Forte d’une décennie d’expérience dans le domaine de la fabrication additive (FA), Honeywell s’est forgé une solide réputation en tant que développeur majeur d’applications aérospatiales commerciales rendues possibles par la FA métal. Aujourd’hui, l’entreprise continue d’explorer de nouvelles voies technologiques dans son domaine d’activité. Brian Baughman et Curtis Swift ont pris cinquante minutes sur leur emploi du temps chargé pour m’éclairer sur ces pistes. Ils m’ont également fait part des difficultés rencontrées dans leur adoption de la FA et m’ont expliqué comment le conglomérat industriel est prêt à continuer à gagner des milliards dans ce domaine.
Honeywell dispose peut-être d’installations dédiées dans cinq pays, mais la véritable magie opère dans son centre de fabrication additive de Phoenix. Si chaque année apporte son lot de joies et de leçons, Baughman a attiré notre attention sur cinq dates importantes qui ont été déterminantes dans le parcours d’Honeywell en matière de fabrication additive.
2008 : À l’instar de nombreuses autres entreprises du secteur aérospatial, Honeywell a commencé à étudier le potentiel de la FA par le biais d’applications de prototypage.
« Notre objectif était de découvrir la FA, ce qu’elle pouvait faire et ce qu’elle ne pouvait pas faire », explique Baughman. « Ces années ont vu le développement de pièces prototypes produites en collaboration avec des fournisseurs externes. Ces années ont été décisives car elles ont également aidé l’équipe à comprendre les aspects économiques de la technologie et les applications à exploiter pour en tirer le meilleur parti. »
L’année 2014 a été marquée par l’achat des premières machines de fusion laser sur lit de poudre, qui sont restées jusqu’à présent le principal procédé de FA de l’entreprise. Cet achat s’accompagne de l’ouverture d’un centre de fabrication additive à Phoenix.
2015 a vu la réalisation de la première pièce métallique fonctionnelle imprimée en 3D.
L’année 2016 a vu l’expansion de cette installation de FA avec un laboratoire d’impression 3D d’aluminium à Phoenix. Comme vous le verrez dans le « segment des matériaux » de cette édition de 3D ADEPT Mag, l’aluminium est un métal privilégié pour les pièces aérospatiales en raison de sa légèreté et de ses qualités anticorrosives.
L’année 2018 a vu l’achèvement d’applications de production pour des cas d’utilisation spécifiques.
Les raisons du choix des technologies de FA
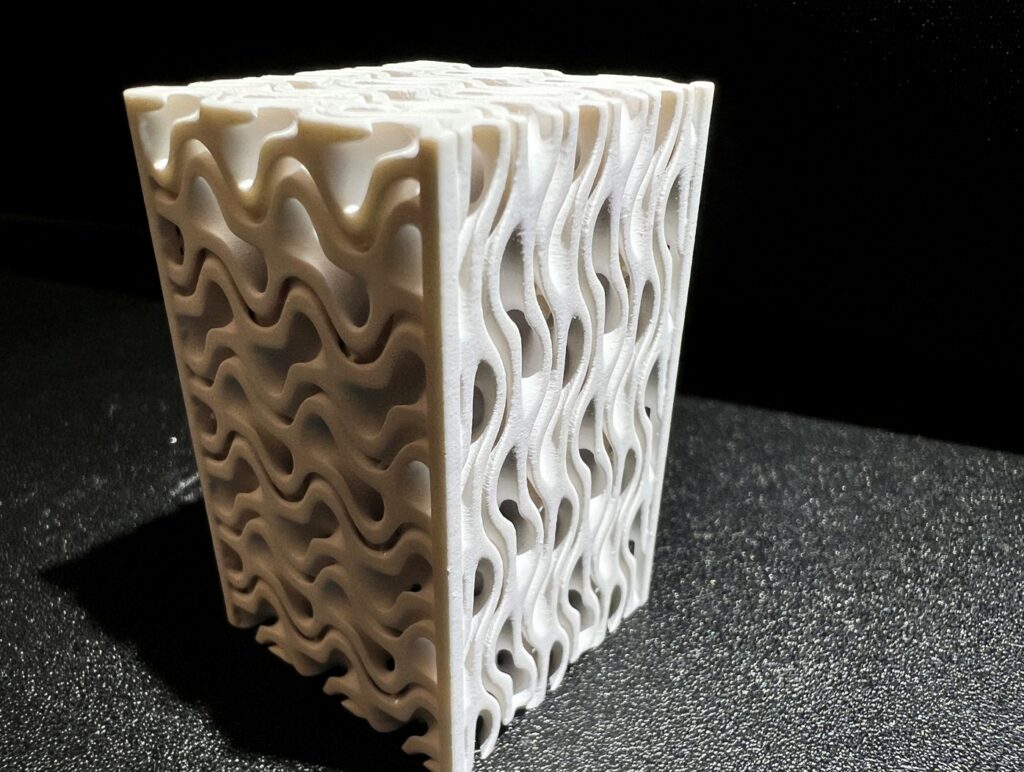
Il n’est pas surprenant que la technologie de fusion laser sur lit de poudre soit la principale technologie de FA d’Honeywell, mais l’entreprise utilise également d’autres technologies telles que le procédé DED, la fusion par faisceau d’électrons et les technologies d’impression 3D de polymères. Les principales raisons qui justifient l’accent mis sur la technologie LPBF sont la capacité à réaliser une fabrication à l’échelle de la production et la cohérence des propriétés des matériaux. Baughman explique en faisant une brève comparaison avec le procédé DED – une technologie qui, à mon avis, est également très avancée pour les pièces aérospatiales, et pour laquelle il avait été embauché à l’origine :
« Au centre de FA métal de Phoenix, la fusion laser sur lit de poudre est le principal objectif. Nous utilisons d’autres technologies comme le procédé DED, mais pas autant que le procédé LPBF. La raison en est que le procédé DED est un processus difficile à contrôler lorsqu’il s’agit de construire différentes caractéristiques géométriques. Et ces caractéristiques ont tendance à avoir des grains de tailles différentes, ce qui se traduit par des propriétés matérielles différentes. Ce n’est pas une bonne chose pour l’aérospatiale. La cohérence dont l’aérospatiale a besoin au niveau des propriétés des matériaux peut être obtenue plus facilement avec le procédé LPBF. Cela dit, dans notre activité de réparation, le procédé DED est utilisé pour réparer les roues de nos moteurs. »
En ce qui concerne l’impression 3D de polymères, « nous n’avons pas de pièces de production en plastique », reconnaît Swift. « L’impression 3D de polymères est utilisée pour soutenir la conception des cockpits de nouvelle génération, des fixations et des essais. Lorsqu’on travaille dans le domaine de la FA, il est facile de supposer que tout le monde connaît la FA, mais ce n’est pas toujours le cas. L’impression 3D de polymères est l’une de ces technologies qui peut vous aider à faire connaître le potentiel de la FA, que ce soit pour répondre aux besoins d’un client ou pour un projet dans le domaine des sciences de la vie qui n’est pas directement lié aux applications aérospatiales commerciales. »
Outre ces technologies, les représentants d’Honeywell m’ont agréablement surpris lorsqu’ils ont déclaré que l’une des technologies qu’ils explorent actuellement est l’impression 3D de céramiques. Si vous vous souvenez, au cours du premier trimestre de l’année, nous avons discuté dans l’une des premières éditions de 3D ADEPT Mag de la valeur ajoutée de la FA céramique pour les industries automobile et aérospatiale. Nous nous sommes rendu compte que les défis et les opportunités se reflètent au niveau des matériaux, et lorsqu’il s’agit de la décision « haute valeur vs haut volume ». En effet, la difficulté de créer des matériaux céramiques denses peut souvent limiter les applications dans ce secteur au stade de l’exploration.
« Honeywell utilise l’impression 3D de céramique pour créer des moules de coulée. Cette technologie, conçue pour un processus spécifique, nous permet de couler des pales de turbine dont les dimensions et les caractéristiques sont extrêmement précises », explique Swift.
« Nous nous concentrons sur la fabrication de composants de turbines à chaud », souligne Baughman. Même s’il n’a pas mentionné le type d’impression 3D de céramique qu’ils utilisent spécifiquement, il a indiqué que la technologie les avait déjà aidés à améliorer l’efficacité de la production de pièces moulées en monocristal de qualité moteur pour une aube. « Lorsque vous effectuez le moulage avec un processus traditionnel, il faut environ deux ans pour fabriquer l’outillage et environ un million de dollars par moule de lame. Grâce à l’impression 3D de céramique, nous avons pu réduire ce délai à six semaines. Pour y parvenir, nous avons passé beaucoup de temps à développer nos matériaux céramiques pour les rendre stables afin qu’ils fonctionnent parfaitement avec le processus de moulage. »
« Nous sommes à l’avant-garde de la technologie d’impression 3D en céramique. Je ne connais pas d’autre entreprise qui fasse mieux que nous », ajoute Swift.
Dans l’ensemble, nos experts en la matière nous apprennent que l’équipe d’Honeywell a su trouver la bonne opportunité pour l’outillage, les pièces de production et les pièces obsolètes. Compte tenu du nombre d’exemples mentionnés au cours de notre conversation, nous pensons qu’un important retour sur investissement réside dans la fabrication de pièces de production.
Défis à relever tout au long du processus d’adoption
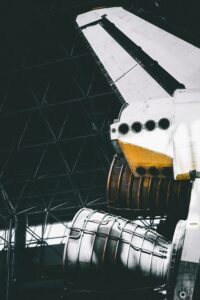
Parmi les nombreuses choses que je peux apprendre des utilisateurs des technologies de FA, je suis souvent curieuse de découvrir ce qu’ils considèrent comme le plus difficile dans leur courbe d’apprentissage. Les réponses varient évidemment d’une personne à l’autre, mais elles finissent souvent par aider les fournisseurs de technologies de FA à savoir ce qu’ils peuvent faire de mieux dans la manière dont ils développent leurs solutions.
Dans le cas d’Honeywell, je me suis rendu compte d’une chose : les défis sont également inhérents aux individus. Pour Swift, « l’impression 3D est la partie facile. Le post-traitement est très difficile. Le passage d’une pièce à la production est long. C’est plus long que ce que les gens pensent. Mais au milieu de tout cela, je dirais que le plus grand défi pour moi est de ne pas disposer d’une bibliothèque complète des propriétés des matériaux. Comme Brian me l’a mentionné il y a longtemps, il existe une bibliothèque complète de propriétés de matériaux lorsque vous regardez le moulage pour les processus traditionnels. En comparaison, la FA ne dispose que de quelques boîtes. Il est très difficile de rivaliser avec cette différence de caractérisation des matériaux. »
Pour Baughman, cette absence de bibliothèque de propriétés des matériaux est l’un des trois principaux défis qu’il a rencontrés. « L’aspect qualification de la FA est également un grand défi. Compte tenu du grand nombre d’organismes de réglementation dans l’industrie aérospatiale, nous devons être en mesure de fabriquer des produits avec lesquels tout le monde est à l’aise. »
Pour une pièce de production donnée, l’approbation doit d’abord être faite en interne, puis par le client et enfin par la FAA qui certifiera que la pièce répond aux critères souhaités.
Baughman a également mentionné le coût du processus dans ce trio de tête. Si on compare la fabrication traditionnelle d’une pièce unique à sa production par FA, la FA reste coûteuse. « Il y a tellement de gens qui veulent utiliser la FA, mais la clé de l’utilisation de la technologie aujourd’hui n’est pas seulement de trouver la bonne combinaison entre la qualification, le processus et les coûts ; il s’agit de trouver la bonne opportunité. »
Face à ces deux défis, l’ingénieur en chef met sur la table deux considérations déjà évoquées par Melissa Orme, vice-présidente de Boeing chargée de la FA. En ce qui concerne la qualification, nous avons partagé nos enseignements sur la manière de l’aborder dans l’édition de juillet/août de 3D ADEPT Mag. En ce qui concerne les coûts, les fournisseurs de FA ont déjà partagé un certain nombre d’astuces pour aborder la question des coûts, mais c’est un sujet que nous aborderons dans un autre article.
Réflexions finales
L’aérospatiale est peut-être l’un des principaux utilisateurs de la FA, mais ses progrès restent lents pour des raisons évidentes : des réglementations strictes, mais aussi les matériaux. Swift m’a ouvert les yeux sur l’importance de comprendre comment le matériau se comportera pour être efficace dans sa production, ce qui prend beaucoup de temps.
En outre, les raisons qui ont motivé le choix de chaque méthode de FA et les défis à relever tout au long du processus d’adoption pourraient être les principaux points abordés ici, mais il convient de noter qu’Honeywell a créé des opportunités dans plusieurs autres domaines cruciaux : la transformation de la chaîne d’approvisionnement grâce à la FA en est un que j’aimerais que vous gardiez à l’esprit, car le besoin de chaînes d’approvisionnement flexibles est devenu plus pressant avec la pandémie du virus Covid-19.
En fin de compte, quels que soient ces autres domaines, gardez à l’esprit la pensée stratégique de Baughman si vous travaillez dans l’industrie aérospatiale : votre opportunité réside dans la bonne combinaison de qualification, de processus et de coûts.
Image de Une: Honeywell Aerospace. APU commercial RE220 avec le conduit d’échappement imprimé en 3D à l’avant et au centre.
Notes de l’éditeur :
Swift et Baughman travaillent tous deux chez Honeywell Aerospace, dans le centre technologique de fabrication additive situé à Phoenix, dans l’État d’Arizona. Swift est ingénieur principal en fabrication additive, tandis que Baughman est ingénieur en chef du centre technologique de fabrication additive. Swift a commencé sa carrière dans l’industrie automobile, en travaillant sur les systèmes de sécurité active et passive, avant de passer à un rôle d’ingénieur concepteur dans l’avionique, ainsi qu’à l’impression 3D plastique sur le site de Honeywell Deer Valley, et est maintenant ingénieur de fabrication pour l’impression 3D métal de LPBF. Baughman, que j’ai découvert pour la première fois en tant que co-auteur de « Additive Manufacturing of Metals : The Technology, Materials, Design and Production (Springer Series in Advanced Manufacturing)« , a occupé plusieurs postes à responsabilité croissante dans les groupes Aftermarket Repair and Overhaul, Materials and Process Engineering et Advanced Manufacturing Engineering. Dernièrement, il a été directeur de l’usine de FA de Phoenix, où il s’occupait des applications de prototypage et de production par FA. Son travail consiste à introduire des technologies de fabrication dans la chaîne de valeur de l’entreprise.