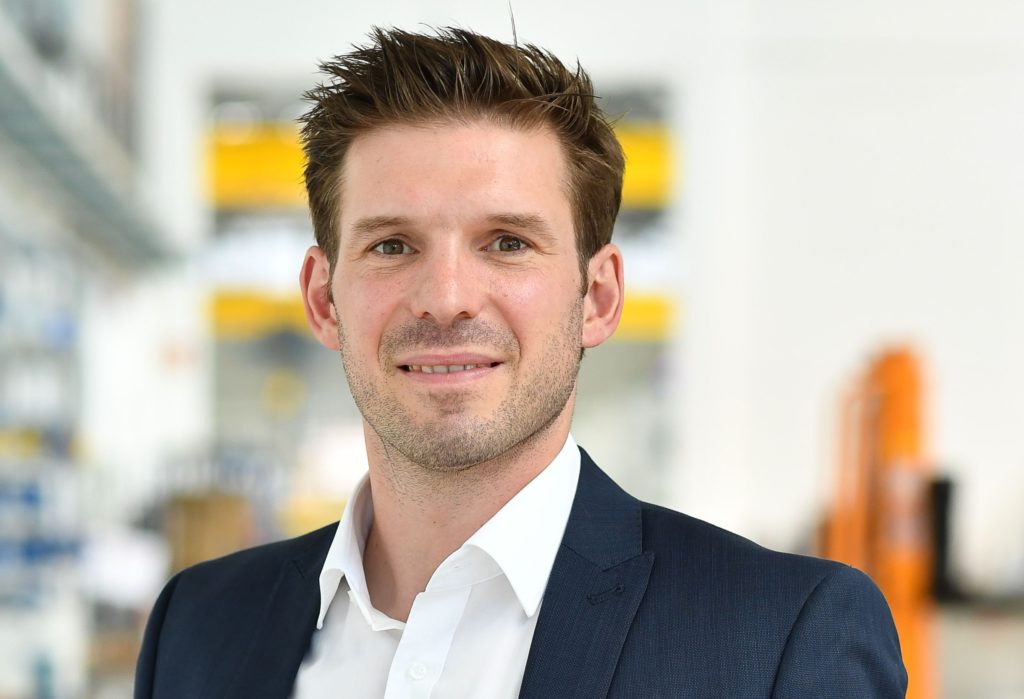
I had always thought the company voestalpine only produces and delivers metallic powders for the AM industry, until this conversation with Dr. Armin Wiedenegger, our guest in this Opinion of the Week series.
For the record, Wiedenegger joined the Austrian company six years ago and recently took over the role of Managing Director (MD) of the 3D Printing Research and Production group voestalpine Additive Manufacturing Center GmbH.
He therefore witnessed voestalpine beginnings in the AM industry four years ago and the development of its offering to push Additive Manufacturing forward.
2016, the research and development center for 3D Printing of metal parts
In 2016, when voestalpine decided to innovate in pioneering technologies, it opened a research and development center for additive manufacturing of metal parts. The company’s goal was to gather all its researches in the AM sector in this center.
“The Additive Manufacturing activities were officially launched. 2016 was the time when we started to use powders in the market. There was an increasing interest in metallic powders and the applications that could result from them. That’s how we started producing powders and providing services to the industry, services that consist in designing and producing parts for our customers”, states the Managing Director.
The voestalpine Additive Manufacturing Center leverages AM for the production of metal 3D printed components used across several industries such as the automotive, aerospace, tooling, to name a few. Over the years, the development of metal powders on the one hand, and the design and production of metal 3D printed components on the other hand, enabled the company to sign cooperation partnerships and envisioned new business locations on the international arena.
“Today, we are uniquely positioned to offer the full value chain to the additive manufacturing industry: additive manufacturing systems, production and distribution of powders, machining, coating, inspection. However, currently the bigger part of our offering remains the services related to the design and production of metal 3D printed components and the smaller part is the production of powders”, Wiedenegger outlines.
A brief snapshot of the production of powders
It should be noted that voestalpine BÖHLER Edelstahl & Uddeholms AB, two other voestalpine companies, take in charge the production of metal powders. The fine metal powders voestalpine BÖHLER Edelstahl & Uddeholms AB develop, are used by both external customers and the voestalpine Additive Manufacturing Centers.
The truth is the production of metal powders for AM is complex and requires thorough expertise.
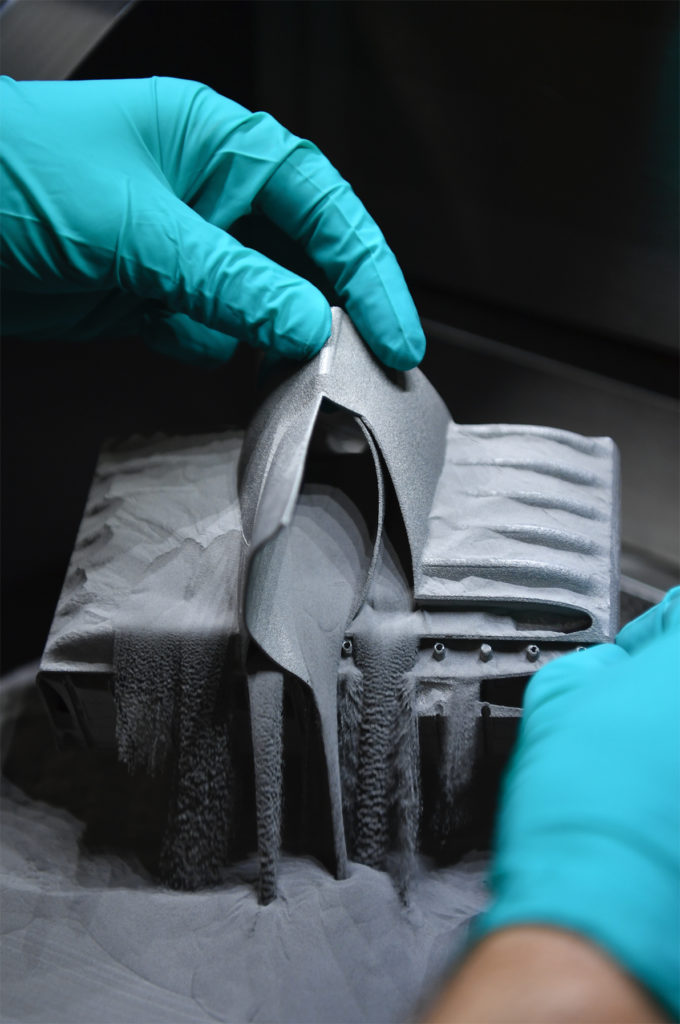
“There are so many varieties of this essential basic material. The production of metal powders for traditional production processes is completely different from the production of metal powders for AM processes. Sometimes, one can harness different kinds of production processes to manufacture powders for AM. I can only affirm that we benefit from the many years of experience the voestalpine Group has in the production of materials for powder metallurgical steels. ”, the Manager explains.
A close look at the design and production of metal 3D printed components
Speaking of their core business, Wiedenegger reveals that the key markets that really benefit from the company’s expertise in AM are the tooling industry as well as the oil & gas sector.
Industrial tooling applications the voestalpine AM Centers can provide include for instance tooling inserts with integrated cooling channels for plastic injection molding, high-pressure aluminum die-casting or extrusion. Despite the broad range of applications, enabled by AM, conventional manufacturing processes continue to be used to fabricate tooling. The reason might be that, for most AM tooling applications, users do not see the great benefit of AM compared traditional methods of fabrication.
Our conversation with Wiedenegger shows that they rather have to look at the processes. What process enables to save production time? What process enables to improve functionality or customize? The answer to these questions is always likely to be AM and for the voestalpine’ s representative, two steps are crucial in this process: the design and simulation process as well as the post-processing steps which include for their team, heat treatment and machining.
To illustrate the importance of the design and simulation process, the expert takes the example of the Flow Filter their team has developed.
The Flow Filter is a device specially engineered for high mixing and great filtering of unmolten plastic particles. The device’s role is to mix batches of different colors before the plastic is injected into the mold and also filter unwanted particles out of the melt.
A deep analysis of the voestalpine AM team showed that the standard solution of the Flow Filter delivers high-pressure loss (which increases energy consumption and negative optical effects) and high shear stress (which leads to lower mechanical properties, color changes and limited material choices).
By taking advantage of DfAM capabilities, the team has drastically improved the functionalities of the product: up to 33% less pressure drop, up to 50% less shear stress. The new Flow Filter integrates a large filtration area, and is now corrosion and wear resistant.
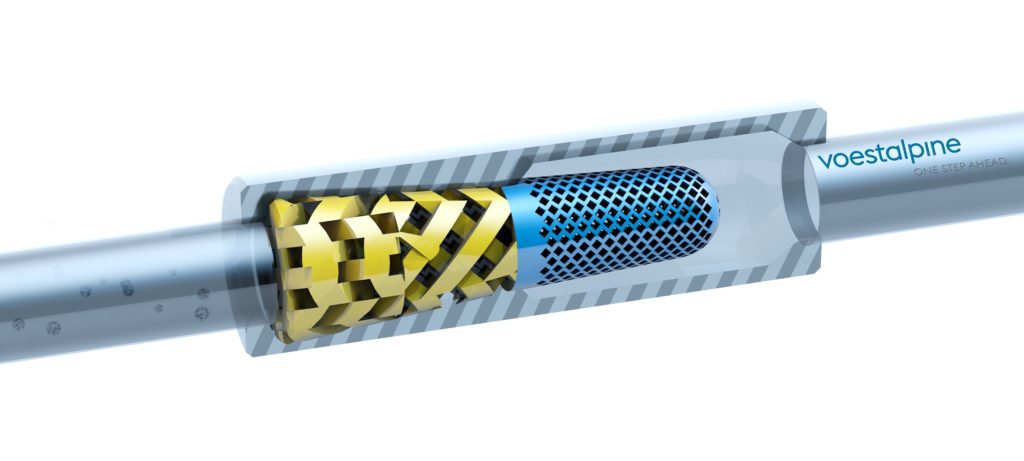
The Flow Filter constitutes the company’s first product developed for the medical industry.
Speaking of the oil & gas industry, Wiedenegger lays emphasis on the reason why AM applications for this industry are different from AM applications in other industries:
“The oil & gas industry has its own guidelines. Quality assurance for the manufacturing of components is not the same than in other industries. The continuous search for lightweight parts that we observe in aerospace and automotive applications for example, cannot be applied in the oil & gas industry so much. The main challenge here is to produce parts cheaper & faster than with conventionally process routes. Nevertheless, we actively work with partners to optimize the parts during the design stage. From the materials perspective, the most-widely used alloys are still nickel-base & cobalt chrome.”
The next step for voestalpine Additive Manufacturing
The voestalpine Group has invested in special powder atomization facilities at the Group subsidiaries voestalpine Böhler Edelstahl GmbH & Co KG, Austria, and Uddeholms AB, Sweden. Those two plants serve for the production of powders for the AM industry, and other industries as well.
“We are now busy building a very good global network but our next step in the short term is to push the business locally, especially in the tooling, oil & gas applications. The customers always have to be convinced of the advantages of AM, and the best way to convince them is to focus on applications where you are an expert in”, concludes Wiedenegger.
Remember, you can post free of charge job opportunities in the AM Industry on 3D ADEPT Media or look for a job via our job board. Make sure to follow us on our social networks and subscribe to our weekly newsletter : Facebook, Twitter, LinkedIn & Instagram ! If you want to be featured in the next issue of our digital magazine or if you hear a story that needs to be heard, make sure to send it to contact@3dadept.com