Avant d’entamer une nouvelle année, chez 3D ADEPT Media, nous avons pris l’habitude de nous asseoir et de discuter des faits marquants, des étapes importantes ou des solutions qui ont d’une manière ou d’une autre marqué notre industrie tout au long de l’année. Les raisons qui peuvent expliquer le choix d’un fait marquant diffèrent d’une personne à l’autre. Pour une raison ou pour une autre, les choix ci-dessous soulignent l’ingéniosité et la résilience qui animent ce domaine en constante évolution.
1. Cinquante nuances de fabrication additive grand format
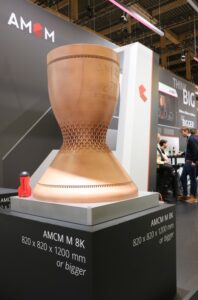
Les équipementiers qui fabriquent des imprimantes 3D grand format vivent une période intéressante. La demande pour ces imprimantes 3D augmente au fil du temps, ce qui conduit au développement de nouvelles solutions à d’autres étapes de la chaîne de fabrication. Prenons l’exemple de l’enlèvement de poudres : Le développement du système automatisé d’enlèvement de poudres SFM-AT1000-S de Solukon est le résultat d’une demande du fabricant de machines AMCM GmbH. Maintenant qu’AMCM peut régler des imprimantes 3D avec des enveloppes de construction de 820 x 820 x 1200 mm ou même plus, je suppose que le SFM-AT1500-S récemment lancé par Solukon conviendrait parfaitement à de telles imprimantes 3D métal.
Cela dit, la capacité à produire des grandes pièces est vraiment une tendance, quel que soit le type de processus de FA, qu’il s’agisse de l’impression 3D de composites, du procédé LPBF, du procédé WAAM, de l’impression 3D de polymères ou même de la photopolymérisation. Cette année, le point commun de la plupart des lancements d’imprimantes 3D est la capacité de fabriquer des pièces plus grandes en une seule impression.
2. La personnalisation reste la priorité des fabricants
Nous avons mis en évidence et vu des applications très intéressantes cette année. Aussi belles soient-elles, je m’interroge parfois sur leur raison d’être. L’argent étant actuellement le nerf de la guerre, la personnalisation suffit-elle à rendre la FA rentable ? La personnalisation peut même être à l’ordre du jour, mais est-elle nécessairement liée à la fabrication en série ? Jusqu’à présent et d’après nos observations, nous ne pouvons pas toujours avoir les deux. Toutefois, ceux qui ont réalisé des bénéfices avec la FA ont fourni des services de fabrication en série.
3. Les industries de semi-conducteurs et défense ouvrent la voie
Les secteurs de semi-conducteurs et la défense sont les deux secteurs verticaux où l’on observe une utilisation croissante des technologies de FA. Ce sont les secteurs verticaux à surveiller l’année prochaine.
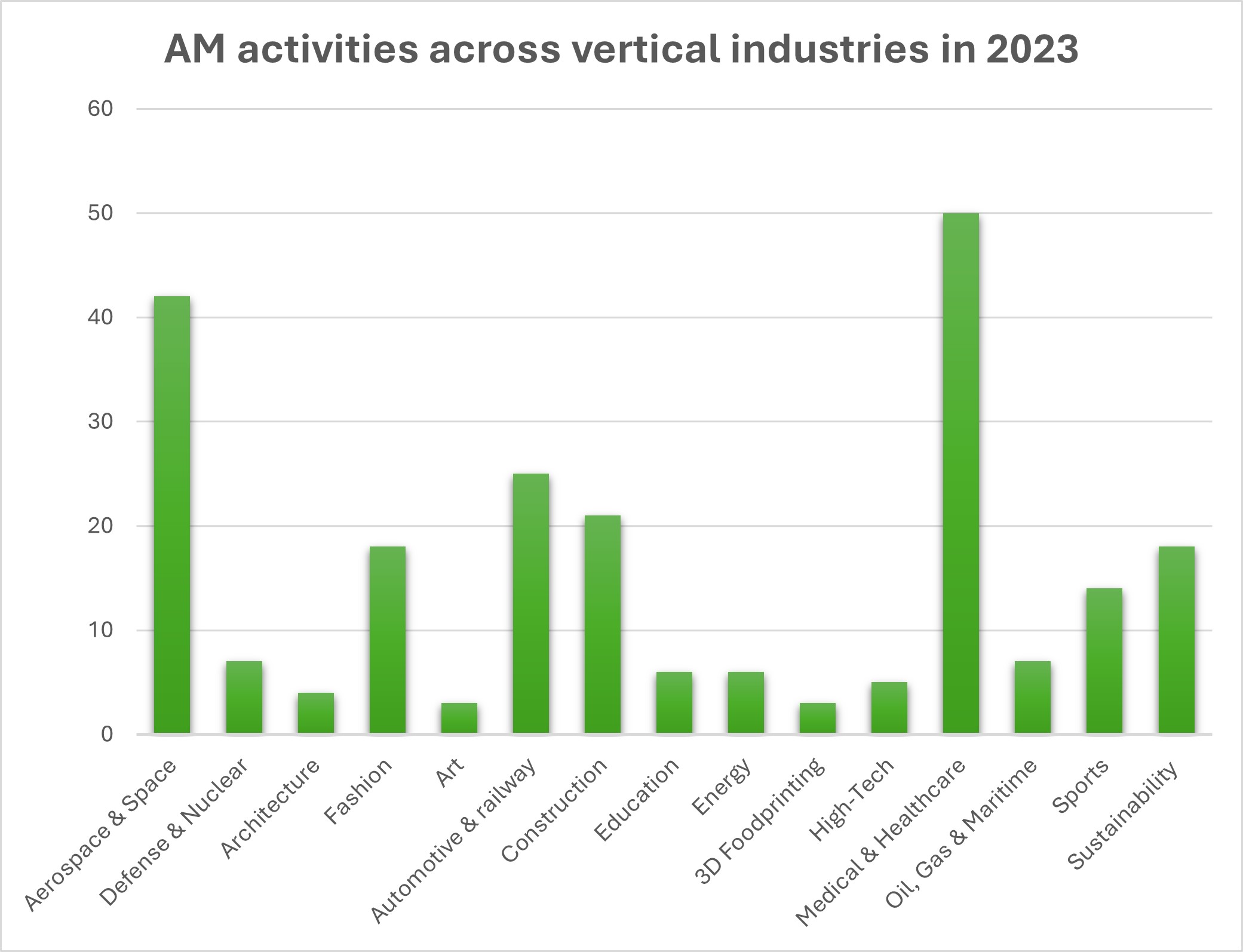
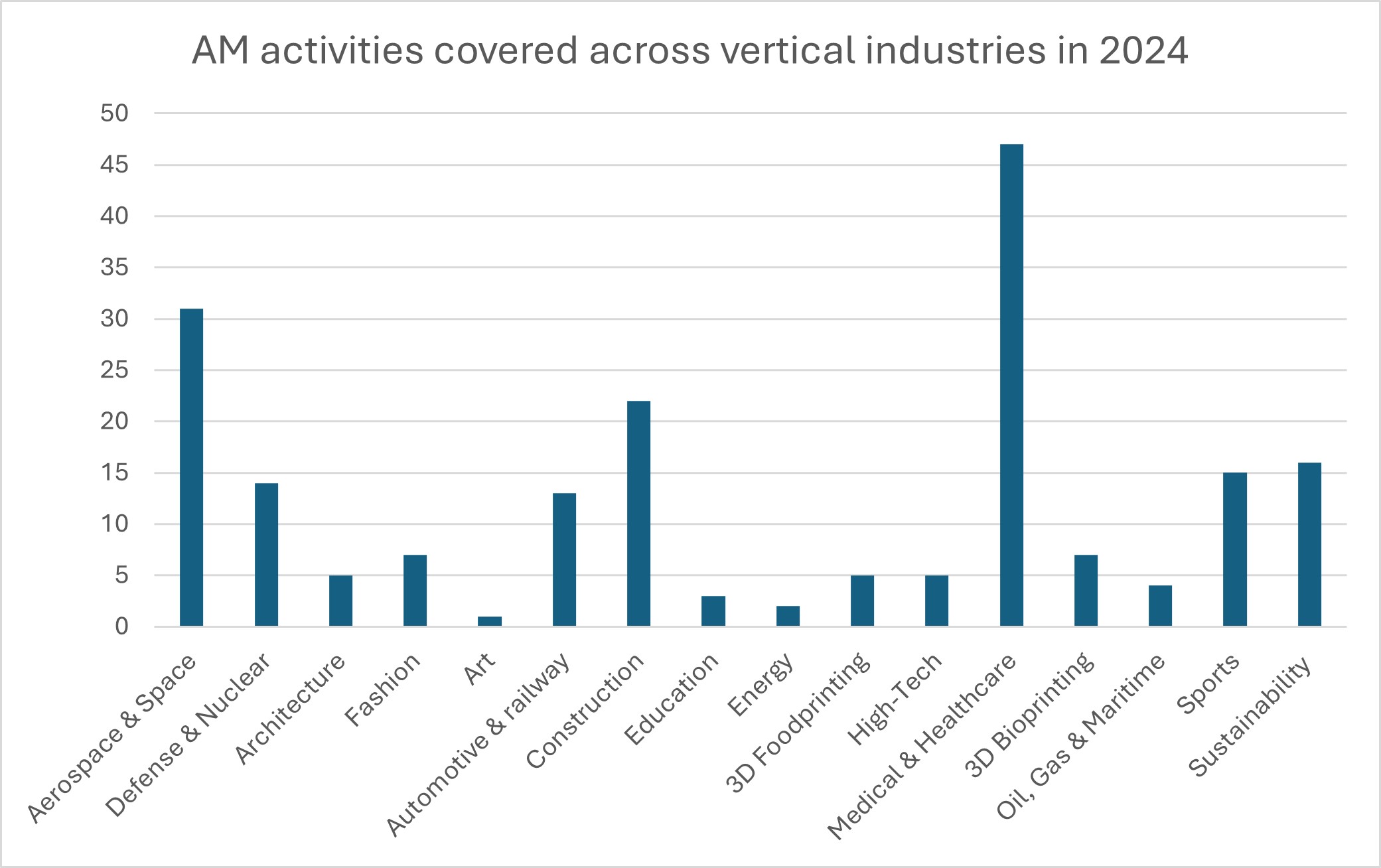
Les défis actuels de la production de semi-conducteurs comprennent la capacité de production mondiale, les longs délais de livraison et la demande d’approvisionnement – autant de problèmes qui peuvent être résolus par la FA. Si les procédés de photopolymérisation VAT et LPBF sont les technologies de FA qui ont été le plus mises en avant cette année pour ces applications, d’autres technologies peuvent également être des candidats idéaux pour la production.
Par rapport à l’année dernière, l’analyse de la couverture de cette année a révélé un intérêt croissant des organismes de défense pour la FA. Comme annoncé dans la première partie de cette analyse (PP xxx de ce magazine), nous ne sommes pas au bout de nos peines. Que ce soit en Europe ou aux États-Unis, les organismes de défense continueront à investir dans la FA… Le nombre d’événements qui mettent en lumière l’utilisation de la FA dans ce secteur vertical en témoigne. Malgré la nature sensible de la couverture de la FA dans ce secteur vertical, il serait intéressant de voir ce que la FA peut faire de mieux dans ce secteur vertical.
4. L’extrusion de matériaux, le segment où nous avons vu le plus de lancements d’imprimantes 3D
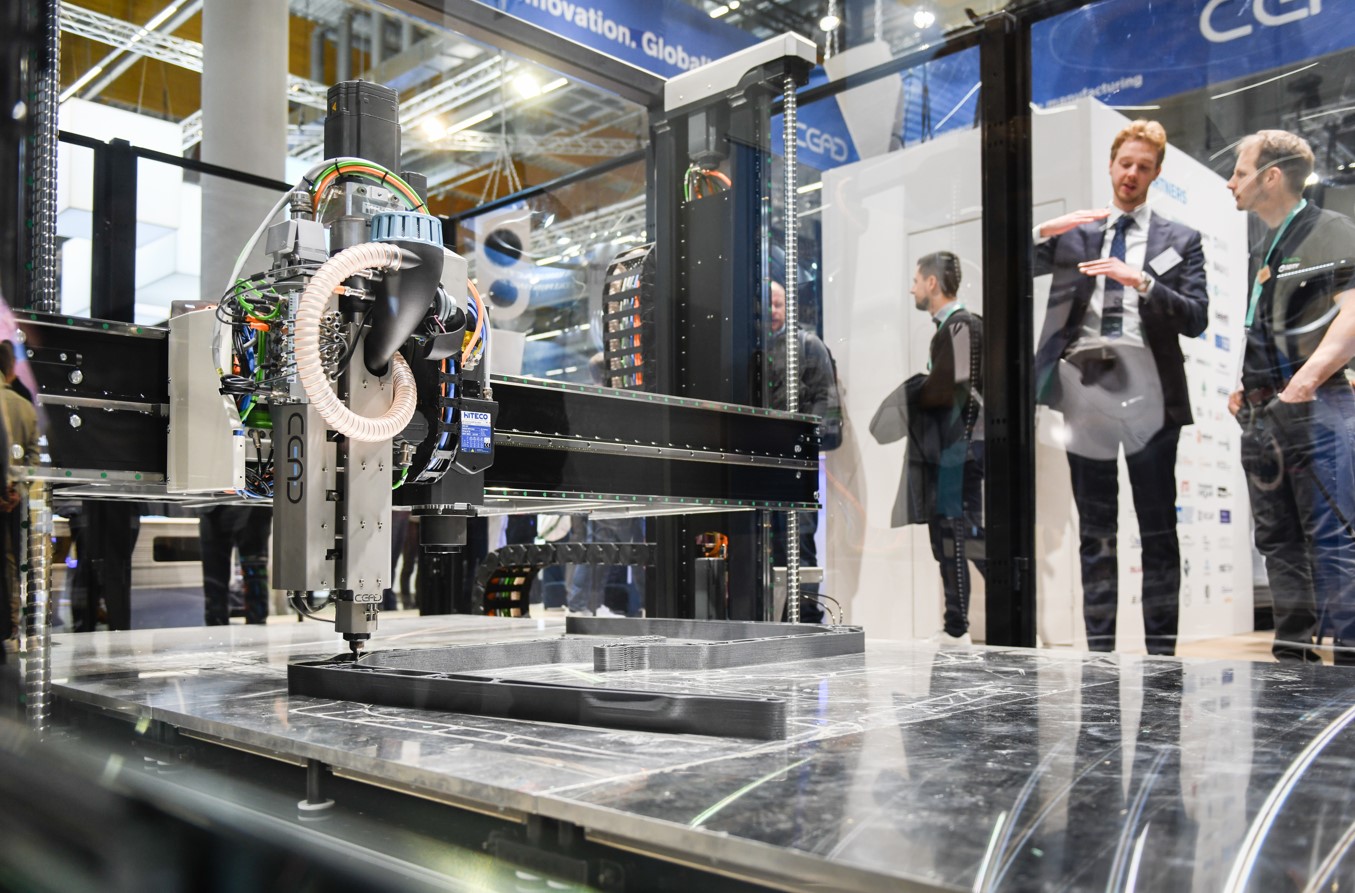
La majorité des lancements d’imprimantes 3D couverts cette année entrent dans la catégorie de l’extrusion de matériaux, suivie de près par la fusion sur lit de poudre et la photopolymérisation .
Même si la plupart de ces lancements s’inscrivent dans des catégories prétendument connues de procédés de fabrication additive, chaque imprimante 3D dispose d’une terminologie propre à son fabricant. Cela souligne la nécessité d’un cadre linguistique commun qui permette aux utilisateurs et aux fournisseurs de technologie de collaborer plus efficacement.
Cela dit, nous ne pouvons pas ignorer les équipementiers qui se sont démarqués en lançant des processus de FA intrigants. Parmi eux, Rosotics et son Halo « supercreator » – une imprimante 3D métal grand format décrite comme étant à l’intersection de la science des matériaux et de l’IA ; Fugo Precision 3D et sa solution d’impression 3D centrifuge ainsi qu’ADDiTEC et sa machine hybride qui combine à la fois le jet de métal liquide et le dépôt d’énergie dirigée par laser avec l’usinage à commande numérique.
5. L’essor de l’imprimante 3D d’entrée de gamme
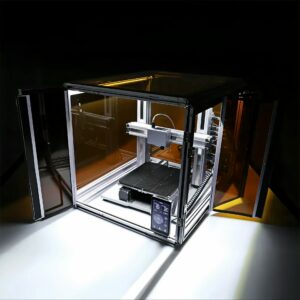
Les équipementiers qui fabriquent des imprimantes 3D de bureau et d’entrée de gamme revendiquent leur capacité à répondre à la demande d’industrialisation et, pour être honnête, après ce dernier Formnext, je suis sûre qu’ils peuvent tenir cette promesse – du moins une partie de cette promesse.
Selon le dernier rapport de CONTEXT, la catégorie bas de gamme ENTRY-LEVEL (<$2,500) a excellé avec des livraisons en hausse de 34% en séquentiel, de 65% en année pleine et de 41% sur une base trimestrielle. Creality a continué à écraser la concurrence avec des livraisons en hausse de 64 % (et de 45 % sur l’ensemble du semestre), représentant ainsi 47 % de toutes les imprimantes livrées dans cette catégorie de prix au cours du trimestre. Son taux de croissance n’a été surpassé que par Bambu Lab, qui a de nouveau enregistré une croissance à trois chiffres de ses livraisons en glissement annuel (+ 336 %), ce qui lui confère 26 % des parts de marché mondiales. Au total, 94 % des livraisons dans cette catégorie de prix inférieure à 2 500 $ ont été effectuées par les quatre premiers fournisseurs – Creality, Bambu Lab, Anycubic et Elegoo.
6. Le paysage des logiciels de FA reste fragmenté
Plus nous progressons, plus le paysage logiciel se fragmente. C’est probablement le segment de la chaîne de valeur de la fabrication qui révèle le plus le besoin d’un cadre linguistique commun et d’une plateforme où l’on peut accéder à tout.
C’est un paysage qui est de plus en plus façonné par un nombre croissant de solutions alimentées par l’IA. Même si je reconnais le potentiel de ces solutions, je ne peux m’empêcher de rappeler aux concepteurs de produits de rester prudents. En effet, plus les limites des technologies alimentées par l’IA sont repoussées, plus les concepteurs de produits doivent être attentifs et faire de leur mieux pour ne pas laisser de côté leur créativité.
En outre, si les solutions logicielles destinées à améliorer la production se présentent sous de nombreuses formes et couleurs, le fil conducteur de la couverture de cette année reste leur capacité à optimiser la fabrication tout en réduisant le nombre d’échecs de construction.
7. Surveillance des processus :Outils d’identification des défauts
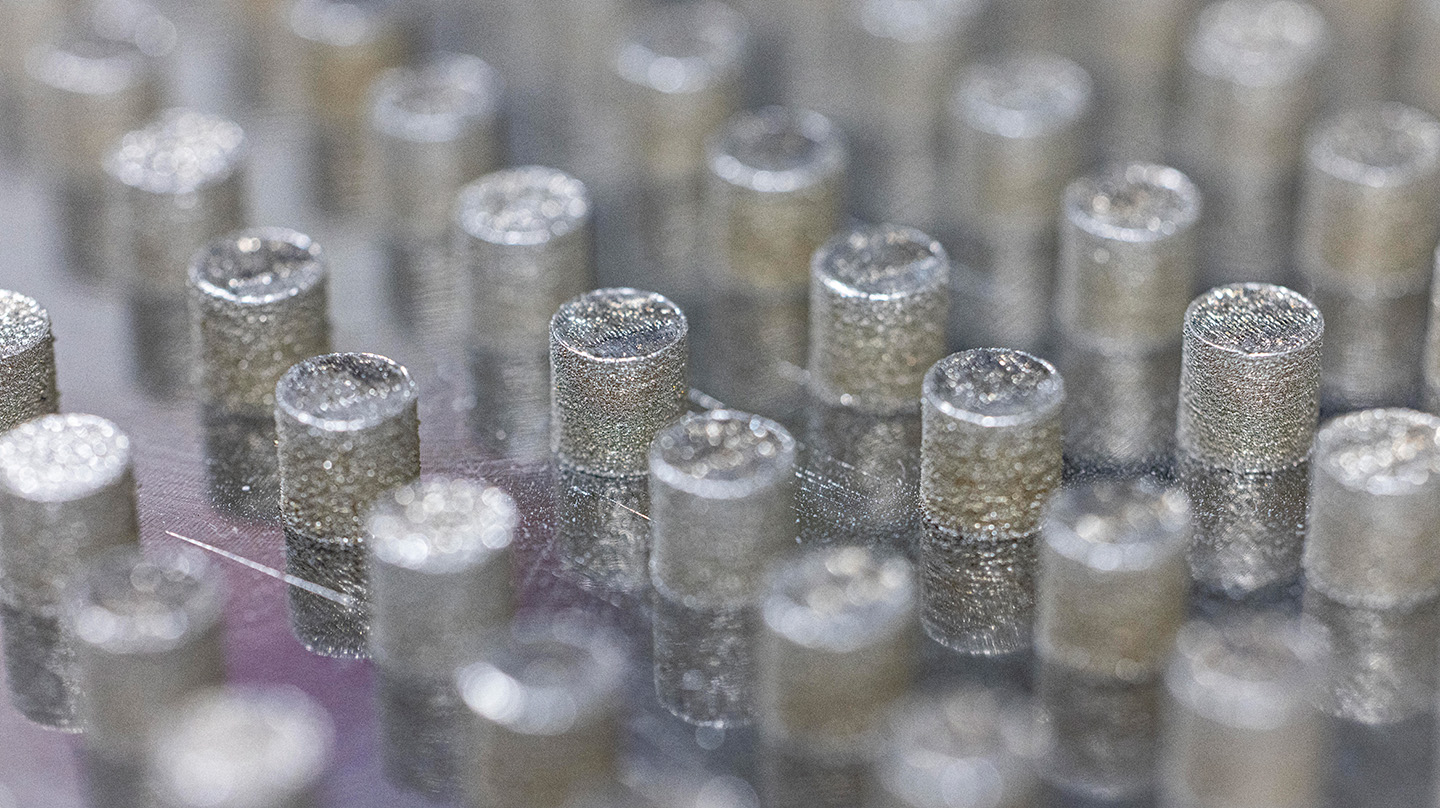
Selon moi, les progrès en matière d’identification des défauts sont l’une des meilleures choses qui puissent arriver à cette industrie. Son importance est tout simplement sous-estimée et pourtant, au-delà de la capacité à améliorer la qualité de la surface et les propriétés mécaniques des pièces imprimées en 3D, ses avantages peuvent conduire à des économies de matériaux, à une amélioration de la capacité des machines, à une réduction du temps d’essai et à la prévention des défaillances, des accidents et des essais inutiles.
Dans la liste des solutions mises en avant cette année, que ce soit au niveau de la recherche ou dans le domaine des solutions déjà commercialisées, j’espère voir plus de cas de défauts que l’on peut identifier « en écoutant » lorsqu’ils se produisent dans une imprimante 3D métallique et des cas liés à la solution logicielle de Phase3D.
8. La combinaison de plusieurs procédés de fabrication
Décrire ce point comme un point fort est probablement une hyperbole car nous constatons généralement une combinaison des technologies de FA et des processus de fabrication conventionnels dans les applications qui impliquent une fabrication en série.
Cependant, il est assez rare de voir une combinaison de deux procédés de FA dans une même pièce – comme cela a été découvert lors du récent salon Formnext.

La fabrication consiste à appliquer le procédé DED sur des pièces de cuivre en lit de poudre.
L’un des principaux avantages de ces techniques reste la possibilité de fournir des propriétés matérielles optimisées localement qui peuvent remplir des fonctions spécifiques, ce qui pourrait être bénéfique pour un grand nombre d’applications si elles sont bien exploitées.
9. Pièces imprimées en 3D en tungstène
Il y a quelque chose de fascinant dans le tungstène et dans la façon dont les fabricants et les chercheurs essaient de « déchiffrer le code » de sa fabrication. Pour rappel, la dureté du tungstène et son point de fusion extrêmement élevé l’ont toujours rendu difficile à traiter par les technologies de FA. Alors que le procédé LPBF est souvent mentionné comme l’un des processus de FA pouvant le traiter, je souhaite faire la lumière sur les fabricants de pièces qui étaient prêts à explorer d’autres techniques cette année, parmi lesquelles la fabrication additive par faisceau d’électrons ainsi que le procédé DED par soufflage de poudre laser.
10. Le Raptor 3 de SpaceX fait confiance à la fabrication additive
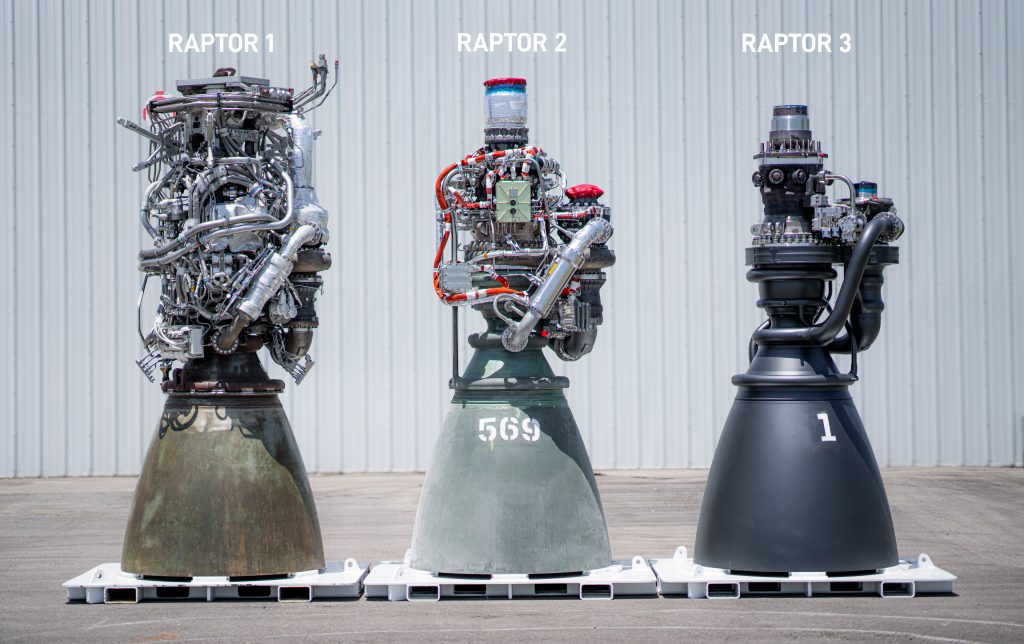
Si vous pensiez avoir perdu la foi dans la fabrication additive, le moteur Raptor 3 de SpaceX devrait suffire à vous faire changer d’avis. C’est certainement l’application qui a le plus attiré l’attention cette année, et pour cause :La fabrication additive métal a joué un rôle essentiel dans la transformation de l’exploration spatiale, en permettant la transition de programmes dirigés par l’État à des entreprises privées, en réduisant les barrières de coûts et en raccourcissant le délai de développement des technologies spatiales.
Avec cette innovation, l’équipe de SpaceX a partagé un zeste de sa recette : moins de travail et d’étapes d’inspection, moins de main-d’œuvre, une sécurité accrue et une conception radicalement optimisée.
Que demander de plus ?