As you may already know, once they pop out of the 3D printer, 3D printed parts must undergo some sort of post-processing (such as removing supports, tumbling, sandblasting, CNC milling, chemical dips or even powder handling). In the range of these tasks, powder handling requires special attention due to the overall production time and costs, but also due to the safety concerns metal powders raise for operators. As we continuously explore the capabilities of the different solutions available on the market, we came to realize that Volkmann GmbH is one of those companies that advocate for the complete automation of this process.
Volkmann popped up on our radar when it signed a partnership with 3D printer manufacturer EOS. Headquartered in Germany (Soest, Westphalia), OEM is one of those companies that has built up extensive expertise in a previous field before entering the AM market. In this specific case, it brings about 5 decades of expertise in the development and commercialization of vacuum conveying systems for powder transport. This expertise enabled the team to expand their scope of expertise to powder handling in the AM industry. Over time, the company has created standards for powder transport, sieving and preparation of the powder, fully automatic depowdering, mixing and drying of powders. To understand the specifications of their powder handling solution for the AM industry, we asked the team 4 key questions.
As a regular reader of 3D ADEPT Media, you may already be familiar with powder handling, that step of the manufacturing process meant to convey and sieve materials that were not processed in the build job during the manufacturing process.
Volkmann refers to the process that goes from filling the AM machine to closing the loop as a closed circuit of powder handling. After the filling phase, this circuit involves unpacking and depowdering, cleaning, mixing of reclaimed powder as well as buffering of the powder.
“The powder loop begins with the extraction of the powder when the build job is unpacked in the 3D printer or an unpacking station. The next process step is the preparation of the powder by sieving to separate out foreign bodies and agglomerates, e.g. with a Volkmann PowTReX system. The powder loop ends with the 3D printer being refilled with the prepared powder, e.g. by a Volkmann vLoader 250,” the company says.
Here we can insert the attached picture in the email (pic 1 – closed powder loop)
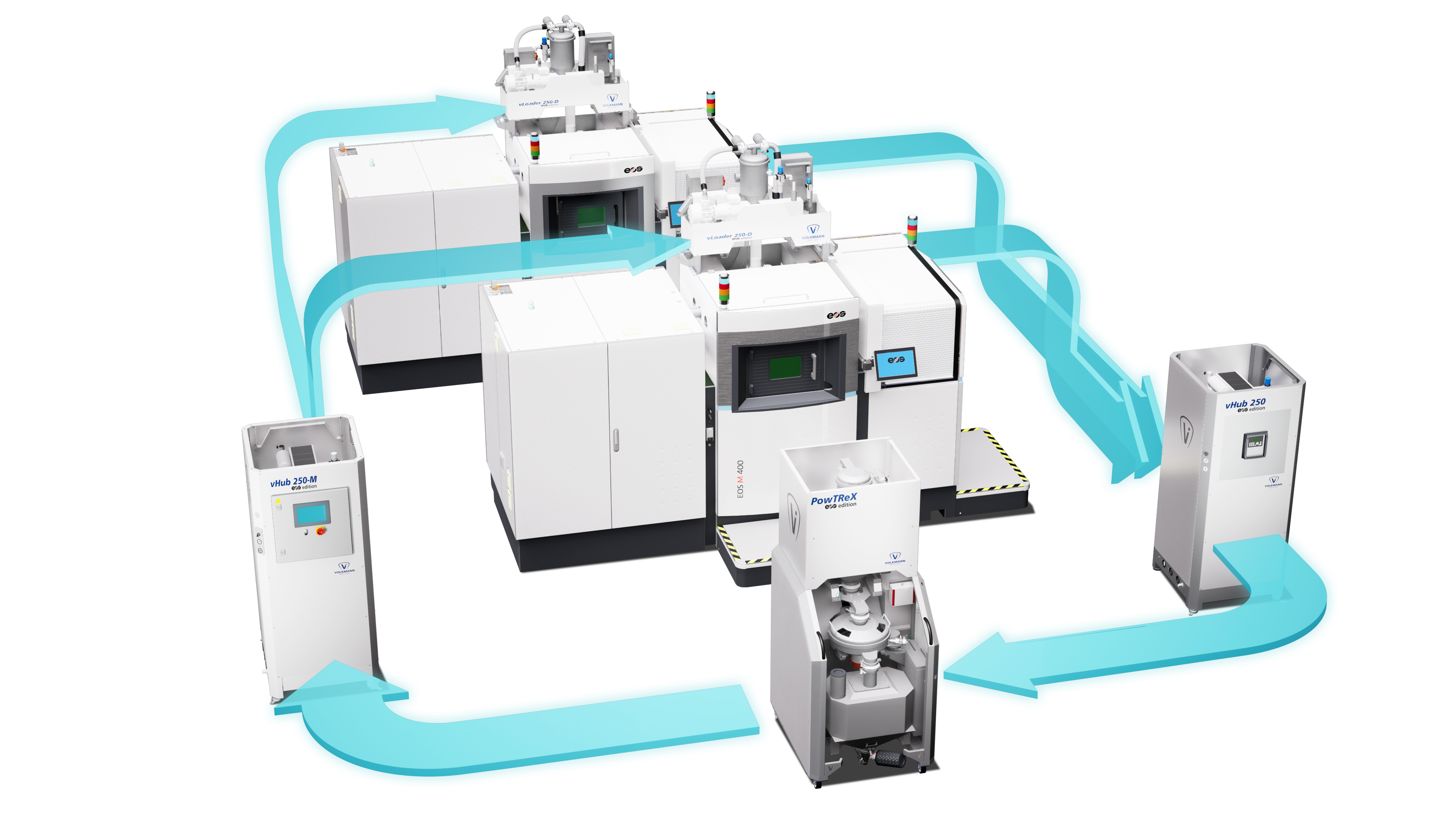
“The current practice is a powder cycle using containers such as metal bottles or containers. These are docked at one station, filled, undocked and transported to the next station. During each docking and undocking process, there is a risk of metal powder and dust being released into the environment; or that contaminants from the environment enter the container and contaminate the metal powder. In addition, operator errors and the mixing up of containers can lead to an incorrect batch or cross-contamination. From an economic point of view, these manual processes are time-consuming and expensive.
In a closed powder circuit, the powder is transported or conveyed between the stations through pipes. A vacuum is used for this purpose. This largely eliminates the risks for the product, personnel and the environment. A powder circuit can also connect several 3D printers to a central powder preparation station, but this requires the use of one type of metal powder for all printers.
Conveying with an inert gas such as argon or nitrogen is possible, but most users do not do this for cost reasons. Many users have also been unable to identify any significant differences in the quality of the components. When conveying with air, however, the powder must be flushed with an inert gas before the printer is filled.
In a powder circuit, a buffer container such as the Volkmann vHub 250 can help to increase performance. On the one hand, large quantities of powder can be transferred from the printer, for example, even if the downstream powder processing unit has no free capacity. On the other hand, a powder container can also be used to store powder for supplying the connected printers. Especially in production cells with several 3D printers in a closed powder loop, such buffer containers are indispensable.
With some 3D printers (e.g. EOS M 400), the removable frame can be removed from the machine with the build job in the powder bed. Volkmann has developed the DPS Metal 1 system for fully automatic unpacking and powder removal. The extracted metal powder is transferred by pipeline to a Volkmann PowTReX system for subsequent processing”, they explain.
As far as materials are concerned, the company’s solutions can process all types of AM powders, from polymer to metal and ceramic powders.
“Even bulk densities of 10 kg/l, such as those occurring with tungsten carbide powders, pose no problem. The systems are designed differently depending on the material. In the case of relatively light polymer powders, for example, the main focus is on throughput. With metal powders (especially toxic and respirable particles), the focus is on making the systems particularly leak-proof and, due to the large masses of the materials, on a particularly stable design,” the team outlines.
As this edition of 3D ADEPT Mag focuses on medical 3D printing, we couldn’t help but ask what they find the most challenging in the powder handling of medical 3D printed parts. To this question, the company replies:
“When handling powders for the medical sector, special attention must be paid to avoiding cross-contamination, GMP-compliant production and batch traceability and the materials used. Volkmann has known the pharmaceutical industry and its customers in this sector for decades. We then incorporate the knowledge gained into powder handling for our customers in the medical 3D sector. As the requirements of the customers and the powders used can vary greatly, these special projects must be coordinated in great detail between the user/customer and the machine supplier.”
How is automation being handled during that process?
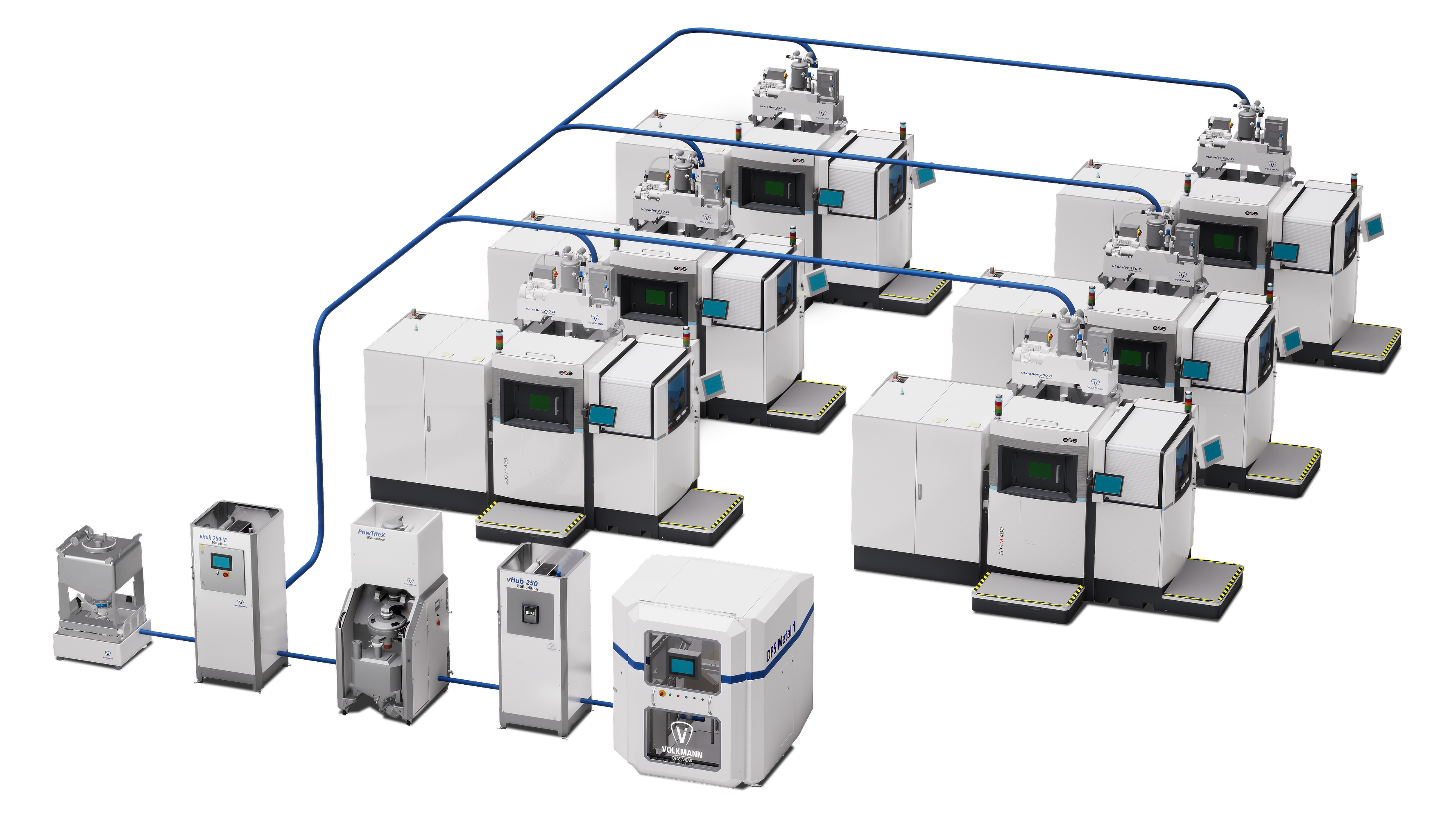
“The great advantage of 3D printing in the medical sector is the individual production of parts for patients. The systems for pre-and post-processing are just as individual as the prostheses, orthoses and dentures from the printer. Powder handling can be purchased for specific printers. As most manufacturing companies still work with a small number of printers and very small quantities of powder, fully automated systems for post-processing are not yet in use. Initial approaches have been developed for automotive parts as part of the IDAM project. Due to the high requirements concerning the qualification and quality of the parts, these work steps are still largely carried out manually. Major growth is expected over the next few years, particularly in medical 3D printing. It can therefore be assumed that fully automated systems will also be used in larger companies in the medium term,” the company concludes.
This dossier has first been published in the March – April 2024 edition of 3D ADEPT Mag.