You may have heard it more than once: the transformative shift that the space field is undergoing is marked by the emergence of a “new space” economy. The New Space covers several industrial manufacturing fields that continuously attract companies seeking to put communications, observation, lab packages, and potentially mining into space.
To drive this billion-dollar industry, space ventures need to overcome several challenges to place satellites, probes, landers, telescopes or even spacecraft in orbit. At the technological level, Additive Manufacturing has proven its capability to alter the landscape of designing and producing launchers and space systems. But how far can we go with the technology?
What are the industrial catalysts driving AM adoption across key space domains? What are the industry gaps and hurdles that need to be addressed to make space missions a tangible reality?
This is just a short list of questions that the next Additive Talks session ambitions to discuss.
Entitled “New Space & AM: Current Applications driving industrialization & technological challenges”, this virtual panel will take place on Wednesday 21st February 2024 from 03.30 pm to 04.30 pm Central European Time – CET (09.30 am – to 10.30 New York Time, USA).
Around this virtual panel, one will find:
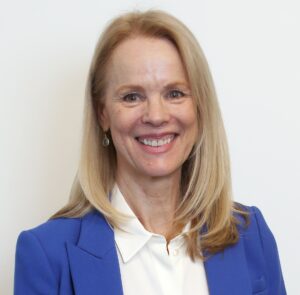
Melissa Orme, Vice President for Additive Manufacturing at Boeing. Orme leads the Additive Manufacturing activities ranging from engineering and manufacturing of new designs that differentiate Boeing products; to developing new materials and processes; to establishing the digital thread of the end-to-end values stream.
She is a renowned pioneer, innovator and leader in Additive Manufacturing, where her seminal work spans three decades and has resulted in 15 US patents and numerous peer-reviewed journal articles. She has a rich and diverse professional background, having begun her career in academia where she rose to the rank of Full Professor of Mechanical and Aerospace Engineering at the University of California Irvine.
There, she established globally recognized research laboratories in the field that is now termed ‘Additive Manufacturing,’ where she developed methods for controlled electrostatically charged and deflected molten metal droplet deposition for precision manufacturing, direct writing of electronic components, and precise powder production. Subsequently, she transitioned from academia to high tech startups where she served as the Chief Technology Officer of Morf3D, a company that is focused on producing and delivering flight-qualified additively manufactured hardware to the aerospace industry. From Morf3D she was recruited by Boeing to lead Additive Manufacturing across all business units.
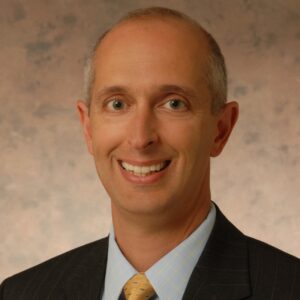
Next to Orme, one will find William C. Haddad, Director, Additive Design and Manufacturing at Collins Aerospace, an RTX business. Haddad currently leads Collins Aerospace’s Additive Design and Manufacturing organization. In this role, he is responsible for a global team working on all facets of Additive Manufacturing including digital tool chain, design for additive, training development, material characterization, and industrialization all on behalf of internal Collins business unit customers. Haddad’s organization has established two additive production facilities in Singapore and Monroe, North Carolina that are focused on delivering flight-ready hardware to Collins business units. Haddad has held positions of increasing responsibility in finance, operations strategy, strategic development, and supply chain across his nearly two decades of experience with Collins. His previous work experience includes Johnson & Johnson, Stanley Works, and The Hartford. He started his career as an engineer officer in the U.S. Army.
While Boeing and Collins Aerospace are two aerospace companies that no longer need any introduction, it’s fair to say that their AM efforts both aim to make the technology continuously evolve from research and development projects and low-cost tooling to printing high volumes of high-value metallic components and large families of tools – and this despite the stringent requirements of their industry.
Does this look like a discussion that you do not want to miss?