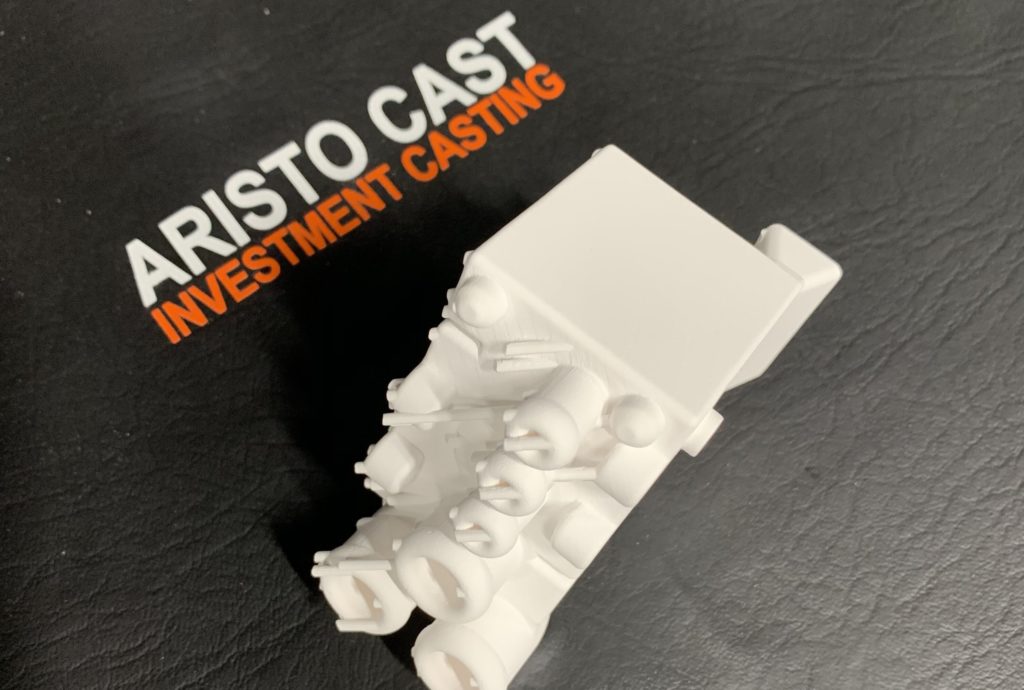
Admatec and Aristo-Cast collaborate together on a new pattern-less investment casting process with additive manufacturing.
Admatec is a specialist of metal and ceramic 3D printers. Its proprietary technology ADMAFLEX can be used with ceramic materials such as Alumina, Zirconia and Fused Silica and metals such as 316L, 17-4-PH, Inconel 625 and Copper. Aristo-Cast on its side an investment casting company that applies AM to its process.
What led to the development of a new pattern-less investment casting (IC) process with AM?
The conventional IC process can take two to ten days to create a shell that is ready for casting. The shell is created by dipping the pattern in a liquid slurry and subsequently drying each coat before adding the next of as many as 8 coats to complete the shell.
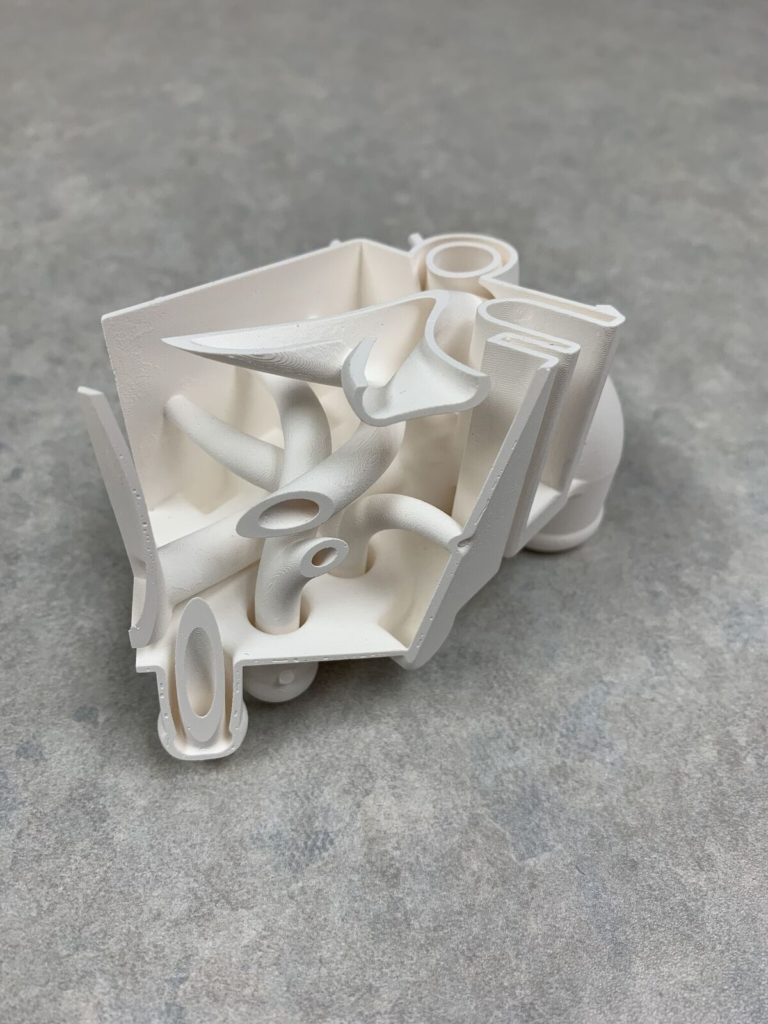
The first coating is the key factor of the fine detail and surface finish the user can achieve on the final product. Furthermore, a pattern with complex cores or passages is sometimes a real issue for professionals due to the inability to verify the integrity of the coat and the difficulty in determining when the coat is sufficiently dry to allow the application of the next coat.
Once Aristo-Cast started working with the Admaflex 130 ceramic 3D printer, the company has bee able to directly print the shell, thus eliminating the need for a costly injection mold or a costly 3D printed pattern.
Five steps have therefore been removed: creation of pattern, cluster pattern, stucco coat forming, dewax shell mold. Moreover, printing the shell directly from a cad file eliminates the doubt of what the surface detail looks like and allows the inspection of intricate core passages before the alloy is poured. The issue related to coat drying is completely removed allowing much faster creation of the shell. In some cases, reducing the time by 75%.
Jack Ziemba, CEO of Aristo-Cast, explains that – “the reduction in material used, allowed a more consistent isotropic shrinkage of the final part and the ability to print a perfect hollow surface from the inside of the Shell allowing easier removal of the core.” – he adds – “with the Admatec technology, anybody that is able to melt metal could become an investment caster.”
For further information about 3D Printing, follow us on our social networks and subscribe to our newsletter
Would you like to subscribe to 3D Adept Mag? Would you like to be featured in the next issue of our digital magazine? Send us an email at contact@3dadept.com
//pagead2.googlesyndication.com/pagead/js/adsbygoogle.js (adsbygoogle = window.adsbygoogle || []).push({});