supplémentaires produites par an dans toutes les usines qui forment le réseau de production mondial, de Spartanburg et des usines allemandes aux sites d’Asie.
« Outre la procédure de fabrication additive directe, la société utilise également l’impression 3D sur sable pour créer des moules depuis de nombreuses années sur son site de Landshut. Cette technologie est généralement utilisée pour fabriquer des moules de prototypes, ainsi que pour la production à grande échelle de composants pour les moteurs haute performance. Un autre domaine d’application très intéressant est désormais celui des aides à la production à grande échelle », explique Klaus Sammer, responsable de la planification des produits et des processus pour Light Metal Casting.
Priorité à la production de pinces
Depuis plusieurs années, le centre de construction légère et de technologie du BMW Group à Landshut utilise un élément de préhension particulièrement grand, qui a été fabriqué par le processus d’impression 3D. Pesant environ 120 kilogrammes, la pince pour robot peut être fabriquée en seulement 22 heures et est ensuite utilisée sur une presse pour la production de tous les toits en PRFC des modèles de BMW M GmbH. La presse est d’abord chargée de la matière première CFRP. Il suffit de faire pivoter la pince de 180 degrés pour retirer les toits finis. Par rapport aux pinces conventionnelles, la version fabriquée par impression 3D est environ 20 % plus légère, ce qui prolonge la durée de vie des robots et réduit l’usure du système ainsi que les intervalles de maintenance. L’utilisation combinée de deux étapes a également permis de réduire le temps de cycle. L’une des caractéristiques uniques du préhenseur robotisé est la combinaison idéale de deux processus d’impression 3D différents. Alors que les pinces à vide et les pinces à aiguille destinées à soulever la matière première en PRFC sont fabriquées par frittage sélectif par laser (SLS), la grande coque du toit et la structure portante sont fabriquées par impression à grande échelle (LSP). L’impression à grande échelle peut être utilisée pour produire des composants de grande taille de manière économique et durable. Le processus utilise des granulés de moulage par injection et des plastiques recyclés, tandis que les matériaux résiduels du CFRP peuvent également être utilisés et recyclés. Par rapport à l’utilisation de matières premières primaires, les émissions de CO2 lors de la fabrication de la pince sont réduites d’environ 60 %.
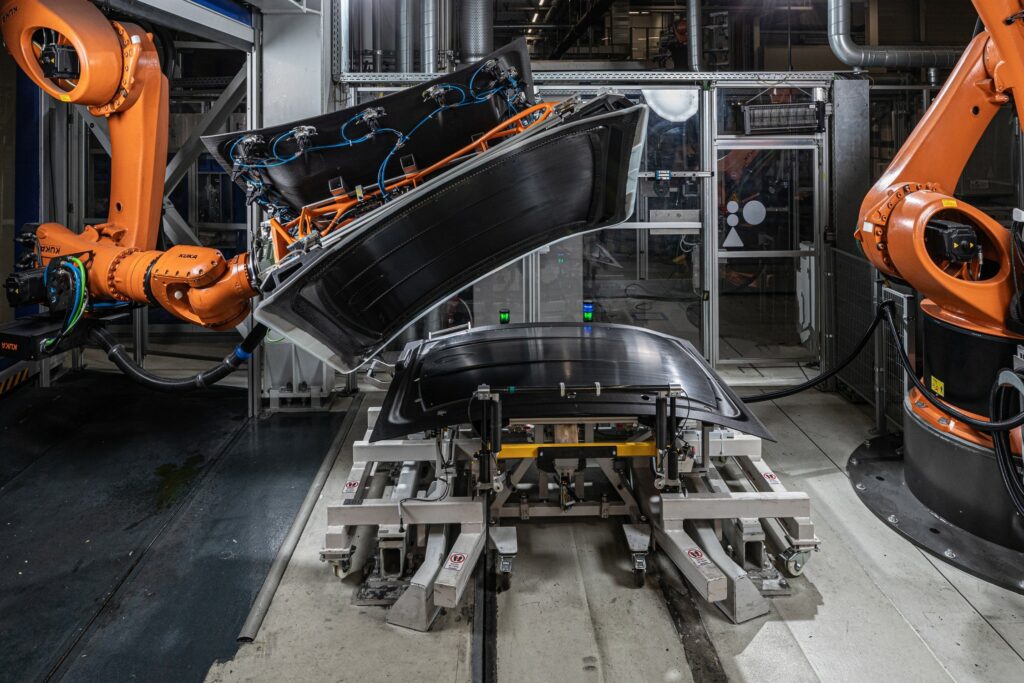
Au cours de l’été 2023, une nouvelle génération de pinces encore plus légères a été introduite. Pour ce faire, l’ancien concept de pince a été analysé et optimisé sur le plan topologique – c’est ainsi qu’est né le robot de préhension bionique. Celui-ci combine la coque de toit de l’imprimante LSP avec des aspirateurs SLS et une structure portante optimisée sur le plan bionique. Pour ce faire, un moule avec des noyaux imprimés est utilisé pour le moulage en sable. Ce moule est ensuite coulé avec la structure complexe en aluminium. Le nouveau préhenseur est 25 % plus léger que son prédécesseur, ce qui signifie que l’ensemble du processus de fabrication d’un toit en PRFC de la BMW M3 peut être réalisé avec un seul robot, au lieu de trois comme c’était le cas auparavant. Aujourd’hui, des pinces doubles fabriquées individuellement au sein du BMW Group, grâce à l’impression 3D, sont utilisées pour tous les toits en PRFC à l’usine BMW Group de Landshut.
Cependant, l’entreprise va maintenant plus loin à l’usine BMW Group de Munich. Depuis peu, les premiers exemples d’une pince robotisée bionique sont utilisés dans l’usine mère. Ce préhenseur peut tenir et déplacer l’ensemble du plancher d’une BMW i4. Pour le préhenseur du plancher, l’impression 3D est utilisée pour créer un moule de moulage en sable, qui est rempli d’aluminium liquide. Le support est optimisé en termes de poids et de capacité de charge maximale et ne pèse, avec tous les éléments supplémentaires, que 110 kilogrammes. Il est donc environ 30 % plus léger que le modèle conventionnel précédent. La fabrication par moulage au sable et en aluminium permet de représenter des structures complexes optimisées en fonction de la charge. Il en résulte une réduction maximale du poids, ce qui permet à moyen terme d’utiliser des robots de levage lourds plus petits et plus légers, qui consomment moins d’énergie et réduisent ainsi les émissions de CO2.
N’oubliez pas que vous pouvez poster gratuitement les offres d’emploi de l’industrie de la FA sur 3D ADEPT Media ou rechercher un emploi via notre tableau d’offres d’emploi. N’hésitez pas à nous suivre sur nos réseaux sociaux et à vous inscrire à notre newsletter hebdomadaire : Facebook, Twitter, LinkedIn & Instagram !