Founded in 2015, Roboze is a brand of additive manufacturing (AM) solutions that hundreds of customers in 25 countries around the world use to solve challenging industrial applications. 2017 was a decisive turning point in the company’s journey as it marked the launch of the Argo 500 3D printer and some processing super polymers and composite materials solutions that could replace metals.
We probably do not teach you that the story of this 3D printer manufacturer starts in Italy with Alessio Lorusso, thecompany’s founder & CEO. Unlike many experts that discovered 3D printing as part of their career, Lorusso discovered 3D printing when he was still a teenager. “Out of pure passion and a spirit of curiosity, I built my first 3D printer in my bedroom”, he explains.
Today, hard work, passion but most importantly a team for which he will always be grateful have led to the opening of 3 offices around the world: the EMEA HQ in Bari in Italy, Roboze GmbH in Munich and the American HQ Roboze Inc in Houston, Texas.
In this Q&A series, Lorusso recounts the company’s evolution within the AM industry and how it addresses some of its current challenges.
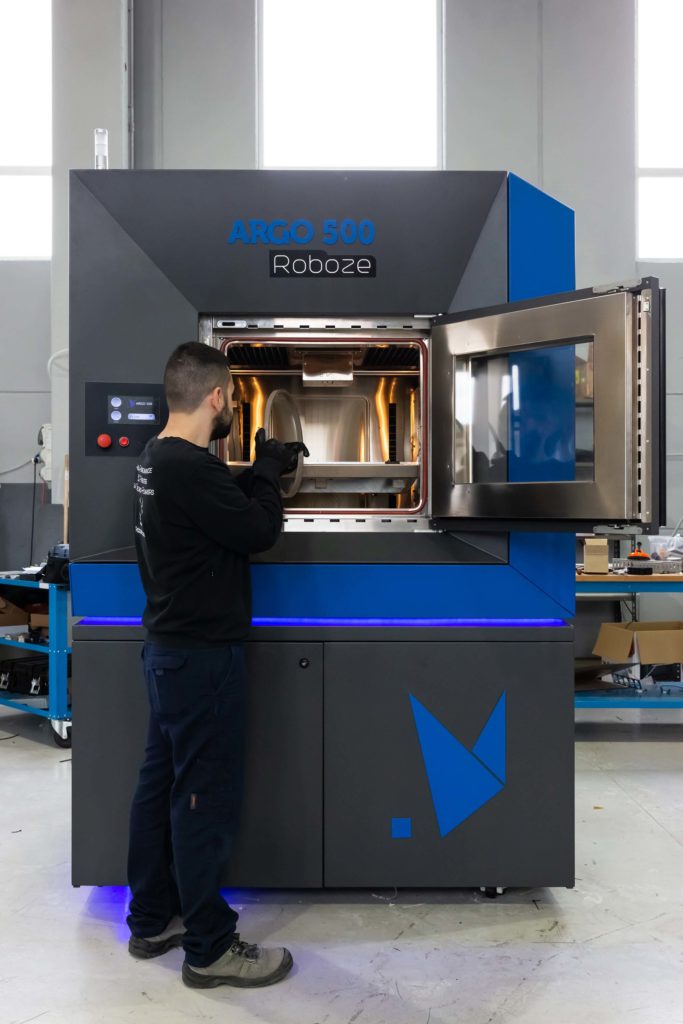
Roboze started without any capital investment from outside sources. Would you say it was a handicap?
Starting without external capital is very challenging. To found Roboze, I invested all my very few savings, which had been set aside in the meantime, after working as an employee for another company. You must constantly not lose sight of your goal, measure your investments and not be afraid to take risks. Furthermore, it is essential to have a strategic approach to investments by setting the right actions based on the objectives set, without moving into superfluous or unnecessary actions at that time.
Two years ago and even more recently, the company secured a funding round. What difference does it make when you are backed by investors ?
If you can go from A to B without external capital, you will be able to go from B to C at twice the speed of the first. The speed is given by the presence of capital that allows you to invest simultaneously in different areas, secure the best talent, create strong expansion strategies. To do this, it takes strategic vision first, and flawless execution afterwards. By the time we secured our first round, our investor has already found a company of dozens of people, producing revenue and in surplus. This gives you a way not only to collect money, but to choose who to collect it from. This is a fundamental issue, little dealt with in my view. The strategic importance of the type of investor and the personal commitment of the people within the funds is of vital importance for the success of the partnership.
Roboze is now a global company. What are according to you, the cities that adopt the most AM?
Roboze works now in 2 continents with direct offices in America, Germany and Italy. We expect new expansions in the next 15 months to another continent. Thanks to our concept of distributed manufacturing, we are bringing 3D printing even to remote areas, creating production capacity where it wasn’t before and bringing the value back to the territory. A very strong adoption of our technology is in Europe and America, but we also have many systems in South Korea, Japan, Australia and even on islands off the coast of Africa.
The company has recently launched Roboze 3D parts. Could you tell us a bit about how it works since its launch?
We are focused on creating the largest distributed manufacturing network in the world. We already have hundreds of machines in the world and many of these today are connected to our Roboze 3D Parts network, which produces medium batch productions, just in time and on demand, close to the place of need. The goal is to create a new customized production model, which in the coming years will increasingly take the place of large delocalized serial productions, bringing the value back to Europe and America. With the 3D Parts service, Roboze wants to accelerate this trend, a network of production sites distributed over multiple locations and interconnected around the world, with the aim of replacing the “make-to-stock” model with a “make -to-order ” model, rethinking the entire concept of warehouse. This way, manufacturers will be able to reduce costs and time in their supply chain by digitizing their inventory, accelerating innovation and facing rapidly changing market dynamics, with the production of customized parts with our super materials, strong like metal, whenever and wherever needed.
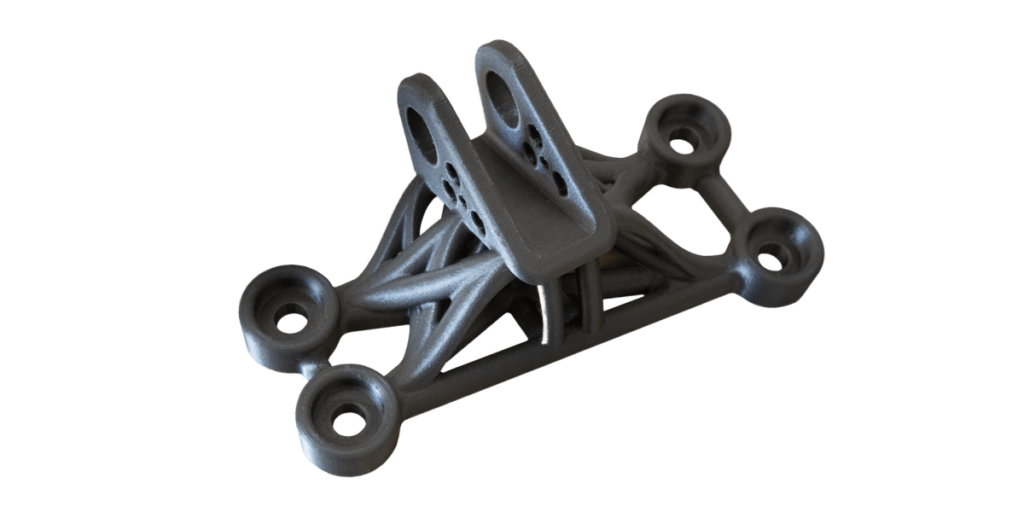
At the manufacturing level, Roboze positions its technology as one that could replace metal. Do you think it is possible for all industry applications?
It would be unreasonable to argue that super-polymers and composites, processable with Roboze printing solutions, are capable of replacing metal parts in any applications. These are plastic materials that combine the typical characteristics of this category, such as low density and excellent thermal and electrical insulation, with less common properties, capable of expanding their range of use in various industrial sectors. Some composites offer considerable mechanical characteristics, registering a tensile strength equal to that of an aluminum alloy. Others maintain a particularly broad chemical resistance even at high temperatures, working up to 280 ° C. Still others boast self-extinguishing properties or develop a self-lubricating regime when subjected to creep … And so on. All this is accompanied by Roboze’s particular attention to the process of industrialization of technology. If on the one hand we have created an entire ecosystem aimed at controlling the printing process, on the other hand we are aware of the enormous importance of filament certification for an industrial sector. Some significant examples of certifications are the Norsok M710 for the PEEK for the Oil & Energy sector, the Blue Card for the Extem for the space and electronics sectors, the aerospace certifications for the Ultem 9085 and so on.
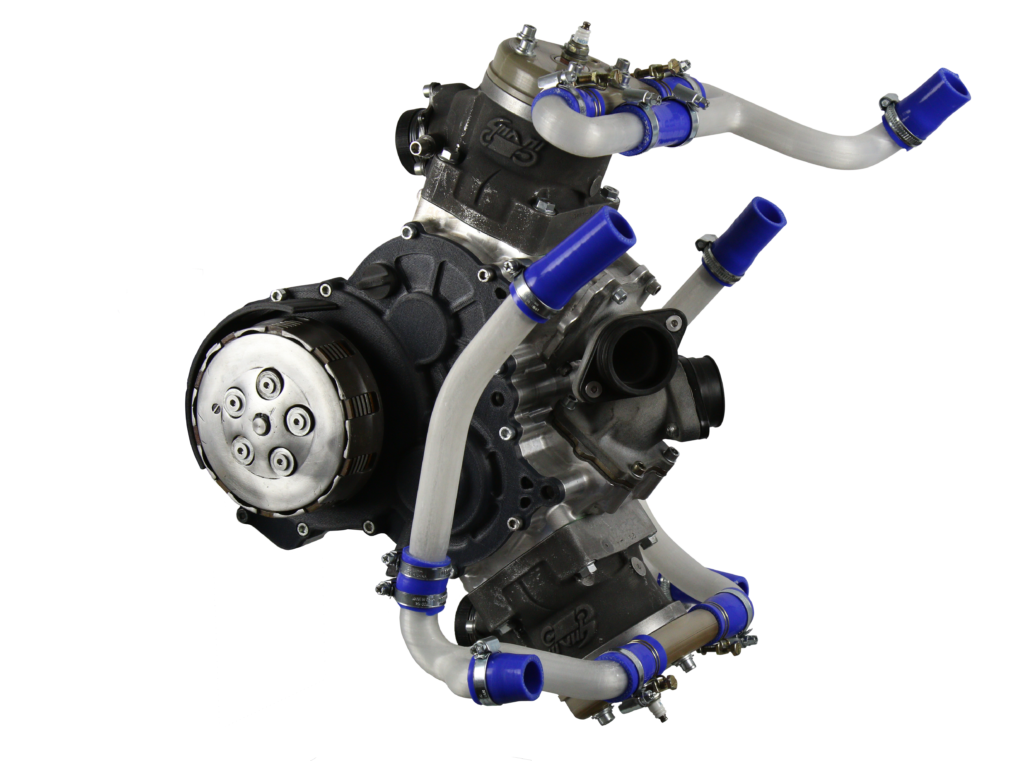
You recently shared your view on the benefits of AM in terms of sustainability as part of an event. Could tell us how sustainability is part of Roboze?
Sustainability is not just about the environment. It also includes human, social and economic factors. This is one of the reasons why people see it as an added value, because it can lead to important advantages for every business. Roboze is delivering tangible sustainable improvements to clients. The additive nature of AM makes it already a more sustainable manufacturing process since less waste is generated compared to traditional subtractive technologies. With Roboze 3D Parts everyone can use digital designs to produce spare parts on demand. This would eliminate or at least minimize inventory waste. It will also reduce the amount of unsold finished goods, potentially improving revenue flow since goods are paid for before being manufactured. Printing what you want, where and when you want, is leading to shorter and simpler supply chains, more localized production and innovative distribution models that would improve every customers’ life.
Remember, you can post free of charge job opportunities in the AM Industry on 3D ADEPT Media or look for a job via our job board. Make sure to follow us on our social networks and subscribe to our weekly newsletter : Facebook, Twitter, LinkedIn & Instagram ! If you want to be featured in the next issue of our digital magazine or if you hear a story that needs to be heard, make sure to send it to contact@3dadept.com