With a 30-year-plus pedigree in the industry, Additive Manufacturing continues to evolve. While it is clear to many that it is no longer just a solution for rapid prototyping, preconceptions regarding its usefulness as a production technology often need to be reassessed. As we evolve in a context where attention is shifting to higher-volume applications such as mass customization and the fabrication of standard parts, production losses due to process variability and inefficient machine use may be common concerns – leading AM users to ask themselves a million-dollar question: what are the key performance indicators for a “good” (metal) AM production?
Given the economic constraints of the current times, many assess the value of AM by its ROI – return on investment. It is not a bad thing in itself, as it may help determine the number of parts machines can produce or how much production has increased during an average workday, thus facilitating calculation of the cost-benefit. The problem is it can be difficult to define AM based on the numbers of ROI for a simple reason: AM doesn’t function the same way as the other machines on the floor.
AM users therefore need another approach to assess the success metrics of AM. This dossier is at the intersection of general business considerations and manufacturing needs of industries.
With a focus on four metal AM processes (DED, Cold Spray AM and Material Extrusion), this dossier aims to help AM users assess the manufacturing capabilities of AM; assess a technology production candidacy regarding mass production as well as discover the metrics that enable a user to determine a machine performance.
The constant comparison with traditional manufacturing: is it still worth it?
In general, and for a long time, assessing the metrics of success of AM has been done in comparison with traditional manufacturing. This somehow makes sense when one knows the key advantages (design freedom and flexible and rapid fabrication) AM brings compared to traditional manufacturing processes (acknowledged for their ability to allow mass production or large economy of scales).
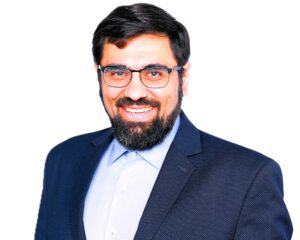
The truth is, talking about production and AM does not necessarily refer to mass production. “When talking about production and additive manufacturing, especially in metal AM, we do not necessarily always think of mass production. Production can involve a wide range of conditions from initial proof of concept (POC) and prototyping to custom or small batch production, low-rate initial production (LRIP), full rate production, and mass production,” Dr Behrang Poorganji, CTO of Nikon AM Synergy Inc explains.
Making a clear comparison with casting and forging, Herbert Koeck, Managing Director at Titomic explains:
“Unlike casting and/or forging foundries that can require larger economy of scales to justify tooling investment and parts production, cold spray additive manufacturing (CSAM) in certain geometries can offer an alternative source for near net parts. CSAM can be setup for mass production, although the investment in CS has the added advantage of versatility, where one day the machine is producing as a titanium caster, and the next day running as copper foundry.”
However, this comparison may not always be applicable when one realizes that AM often comes to enhance existing processes, making them more efficient and effective. Furthermore, AM is sometimes a victim of its own success: the more the technology advances, the more complexity it brings to other areas of the manufacturing chain, even when the process reduces industrial costs, shortens lead times, or enhances the sustainability of manufacturing.
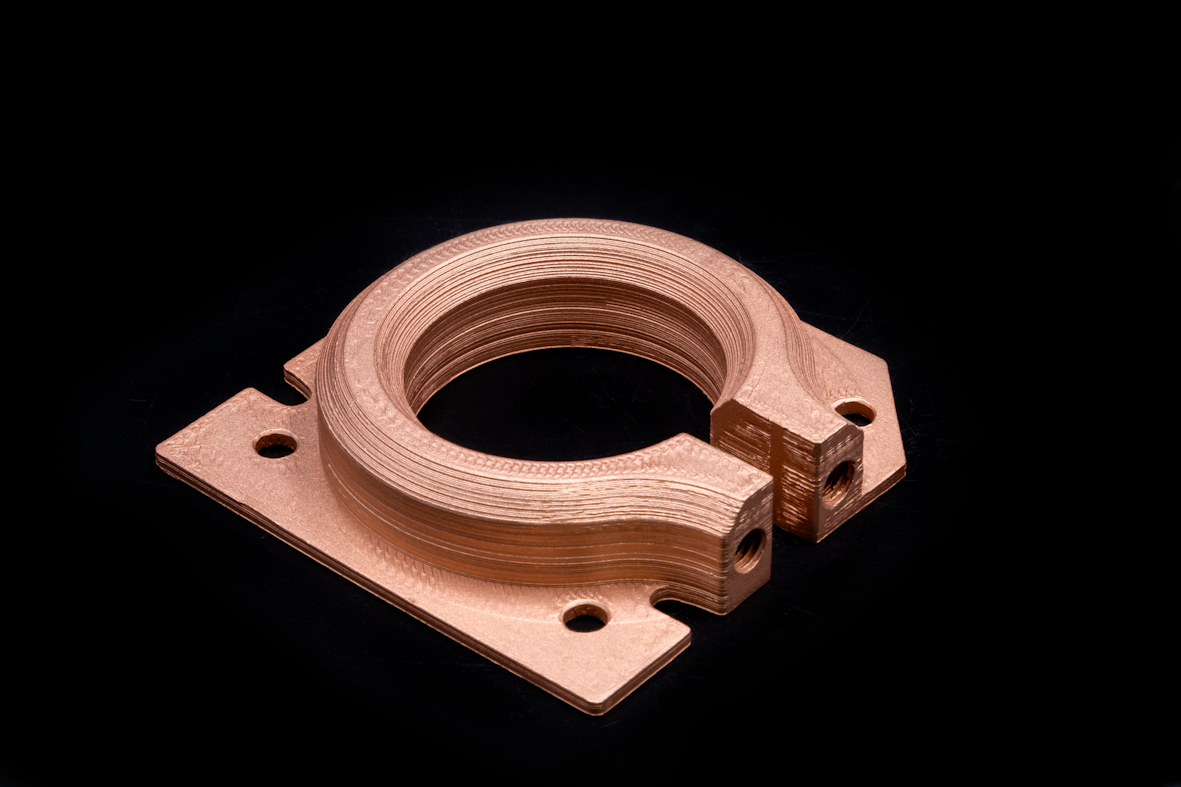
These considerations make the definition of AM evolve among its users, and often lead to a comparison between AM technologies themselves.
With over twenty different metal 3D printing processes, the metal AM landscape is probably the most diverse field of manufacturing. While the application often determines the choice of the technology, laser powder bed fusion remains the most widespread technology. For obvious reasons, we decided to focus three other metal AM processes that are gaining momentum in the market.
That being said, for those who are looking to take their first steps in AM, there is no clear communication about the appropriate use and scope of each technology.
If we were to evaluate the appropriate use and scope of traditional manufacturing processes, we would have considered features such as cost and price, as well as other considerations related to mass production and the global supply chain. These considerations may include labor, energy, material feedstocks, production support, research, design and engineering amortization to name a few.
(Cost indicates manufacturing efficiency, whereas price is a customer-oriented measure that ideally reflects the value of the product.)

In the case of metal AM, “the first question we should ask ourselves is why we would choose AM for mass production and consider using a global supply chain for that purpose. Are we considering cost, functionality, performance, lead time, environmental impacts and sustainability, security, etc. as our decision factors in choosing AM?
Cost efficiency, materials availability and materials properties, design complexity (where AM provides tremendous advantages), precision and quality requirements, and scalability all factor into the suitability of mass production. High-demand products experiencing a strained supply chain using conventional manufacturing processing technologies could be strong candidates for mass production using metal AM and implementing a global supply chain. IP considerations are also important when thinking of leveraging a global supply chain in metal AM,” Poorganji outlines.
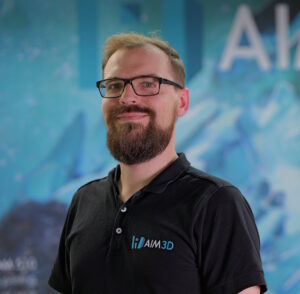
For Clemens Lieberwirth, CTO at AIM3D GmbH, “there is no good business case for mass production with AM – but talking about small series production, there are three indicators in my opinion:
- Series Size – depending on part size/complexity up to 10.000 pcs/year
- AM-optimized product design (depends on AM process) – part size, wall thickness, overhangs, smallest details, and internal channels should be tuned to the specific AM process to get the best result concerning quality and cost
- Independency in terms of material choice and production location. Systems that have open material policies allow the best cost & quality performance and make the production line crisis-safe”
So, a comparison between traditional and AM processes may be interesting but it is no longer a must to determine the key performance indicators of a good AM production.
Moreover, we may link conventional manufacturing with mass production, but one thing we should keep in mind is that the value of Additive Manufacturing does not lie in replicating what mass production already accomplishes, but in excelling where mass production falls short or struggles to perform effectively.
The question of standardization
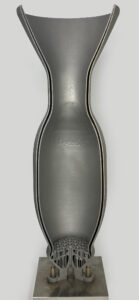
It would have been difficult to not mention the question of standardization when one knows that manufacturing strategies that rely on traditional manufacturing processes champion standardization. Indeed, some products – especially those that are mass-produced or certain industries, give more value to standardization whereas this value seems diminished with AM which favors customization.
“For high-rate production in aerospace and defense, ISO/ASTM recognition assists in achieving consistent results as a product transition from development to full-scale production that require collaboration of larger teams,” Titomic’s expert outlines.
On another note, there are only 7 AM process categories established by ISO/ASTM (the International Organization for Standardization). For those who are new to AM, these categories include material extrusion, material jetting, powder bed fusion, sheet lamination, binder jetting, direct energy deposition (DED) as well as VAT photopolymerization. This does not prevent AM users from using metal AM processes that do not fall within these categories.
The question is: does it matter? Experts have different opinions on the topic:
“Recognition under a globally used standard such as ISO/ASTM joint standards for AM is highly important, but whether it is absolutely necessary or not depends upon the industry and products. There are other standards and specifications such as SAE AMS, AWS, MIL that are necessary in certain contexts for specific products/industries. Standards are critical in assuring quality when it comes to repeatability and reliability of the process. They also establish a common language in building trust and credibility, and understanding risks, as well as in satisfying specific regulatory compliances defined by agencies such as the FAA, FDA, NASA, etc. by defining requirements and establishing certification processes,” Nikon AM Synergy Inc’s expert said.
“I [don’t] think it absolutely matters now. The standards are in part very general and try to merge different technologies, that have different technological principles of action. There are still many customers that are confused by the amount of different AM technologies and that cannot differentiate what is suited for one process or another. Standards that are mixing these processes won´t help with that. But of course, more enlightenment and suiting standards could also help with that in the future,” AIM3D’s CTO argues.
So, what performance indicators should one consider for an AM production and for a 3D printer?
In this dossier, metrics of success and key performance indicators are used interchangeably to qualify an AM production and a machine performance. For an AM production, we believe that if an AM process has been able to deliver value through customization, enable complexity at low cost and in small volumes, allow on-demand manufacturing, and ensure amortization – it’s already a win.
Some technical considerations may emphasize this:
“In metal AM production, there are several key indicators of production success. Part quality, repeatability and reliability of the build process, cost effectiveness and production efficiency, lead time/ on time delivery, as well as sustainability with regards to reducing waste and being able to reuse and recycle materials are among these indicators.
When it comes to AM machine performance assessment, equipment uptime, reliability, ease of use and available services and maintenance are essential factors. Other critical considerations include machine throughput, build volume, printing resolution, process automation (especially in serial production, or when skilled operators are not readily available), and in-process monitoring integration for machine health and quality assurance purposes,” Dr Behrang Poorganji outlines.
Taking example on their technology, Titomic’s Herbert Koeck points out:
“Process consistency is of high importance and is measured in several ways by Titomic. A primary metric for Titomic’s systems is powder velocity and material deposition. With high deposition rates, Titomic produces large, strong titanium parts at 5kg per hour, depending on the application.”
Before highlighting the performance indicators of their industrial 3D printers, let’s note that Nikon AM Synergy Inc. brings its expertise as a manufacturer of DED technologies. The company recently unveiled a Lasermeister DED repair solution which attracts customers looking for the highest quality and precision to repair critical parts such as turbine blades or complex and expensive molds and dies. One of the main features of its DED solution is its compact size and automation capabilities with integrated scanning, geometry compensation and tool path generation for the repair of complex parts. This will enable extremely low scrap rate, as well as highly efficient and repeatable processing, independent of machine operator skill level.

This is how Poorganji describes their 3D printer’s performance in light of the value benchmarks below.
Value benchmarks | Answers |
Does it help to achieve wall thickness? | Nikon DED Lasermister repair systems are very capable of delivering thin wall thicknesses and high-resolution features, down to 500 microns (0.5mm). Our next-generation high-throughput machines have even finer capabilities down to 200 microns resolution (0.2mm) |
What’s the minimum and maximum part size feasible? | Our current generation system can produce up to 400mm tall parts with approximate cross section of 300 X 200mm. Our next-generation DED system will have capabilities for up to 650mm parts. |
Build rate | Our current generation DED repair system can deliver 2-5 cc/hr. For our next-gen DED system, we are targeting +100cc/hr. |
In-process quality assurance | We have in-process monitoring in our DED system for both the melt pool and powder feed rate. |
Inspection and quality controls | Our DED repair solution is integrated with pre and post-3D optical scanning for dimensional accuracy. We at Nikon are also benefiting from our non-destructive Nikon X-CT inspection. |
Finishing and post-processing? | Our DED repair system’s high resolution and fine material deposition enables very smooth surfaces as well as minimized heat affected zone (HAZ) and thermal distortion. Using our Nikon DED repair solution can thereby reduce time and cost at the post processing step. |
Materials? | We have parameters for a variety of materials and our system is compatible with both reactive and non-reactive powders. As a few examples – we can process Steels, Ti alloys, Ni alloys, Cu alloys, and Nb alloys. |
Quality sensitivity (Does it require specific tools to control defects for instance?) | Standard microstructural characterization, mechanical and physical material property, and standard non-destructive testing (NDT) are the conventional tools we use. |
Titomic’s cold spray technology excels at creating large parts from pure titanium to a near-net shape. Titomic develops the world’s leading cold spray solutions to meet customer demands. From low-to-medium pressure portable systems, to high-pressure Titomic Kinetic Fusion® Additive Manufacturing Systems, Titomic’s engineered cold spray solutions provide a robust platform for cold spray implementation across the R&D, industrial, and government organizations, including applications in defence and aerospace.
Titomic’s High-Pressure TKF-1000 Cold Spray System is a modular cold spray system designed for prototyping and R&D, as well as small-scale production. With advanced robotics and control systems, industry-leading build rates, and state-of-the-art hardware.
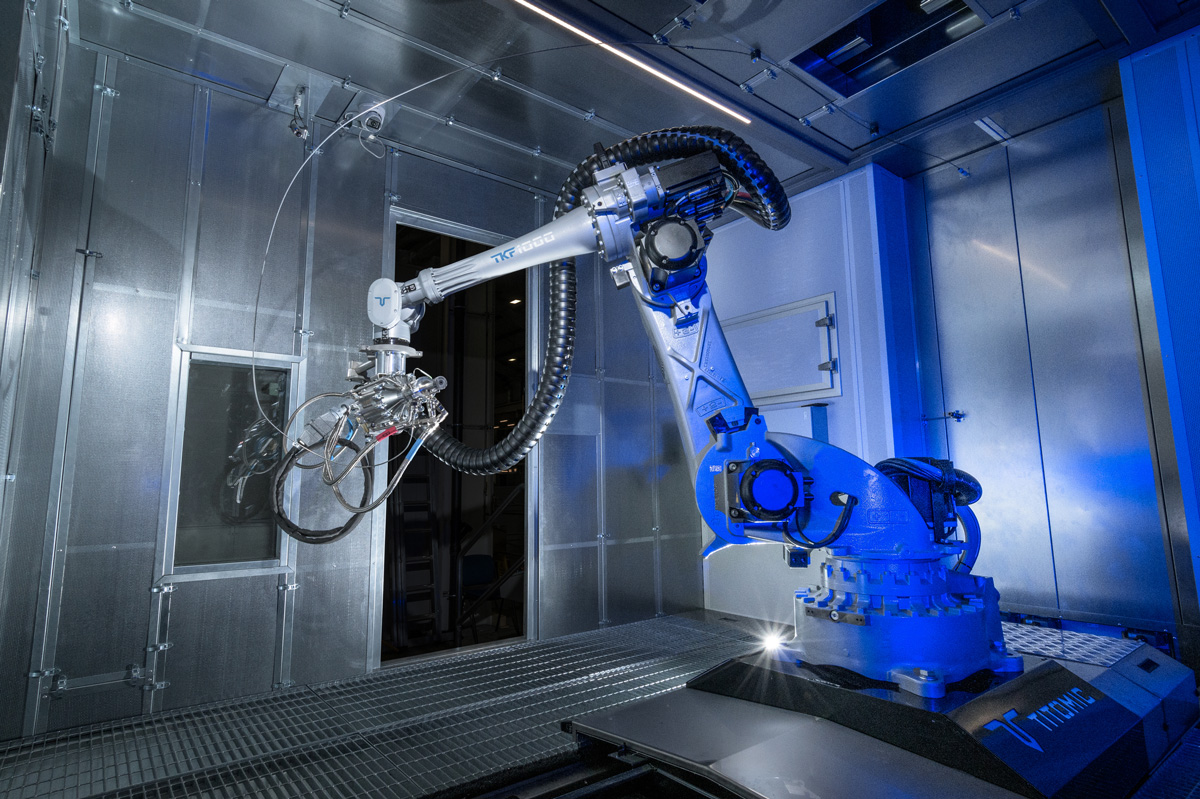
This is how Herbert Koeck describes their 3D printer’s performance in light of the value benchmarks below.
Value benchmarks | Answers |
Does it help to achieve wall thickness? |
Yes. Wall thickness is dependent on the material, the cold spray parameters used, and the geometry being built (i.e., flat vs rotational parts). For example, Titomic has achieved wall thickness in CP-Ti of 75 mm. |
What’s the minimum and maximum part size feasible? |
The maximum limitation is either residual stress limits or post processing limitation such as the heat treatment size available.
The minimum does depend on the geometry and cold spray system used. With a plum diameter ranging from 3 to 12 mm, parts that a derived from near net casting or forgings can be well suited to cold spray. |
Build rate | A reasonable build rate is 1 Liter per hour. For higher stressed materials this is dialled back to 0.5 and 0.25 Liters per hour.
Titomic can produce titanium and other parts at rates of 5kg/hour, depending on product application requirements, including optimisation of material properties. |
In-process quality assurance |
Titomic carefully records all cold spray parameters, such as power feed rate, gas temperature, and pressure. |
Inspection and quality controls |
Non-destructive testing techniques can be used, such as ultrasound, to inspect parts for defects.
Titomic conducts further inspection with its on-site laboratory and machine finishing facility. |
Finishing and post-processing? |
Titomic parts can be used as sprayed in some applications. Otherwise, the as-sprayed part is directly machinable. As parts made with cold spray are near-net-shape, they may require machining to remove 5-10% of material to bring the part to final tolerance.
Once complete, the part may require heat treatment, depending on the final desired outcome or part application. Titomic has found very strong results in the use of hot isostatic pressing, with parts showing significant strength-to-weight values. |
Materials? | Most metals that can be powdered can be cold sprayed, however, if a powder has a high strength-to-density ratio, it can be difficult to build with as it required a high particle velocity and therefore can be highly stressed during deposition (for example carbon steels).
Titomic’s cold spray process excels at manufacturing and coating with copper and its alloys, titanium and its alloys, tantalum, stainless steels, and Inconel In718 and 625. |
Quality sensitivity (Does it require specific tools to control defects for instance?) |
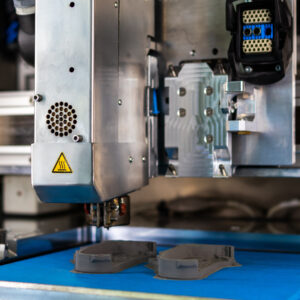
AIM3D GmbH has developed a multi-material 3D printer that prints products made of metals, ceramics, plastics and reinforced plastics based on standard injection molding granules without costly machine conversions.
This is how Clemens Lieberwirth describes their 3D pellet printing technology’s performance in light of the value benchmarks below.
Value benchmarks | Answers |
Does it help to achieve wall thickness? |
Yes, it helps to achieve wall thicknesses. |
What’s the minimum and maximum part size feasible? |
Minimum part size ~ 0,125 cm³ (Size of a tooth)
Maximum part size ~ 500 cm³ (Size of a palm) |
Build rate | ~ 60 -250 cm³/h |
In-process quality assurance | Process parameter control (temperature, movement, extrusion, nozzle clogging) |
Inspection and quality controls | Visual inspection, weight, dimensional measurements |
Finishing and post-processing? | Deburring, Debinding, Sintering, cutting threads, sanding polishing if needed |
Materials? | Stainless steels, low alloy steels, nonferrous metals like titanium, copper, brass, ferromagnetic alloys, hard metals, ceramics … |
Quality sensitivity (Does it require specific tools to control defects for instance?) |
Depends on use case |
In a nutshell…
While a good production with conventional manufacturing processes depends on its ability to ensure mass production and meet supply chain requirements, a good production with AM depends on many metrics that involve the machine performance, its ability to deliver value through customization, to allow complexity at low cost and in small volumes, as well as the ability to allow on-demand manufacturing. Moreover, given the current economic context of the market, broad accessibility, speed, entry costs and low production costs per unit, are also performance indicators that play to the strengths of AM. They reveal that the more AM evolves and is being utilized, the more performance indicators are identified on the road to success.