Among the wide range of applications that Additive Manufacturing allows, a key interest is devoted to processing superalloys for aerospace, automotive and even nuclear; industries in a nutshell, that require outstanding combination of superior mechanical properties and wear resistance. In this context, Inconel 718 receives increasing interest.
Quick reminder: superalloys are a type of materials that can retain high strength at elevated temperatures. Such materials become of utmost importance for industries that need to manufacture components out of high-performance metals. Nickel-based superalloys are the type of alloys that are compatible with additive manufacturing. One of these superalloys is Inconel 718.
To date, many operators do not know the type of AM technologies that can process this alloy as well as its main applications and features. This article aims to shed light on this material and its use in the AM industry.
Introducing Inconel 718
Inconel 718 (IN718) is a low cost nickel-based superalloy which is mostly used as a turbine disk material. The superalloy was first used to overcome the poor weldability of superalloys in 1960s. As AM and welding processes are quite similar, operators have been using IN718 with metal AM processes since then, to facilitate the understandings of process-microstructure-property relationships. This might explain the reasons why IN718 is mainly associated with 3D printing/AM technology.
In terms of mechanical properties, IN718 provides an exceptional thermal resistance – up to 700°C and high resistance to oxidation and corrosion. It is also acknowledged for its excellent strength, high yield, tensile and creep-rupture properties. When additively manufactured, Inconel delivers strength over a wide temperature range, which makes it a good candidate for high-temperature applications or low-temperature applications.
With a melting point of 1430°C for instance, the material demonstrates effective resistance to heat and high temperatures, therefore suits well in cryogenic conditions. At room temperature on the other hand, it exhibits a minimum of 725 MPa yield strength and 1035 MPa tensile strength. When it undergoes solution and precipitation treatment, these numbers rise to 1035 MPa and 1240 MPa, respectively.
IN718’s composition includes about 50-55 % nickel, 17-21% chromium, 4.75-5.5 % niobium and tantalum, and trace amounts of molybdenum, titanium, cobalt, aluminium, manganese, copper, silicon and other elements.
It should be noted that Inconel 718 often raises confusion with another popular nickel-based superalloy, Inconel 625. The addition of iron in IN625, coupled with a lower nickel content allows the price point of Inconel 718 to be lower than that of Inconel 625. These elements mainly constitute the differences between the two materials. Let us see now how it functions when it is processed.
Processing Inconel 718
Inconel 718 is mainly processed by powder-bed processes. Metal AM technologies that can process this material include Electron Beam Melting (EBM), Selective Laser Sintering and recently Binder Jetting.
As each metal AM process is unique, the way it will process Inconel 718 will undoubtedly alter the structure – property – processing – performance of the part that is being manufactured.
We’ve asked Kyle Myers, ExOne’s R&D Manager, a number of questions about this material and the way they tune it before it is used by any customers. As a reminder, the recent qualification of Inconel 718 brings the total number of materials ExOne’s binder jetting can process to 22.
With several decades of expertise in binder jetting and the industry in general, it’s safe to say ExOne knows a thing or two about the market and the way companies across vertical industries adopt these new technologies.
The manufacturer of binder jetting systems does not develop their own unique chemistries and powders. As per the words of Myers, they “mostly develop processing parameters that work for traditional materials and commonly used powders”. “These traditional materials are qualified to known standards which most of our customers are familiar with, which alloys them to adopt our manufacturing process for their application quicker. Therefore, any customer that already designs a part, for their application with the inherent physical and mechanical properties to that specification, can insert binder jetting into their manufacturing process. Other customers may want to take advantage of AM, but work with a similar alloy to In718. They will need to do their homework to make sure the specifications of In718 can fit their specific application”, Myers told 3D ADEPT Media.
For researchers, the microstructure of additively manufactured IN718 is largely dependent on the specific process history. With different process parameters, such as scanning strategy and component geometry, quite different as-manufactured IN718 microstructures can be obtained even under same manufacturing method, let alone different manufacturing methods. Therefore, the heat treatment for AM IN718 should be customized with regards to its specific process history. Standard specification ASTM F3055 recommends a heat treatment for powder-bed-fusion additively manufactured IN718.
However, this standard only provides a guideline for stress relief and hot isostatic pressing treatments. Establishing the actual heat treatment should be as agreed between the component supplier and purchaser.
Applications of Inconel 718
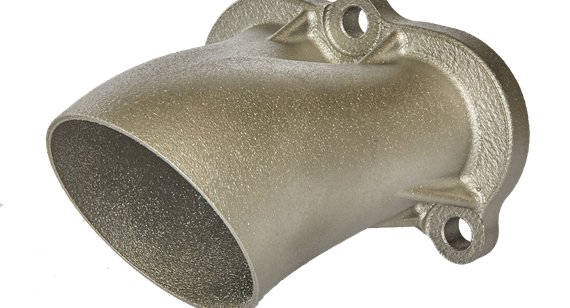
Inconel 718 is a natural fit for extreme heat applications such as metal die casting.
As mentioned before, IN718 is mostly used as a turbine disk material. Due to its efficient weldability and heat resistance, it has become an integral component of gas turbine engines and turbojet engine parts such as compressor casings, discs and fan blades.
A recent study from The Pennsylvania State University highlights the degradation of turbine blade tips in aerospace today: “after degradation surpasses a definite point, the entire blade must be taken out of service and replaced with a new blade. The material taken out of service is regarded as scrap and thrown out. This wasteful procedure causes serious financial impact to the aircraft industry as well as being a nuisance in the attempt for a more sustainable earth”.
Combining additive manufacturing (AM) and Inconel 718 for the manufacturing of these turbine blades would provide a possible solution to this problem by allowing for the incremental replacement or repair of the worn or broken part.
The superalloy has also found its way into the production of rocket engines and into the nuclear industry.
At the end of the Winter season, Westinghouse Electric Company installed a 3D-printed thimble plugging device in Exelon’s Byron Unit 1 nuclear plant. The installation was made during their spring refueling outage.
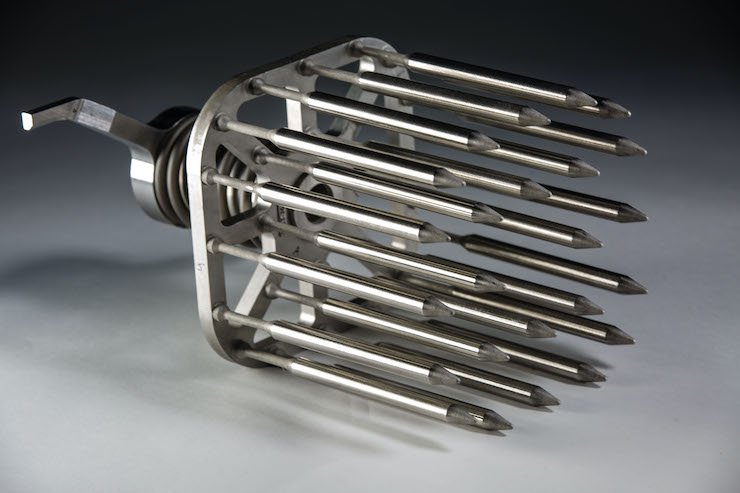
Westinghouse Electric Company provides a wide range of nuclear power plant products and services to utilities throughout the world. The company’s products and services include advanced nuclear plant designs, nuclear fuel, service and maintenance as well as instrumentation and control systems. Exelon on the other hand is a US-based energy provider.
The collaboration between both companies is the result of three years of development work. According to our colleagues from Nuclear Engineering, when Westinghouse embarked on this mission, the nuclear industry did not have any direct radiation experience with additively manufactured materials. Westinghouse was therefore one of the first to take these first steps in the production of a 3D printed component intended for a commercial nuclear reactor. The company had mini-tensile specimens of Stainless-Steel Alloy 316L and Inconel Alloy A718 additively manufactured for testing. Those alloys were the ideal material for crossover to nuclear applications.
A laser powder-bed system has been leveraged for the production, as it fuses layers of powdered metal together.
Over time, the company designed and additively manufactured other fuel components such as a bottom nozzle and an advanced tubular grid. The designs fully take advantage of additive manufacturing. It also affects the freedom component designers have in applying the advantages of the process to think out of the box. This technology has allowed them to better address flow, pressure and other issues to fuel performance with improved designs; issues in the end, that they have not been able to address using traditional manufacturing methods.
This exclusive feature has originally been published in the September-October 2020 issue of 3D ADEPT Mag.
Remember, you can post free of charge job opportunities in the AM Industry on 3D ADEPT Media or look for a job via our job board. Make sure to follow us on our social networks and subscribe to our weekly newsletter : Facebook, Twitter, LinkedIn & Instagram ! If you want to be featured in the next issue of our digital magazine or if you hear a story that needs to be heard, make sure to send it to contact@3dadept.com