Des experts de Promation, ModuleWorks et du « Multi-Scale Additive Manufacturing (MSAM) Laboratory » de l'Université de Waterloo ont exploré une nouvelle méthode pour fabriquer des géométries en surplomb sans avoir recours à des structures de support.
Promation apporte ici son expertise en matière d'outillage, d'automatisation et de systèmes robotiques de haute qualité. ModuleWorks est un fournisseur de composants logiciels pour l'industrie de la fabrication numérique, tandis qu'en se concentrant sur les processus de fabrication additive de nouvelle génération, le MSAM Lab, situé au département d'ingénierie mécanique et mécatronique de l'université de Waterloo au Canada, continue d'explorer de nouvelles techniques pour développer des matériaux avancés, des produits innovants, des outils de modélisation et de simulation, des dispositifs de surveillance, des systèmes de contrôle en boucle fermée, des algorithmes d'assurance qualité et des techniques de caractérisation holistique in situ et ex situ.
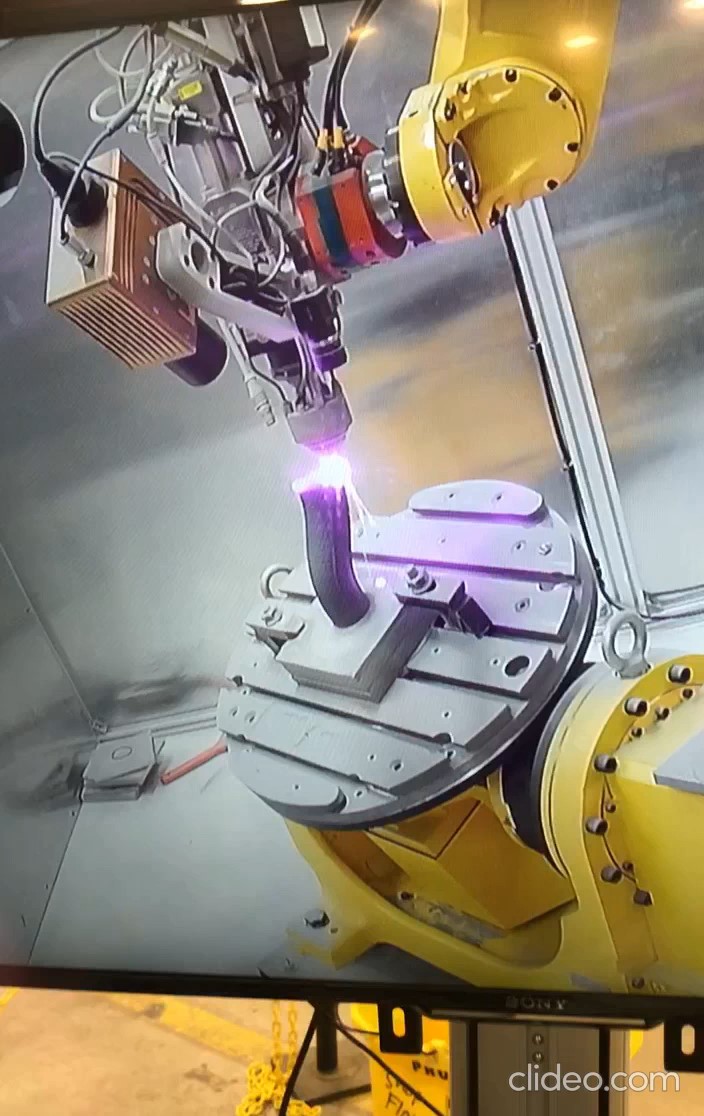
Les essais de ce projet ont été réalisés à l'Université de Waterloo en Ontario, au Canada, à l'aide de la technique de dépôt d'énergie dirigée par laser (LDED – Laser Directed Energy Deposition). En éliminant les structures de support, l'équipe a pu simplifier la planification du processus et réduire les déchets de matériaux.
Les pièces présentant des surplombs géométriques, comme les tuyaux coudés, constituent un défi particulier pour les procédés additifs qui déposent le matériau en couches horizontales. Pour déposer le matériau dans la zone de surplomb du coude, le procédé doit intégrer des structures de support qui permettent aux couches de s'étendre au-delà du tuyau. Cela fonctionne assez bien, mais l'incorporation de structures de support ajoute du temps et des efforts à la planification de la production et crée des déchets supplémentaires.
Pour simplifier et accélérer le processus LDED, Promation, ModuleWorks et MSAM se sont associés pour développer une nouvelle méthode qui dépose les couches dans des plans non horizontaux. La buse d'impression est montée sur un bras robotisé à 6 axes pour s'assurer qu'elle reste toujours tangente à la surface de dépôt qui est automatiquement inclinée à l'aide d'un positionneur à 2 axes. L'application de couches de dépôt sur une surface inclinée permet d'imprimer des coudes de tuyaux et d'autres géométries en surplomb sans structures de support, ce qui simplifie la planification de la production et réduit les déchets de matériaux.
Lors des essais en laboratoire, l'équipe a utilisé la nouvelle méthode pour fabriquer un tuyau avec un coude de 45 degrés sans structures de support.
La nouvelle méthode a également été utilisée pour imprimer avec succès un dôme creux fermé.
N’oubliez pas que vous pouvez poster gratuitement les offres d’emploi de l’industrie de la FA sur 3D ADEPT Media ou rechercher un emploi via notre tableau d’offres d’emploi. N’hésitez pas à nous suivre sur nos réseaux sociaux et à vous inscrire à notre newsletter hebdomadaire : Facebook, Twitter, LinkedIn & Instagram ! Si vous avez une innovation à partager pour le prochain numéro de notre magazine numérique ou si vous avez un article à faire connaître, n’hésitez pas à nous envoyer un email à contact@3dadept.com.