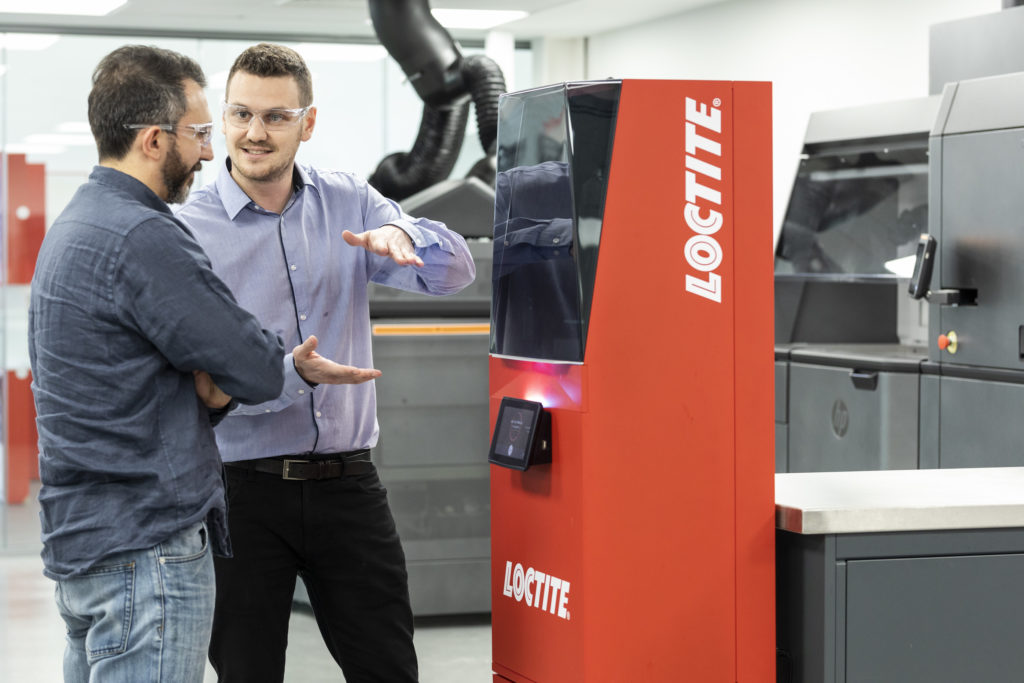
Last year, the Bossard Group announced its entrance in the 3D printing industry alongside a collaboration with three companies that should support its team in this journey: German RepRap, Trumpf and Henkel. As part of this agreement, Henkel revealed that the Bossard Group would take advantage of its 3D printing technology, but did not give further information about its specifications.
At Formnext 2018, Henkel officially launched its 3D printing solutions as part of a programme called the Loctite 3D Printing programme, a programme that raised the attention of Partool, a Belgian company that provides a wide range of industrial solutions.
We recently saw Henkel’s 3D printing solutions at Partool’s booth during Machineering 2019, an event dedicated to machines and tools, and decided to invite the company in this Opinion of the Week. Jonas Fincioen, one of the management executives, told us more about these solutions and their services. Jonas Fincioen has been working in the company for more than 9 years now and has gradually built up extensive experience in various departments of the company.
Jonas, what brought the company to the 3D Printing industry?
Partool has been providing the market with a wide range of industrial solutions for several years: parts, tools, machines, welding, etc. and it’s already been 4 years that we have rolled out our 3D solutions.
At first, the idea was simply to discover 3D Printing. With our FDM 3D printer, we started to produce some parts in order to see what was possible. Thereafter, we started receiving some requests from clients, here and there, for 3D printing services.
The more complex the requests were, the more powerful our technology was supposed to be. We received a request for an enhancement and refurbishing project. A small part of this project needed caps. We made some improvements on the weak points of the caps but to meet the requirements of the finished product, we needed a different printing process. That’s how we bought our SLA- 3D printer.
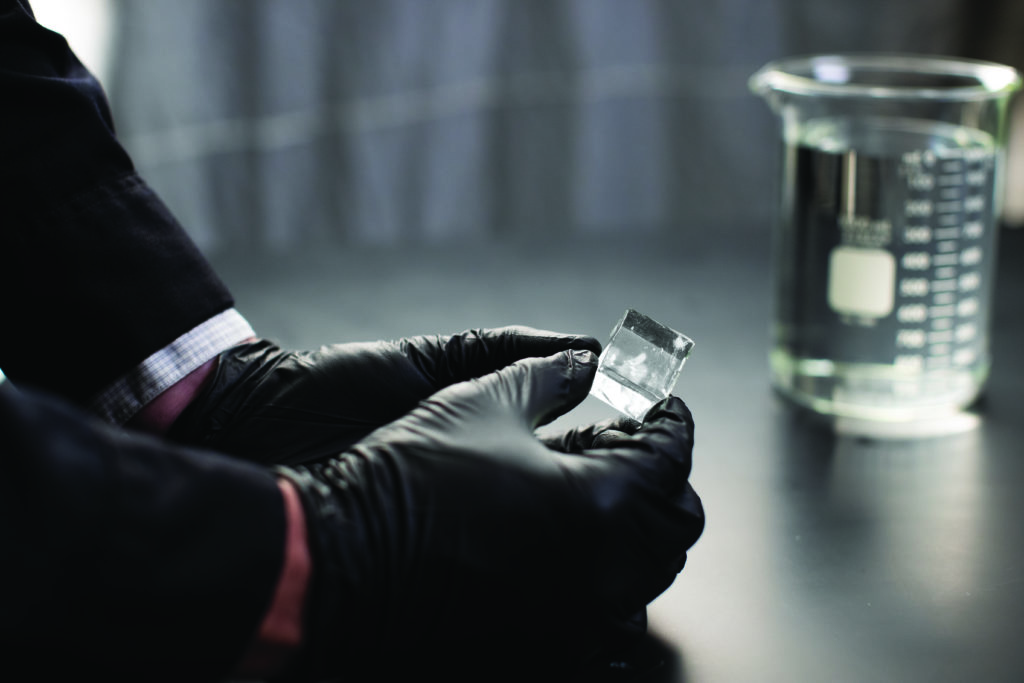
From then on, we started to work on the basis of projects with our clients. At the beginning of 2018 we stepped in the beta-partner program of Loctite. We’ve always been a distributor for the bonding products so when the question came to step into the 3DP-program, we jumped at the opportunity and Formnext 2018 enabled us to increase our visibility and to enlarge our services. So today, we also distribute the functional resins, 3D specific bonding, enhancement coatings and equipment (DLP-printer, UV-chamber).
What are the different 3D printing technologies Partool provides?
We provide FDM, SLA and Loctite DLP and our partners provide other technologies.
Tell us more about Henkel’s 3D Printing solutions
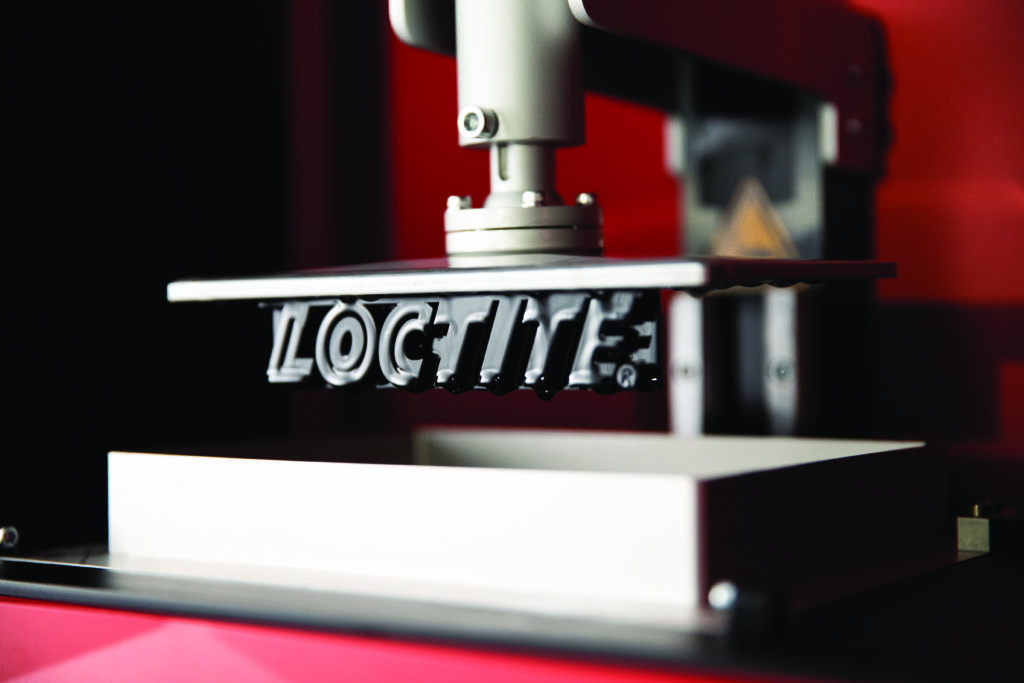
First, Henkel’s DLP industrial 3D Printer, the PR10.1, delivers accurate parts and can be used with the new resins of the producer. The printer enables the production of multiple components at the same time without influencing build speed.
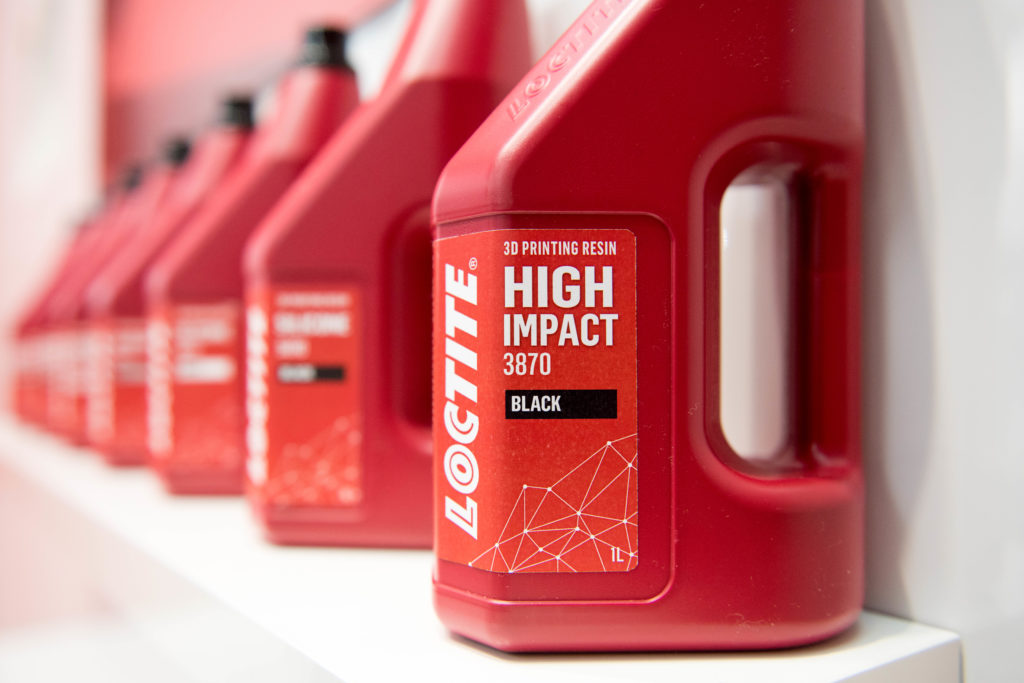
Thereafter comes the bonding kit. It contains 2 different bonders – the Loctite 3D Printing Universal Bonder and the Loctite 3D Printing Instant Bonder –, a primer, an activator and a cleaner. So, everything to get started but all the products can be bought separately as well. Having a kit enables to easily bond prototyping parts for the most-known 3D Printing technologies.
Both bonders have been tested on different 3D printing technologies and materials (MJF, SLS, FFF, DLP, SLA and binder jetting) and are easy to use. However, they are not only intended for professionals, as one may think. Industrials can also take advantage of them.
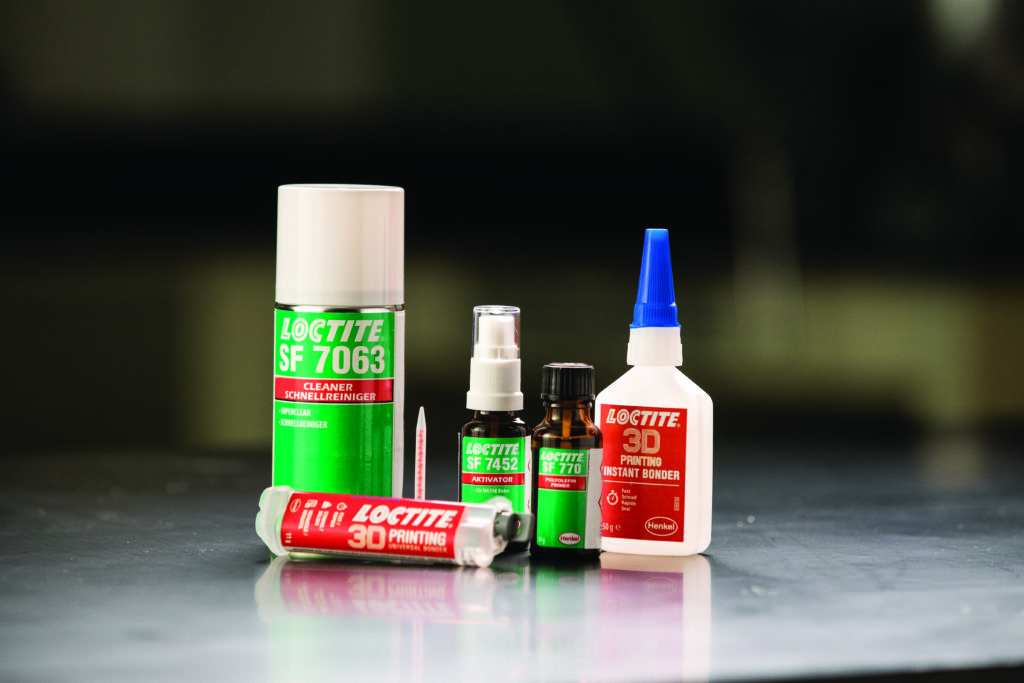
Speaking of 3D printing technologies in general, is there a specific 3DP technology that performs better than others in the Belgian and Dutch markets? How do you see this evolution in the long run?
At this moment, the highest demand is for functional parts, so MJF and SLS do tend to outperform the others.
In the long run, I think these markets will become more diverse. Current technologies that outperform the others or new entrants on the market that deliver functional parts with diverse mechanical properties will lead to an increasing number of applications within certified markets.
Jonas
Any last words regarding Partool’s contribution/development in the 3D printing industry?
With the Loctite 3DP program we just want to show that borders are starting to fade. There are functional materials that we can use for the printing process but the market is not limited to 1 process or just 1 set of part properties.
The bonding kit might enable to push the boundaries of the printing volume or combine different product properties. Furthermore, the best part of it, is the possibility to combine traditional technologies with new AM technologies and get the best of both worlds.
And if he adds coatings, the user can enhance the manufacturing process even further and obtain various benefits including wear-resistance, flame retardancy, UV- and weather protection, waterproof, electrical conductivity and more.
It opens up new possibilities and new ways of thinking in terms of parts creation.
For further information about 3D Printing, follow us on our social networks and subscribe to our newsletter!
Do you want to be featured in the next issue of our digital magazine? Send us an email at contact@3dadept.com
//pagead2.googlesyndication.com/pagead/js/adsbygoogle.js (adsbygoogle = window.adsbygoogle || []).push({});