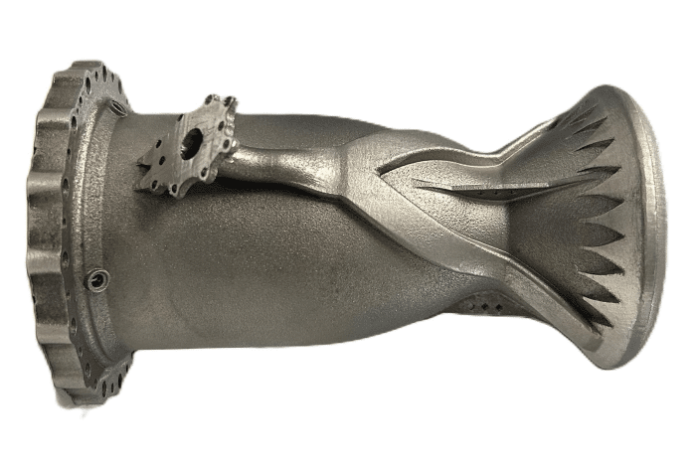
Wipro 3D, fournisseur de services d’impression 3D, s’associe à l’Organisation indienne de recherche spatiale (ISRO – Indian Space Research Organisation) pour fabriquer un moteur de fusée PS4 imprimé en 3D. Le moteur-fusée équipe le quatrième étage du Polar Satellite Launch Vehicle (PSLV), un système de lancement non réutilisable conçu pour placer des satellites d’observation de la Terre et des satellites scientifiques sur des orbites précises permettant de multiples applications telles que la télédétection, l’océanographie, la cartographie, la cartographie minérale, l’alerte en cas de catastrophe, etc.
Pour assurer une mise en orbite précise, l’étage PS4 est équipé de systèmes avancés de navigation, de guidage et de contrôle. Son adaptabilité à différents types de missions spatiales est renforcée par sa capacité à prendre en charge de multiples capacités de redémarrage et adaptateurs de charge utile.
Le moteur PS4, traditionnellement fabriqué par usinage et soudage, a fait l’objet d’une refonte grâce à la fabrication additive.
Les deux partenaires se sont appuyés sur la conception pour la fabrication additive (DfAM) et la technologie de fusion laser sur lit de poudre (LPBF) pour consolider les composants complexes multiples et diversifiés du moteur PS4 en une seule unité de production unifiée, améliorant ainsi l’efficacité de la production et l’intégrité structurelle.
Yathiraj Kasal, GM & Business Head, Wipro 3D, a déclaré : « Nous sommes honorés de collaborer avec l’ISRO sur ce projet, qui met en évidence le potentiel de la fabrication avancée dans l’espace. Ce partenariat fait non seulement progresser l’initiative « Make in India » de l’ISRO, mais il encourage également l’innovation et la fabrication nationales. C’est un honneur et un privilège de fabriquer le moteur PS4 du véhicule PSLV. Nous attendons avec impatience la réussite de la deuxième série d’essais pour voler haut aux côtés de l’ISRO ».
Le moteur PS4 imprimé en 3D, doté de canaux de refroidissement complexes intégrés, donne la priorité à la durabilité et à l’efficacité dans sa conception, avec un minimum de gaspillage de matériaux et d’opérations d’usinage après impression. Des essais rigoureux du matériel dans les installations du complexe de propulsion de l’ISRO à Mahendragiri ont confirmé les performances du moteur dans des conditions réelles, répondant aux normes de sécurité et d’efficacité de la conception.
Les principaux paramètres de performance de l’essai de longue durée du moteur-fusée imprimé en 3D de l’ISRO comprenaient la pression optimale de la chambre, la gestion du carburant, l’efficacité de la combustion et l’impulsion spécifique (Isp). L’adoption par l’ISRO de la fabrication additive offre une précision supérieure, une utilisation minimale des ressources et une réduction significative du gaspillage de matériaux et du temps de production.
N’oubliez pas que vous pouvez poster gratuitement les offres d’emploi de l’industrie de la FA sur 3D ADEPT Media ou rechercher un emploi via notre tableau d’offres d’emploi. N’hésitez pas à nous suivre sur nos réseaux sociaux et à vous inscrire à notre newsletter hebdomadaire : Facebook, Twitter, LinkedIn & Instagram !