La première fois que nous avons écrit sur Titomic, c’était pour annoncer que la société d’impression 3D métal allait fabriquer l’équipement de Golf de Callaway. Quelques semaines plus tard, au cours du mois de mai, l’entreprise a dévoilé une nouvelle imprimante 3D à métal, l’une des plus grandes et des plus rapides au monde.
De plus, en collaboration avec la Commonwealth Scientific and Industrial Research Organization (CSIRO), la société a co-développé un procédé de fusion cinétique. Lors d’un entretien avec nos collègues de Manufacturer’s Monthly, directeur fondateur de Titomic et CTO, Jeffrey Lang a expliqué que le procédé breveté « produit des formes 3D à partir de la fusion de poudres métalliques pulvérisées à des vitesses supersoniques ». Grâce à son bras robotisé à 6 axes, le procédé pulvérise des particules de poudre de titane sur un échafaudage à des vitesses supersoniques de l’ordre de 1 km/s environ.
En ce qui concerne l’imprimante 3D, elle a une surface de construction de 9 x 3 x 1,5 m et selon l’entreprise, sa technologie permet d’imprimer en 3D des pièces plus grandes que ce que les imprimantes 3D métalliques actuelles de l’industrie pourraient offrir.
Le CTO et fondateur a expliqué que bien que la plupart des procédés d’impression sur métal utilisent un laser à faisceau d’électrons pour faire fondre le métal, il n’y a pas de fusion dans leur procédé. Il n’y a donc pas de distorsions liées à la chaleur et les matériaux conservent leurs propriétés.
« Cela signifie aussi que nous ne sommes pas limités par la taille. Parce que la fusion des métaux dans les procédés d’impression 3D conventionnels provoque leur oxydation, l’impression 3D des métaux conventionnels doit avoir lieu à l’intérieur d’une chambre à vide. L’absence de fusion dans notre procédé signifie que nous ne sommes pas limités par la taille », a déclaré Jeffrey Lang.
De plus, si cette technologie se positionne comme le candidat idéal dans l’industrie aérospatiale, le directeur a encore des réserves quant à certaines applications : « Si nous pouvions fabriquer des pièces aussi proches de la forme nette, c’est-à-dire créer la forme finale de la pièce et y ajouter un peu plus de matériau, nous pourrions réduire le temps d’usinage de 80 % dans certains cas », a dit Lang.
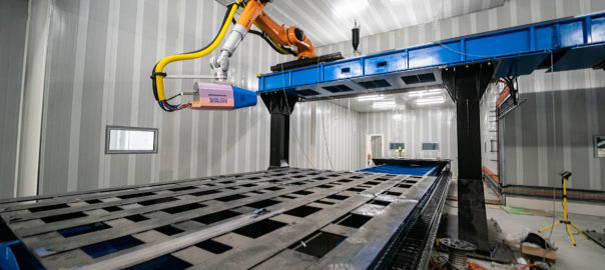
« Nous ne disons pas que cette technologie peut démarrer maintenant et remplacer le processus aérospatial actuel. Mais notre processus est actuellement l’un des processus les plus importants que ces entreprises aérospatiales étudient. Nous avons trouvé des solutions supplémentaires pour éliminer une petite quantité de porosité afin d’obtenir une qualité aérospatiale.
« Pour l’un des composants de l’aérospatiale, qui peut coûter jusqu’à 4 millions de dollars, nous pouvons réduire le temps de production de 200 heures à 6 heures. »
Enfin, même si la technologie est fabriquée en Australie, « elle ne profite pas à un seul pays. Il s’agit d’assurer un avenir meilleur pour toute l’humanité et les générations futures sur cette planète. »