A general understanding of Additive Manufacturing (AM) and Lean Management (LM) will make most industrials agree on what seems an undisputable fact: AM can easily converge with LM as the former promotes resource efficiency and cost efficiency that the latter already provides. The problem is, since productivity has often constituted the basis of measuring operational excellence, thus the primary goal to achieve in industrial production, Small and Medium Enterprises (SMEs) have often failed to realize that although the advantages of AM are the same, different scenarios may apply to them when it comes to achieving series production with AM – in a more agile way. We recently caught up with ADDVANCE’s CEO Elvira Leon to understand the mistakes they often make when trying to make their business agile with AM, and the areas where the company can provide its expertise to help them achieve this goal.
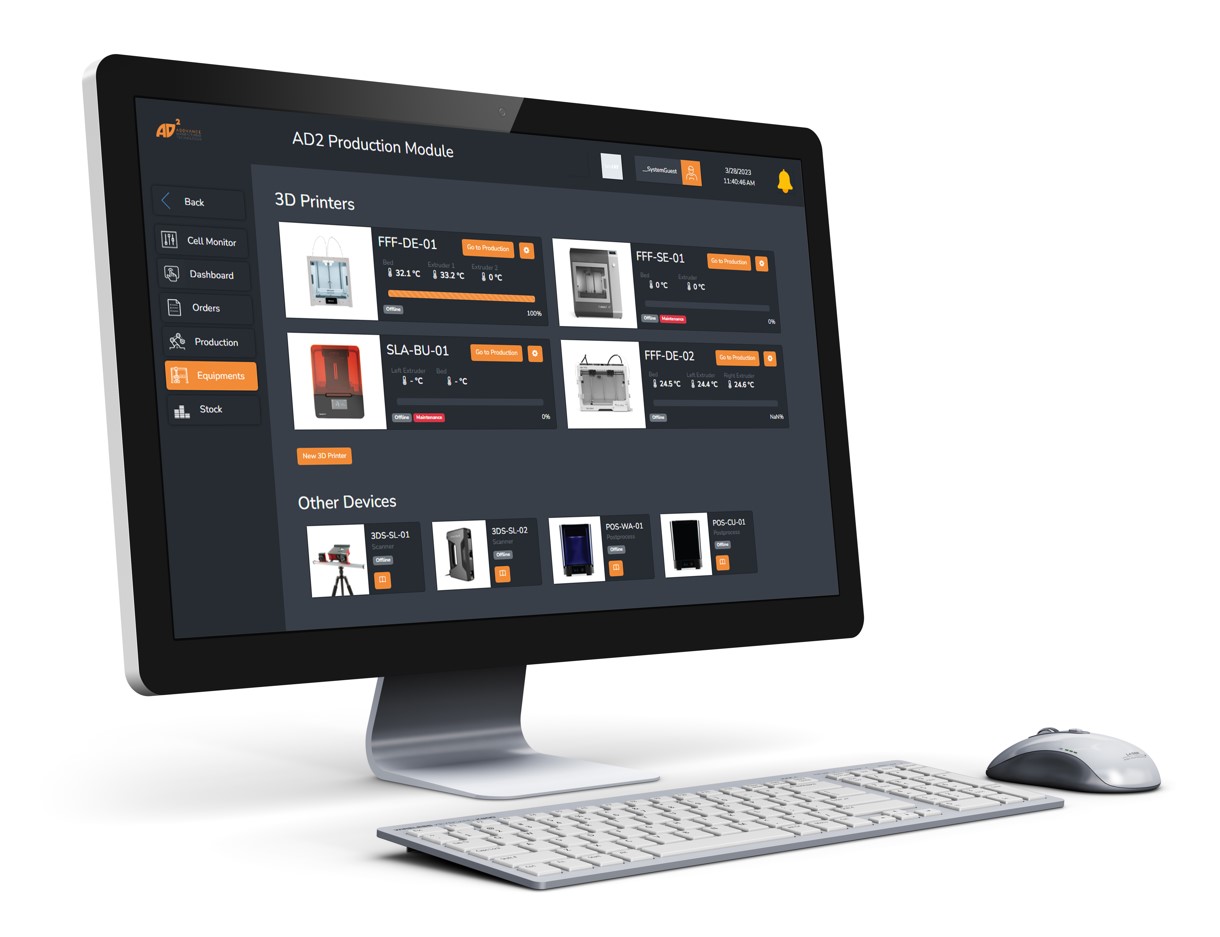
ADDVANCE is a Spanish company founded by three engineers with decades of experience in the industrial sector. Despite the advantages of AM, the founding team deplored the fact that the technology was difficult to integrate into industrial production environments. Three years ago, they started working on the development of a digital warehouse product, a digital warehouse and on-demand manufacturing software, which aims to guarantee traceability and facilitate the process both in internal manufacturing and with external suppliers and service bureaus. The team may have started operations on the Spanish market, but they now work with clients in Europe and America.
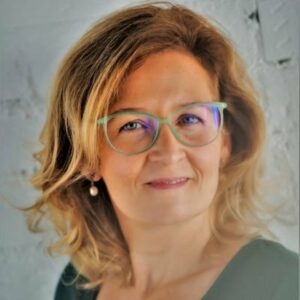
“Our mission is to provide a comprehensive solution to manufacture on demand, close to the point of consumption, ensuring quality and traceability without compromising the industrial property of OEMs. A digital and sustainable manufacturing, that allows the relocation of the industry. We focus on the industrial sectors (railway, automotive, machinery and industrial goods, among others) providing solutions for production and aftermarket operations optimization, supporting our customers in the creation and exploitation of their on-demand manufacturing business model, enhancing the digital warehouse with the additional functionality of process control to ensure regulatory compliance. In other sectors with relevant production or maintenance operations in distributed or remote locations (e.g. energy, Oil & Gas, infrastructures maintenance, naval, defense), we complement our offering with a local manufacturing solution, deployable smart micro-factories,” ADDVANCE’ CEO explains.
How LM and AM may influence each other
As far as lean management is concerned, companies often rely on an integrative approach consisting of human resources, machinery, strategies, and emerging technologies for maximized operating performance. While there is a lack of resources on how LM and AM complement each other, holistic experiences observed so far, reveal that when done well, the convergence of AM and LM easily enables the manufacture of personalized products, increasingly demanded in a globalized and digitally connected world. This is exacerbated by the fact that higher customer expectations lead to an increase in variant diversity and intensify the complexity of the production environment.
While the focus is made on AM, please keep in mind that LM can influence all technologies and processes of industry 4.0. (automated guided vehicles, virtual representation, human-computer interaction, cloud computing, big data & data analytics).
That being said, LM is often considered a prerequisite for the successful introduction of AM or industry 4.0 in general. This is supported by the fact that standardized, transparent and reproducible processes are of paramount importance for AM, therefore, executives need LM competence for considering customer value and avoiding waste. Furthermore, by reducing product and process complexity, LM enables the efficient and economic use of industry 4.0 tools.
On another note, industry 4.0 tools such as AM advance lean management as they rely on real-time data that improve transparency and information quality; not to mention that our industry continuously needs to cope with a fluctuating market demand that is influenced by a wide range of variables.
According to Elivra Leon, when looking to make their business agile, the difficulty for SMEs is often to find the applications or the business case, as they lack knowledge in the economic and organizational aspects of AM. “There is a tendency to compare the current price per part in conventional technology with the price in AM, and the advantages in the pre-production stages or in the logistics chain are not considered. Once the applications have been identified and the possibility of managing their production through an on-demand manufacturing platform, managing their digital warehouse safely gives them flexibility and significant savings, and their competitiveness multiplies”, Leon said.
This price comparison would be the major hurdle that would prevent an effective integration of AM into SME’s supply chain. Leon adds:
“The nirvana of logistics is a process in which there are no stocks, and in which the parts or finished products reach the end customer, wherever he is, in the proper time it is needed. This is the basis for building a supply chain management strategy that aims to bring warehouse closer to the place of use. In this scenario, the combination of digital warehouse tools with additive manufacturing technologies is the solution to a new model of manufacturing on demand, for which a new agile supply chain must be designed. This model implies many changes in the way companies work nowadays and requires the implementation of new traceability solutions, but today we can say it is already feasible”.
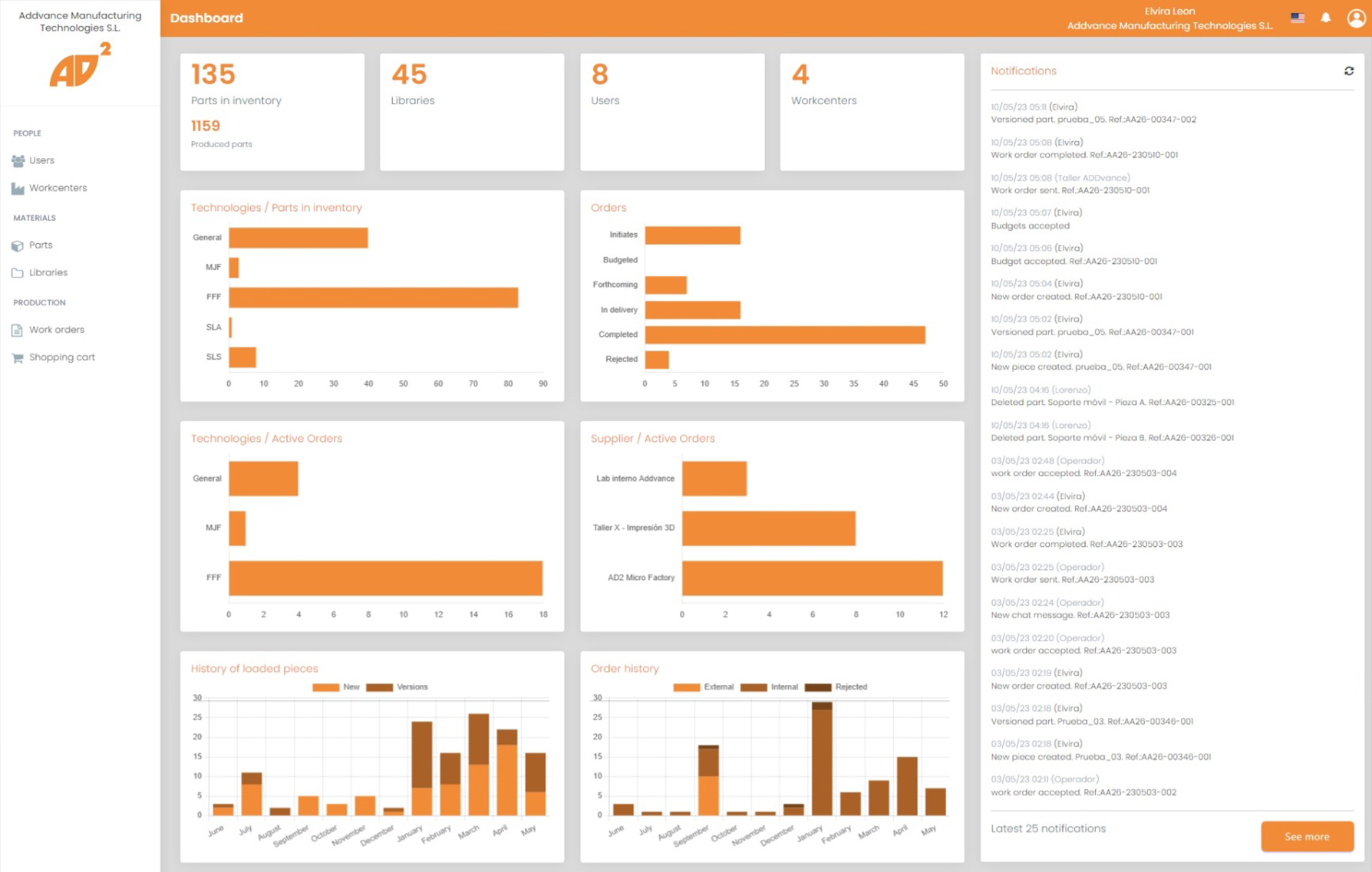
This means that to mitigate specific supply chain risks, manufacturing can distribute geographically (fabricating products at multiple locations, often close to the point of demand), across the value chain (fabricating the products by other entities, such as supplier networks or even customers) and over time (spreading production over time in specific quantities to meet sporadic and hard-to-predict demand).
Moving forward, to companies that are still looking to converge AM and lean management, ADDVANCE’ CEO recommends following a few steps:
“First, carry out a feasibility analysis of the manufacturing model, assessing the benefits, challenges, and costs in implementation, both technically and economically. If the result of the analysis is positive, then identify the most appropriate AM technologies to carry it out, and consider internalization or externalize totally or partially, with external manufacturing suppliers. The key is to choose the optimal AM technology, as we know there are many different options, each of them suitable for different applications and materials.
Once the manufacturing model is defined, the implementation is simple. However, it is important to count with experts. Build a digital warehouse, a ‘digital twin’ of your physical warehouse, which collects all the information of parts and manufacturing process and operate it through a connected on-demand manufacturing platform, to assess an integrated, monitorable, and traceable process, and to guarantee the security of assets and intellectual property of the company.”
This article has first been produced in the May/June edition of 3D ADEPT Mag.