The manufacturer of large-format 3D printers BigRep has unveiled DRYCON, a drying, storage & annealing machine for optimal filament performance. Its dual chamber system perfectly complements industrial 3D printers to offer high-quality printed parts.
The announcement follows the launch of the Expansive Altra 280 and the debut of the company on the stock exchange.
DRYCON addresses one of the common issues regarding the moisture content in filaments, which creates problems during the extrusion process and poor-quality prints. The system will ensure optimal drying conditions by periodically changing air that continues to recycle back while conserving energy & helping them operate at peak performance.
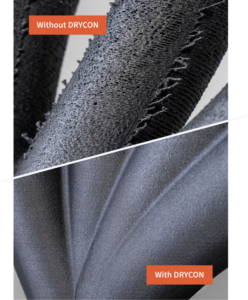
The notable characteristic of DRYCON is the annealing of parts made through the 3D printing process. This gives the prints increased strength, heat resistance, and dimensional accuracy for offering industrial-level outcomes.
DRYCON is created specifically for flexible, & high-temp materials. Its massive dual chambers can dry & save around 36 kg of filament and heat up to 180°C to suit the annealing process of 3D printed parts to provide industrial-grade strength.
The hygroscopic filament performance is enhanced by DRYCON, ensuring three key advantages: building optimal space that improves print quality, reducing extrusion issues & enhancing the mechanical power of printed parts. The 3-in-1 machine can help users achieve reduced production costs & minimal defects/failures, and repeatable print quality.
The DRYCON’s 4 filament openings simplify the Additive Manufacturing model by feeding the element directly into the 3D printer by eliminating manual transfers & separate storage demands.
Key features of DRYCON:
- Dual Chamber Capacity
- Active Air Exchange
- Annealing for Industrial-Grade Parts
- Seamless DRYCON to Printer Filament Feed
DRYCON from BigRep is available in the EMEA region and will be globally available in early 2025, enabling companies to boost the Additive Manufacturing process in their pursuit of high-performance parts.
Author: Nagarjun M
Remember, you can post free-of-charge job opportunities in the AM Industry on 3D ADEPT Media or look for a job via our job board. Make sure to follow us on our social networks and subscribe to our weekly newsletter: Facebook, Twitter, LinkedIn & Instagram! If you want to be featured in the next issue of our digital magazine or if you hear a story that needs to be heard, make sure to send it to contact@3dadept.com.