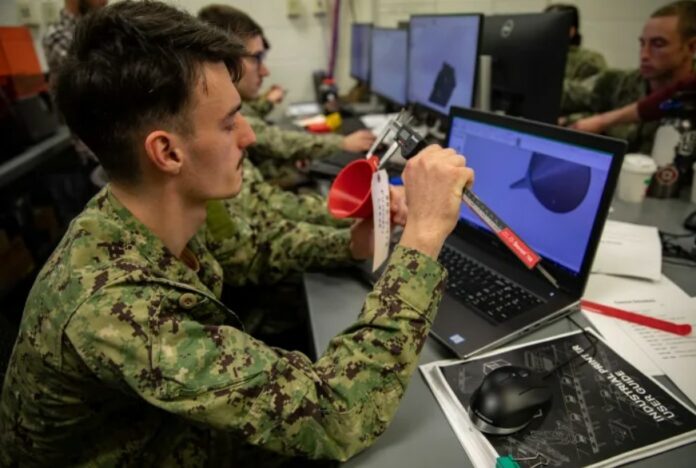
L’aventure de l’US Navy dans la FA a commencé en 2016. Depuis qu’ils ont validé leur premier business case , différentes divisions de l’organisation ont exploré les capacités de cette technologie. Le dernier exemple qu’ils ont partagé révèle comment ils ont pu résoudre les problèmes de la chaîne d’approvisionnement avec la FA.
Selon Matt Sermon, directeur exécutif du Program Executive Office for Strategic Submarines, la base industrielle a le plus grand mal à maintenir la capacité requise de pièces et de composants en métal lourd. Il s’agit notamment de pièces moulées, de pièces forgées, de vannes, de raccords et d’éléments de fixation.
La marine a examiné 5 500 pièces qui ont posé des problèmes de calendrier pour les nouvelles constructions et les disponibilités de maintenance pour les sous-marins et les navires ; six matériaux sont responsables de 70 % des retards de livraison, note Sermon. Ajoutez à cela le fait que certaines de ces pièces sont complexes à fabriquer à l’aide de certains de ces procédés de fabrication conventionnels, le processus en est davantage ralenti. Les pièces moulées, par exemple, sont particulièrement difficiles pour le chantier naval, et la liste des pièces en métal moulé qu’il s’efforce d’obtenir à temps et en bonne qualité est longue. La fabrication additive pourrait raccourcir le délai de production de certaines pièces métalliques de 80 % en moyenne, selon l’efficacité de l’imprimante.
Ces pièces ont toujours constitué un défi pour l’industrie, car la métallurgie fondamentale est complexe et peut entraîner des défauts. Mais il y a moins d’entreprises qui fabriquent ces composants aujourd’hui qu’au cours des dernières décennies, et cette petite base a du mal à répondre à la demande croissante.
La marine a élaboré un plan pour faire mûrir les métaux, les machines d’impression et les processus associés à ces six matériaux cette année, de sorte que d’ici mars 2024, ils puissent être imprimés en volume et installés sur les sous-marins, a déclaré Sermon.
« Nous n’avons pas encore atteint la maturité de ce processus au point de pouvoir développer la fabrication additive à grande échelle comme je le pense« , a déclaré Bill Galinis, commandant du Naval Sea Systems Command. « Nous pouvons faire les pièces uniques, et franchement, même pour un composant de réacteur, nous avons construit des pièces assez complexes en utilisant la fabrication additive, mais nous ne sommes pas encore arrivés au point où cela est évolutif. »
La prochaine étape pour l’équipe consiste maintenant à identifier les pièces à fort volume et à fort usage, et à disposer d’une capacité d’impression qui lui permette de les imprimer assez régulièrement.
Le « défi actuel est, d’une part, de passer rapidement par le processus de certification, de codifier ce à quoi cela va ressembler et, d’autre part, d’être capable de faire évoluer la fabrication additive« , explique Galinis.
N’oubliez pas que vous pouvez poster gratuitement les offres d’emploi de l’industrie de la FA sur 3D ADEPT Media ou rechercher un emploi via notre tableau d’offres d’emploi. N’hésitez pas à nous suivre sur nos réseaux sociaux et à vous inscrire à notre newsletter hebdomadaire : Facebook, Twitter, LinkedIn & Instagram !