Metal Additive Manufacturing applications are filled with examples that involve the use of titanium, Inconel and recently, pure copper. As we are exploring the next phase of growth of this segment, we need to consider aluminum and aluminum alloys as the range of materials AM users can capitalize on. The only thing is that the benefits one can get by processing aluminum alloys with AM are underrated, even overlooked and the weird part of it, is that I understand why.
It’s been centuries that aluminum and aluminum alloys have been serving the needs of industries such as aerospace, automotive or packaging, due to their mechanical properties: high strength-to-weight ratio, malleability, electrical conductivity, corrosion resistance and recyclability. The processing of these materials has long been associated with conventional manufacturing processes such as casting, sheet metal forming or machining.
“There are excellent options for making high-performance aluminum parts. For example, aluminum alloys can be machined much more readily than other metals (titanium, stainless steels…). We can cast aluminum into complex shapes, we can form sheets into beverage cans or automotive body panels. Many assembling processes exist (welding, brazing, mechanical assembly, adhesive bonding… And of course, aluminum is infinitely recyclable. This is why aluminum is the material of choice in many packaging and transportation applications, particularly when light weight and/or recycling are the drivers,” Alireza ARBAB, Head of Additive Manufacturing at Constellium told 3D ADEPT Media.
Furthermore, when we look at costs, aluminum is less costly than copper, stainless steel, titanium, and other metals – even if its raw form tends to cost more than the common grades of low-carbon steel and low-alloy steel.
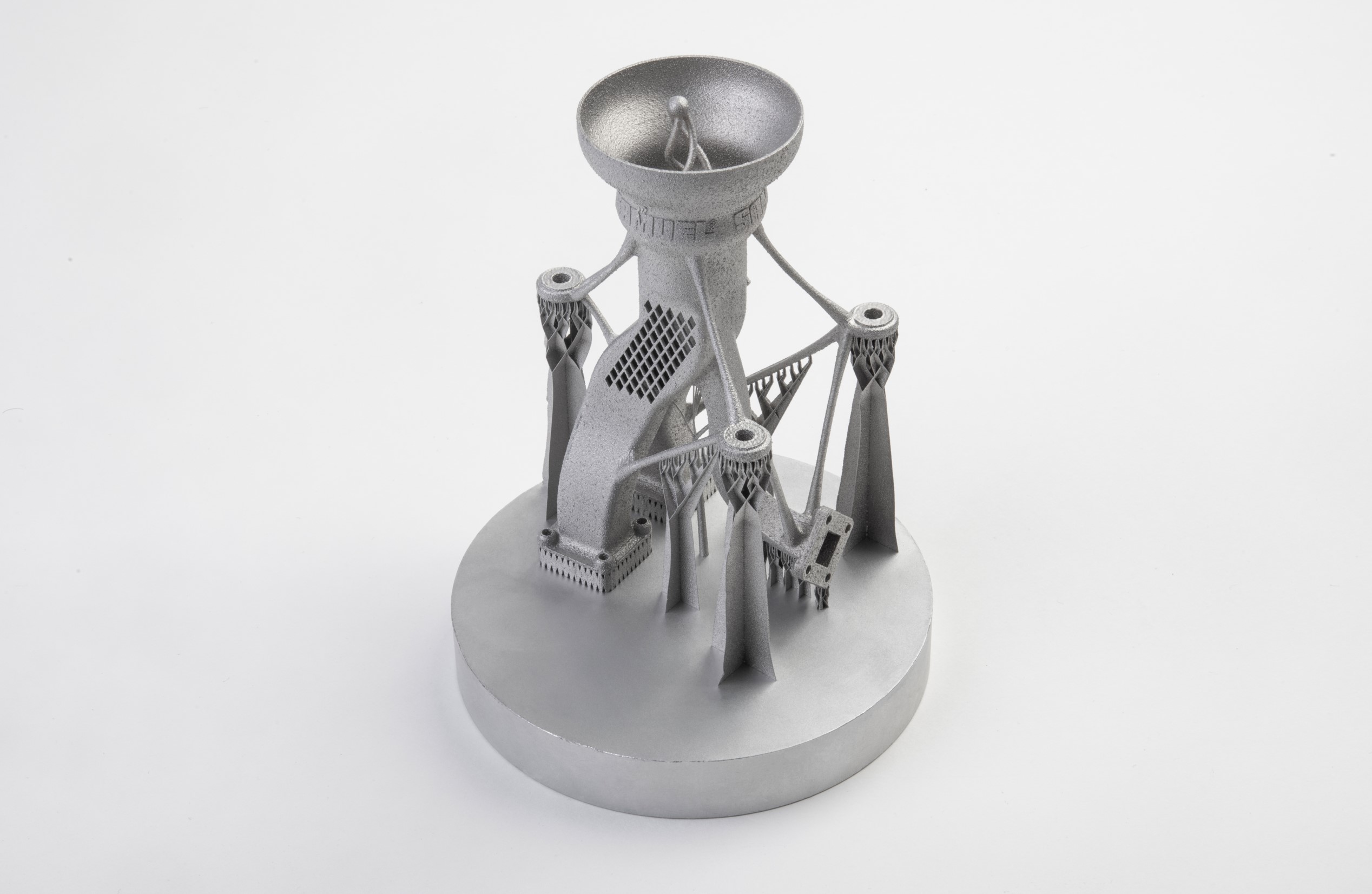
These favorable properties and these cost considerations have raised the interest of AM users and AM solutions providers that have started exploring how they could combine these advantages with the ones of AM, providing this way another manufacturing option to vertical industries adopting AM.
The article below aims to understand the opportunities and challenges of aluminum AM. To do so, it will highlight:
- First, aluminum or aluminum alloys?
- The different AM technologies that can process aluminum: key focus on LPBF and a manufacturing process specifically designed for aluminum components
- The AM applications that will drive the use of aluminum alloys across the metal AM segment
- And the considerations that one should take into account to explore a sustainability route.
1- First, aluminum or aluminum alloys?
If you’re new in the materials industry, one question that may legitimately come to your mind is: why are aluminum alloys used rather than pure aluminum? The answer obviously varies from one application to another, but it should be noted that for most industrial applications, pure aluminum is often reported to be expensive, too soft and weak to act as a structural material – despite its many winning properties.
To the best of our knowledge, USA-based Elementum3D and Germany-based m4p (metals 4 printing) are two material producers that have been able to develop pure aluminum powders for L-PBF.
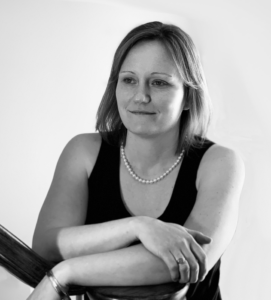
“Aluminum is almost always alloyed and heat-treated or work-hardened to increase strength. The alloy depends on the application. Casting and PBF both require melting and flow, as such they commonly have high levels of silicon and the resulting parts are prone to porosity. This reduces the strength of the parts. Alloy’s Sheet Forging process does not require melting or flow, and as a result a wider array of aluminum alloys is possible and porosity is not an issue. Our first alloy is 6061 – fully dense,” Alison Forsyth, CEO of Alloy Enterprises explains.
Moreover, it can be alloyed with many other elements to overcome its low strength. According to Arbab, aluminum can be combined with elements such as Magnesium, Zinc, Copper, Silicon, Manganese, to name a few. The key is to be able to design the right aluminium alloys for different markets and production processes.
1- The different AM technologies that can process aluminum and aluminum alloys
Among the wide range of AM processes that are available on the market, this may come as no surprise to you to read that powder-bed fusion (PBF) is the most-widely used process for aluminum. Other processes include WAAM, binder jetting, DED, EBAM and Kinetic. Each of these technologies can process a specific type of aluminum alloys.
Compared to other metals, the high reflectivity towards the typical fibre laser wavelength, the high thermal conductivity and tendency to crack during solidification are items that make it difficult to process aluminum with a laser beam process. That’s why conventional casting alloys such as AlSi10Mg and AlSi12 have been mainly used for LPBF. They are relatively easy to process compared to high-strength Al alloys.
Among the aforementioned processes, Laser Beam Powder Bed Fusion (LPBF) and Directed Energy Deposition (DED) can use a laser beam – the latter of which can use powder or wire as a feedstock.
Let’s focus for a few minutes on laser powder-bed fusion.

Constellium’s Head of AM told 3D ADEPT Media that “the many alloys developed for existing applications are not optimized for production using AM technologies, in particular Laser Powder Bed Fusion (LPBF).” For the expert, a look at the big picture is necessary to understand the full process – from powder management to the final parts, including printing, post-processing and quality control – and the areas that may require specific points of interest.
“Our Aheadd® CP1 alloy [a material specifically designed for AM] uses the advantage of the extremely rapid solidification rate of LPBF allowing Constellium to use specific alloy design rules to create a much better solution. As an example, CP1 contains 1% of iron as a key alloying element. In most aluminum alloys, iron alloy is limited as impurity”, he points out.
On another note, in addition to high reflectivity and low laser absorption that may result in defects, the properties of certain aluminum alloys may also result in defects like porosity, cracks, poor surface finish, shrinkage, oxidation and residual stress.
Furthermore, each 3D printer comes with a set of unique parameters. This means that an issue observed in machine X may not necessarily be the same as the issue observed in machine Y.
Among the solutions that can be explored to overcome these defects, one notes the use of additives, laser power, scanning and powder drying.
Researchers from the Norwegian University of Science and Technology explain in a research that the category “additives” refers to solutions that include the addition of additives to the Al alloy powder or new alloys. This means that alloy blends can be created to enhance the desired properties. Laser power refers to solutions where it is proposed to either increase or decrease the laser power. This is often combined with other solutions such as changing the scanning speed. The category scanning includes solutions, where the scan parameters are changed, such as changing the scan speed or performing a double scan. With powder drying, it is possible to pre-dry the Al alloy powder before melting the powder.
What if we consider a process specifically designed for aluminum parts?

Alison Forsyth opened our eyes to a new way to fabricate aluminum parts and materials using high-speed manufacturing. For Forsyth, aluminum is different from other metals because it “forms a robust oxide layer in milliseconds. This makes it difficult to bond or print, particularly in processes with a high surface area-to-volume ratio which maximizes the amount of oxide. Alloy’s Sheet Forging process has been designed to overcome this challenge.”
Speaking of their Sheet Forging process, she explained that “Alloy Enterprises is transforming how aluminum components are made. Alloy manufactures fully dense aluminum components, enabling customers to scale from prototype to production. Unlike powder-based additive manufacturing processes, Alloy’s Sheet Forging process is high-throughput and produces components with superior material properties. The process starts with digitally slicing the 3D component into discrete layers. The layers are then laser-cut from Alloy’s custom feedstock and an inhibiting agent is selectively applied to create in-situ supports. The full stack of registered sheets is then diffusion-bonded together. Finally, the parts are removed from the block and heat-treated. Alloy’s process provides the flexibility of wrought material properties and the geometric complexity of additive manufacturing to produce lightweight components with optimal strength, durability, and thermal conductivity.”
We are not aware of any limitations of the process yet, but if it works well, this process could yield a significant speed advantage over LBPF as it does not need to move point by point through the entire area.
1- The AM applications that will drive the use of aluminum alloys
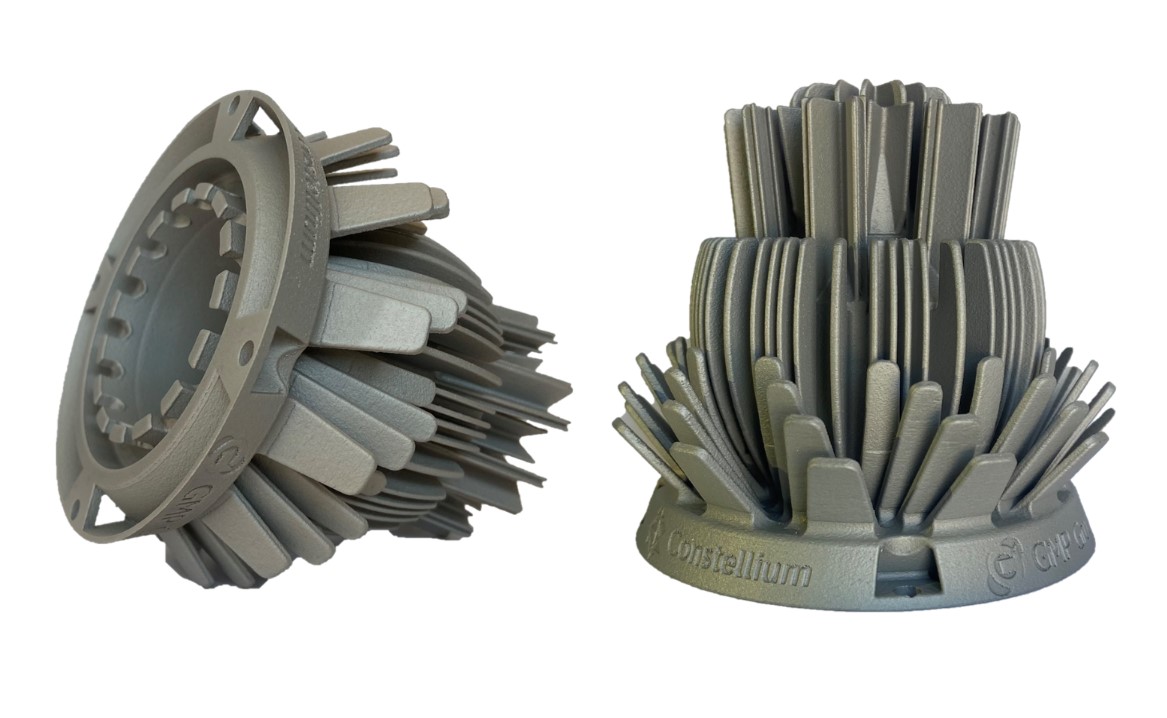
Among the vertical industries mentioned above, one industry that may see the increasing use of aluminum alloys is the EV industry. The more EVs will be developed, the more OEMs in this sector will need strong, lightweight materials such as aluminum.
According to Alloy Enterprises’s CEO, aluminum will be part of the electrification journey of everything that moves, and flexible on-demand cost-competitive fabrication will be essential to this transition. Speaking of their Sheet Forging process especially, she explains: “Automotive, EV, heavy and industrial equipment can all be served by Alloy’s Sheet Forging process. Additionally, some aluminum alloys have high thermal conductivity relative to its weight. Cooling and thermal management applications, as we pack more batteries or electronics into vehicles, machines, and computers, will continue to drive adoption of Alloy’s Sheet Forging process.”
For Arbab, there are already many exciting LPBF applications that can be achieved with aluminum alloys. They include, for instance, satellite components, defense, heat-exchangers, and high-end automotive parts.
“As costs come down and designers become more aware of the new possibilities brought by specific alloys such as Aheadd® CP1. We already receive many requests for application studies in areas such as on-demand spare parts, semi-conductor industry applications…The current business is just the tip of the iceberg,” he adds.
2- Which considerations should be explored on the sustainability route?

At present, apart from reusability of powders, one realizes that material producers mostly focus on sustainability factors that are inherent to the manufacturing process of their material.
Forsyth told 3D ADEPT that the feedstock used in Alloy’s Sheet Forging process has been designed to reduce carbon emissions by 15X compared to powder. Scrap from the Sheet Forging process can be reused without requiring energy-intensive and costly recycling processes.
In the same vein, Constellium’s powder can be recycled multiple times in the AM machines and without any physical limit. Arbab said the team is currently working on optimizing powder production yield, quality and recycling with their atomizer pilot line at the Research & Technology Institute IRT M2P in northern France which is entirely dedicated to optimize production processes including recycling.
That being said, understanding the full lifecycle of a material is probably the first step to take for companies that are looking to produce more sustainable products and this should be the main topic of another article.
This dossier has first been published in the 2024 September/October edition of 3D ADEPT Mag.Featured image: Alloy Enterprises.