Laser metal deposition technology developer Meltio is improving user experience on its wire-laser metal 3D printing technology with two new solutions: a toolpath generator software and a new laser calibration system.
In case you don’t know, laser metal deposition is one of the most versatile processes due to its ability to perform repairing or coating processes. Ideal production candidate for the repair of turbine blades, as well as other high-performance applications in demanding industries, the process works by generating a weld pool on the component surface. A metal filler material is gradually added and melted on in this pool. Beads that are welded to one another are created, and thereafter form structures on existing base bodies for repairs or coating, or form entire components.
The toolpath generator software
CEO of Meltio, Ángel Llavero, states that “metal additive manufacturing has historically been associated with complex and expensive software, limited to the use of very few people because it was very specialized” – hence their willingness to facilitate and shorten the learning time of metal AM.
Named Meltio Horizon, the software solution is compatible with the Meltio M450. Up until now, Meltio users have been reliant on using 3rd party FFF slicers to prepare toolpaths for that machine.
In addition to traditional slicing parameters used in FFF software such as layer height, line width, print speed, and support materials, the new Meltio Horizon provides tailor-made access to Meltio’s laser-wire process, and material-specific parameters such as laser power, dual wire, and hot wire settings.
With the Meltio Horizon software, all of the material-related settings are directly in the slicing software, allowing for full control and just a single profile. This also allows us to create more specialized printing profiles, with the power to directly control the laser and hot wire on a “per slicing feature” basis, rather than being set for the full part.
This slicer is currently only compatible with the Meltio M450 metal 3D printer. For Meltio Engines (CNC and Robot Integration), the company is currently working on developing its open software ecosystem partnerships that allow the generation of 5 Axis G-Codes.
The laser calibration system
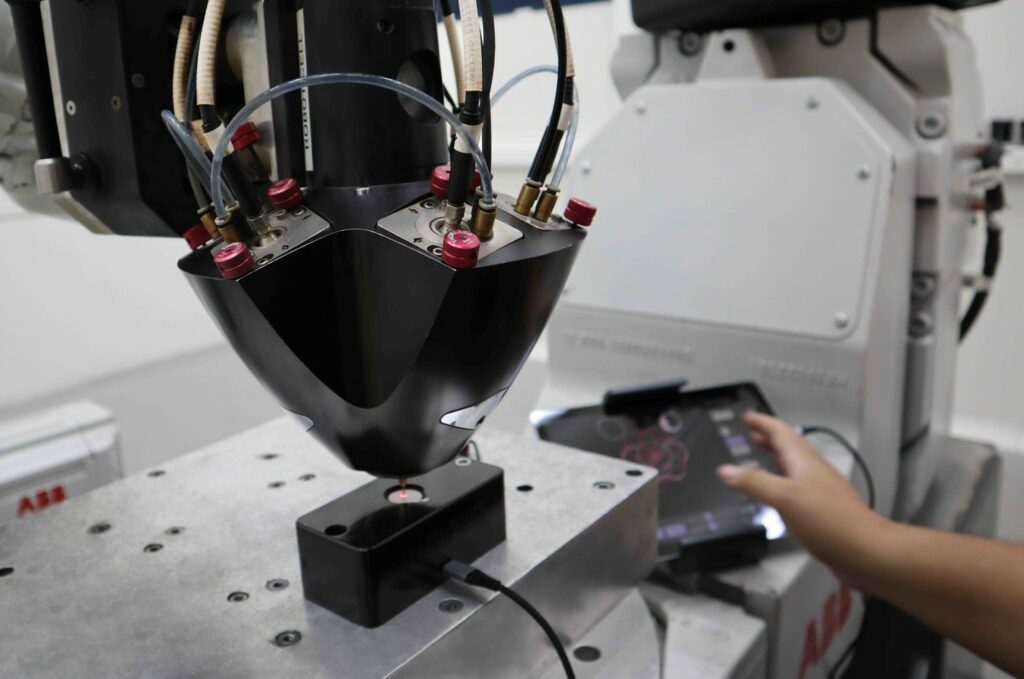
The Laser Calibration System is an optional kit that would enable to calibrate Meltio’s multi-laser deposition head accurately and effortlessly on all three of its metal 3D printing solutions. The system consists of a laser alignment camera that has to be placed under the printhead as it allows for a clear view of the focus point of the lasers. The camera is controlled using a portable controller, which also comes included in the kit as well as a software specifically designed to filter the camera image and guide the user to focus each laser on the most optimal point.
However, manual laser alignment remains possible but will require a very experienced operator to match the consistency of the laser alignment kit.
Meltio’s multi-laser metal 3D printing technology is based on the use of six lasers pointing to a mutual point to melt the welding wire that is fed through the center of the deposition head. The lasers generate a high concentration of energy, called meltpool, that melts the metal feedstock. As a result, welds beads are stacked precisely on top of one another.
The alignment of each laser is critical so they hit the exact point where the energy is concentrated, the misalignment of the lasers leads to energy inefficiency and defects on the 3D printed parts. The camera makes the calibration process easy to follow.
“We have developed the Meltio Horizon software and the Laser Calibration System with the aim of facilitating the use of Meltio’s metal 3D printing technology for industries around the world. The launch of our new software [facilitates and shortens the learning time while the] Laser Calibration System will give industrial companies a new tool to be able to work with guaranteed reliability in the creation of their metal parts”, Ángel Llavero concludes.
Remember, you can post free of charge job opportunities in the AM Industry on 3D ADEPT Media or look for a job via our job board. Make sure to follow us on our social networks and subscribe to our weekly newsletter : Facebook, Twitter, LinkedIn & Instagram ! If you want to be featured in the next issue of our digital magazine or if you hear a story that needs to be heard, make sure to send it to contact@3dadept.com