Apart from electric propulsion systems used for commercial communications satellites, most of the rocket engines in service today are chemical rockets. This means that they rely on combustion reactions between a fuel and an oxidizer to produce high-velocity exhaust gases. The thing is, this type of propulsion system presents several challenges that need to be prioritized to deliver high value for the in-space propulsion market. In its list of priorities, Agile Space Industries discusses the challenges where Additive Manufacturing plays a pivotal role.
For me, space exploration comes down to how far we can travel, how quickly and cheaply we can get there, and what we can bring along. With in-space propulsion systems at the heart of the new space economy, Agile Space Industries happens to be one of the few companies that continuously bets on AM.
Although the company was founded in 2009, Agile Space Industries appeared on our radar for the first time in 2021 when it acquired 3D printing service bureau Tronix3D, a long-term supplier based in Pittsburgh, PA, USA. Those who have been following the company since the very beginning probably witnessed its rebranding from AMPT – its first name – to Agile Space Industries.
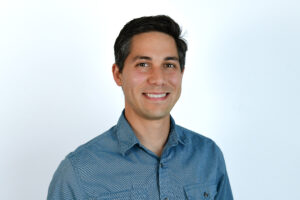
“AMPT was awarded one of the first SBIRs for the additive manufacturing of rocket injectors in 2009, but at the time the technology for additive manufacturing simply wasn’t at the same state of maturity that it is today. As the field of metal additive manufacturing evolved, and with the emergence of a new generation of moon landers requiring innovative propulsion solutions, the timing was perfect for us to begin crafting our own designs. In 2019, AMPT became Agile Space Industries, and we started developing our own thrusters which are uniquely designed to be additively manufactured,” Ben Graybill, Additive Manufacturing Operations Lead and Dustin Crouse, Lead Process & Development AM Engineer at Agile Space Industries told 3D ADEPT Media.
With the acquisition of Tronix3D, what started as an operation to optimize the performance of propulsion systems used to power NASA and SpaceX’s lunar missions turned out to be another core activity of the company.
“While we are our own primary additive manufacturing client and are thoroughly satisfied with the results, we also engage in several external additive projects, typically maintaining 3-4 multi-year programs at any given time.
Our scope of work is diverse, covering a range from in-space propulsion systems to naval applications to petroleum extraction systems. A key aspect of our services is leveraging the expertise of our engineers in Design for Additive Manufacturing (DFAM). The project involves intricate product design challenges and the use of specialized and exotic alloys.
Moreover, when it aligns with our strategic objectives, our process development team takes on the task of integrating new alloys into our workflow. This requires defining and implementing new production processes from scratch, which are tailored at each step to meet the unique demands of the material and application. This approach allows us to continuously expand our capabilities and offer cutting-edge solutions across various industries”, Graybill and Crouse explained.
To date, Agile Space is known for the manufacture of thrusters and rockets engines, providing a set of services that range from design, AM services, subtractive manufacturing to testing capabilities.
The challenges of in-space propulsion systems
Those who do not have an engineering background may keep in mind that space propulsion is a branch of aerospace engineering that sheds light on methods and technologies that propel spacecraft and satellites through outer space.
The problem is the methods used to propel spacecraft and satellites are complex and sometimes hard to combine with new manufacturing technologies. They include Cold Gas Space Propulsion, Nuclear Propulsion, Electric Space Propulsion and Chemical Space Propulsion – the most widely used method and the specialty of Agile Space Industries. As said above, this propulsion technique relies on combustion reactions between a fuel and an oxidizer to produce high-velocity exhaust gases.
With the integration of manufacturing technologies in the development process, space companies have to deal with major hurdles that are both economic (economies of scale), and technological (material science, and miniaturization).
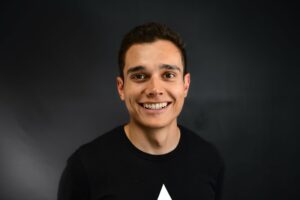
“Top 5 challenges for in-space propulsion are thermal management, ground test capabilities, performance over durations exceeding a year, flight rates, and then material science (kind of plays into thermal management),” Graybill and Crouse said.
However, despite the wide range of considerations to take into account, AM can help to address a couple of these challenges. We learned from Agile’s experts that AM can help with thermal management, flight rates, and material science. “Thermal management and materials because of the geometry you can print and the materials we’re now experimenting with. Flight rates, AM works well for if they’re low, which they generally are – allowing you to not have a lot of engine specific tooling,” they added.
Furthermore, beyond development, what really matters is the size of your system and the production rate. According to Graybill and Crouse, “AM is not favourable for a LOT of engines a year, but for niche components, it’s a great fit (complex cooling channel geometry, etc.) even at higher volumes. It can be great for miniaturization, especially if what needs to be miniaturized is in a hard-to-manufacture location.”
AM: key applications and challenges
Before we delve into the specific added value AM brings to the Agile table, it’s important to consider the investments Agile made so far to achieve their AM operations. The Mount Pleasant-based advanced manufacturing center which is ISO9001, AS9100 certified as well as ITAR Registered and NIST-SP-800-171 Compliant takes care of AM operations that range from initial process development to serial production of qualified flight hardware. To do so, they leverage a wide range of specialized equipment that includes metallographic and inspection solutions, such as a Keyence VHX7100 which serves the needs of process development and characterization.
As far as 3D printers are concerned, one finds the basic FDM and SLA 3D printers in their production environment as well as a range of industrial 3D printers from TRUMPF. In the list of qualified materials these 3D printers can process, the team at Agile focuses on nine unique manufacturable alloys, including oxygen-sensitive refractory alloy Nb C103.
“Occasionally, we encounter situations where off-the-shelf components or systems don’t meet our specific requirements. In such cases, our team has innovatively designed and manufactured proprietary lot mixing and depowdering flushing systems, enhancing our part yield and overall efficiency,” Graybill and Crouse pointed out.
When we only look at Agile’s activities as an in-space propulsion solution provider, AM can be used in every new product development:
“Its most significant advantage lies in its rapid turnaround capability, which enables us to iterate designs within weeks. This agility allows us to bring a new product to the test stand in as little as a month. In fact, many of our products are composed of over 85% additive components by weight, demonstrating the extensive use of AM in our production process.”
Interestingly, Agile goes beyond the widely known benefits of AM to highlight its strength when it comes to manufacturing specific parts. For our experts, that strength lies in the ability to produce complex internal manifolds across various scales within the same machine:
“This capability is particularly crucial in components such as injectors and chamber designs, which often require intricate internal structures. For instance, some of our injectors incorporate over 50 internal curved manifolds, each terminating in orifices smaller than 0.5mm in diameter. This need for high precision contrasts with the broader scale requirements of features like the regenerative cooling jackets in our A2200 engine, which are more than 5mm wide” Graybill states.
And Crouse continues: “To ensure consistency and mitigate any risk of dimensional or process variation, we use the same printers for both development and production. Before transitioning a printer from development to production, it undergoes a series of rigorous process checks to qualify for production use. This seamless transition from prototyping to production underscores our commitment to maintaining high standards of quality and reliability in our AM processes, making it a cornerstone of our operations in providing innovative in-space propulsion solutions.”
Moreover, to give a tangible example of the essential role of AM and its ability to accelerate production speed, the experts told the story of a novel chamber that was in the machining queue and scheduled for a hot-fire test within a week. The thing is, due to the unique surface profile and external manifolds, none of their mills or lathes could hold the component for a necessary cutting operation. Within 48 hours, they designed a 3-part clamshell from scratch, 3D printed it in Ti64, and on the lathe-making chips.
Despite its numerous advantages, we need to be mindful of the potential limitations of the technology. While these limitations are experienced differently from one AM user to another, some challenges are common to everyone who is looking to industrialize AM. Some of these challenges include data integration and management.
As a reminder, managing AM data is crucial for establishing part traceability, understanding AM processes and making decisions during the product development lifecycle. In this vein, their curation, integration, fusion, sharing and analysis become complex when one has to deal with the volume, velocity, variety and veracity of these data.
When asked how they are addressing this challenge, the experts at Agile said they rely on a combination of in-house strategies and third-party applications:
“These tools are designed to process the substantial amount of data collected in-situ and correlate it with data from both upstream and downstream of the process.
For instance, we implement a statistical Design of Experiments approach during process development, focusing on key process parameters. We collect in-process data, primarily thermal signatures, during printing and analyze it to identify key material properties such as porosity. This process enables us to optimize our operations based on empirical evidence. Crucially, our in-house propulsion testing facility, which is extensively instrumented, allows us to validate material properties through functional testing of the actual components, rather than relying solely on representative coupons or samples. This approach provides a more accurate and direct assessment of how materials will perform in our end-use applications for our customers.
While our Agile in-house solutions may accelerate process development and qualification, we are not a software development company. Therefore, we remain vigilant and aggressively adopt advances in software and hardware that can further enhance our ability to transform vast datasets into actionable insights.”
Despite their focus on AM technologies, Agile recognizes that “AM is not a panacea” and this is crucial to map out a broader manufacturing strategy. As I have said before, AM does not benefit from the century of research into the production of components that is the hallmark of precision subtractive techniques. This means that, at some point, despite the current mediatisation of AM, along the manufacturing value chain, there are still certain things that subtractive manufacturing processes do better, and that still require a lot of improvements on the AM side.
At AGILE, it’s about ensuring a synergistic approach to production:
“The additive team would like to thank Oqton and TRUMPF for letting us break things. Part of being an ‘agile’ company is pushing software and hardware beyond current capabilities. We appreciate the companies’ application and development teams working with us to add functionality where we need it. Readers of this magazine [3D ADEPT MAG] may live and breathe additive, but almost all programs require machining operations. So, this is another reminder to consider and thank your machinists.’’
Future outlooks
With a decade of expertise in hot-fire testing and system design and development, Agile Space has nothing to envy others. While its growing use of AM makes it one to watch in this New Space era, I am hoping to see the company explore AM processes that go beyond LPBF and am curious to discover the lessons they would have learned in that exploration.
However, the company is eager to soon explore a range of technologies that extend the capabilities of laser powder bed fusion.
“While fun stuff remains behind closed doors, I can share our growing interest in incorporating more refractory-based alloys and the exciting prospects of experimenting with computationally designed materials. Our focus is on advancing our expertise in thermal-mechanical compensation and additive design software to create innovative thrusters. For example, newer components may incorporate intricate features that have remained difficult to qualify, such as functional lattice or require repeatable orifices smaller than 100 microns in diameter. Furthermore, as we progress into 2024, some of our legacy components might move away from laser powder bed fusion, adapting to newer additive technologies that better align with our evolving production needs.
Beyond the realm of our AM department, AGILE’s experience in developing thrusters for various clients has given us deep insights into the diverse needs of the satellite propulsion market. As a leading developer of in-space rocket engines, we’ve gained a comprehensive understanding of our customers’ requirements for mission enablement. AM, being a cornerstone of our manufacturing process, will play a critical role in these ventures. We plan to leverage AM’s capabilities in these new applications, and we anticipate sharing more updates on this front in the near future. Our strategic direction in 2024 is not just about advancing our AM technology but also about aligning it with the broader needs and aspirations of our customers, ensuring we remain at the forefront of in-space propulsion solutions,” Graybill and Crouse concluded.
*All images: courtesy of Agile Space Industries
This content has first been published in the January/February edition of 3D ADEPT Mag.