Metal 3D printing has proven so many times its efficiency across applications that it’s almost always mentioned as the route to go in demanding applications. One key limitation experts often deplore is its expensive cost compared to other AM techniques –especially when exploring mass production. This urges OEMs to explore the capabilities of AM with other materials that could potentially serve as alternatives to metals. One category that is worth mentioning today is composites which benefit from a century of research into the production of components with subtractive techniques. However, when combined with AM, a couple of points need to be considered: What type would be a great alternative to metal 3D-printed parts? For wchich manufacturing purpose? Are there any specific manufacturing and design choices to consider? The article below ambitions to answer these questions.
We’ve already had a first introduction to composites 3D printing and the first steps one should take when working with this young branch of AM. AM companies might call it “the youngest branch of AM”, but composites are just like alloys to me. I find it fascinating to see the number of materials that can be combined to deliver a specific range of physical and chemical properties – and form in the end one single material that will be 3D printed to fabricate a part.
AM applications we have already witnessed with composites show that these materials bring opportunities for lightweighting – which is the hallmark of AM –, and interestingly, the ability to build onto a custom tool.
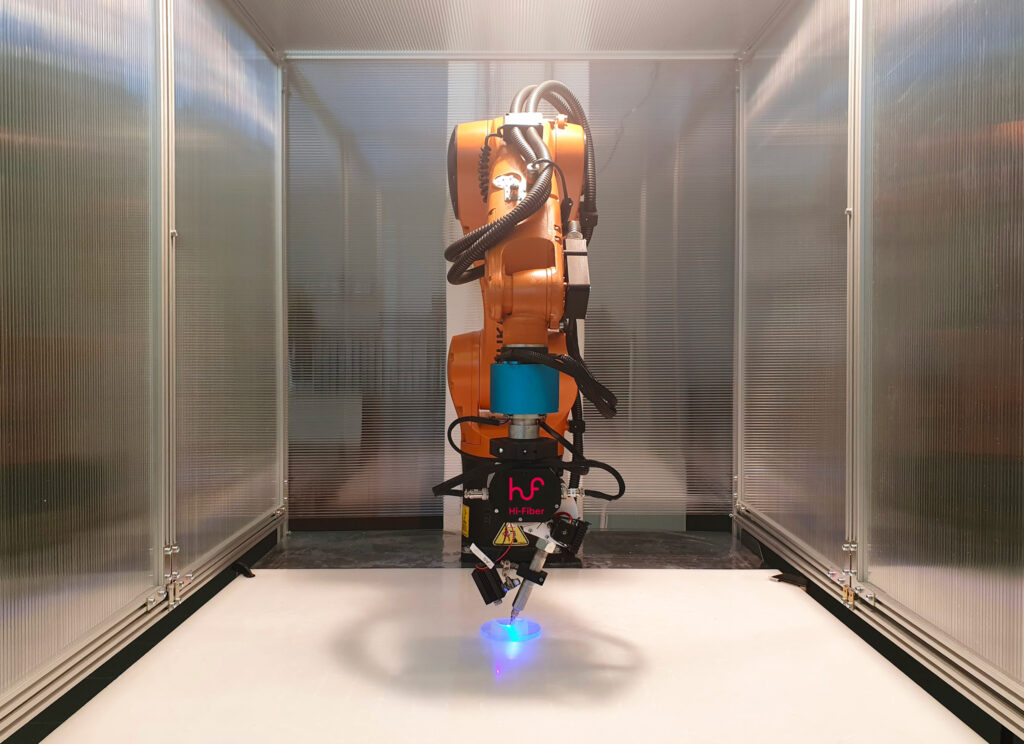
Furthermore, one of our first dossiers on composites reveals that two reinforcement types of fiber are compatible with AM technology: chopped and continuous. According to Michele Tonizzo, CTO of Moi Composites, a company that specializes in Continuous Fiber Manufacturing, “From a structural point of view, the performances obtainable through the use of continuous fiber composites are unbeatable, with tensile strength surpassing 1.5 GPa (*1) and reaching 30 times those of chopped fibers reinforced polymers (*2). Unfortunately, the intrinsic limitation of having a coherent, always-solid part during extrusion limits the geometrical complexities obtainable by using only a single-material approach. This is why the approach pioneered by Markforged and Anisoprint, and extended in three dimensions by Moi Composites, is the best one discovered yet. By depositing unreinforced, or chopped fiber-reinforced, matrices able to describe complex geometries, and continuous fiber-reinforced matrices only in strategic places, thus also shortening print times, it is possible to obtain structural parts with complex geometries such as cavities and internal reinforcements. The approach conceived by Moi Composites takes this idea to a three-dimensional level. In fact, by taking advantage of robotic multi-axis freedom, it is possible to describe complex geometries using short-fiber reinforced polymers, then adding layers of unidirectional continuous fibers following the external geometry to achieve the desired structural integrity.”
There has always been a battle between those who advocate for chopped and continuous fiber reinforcement. In this vein, it’s important to keep in mind that each material brings its own set of characteristics, application areas, and technologies associated with them.
The table below summarizes a few of the most important characteristics captured so far:
Continuous fiber reinforcement | Chopped fiber reinforcement |
More strength and stiffness: its strength lies in the continuity of the strands which can absorb and distribute loads across their entire length. | Stiffness can significantly be improved depending on the material |
Described as more strong and reliable than metal structures | Ideal for improving surface quality, wear resistance or even the look of a part while reducing the weight of the part |
Compatible with several technologies | Cheap material |
When we talk about aerospace 3D printing with composites though, even though there is a predominant use of continuous fiber reinforcement, we did notice a couple of applications made up of chopped fiber reinforcement materials.

Tonizzo has been involved in several projects that all aim to reduce weight or lead times for aerospace parts. He said one that was particularly successful aimed to reduce the overall weight of the plane by redesigning non-structural parts, in this case, the brackets holding the seats to the floor. “The weight reduction came from removing material not contributing to the structural integrity while maintaining the unidirectionality and continuity of the fibers, something impossible with traditional manual or automated methods of composites production,” he explains.
“The part obtained presented similar mechanical performances while reducing the weight by a significant amount. From my experience, the competitive advantage of composites additive manufacturing for the replacement of metal parts in a production environment has almost always been related to the performances obtainable by creating truss-like geometries, elevating the strength-to-weight performances of the part,” Tonizzo adds.
Interestingly, whether one deals with AM or conventional manufacturing processes, the most important driver that leads to the use of composites rather than metal remains “the strength-to-weight performances only obtainable with unidirectional carbon fiber reinforced polymers” – according to Tonizzo.
Applications & limitations
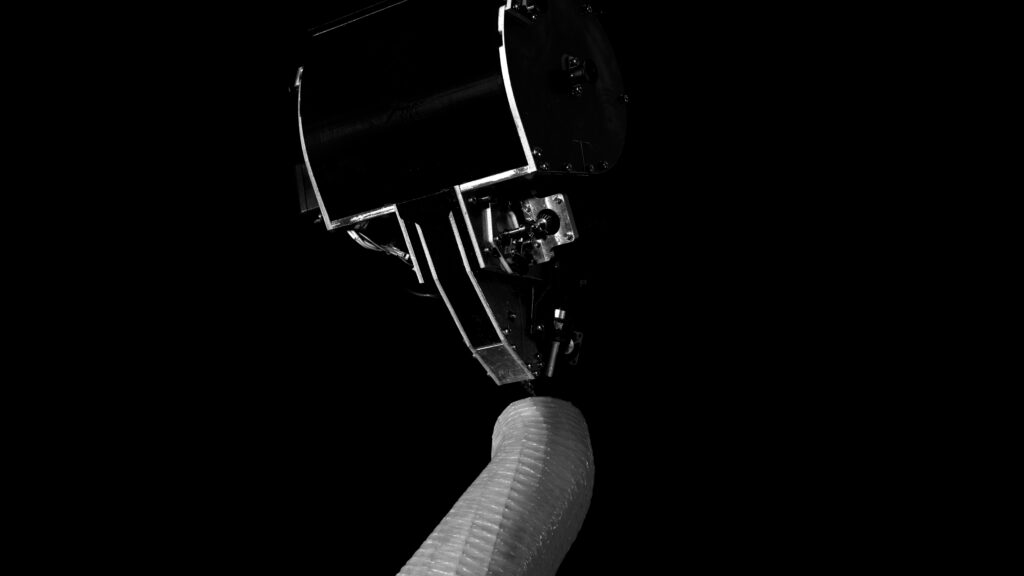
If brackets have been mentioned as a key application in aerospace AM, composites AM also remain an ideal production candidate for fasteners, also used in aerostructures. Despite the complexities of this application, Thermwood has demonstrated several times that autoclave tooling can be a key application of composites AM in the aerospace industry.
Other development opportunities of composites might see a combination of AM with existing composites manufacturing processes. One company that is quietly working in this area is Electroimpact, a US-based company that is also a Boeing supplier. Electroimpact developed a solution to apply compoistes to the Boeing 787 aircraft. That solution combines automated fiber placement or AFP. The company explains that it “has integrated an in-situ out-of-autoclave thermoplastic AFP process and an advanced FFF 3D printing process into a unified Scalable Composite Robotic Additive Manufacturing (SCRAM) system. SCRAM is an industrial true 6-axis continuous fiber-reinforced 3D printer, which enables the tool-less rapid fabrication of aerospace-grade integrated composite structures. High-performance thermoplastics combined with a high percentage of continuous fiber reinforcement are used to produce parts with exceptional material properties previously unheard of in the world of additive manufacturing.”
Electroimpact’s solution is one of a kind in the industry and we do hope to hear more about it in the future.
The question that remains to be answered now is the one of the manufacturing purpose: Does composites AM only lead to prototyping and low-volume production? For Moi Composites’ CTO, composites AM remains one of the very few technologies where 3D printing can be employed in a work environment, and not only for low-volume production.
“I found that a product designed from the start with additive manufacturing in mind is easier to be brought to production than a redesign of an existing part. For example, Hi-Fiber, the dental reinforcement product developed by Moi Dental, Moi’s spin-off, was designed and can be produced only with composites AM, and with thousands of parts produced per year. Given the fact that high-volume production of composite parts is not closely comparable to the numbers produced via plastic injection molding, I am confident that, if the part possesses enough added value, it can be produced in high volumes with AM technologies”, Tonizzo points out.
Tonizzo’s expectation unconsciously implies a limitation that would lead to costs if/when exploring composites AM in mass volume applications. At a technological level, he also mentions some of the hardly-mentioned complexities of continuous fiber composites: they cannot be melted and shaped into form, trimmed, or milled down from a solid object.
“Differently from other manufacturing methods, it’s extremely difficult to obtain high performances out of a layer-by-layer produced part, as they suffer even more from the anisotropic behavior of 3D printing. All these limits are well known and already solved by composite manufacturers, who instead highly appreciate the digital approach brought by AM to the composite industry. Therefore, the adoption of CFC AM comes easier from composite manufacturers rather than the AM industries. Due to the heavy design for manufacturing work necessary to produce a part using CFC AM, I doubt there would be a “Shapeways” for composites, unfortunately”, he concludes.
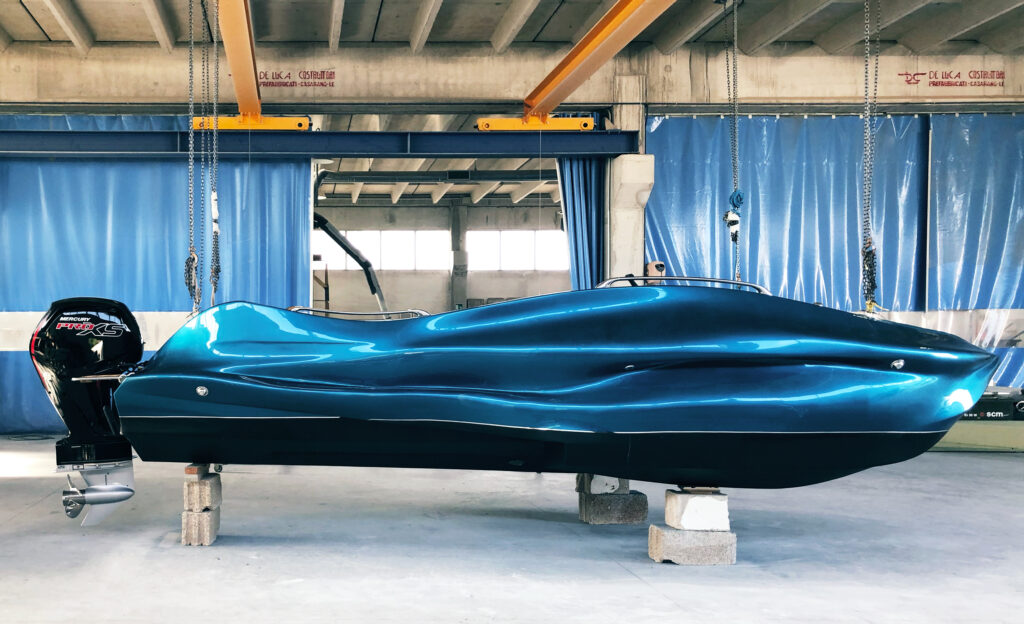
This article hast first been published in the 2024 January/February edition of 3D ADEPT Mag.
Editor’s notes
Michele Tonizzo – the key contributor who shared insights into this topic, is the co-founder and President of Moi Composites, a company that specializes in composites 3D printing and that appeared on our radar when it showcased a 3D printed fiberglass boat at Genova Boat Show 2020. Before founding Moi, he was a research lead at Politecnico di Milano University +LAB, researching new methods of AM for polymeric materials, and a winner of the most prestigious award for innovation in composites, the 2017 JEC Innovation Award.
Moi Composites now focuses on the industrial development of Sistema, its end-to-end system for simplifying the production of composites through robotics and AM. With the soon-to-be launched beta program, the company is now actively looking for first adopters and testers of Sistema in the R&D departments of universities and industries.
References:
*1: Baur JW, Abbott AC, Barnett PR, et al. Mechanical properties of additively printed, UV-cured, continuous fiber unidirectional composites for multifunctional applications. Journal of Composite Materials. 2023;57(4):865-882. doi:10.1177/00219983221146264
*2: Information based on Markforged’s Onyx ESD Material Datasheet