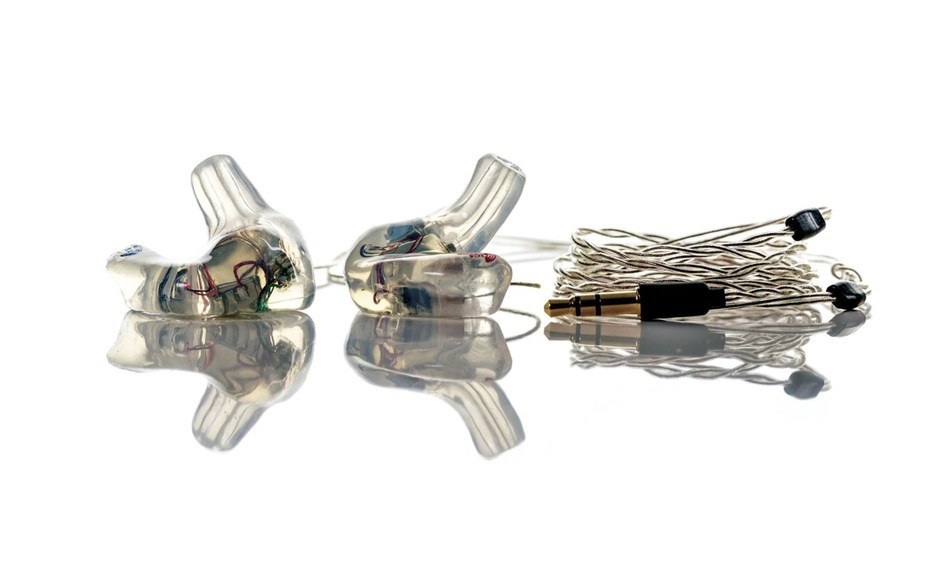
Mis à jour le 25.09
ACS Custom is a manufacturer of custom hearing protection, in-ear monitors and other communication devices. Like in any manufacturing workflow, it is always necessary to find new ways of improvements.
As for the UK-based digital production house, it has decided to integrate two Figure 4™ Standalone 3D printers in its manufacturing workflow. Unveiled last year, the platform integrates high speed digital molding, a process that speeds and simplifies the production of plastic parts.
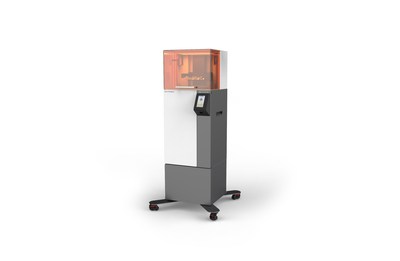
According to experts, the platform allows up “to 15x throughput improvements versus competitive offerings, at up to 20 percent lower cost of current manufacturing processes.”
In ACS Custom case, the manufacturer has realized a 4X increase in capacity and 2X increase in efficiency while reducing material consumption by 50% and labor cost by as much as 80% on one part.
ACS produces custom devices and in-ear audio monitors for musicians, and custom in-ear communication devices for the UK military. The company utilizes a 100% digital production workflow that includes 3D scanning a person’s ear, importing that data into design software to design the end part, and 3D printing an eggshell mold which is then cleaned and filled with silicon. Once the silicon is set, the mold is broken away, and electronic components are added to complete the device.
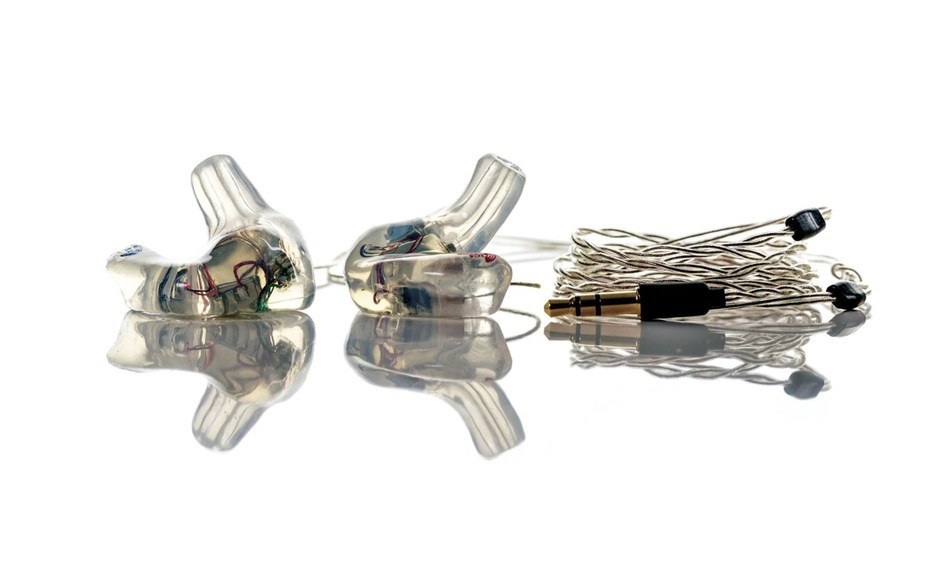
The company combines the use of it Figure 4 with the Figure® 4 PRO-BLK 10 material and the 3D Sprint® software of the manufacturer.
The material is a photopolymer that integrates thermoplastic behaviors and that provides a combination of speed, accuracy, strength, and durability previously only associated with injection molding output. Designed for AM, it has unique and compelling properties that represent significant improvements in first-time print yield, heat deflection, UV stability, durability, flexibility, and impact strength, while also enabling new biocompatible and direct digital production workflows such as the one designed for ACS. Figure 4 PRO-BLK 10’s material properties – which include being biocompatible capable per ISO10993-5 and ISO10993-10 – results in a long-wear device that enables enhanced sound transmission and quality.
“Figure 4 technology has been an integral part of our workflow for the past two years,” said Andy Shiach, managing director, ACS Custom. “Through collaboration with 3D Systems’ team, we’ve been able to maximize the technology’s role in our business and have elevated our company to a whole new level. The unique solution was designed specifically for our application and has helped us dramatically increase production capacity and efficiency as well as unparalleled surface finish to deliver high-quality products to our customers.”
Other technologies for custom hearing protection
Other manufacturers have dedicated their technology to the hearing aid industry. Rapid Shape for instance manufactures hearing 3D printers that serve in the manufacturing of biocompatible hearing aid parts.
In the same vein, EnvisionTEC’s 3D printers are often of a great help for companies like Sonova that specialize in hearing aid solutions. With EnvisionTEC’s 3D printers for instance, Sonova aims to run a great number of 3D printing factories around the world that may produce customized solutions for people in need.
The only factor that might raise a certain concern, is that, the more companies integrate advanced technologies such as 3D printing in their workflow, the more, some labor costs will be reduced.
For further information about 3D Printing, follow us on our social networks and subscribe to our newsletter!
Would you like to be featured in the next issue of our digital magazine? Send us an email at contact@3dadept.com
//pagead2.googlesyndication.com/pagead/js/adsbygoogle.js
(adsbygoogle = window.adsbygoogle || []).push({});