Tech companies that emerge out of anonymity often do it with a bang: through a big launch event to capture the public’s attention or by announcing a seed round but I strongly believe the key in sparking interest lies in the way a company explains how it can transform industries. The latest company that decided to turn stealth mode off is Hyperganic and I sat down with CEO & Founder Lin Kayser to understand the transformation they ambition to bring to the AM industry.
Headquartered in Munich, Germany, Hyperganic, in simple terms, develops and provides a software platform for advanced design and engineering of parts, structures and entire machines of extreme complexity. What makes them outstanding? Artificial intelligence (AI) and algorithms. As per Kayser’s words, they “create the design of physical objects using AI and algorithms.” “We mass produce them in digital factories that have AM at their heart. Our goal is to radically accelerate innovation and it all starts at the design level with engineers who want to create new objects. The truth is, there is a lot of manual work involved in the work of designers. They have to match things in their head and put them on their screen. The process is like building every single façade of the building you want to build. At Hyperganic, we take the thought process of the engineer which requires to answer the question “how do I build something?”, we put it into algorithms and then, the algorithms can automatically recreate parts that otherwise the design engineer would create. The algorithms bring him to the next level to help him produce the things he would like to see and that’s the key enabler of AM.”, he adds.
According to Kayser, a big number of manufacturers do not see the utilization of AM beyond prototyping or small batch runs. Therefore, when it comes to mass production, they often think of another manufacturing process. The Hyperganic team wants to enable this mass production and wants to do so especially for the most complex parts that may absolutely require AM. In Kayser’s opinion, such type of parts are so “tailored to AM, so advanced that not only does AM make sense in terms of functionalities, but also financially and for mass production”.
How it started…
Well, Kayser didn’t just wake up one morning and decide to create a company dedicated to the additive manufacturing industry. As a matter of fact, his entrepreneurial journey started thirty years ago. The software expert’s previous company specializes in digital image processing for the Hollywood industry. Over time, he got dissatisfied with what he was doing. The turning point came when he listened to Al Gore’ speech on “climate change” entitled “An Inconvenient Truth”. Just as everyone (or almost everyone) does on a daily basis, he was doing his part, – sort his waste – but was not aware of the much more important global challenges.
He decided to sell his company in 2011 and started thinking about how he could come up with a significant contribution.
“For me, innovation was something that was happening fast but only in very specific fields like computing or IT but when we look at physical objects, nothing has changed that much in decades. I can’t help but think that was one of the issues to address, in order to be more sustainable, to move forward faster and solve some of the issues we were facing at a global level. Fortunately, in 2012, I stumbled across 3D printing and I was hooked”, he recalls. The thing is, the software guy in him knew that coding and software development was one of the most creative things someone with his background could do, because “you imagine something in your head and you give life to it. But it’s hard to do it physically because software is virtual.” “When I discovered 3D printing [hobby 3D printers], I realized that it is a machine that can essentially prints codes”, he notes.
Needless to say, his learning curve brought him to industrial 3D printing that can process almost any materials but the process has been held back by the models that we send to the 3D printers. Remember that study that reveals that “44% of parts that arrive at digital manufacturing service bureaus do not have a 3D model”?
“We are designing these models in a traditional way of creating CAD models for physical objects. We have been doing that for the last 15 years or so. I started asking myself if we could use computer codes to build physical objects. Instead of modelling something visually, can we use AI and algorithms to create physical objects, structures and maybe entire machines? That was in 2014 and that’s how the idea for Hyperganic was born”, he explains.
Together with Michael Gallo, CTO of his previous company and current CTO at Hyperganic, they sat down, discussed this idea, and hesitated. They finally started developing a software platform where they could basically store every molecule of a part; in other terms, “a workflow that will create various variations of different parts in order to automate the work of the design engineer so that designing becomes finding the right object in these variants”. This means that in the operating systems they create, one could automatically designs objects of a similar type. Therefore, the final look of the end-part will depend on the environment and the parameters the design engineer would have fed into the algorithm. That was in 2017. Hyperganic was officially founded.
How it’s going…
Hyperganic took off and in a few years, has built a growing base of customers across Europe, the US, China and South East Asia. Early at the beginning of this year, the company secured a funding round of $7.8M to expand the team and to continue the development of its software platform.
German funds HV Capital and VSquared Ventures led this first VC investment round for Hyperganic, and co-investors included US-based Converge, industrial partner Swarovski and PC pioneer Hermann Hauser, co-founder of ARM.
At the heart of the developments of the company, there are the Hyperganic Core and Hyperganic Print Framework platforms.
According to Kayser, the first product is a voxel-based geometry platform for AI-based and algorithmic design. This means that voxels help to define geometry be it at normal or higher resolution of the printer. It is available on desktop and as a scalable cloud application platform. The second product on the other hand, aims to support print preparation and highly precise process control.
Interestingly, for those who like to categorize software providers in the AM industry – assuming that Design (CAD), Simulation (CAE); Processing (CAM), Workflow (ERP/MES), as well as QA & Security are the five key categories that might help manufacturers understand what a software does, it would be hard to only check one box (in the case the “Design” category) for Hyperganic.
“We do much more than just the “design” part. We can ensure mesh repair, slicing, support generation, nesting, stacking, voxel-level process control and even multi-material support”, Kayser explains.
How does Hyperganic platform do what it does…
The Munich-based company has developed a software platform that is compatible with any industrial 3D printing platform.
“We work with polymer 3D printers, metal AM technologies, resin-based systems. We even support manufacturers who print with concrete. We cover the full spectrum of materials on the market”, the CEO outlines.
Users of the Hyperganic Core platform can explore and create a broad variety of applications, including aerospace, consumer goods, and medical products. What’s interesting to keep in mind is that these products absolutely need to be customized, they can be super complex since they require voxels to be created or they should be highly optimized objects.
Amid the AI-design based objects, Hyperganic’s platform has already helped to create, there are for instance a 3D printed cycling helmet or even a 3D printed rocket engine. However, it should be noted that the company currently focuses on aerospace applications.
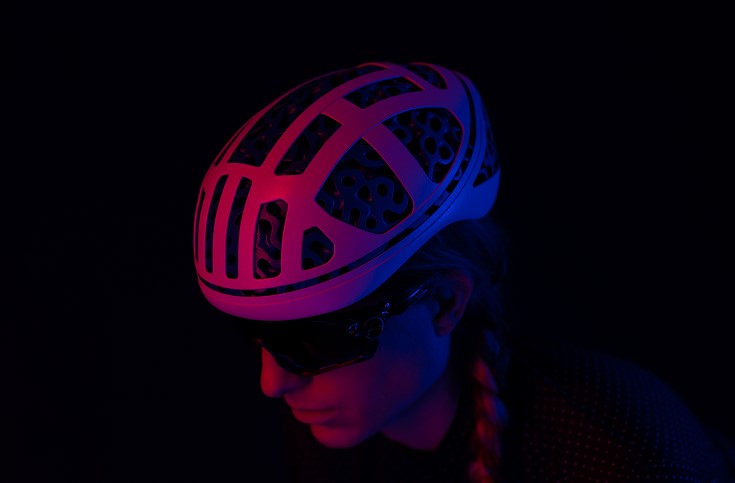
As far as the rocket engine is concerned, the team decided to explore an entirely algorithmic approach for its creation.
“We decided to give the algorithms just one geometric starting point, a spline curve that describes the inside of the combustion chamber, stored in an Excel spreadsheet. There were no CAD files, no existing models, just data, stored in a spreadsheet, plus the algorithms that interpret the data to generate the functional parts of the engine. With this minimal starting point, we built the algorithm that generates the actual geometry. The engine is created top to bottom, laying out channels that transport the cryogenic oxidizer first down around the chamber, cooling the inner wall that is exposed to the burning fuel, and then back up again in an outer layer of channels, for later injection into the chamber itself. We used Hyperganic‘s capability to precisely control the process parameters for every point in space to modify the structure of the metal itself. The inside of the chamber is printed very densely, using high laser power, whereas the outside becomes almost porous to keep the weight down”, a company’s report reads.
The difference with traditional engineering is that here, the engineer does not design a part in a linear fashion; he rather creates a process that leads to the desired part.
“Traditionally you start with an existing solution and make incremental changes. In Hyperganic engineering, you regenerate objects from scratch all of the time. You generate hundreds or thousands of variants that can be evaluated. In traditional engineering, redesigns are costly and need to be avoided; in Hyperganic engineering, it is the norm and the key to coming up with a global optimum”, the report highlights.
What’s next for the company?
From a business standpoint, the company is currently expanding its customer base beyond simple users (design engineers) to reach third parties who would like to use the platform to create their own applications.
Moving forward, Kayser strongly believes that AM will not stay a niche forever. On the contrary, for him the technology will become one of the most important fields in manufacturing in a few years. “By bringing algorithms into this game, we create a new type of manufacturing that has not been done before. We are providing that missing piece that will lift AM to a new level”, he concludes.
This exclusive feature has first been published in the May/June edition of 3D ADEPT Mag.
Remember, you can post job opportunities in the AM Industry on 3D ADEPT Media free of charge or look for a job via our job board. Make sure to follow us on our social networks and subscribe to our weekly newsletter : Facebook, Twitter, LinkedIn & Instagram ! If you want to be featured in the next issue of our digital magazine or if you hear a story that needs to be heard, make sure you send it to contact@3dadept.com