Everyone knows about New Year’s resolutions; those objectives we set ourselves and promise ourselves to keep. While for most individuals, the overwhelming odds are that they ditched those resolutions about a month later after the beginning of the year, things are different for companies that do not even talk about “resolutions” but “strategic goals/plans” to grow.
Like every company, ULT AG set itself strategic goals at the beginning of the year but 2020 had a different plan for the team.
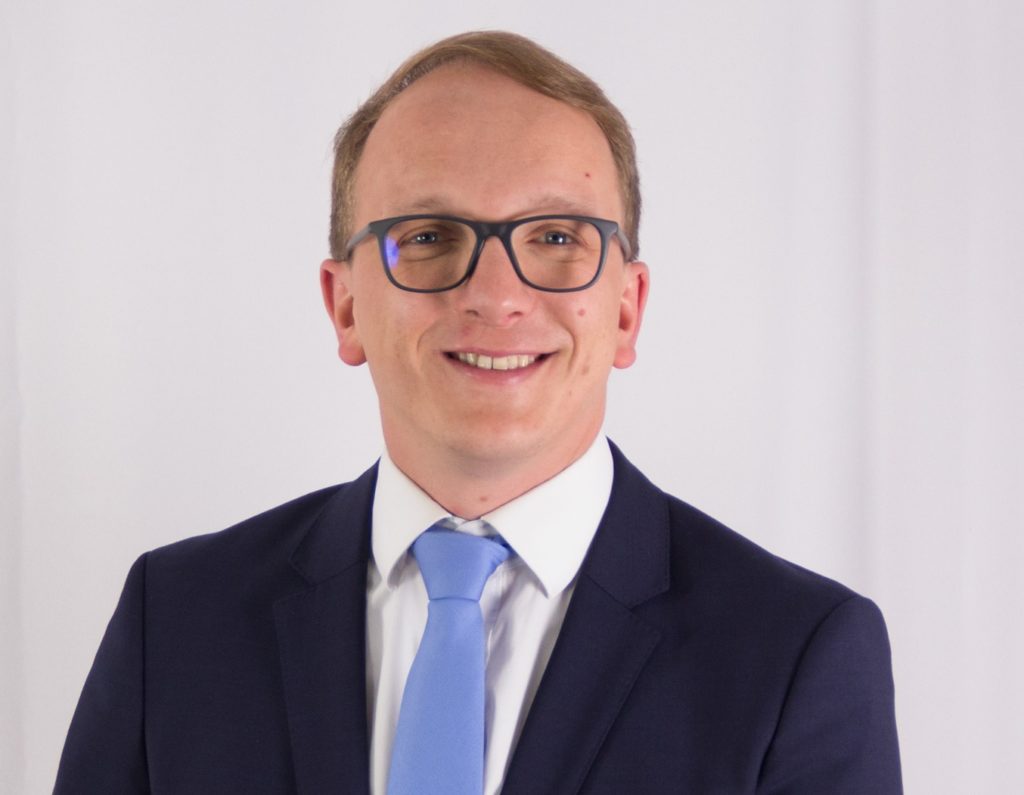
“Just like every year, we had a strategic planning that highlighted key areas where we should focus our expertise. Our planning helps us determine what kind of industry we want to serve more, what kind of branches and where we want to grow. The ultimate goal remains to grow the company further. This year, we wanted to focus our role and position in the additive manufacturing industry as market leaders in the gas cleaning for Selective Laser Melting, Alexander Jakschik, Managing Board at ULT AG states from the outset.
“Another pillar of growth was our network AMP+.” [As a reminder, AMP+ was officially launched last year at Formnext 2019. Made up of Assonic Dorstener Siebtechnik GmbH, Solukon Maschinenbau GmbH and ULT AG, the network helps operators of SLM technology to develop efficient manufacturing practices while addressing issues related to powder processing and handling.]
“Together with Assonic and Solukon, we wanted to push our capabilities forward in order to build a complete end-to-end solution for the depowdering, sieving and cleaning conditions.
Obviously, for our business segment, we wanted to develop new products for extraction and filtration, as well as air drying solutions.
Lastly, another key goal was to optimize and digitize our internal processes. In this vein, we have installed an ERP system – Enterprise Resource Planning – to digitalize our processes. To date, not only has the company’s warehouse been digitalized, but there is a wide range of digital processes that our teams needed to master”, the Managing Director continues.
It’s been two years that digitalization was on the company’s roadmap but this year more than ever, it was crucial to accelerate this part of their activities and makes it an integral part of their enterprise culture. This has facilitated both the work internally but also with customers.
Furthermore, the teams should not only master the new internal digital processes, they should also adapt to a new way of working – remotely. Let’s note that this new way of working remotely was valid for various teams except from operators that build the machines.
“Only a few people needed to work remotely. For a company of our size and our field, it’s very important to have the teams in-house to ensure real-time production planning and other requirements that cannot be performed from home office”, the CSO clarifies.
ULT had therefore a roadmap of well-defined strategic points to achieve throughout this year. Given the unexpected sanitary crisis, some of them have been accelerated while others have been redefined.
“NEVER LET A GOOD CRISIS GO TO WASTE”
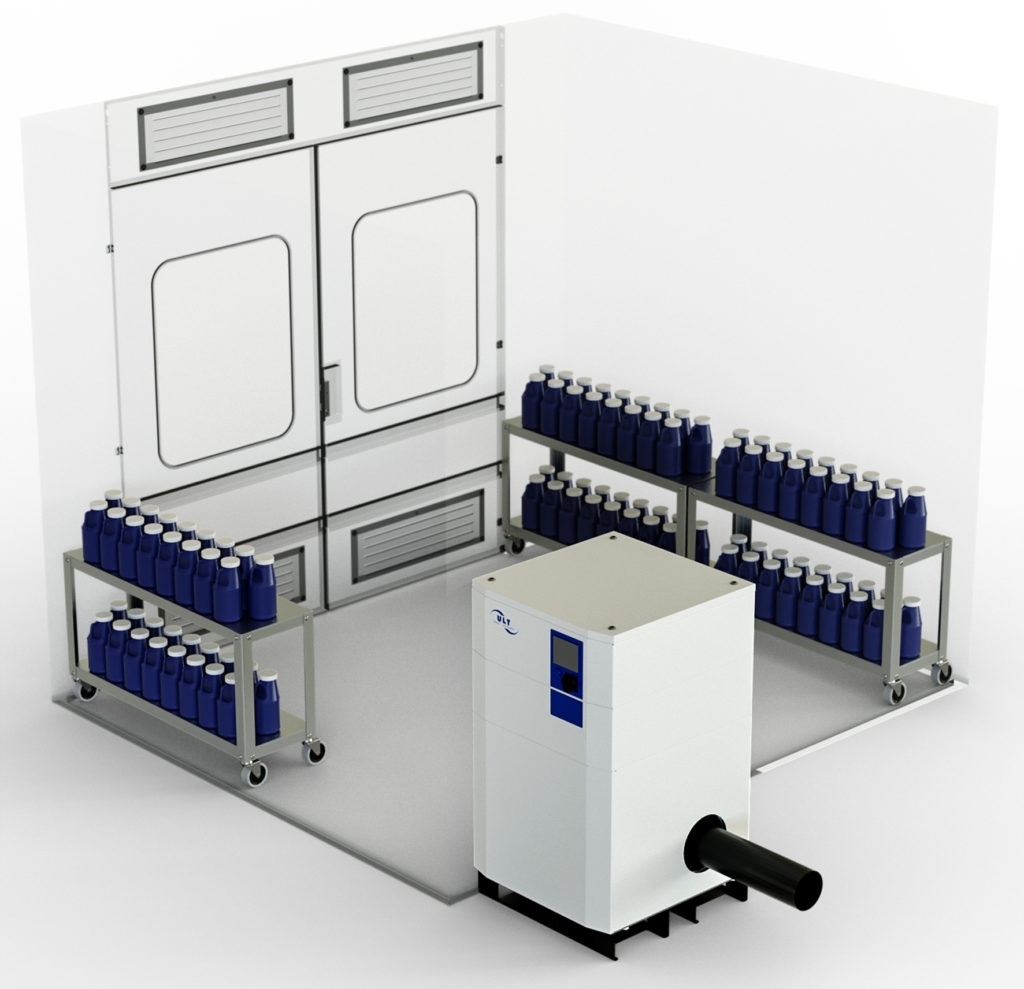
Although the full effects of economic and structural damage caused by COVID-19 have yet to be seen, ULT AG is not one to sit back and wait for the storm to pass. As a matter of fact, Jakschik strongly believes that one should “never let a good crisis go to waste” (Winston Churchill). In this vein, the company’s first actions were to look for a way to bring its contribution to flatten the curve of this pandemic.
“Like many companies, we did not operate at 100% during the peak of the pandemic. We used this chance to push the integration of our ERP system within our processes forward. It was an opportune time to launch it, to make amendments and to improve what needed to be improved.
We also launched two new product lines. These products aim to ensure safety conditions by cleaning the air from the virus in public areas including schools, fitness centers, big office spaces, dental surgeries and more. Named JakAir and SASOO, the new products enable to help fight viruses like Coronavirus by purifying the air”, he explains.
As far as additive manufacturing activities are concerned, the company’s representative admits that they encountered similar issues faced by other AM technologies providers. In these times, exchange with customers and discuss technical issues can easily become complicated when engineers are working from home.
Nonetheless, this was the right time for the ULT team to focus their efforts on R&D activities and “develop new products that would meet customers’ problems of tomorrow” – as per the words of Jakschik.
“In our gas cleaning systems designed for Additive Manufacturing for instance, we have further developed features that enhance easiness of use, safety as well as features which make it possible to reuse powders,” he outlines.
If it is more than clear now, that ULT did not let this crisis “go to waste”, it is worth noting that the company has had to learn the hard way to be flexible, to adapt to changing conditions in a volatile market, to rely on and strengthen its network – in a nutshell, to be more agile.
“It’s difficult to share expectations after such an extraordinary year”
One thing is certain, air technology solutions have proved out their capabilities in AM production environments; capabilities that have been confirmed beyond manufacturing environments – thanks to the Coronavirus pandemic.
However, there is still a long road to go and as of today, it’s difficult to share clear expectations of what ULT’s plans will be for 2021. Nevertheless, the Managing Director remains optimistic about the developments of the AM market and the way ULT intends to improve it:
“We have been working on the launch of a new dehumidification equipment, a new extraction filtration machine which also focuses on highly flammable particles found in AM production environments and for our OEMs that use SLM process, we have developed new features for their AM processes. We will keep a high focus on AM”, he concludes.
This content has been written in collaboration with ULT AG.
ULT AG is on a mission to remove hazardous particles in various manufacturing processes. The company provides the AM industry with advice and product assessment on everything related to air pollution control, occupational safety as well as air drying in plastic and metal AM processes.