Researchers at the Department of Energy’s Oak Ridge National Laboratory recently achieved the production of large rotating steam turbine blades for generating energy in power plants.
Led by partner Siemens Technology, the U.S. research and development hub of Siemens AG, the project team used wire arc additive manufacturing.
These parts have traditionally been made using casting and forging facilities that have mostly moved abroad.
“There’s now a realization that we cannot get low-volume castings and forgings that exceed 100 or 200 pounds from the domestic supply chain,” said Michael Kirka, lead research and group leader for the Deposition Science and Technology group at ORNL. “It’s put us in an untenable position, especially as we see how international conflicts have affected the international movement of critical supplies.”
“When the Siemens wire arc research began in 2019, it focused on component repair. However, the scope expanded during the COVID-19 pandemic, when the wait for new cast steam turbine blades stretched to two years. Then the project broadened to include printing entire replacement parts, because these types of turbine engines are versatile enough to use in gas, coal and nuclear power plants, Kirka said.
Why wire-arc Additive Manufacturing?
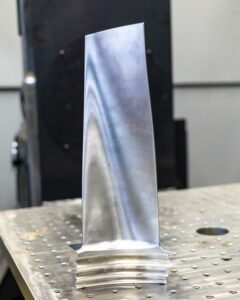
As you may know, WAAM is based on welding technology and is acknowledged for repairing existing parts.
According to the expert, although wire arc is a prominent 3D-printing technology, it had not previously been used to make a rotating component of this scale. Turbine blades typically have no parallel or perpendicular surfaces. Their contoured curves narrow toward the tip. “Being able to print and finish something with no locating features is a challenge,” he said. In addition, heavier parts of this size cool more slowly, adding sensitivity to the speed and order of depositing the layers.
Read more: Unveiling the disguised complexities of Wire-Arc Additive Manufacturing
The technology is ideal for parts that exceed 11 kg (25 pounds). ORNL was able to print the blade in 12 hours. With machining, the blade was finished in two weeks.
A key advantage to 3D printing is that it frees companies from dependence on specific manufacturing tools they don’t control, such as molds made by a single casting house for a single design. Many of the large-scale components in today’s turbines are several decades old, but because of closures and industry offshoring, the tools that created them have effectively disappeared, Kirka said. 3D printing offers a more reliable alternative because it can replicate any design.
With such 3D printed turbine plates, end users like Siemens Energy, a Siemens sister company that is also a partner in the project, could easily maintain and upgrade equipment under service contracts with electric utilities.
The steam turbine blade was printed in DOE’s Manufacturing Demonstration Facility. The MDF, supported by DOE’s Advanced Materials and Manufacturing Technologies Office, is a nationwide consortium of collaborators working with ORNL to innovate, inspire and catalyze the transformation of U.S. manufacturing.
Remember, you can post job opportunities in the AM Industry on 3D ADEPT Media free of charge or look for a job via our job board. Make sure to follow us on our social networks and subscribe to our weekly newsletter : Facebook, Twitter, LinkedIn & Instagram! If you want to be featured in the next issue of our digital magazine or if you hear a story that needs to be heard, make sure you send it to contact@3dadept.com.