Admatec et Aristo-Cast collaborent sur un nouveau procédé de coulée de précision sans modèle en utilisant la fabrication additive (FA).
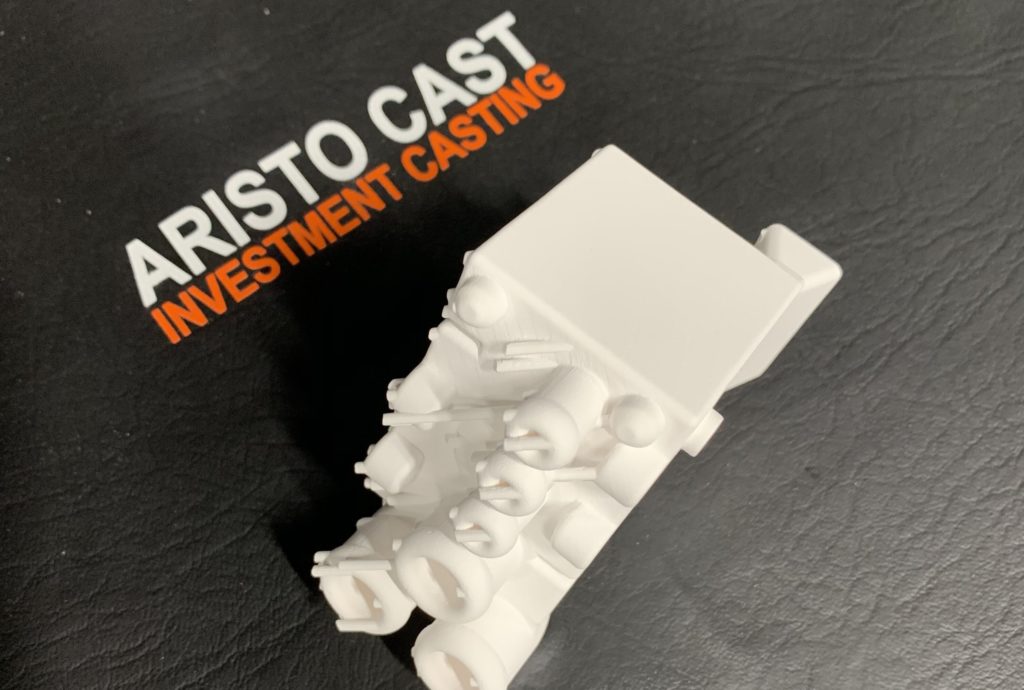
Admatec est un spécialiste des imprimantes 3D métal et céramique. Sa technologie brevetée ADMAFLEX peut être utilisée avec des matériaux céramiques tels que l’alumine, la zircone et la silice fondue et des métaux tels que le 316L, 17-4-PH, Inconel 625 et le cuivre. Aristo-Cast, de son côté, est une société de fonderie de précision qui applique la technologie de FA à son procédé.
Ce qui a mené au développement d’un nouveau procédé de moulage à la cire perdue avec la FA
Le processus conventionnel de moulage de précision peut prendre de deux à dix jours pour créer une coquille qui est prête à couler. La coquille est créée en trempant le motif dans une boue liquide et en séchant ensuite chaque couche avant d’ajouter la prochaine d’un maximum de 8 couches pour compléter la coquille.
Le premier revêtement est le facteur clé de la finesse des détails et de l’état de surface que l’utilisateur peut obtenir sur le produit final. De plus, un motif avec des noyaux ou des passages complexes est parfois un réel problème pour les professionnels en raison de l’incapacité de vérifier l’intégrité de la couche et de la difficulté à déterminer quand la couche est suffisamment sèche pour permettre l’application de la couche suivante.
Une fois qu’Aristo-Cast a commencé à travailler avec l’imprimante 3D céramique Admaflex 130, l’entreprise a pu imprimer directement la coque, éliminant ainsi le besoin d’un moule d’injection coûteux ou d’un modèle imprimé 3D coûteux.
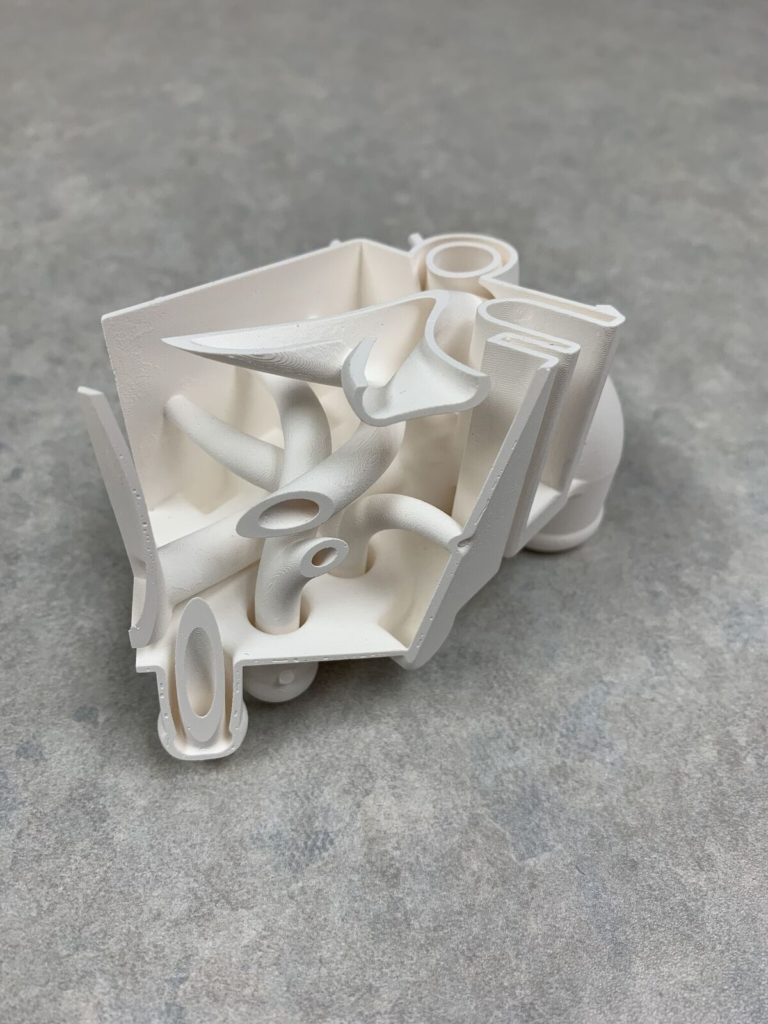
Cinq étapes ont donc été supprimées : création du motif, du motif en grappe, formation de la couche de stuc, moulage de la coquille en cire de déparaffinage. De plus, l’impression de la coquille directement à partir d’un fichier CAO élimine le doute sur l’aspect des détails de surface et permet l’inspection des passages de noyaux complexes avant que l’alliage soit coulé. Le problème lié au séchage de la couche est complètement éliminé, ce qui permet une création beaucoup plus rapide de la coquille. Dans certains cas, le temps est même réduit de 75%.
Jack Ziemba, CEO d’Aristo-Cast, explique que « la réduction du matériau utilisé a permis un rétrécissement isotrope plus constant de la pièce finale et la possibilité d’imprimer une surface creuse parfaite de l’intérieur de la coquille permettant un enlèvement plus facile du noyau . – Avec la technologie Admatec, n’importe qui capable de faire fondre du métal pourrait devenir un fondeur de précision. »
Pour des informations exclusives sur l’impression 3D, abonnez-vous à notre newsletter et suivez-nous sur les réseaux sociaux ! Vous souhaitez-vous abonner à 3D ADEPT Mag ? Ou vous voulez figurer dans le prochain numéro de notre magazine numérique ? Envoyez-nous un email à contact@3dadept.com
//pagead2.googlesyndication.com/pagead/js/adsbygoogle.js (adsbygoogle = window.adsbygoogle || []).push({});