Combien de fois avez-vous vu le mot « allègement » utilisé à côté de « fabrication additive » ? Si va au-delà du buzz que cette combinaison de mots pourrait créer, on se rend compte que ce concept de fabrication implique des équations de valeur pour des types de pièces spécifiques, ce qui peut conduire à des améliorations sur des produits existants, à de nouveaux modèles commerciaux et à de nouveaux marchés.
« Faire plus, avec moins » a toujours été (et, d’une certaine manière, reste) l’objectif principal de l’allègement – un concept de fabrication qui exige de tirer parti d’un large éventail de méthodes pour que les pièces et produits industriels soient plus légères tout en conservant ou en améliorant leurs caractéristiques techniques et mécaniques.
L’intérêt pour ce concept de fabrication a commencé avec les entreprises aérospatiales qui cherchaient à réduire la taille, le nombre et le poids des pièces. À l’époque, l’idée était assez simple : chaque gramme enlevé du poids d’un avion équivaut à une réduction de carburant. Dans un autre domaine, ils ont constaté que la réduction de la taille des pièces des satellites pouvait offrir plus d’espace pour ajouter une batterie, augmentant ainsi la durée de séjour du satellite dans l’espace. Au fil du temps, les équipes de R&D ont exploré les avantages de ce concept de FA pour d’autres applications et industries, et ont découvert que les avantages en termes de matériaux, de performances, de coûts et de délais de fabrication peuvent également être d’une importance capitale.
L’article ci-dessous a pour but de comprendre les bases entourant « l’allègement des pièces fabriquées de manière additive ». En mettant l’accent sur la perspective du logiciel, l’article discute des facteurs décisifs qui conduisent à l’allègement des pièces, ainsi que quelques stratégies logicielles qui peuvent être explorées dans ce processus.
Les facteurs décisifs qui peuvent conduire à l’allègement des pièces
Notons que l’allègement est avant tout souvent compris comme le retrait de matière d’un assemblage ou d’une pièce pour en réduire le poids. En théorie, c’est exactement ce qui se passe. C’est aussi la raison pour laquelle, l’accent est généralement mis sur la « réduction des matériaux » et/ou le remplacement de certains matériaux par d’autres matériaux plus légers ou pouvant apporter des gains supplémentaires.
« Il est possible de réduire le poids global d’une pièce en choisissant des matériaux ayant une résistance spécifique plus élevée. Par exemple, si nous comparons un acier inoxydable, un alliage d’aluminium et un alliage de titane, la résistance spécifique plus élevée de l’alliage de titane permettra d’utiliser moins de matériau pour atteindre le même niveau de performance », note Rhushik MATROJA, CEO et cofondateur de la société de logiciels Cognitive Design Systems.
Cet accent mis sur les « matériaux » a donc une incidence sur la conception de la pièce, qui doit refléter la manière dont les changements fondamentaux apportés à la conception permettent de réduire la consommation de matériaux et, en fin de compte, le temps de construction.
Cette nécessité de réduire le poids en utilisant le bon matériau est souvent abordée parallèlement à un autre problème urgent : les déchets. S’il suscite de plus en plus de questions sur le caractère durable du processus de production, il soulève également un certain nombre de défis qui méritent d’être pris en compte au niveau de la conception. C’est en tout cas ce qu’explique Rhushik MATROJA :
« Étant donné que l’allègement de toute structure aura un impact direct sur la performance mécanique de la pièce, il doit être effectué en gardant à l’esprit la performance mécanique du matériau.
La fabricabilité est l’un des facteurs les plus influents de l’allègement. On peut avoir la conception théorique la plus légère et la plus performante, mais cette conception devient inutile si elle n’est pas fabricable.
Un autre facteur important est le coût de la pièce. Si la pièce allégée à l’aide de l’optimisation topologique n’est pas bien conçue, il y aura des coûts supplémentaires pour la suppression des structures de support excessives et pour le traitement de surface supplémentaire. D’autre part, l’impression de structures en treillis et de structures TPMS peut augmenter le temps d’impression, ce qui entraîne une augmentation du prix de la pièce. »
Les stratégies logicielles au cœur de l’allègement
Cela fait deux décennies que les fabricants tirent parti de la fabrication additive, mais les progrès en matière d’allègement des pièces ne sont apparus que récemment, grâce à l’utilisation de nouvelles stratégies logicielles conçues pour relever ce défi.
L’une des premières stratégies logicielles souvent explorées à ce niveau est l’optimisation de la topologie. La capacité d’optimiser la topologie des pièces en fonction d’objectifs de rigidité ou de résistance basés sur les méthodes des éléments finis (FEM) permet de concevoir des pièces légères de manière ciblée. Cette stratégie de conception optimise la disposition des matériaux dans un espace de conception donné, pour un ensemble donné de charges, de conditions limites et de contraintes.
L’utilisation de structures de remplissage en treillis ou TPMS est une autre méthode intéressante à explorer. Il s’agit d’hybrides de matériaux solides et d’espaces vides qui sont créés de telle sorte qu’ils dictent les propriétés mécaniques. L’utilisation de structures en treillis intelligentes peut aider à explorer des propriétés thermomécaniques intéressantes. « Les connaissances sur les performances de ce type de structures sont très importantes. Des processus de conception et de simulation sont nécessaires pour obtenir des informations sur les performances. Cognitive Design Systems a créé une grande base de données de ces méta-matériaux avec leurs propriétés mécaniques. Notre outil « Infill Optimizer », qui fait partie de notre logiciel de FA « Cognitive Additive », place intelligemment ces structures en fonction de la trajectoire des contraintes afin de réduire le poids total sans diminuer les performances mécaniques », explique Matroja.
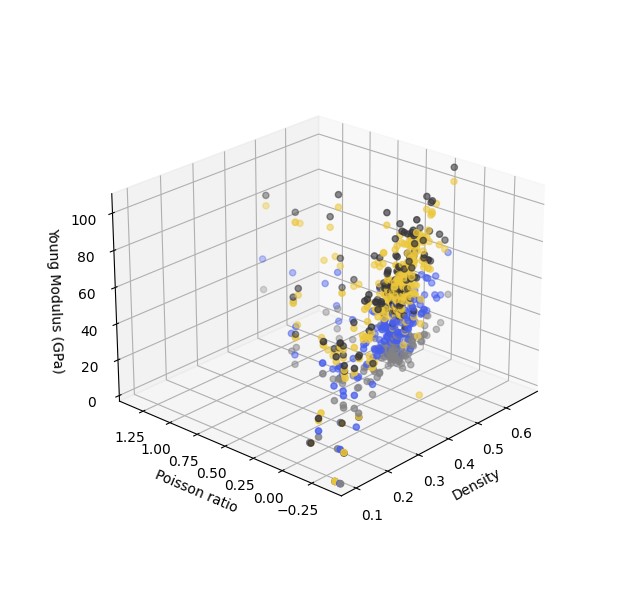
Selon Matroja, l’optimisation de la topologie convient généralement mieux aux technologies à base de poudre/résine, tandis que la stratégie de remplissage fonctionne mieux pour les procédés FFF ou DED.
La consolidation des pièces est une stratégie qui nécessite une expertise et une capacité solides pour rassembler plusieurs pièces en une seule. Si elle est bien conçue, la pièce peut offrir une meilleure fonctionnalité. Il y a quelques années, par exemple, Airbus Defence and Space et 3D Systems ont mis au point le premier filtre radiofréquence (RF) imprimé en métal, testé et validé pour une utilisation dans des satellites de télécommunication commerciaux. Les filtres RF sont traditionnellement conçus à l’aide d’éléments standard tels que des cavités rectangulaires et des sections de guide d’ondes avec des coudes perpendiculaires, avec des formes et des connexions dictées par des processus standard tels que le fraisage et l’érosion par étincelage. Généralement, les cavités des filtres RF sont produites en usinant deux moitiés qui sont boulonnées ensemble, ce qui augmente le poids, ajoute des étapes d’assemblage et des contrôles de qualité supplémentaires. À l’aide du logiciel CST MWS, un outil de simulation électromagnétique en 3D, l’équipe de 3D Systems a développé une cavité super-ellipsoïdale déprimée pour canaliser les courants RF et rejeter les signaux hors bande. La conception a été guidée par la fonctionnalité pure, et non dictée par la fabricabilité, et a abouti à une pièce à construction unique plus rapide à produire, réduisant les coûts de production et le poids de 50 %.
Viennent ensuite les Bord-côte conformes (Conformal ribbing). Cette technique est très répandue dans l’aérospatiale. Selon la société de logiciels nTopology, qu’elles soient construites à partir de polymères, de métaux ou de composites, les nervures conformes visent à rendre les parois plus fines tout en améliorant la résistance au flambage.
Les nouvelles solutions logicielles basées sur l’intelligence artificielle permettent aux ingénieurs concepteurs de « programmer » des algorithmes afin qu’ils prennent en compte les différentes contraintes de ce qui peut (ou ne peut pas) être réalisé avec un type de procédé de fabrication spécifique. De cette façon, leurs conceptions évoluent et se développent en quelque chose qui peut facilement être fabriqué par FA.
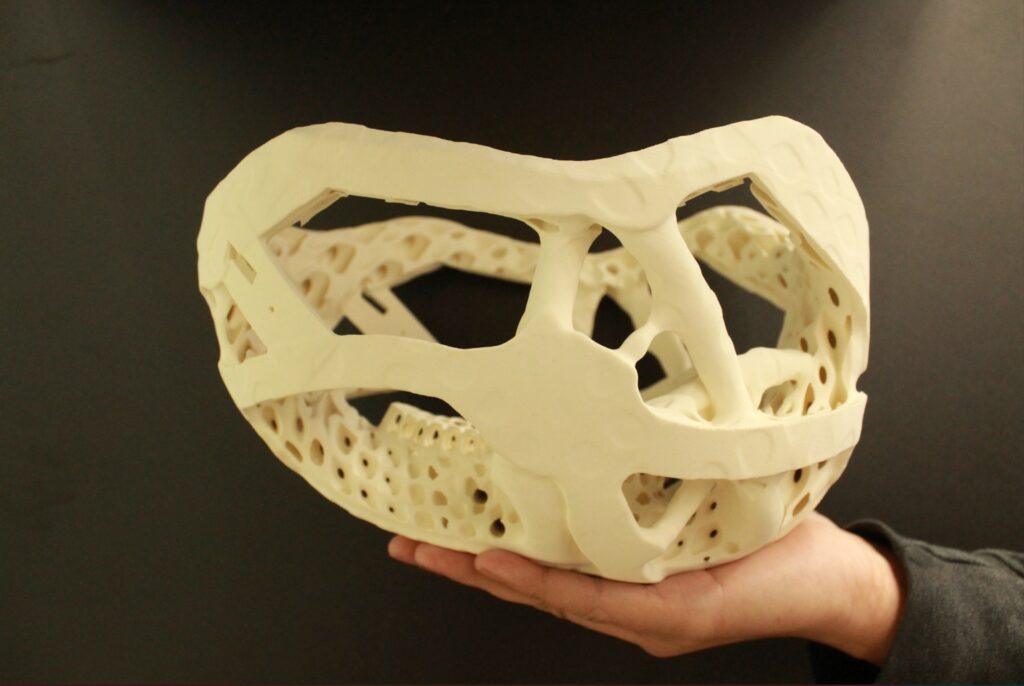
Réflexions finales
Le désir de tirer parti de toutes les capacités de la FA pour réduire les délais de commercialisation ou les coûts, incite les ingénieurs à développer des géométries de pièces alternatives, ce qui se traduit par des solutions techniques innovantes représentées dans les applications finales.
La vérité est que ce qui était autrefois considéré comme « léger » est désormais obsolète. Et cette tendance va se poursuivre, sans doute indéfiniment, car les solutions logicielles continuent d’évoluer.
Cet article a été initialement publié dans le numéro de Juillet/Août de 3D ADEPT Mag.
N’oubliez pas que vous pouvez poster gratuitement les offres d’emploi de l’industrie de la FA sur 3D ADEPT Media ou rechercher un emploi via notre tableau d’offres d’emploi. N’hésitez pas à nous suivre sur nos réseaux sociaux et à vous inscrire à notre newsletter hebdomadaire : Facebook, Twitter, LinkedIn & Instagram !