Remember when we said that the true success of an application usually depends on an underappreciated component: material? Well, the more AM advances, the more we realize that the array of opportunities materials offer are yet to be discovered. In this specific case, I am thinking of opportunities that necessarily intertwine innovative design methods and AM to ensure that optimum functionality and target behaviors are built into a new range of specialized materials. While a lot is being done at the research level, a Swiss startup gives hope for future commercialization of metamaterials.
To be honest, the first time I heard about metamaterials also known as lattice materials, I thought they were too good to be true. While there is still a bit of controversy on their exact definition, one thing scientists seem to agree with is that they are architected cellular materials that can be inspired by nature or human engineering intuition and that undergo modification in order to possess properties they don’t naturally possess.
If the concept of metamaterials was first introduced in 1967 by Victor Vesalago, it should be noted that their ability to become mainstream could largely depend on the growing adoption of AM across industries and the cost considerations of the technology that will enable them.
As AM is more mature today than it was 10 years ago, it’s about time to draw the industry’s attention to what could be the next material driving the development of new applications.
At the intersection of software design and material development
The development of metamaterials would logically call for so many cross-disciplinary competencies that it might be hard to define the people behind their creation as exclusive material producers. After a conversation with Daniel Bachmann, Chief Innovation Officer of Swiss startup Spherene Ltd., I am tempted to define the developers of metamaterials as organizations/companies at the intersection of software design and material development.
Bachmann explains that in 2018, by working on a paper model, the team at Spherene explored the development of a new class of minimal surface which led them to the creation of a specific algorithm. Based on a cloud-based API, this algorithm can fill a design volume with an Adaptive Density Minimal Surface (ADMS), that follows inverted spherical surfaces to create a strong yet open framework within a given object. Simply put, they develop lattices using an algorithm based on a minimal surface which allows for the creation of accurate shapes with optimal geometry.
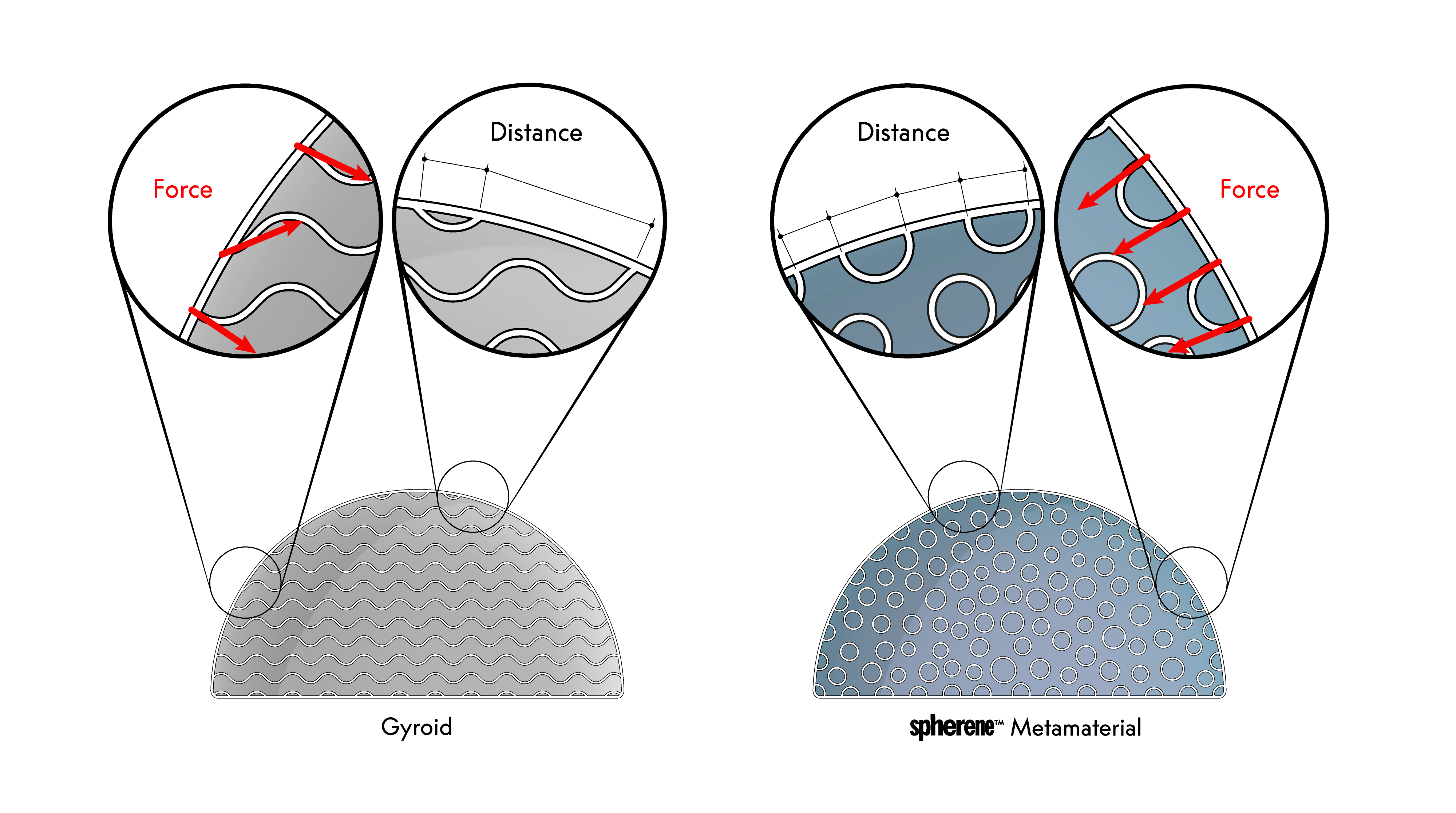
One of the strengths of Spherene probably lies in the distribution of forces in the desired area. According to Bachmann, while a sphere can distribute forces around an empty volume, a spherene allows for the distribution of forces across the interior in an ideal manner.
“Our technology enables us to apply forces in any direction of the sphere. These isotropic and surface conformal capabilities help for instance to make a piece of steel as light as aluminum and to save a lot of energy to produce the end material”, Bachmann outlines.
Spherene’s solution makes it possible to develop metamaterials based on plastics (filaments), metals, or even resins. Despite these varieties of materials, the Chief Innovation Officer confirms the solution is most advanced to produce parts in powder-based materials. “It does not matter if it is plastic or metal. Resin comes in 2nd position while FDM might take a longer time to print new materials developed with our technology”, he adds.
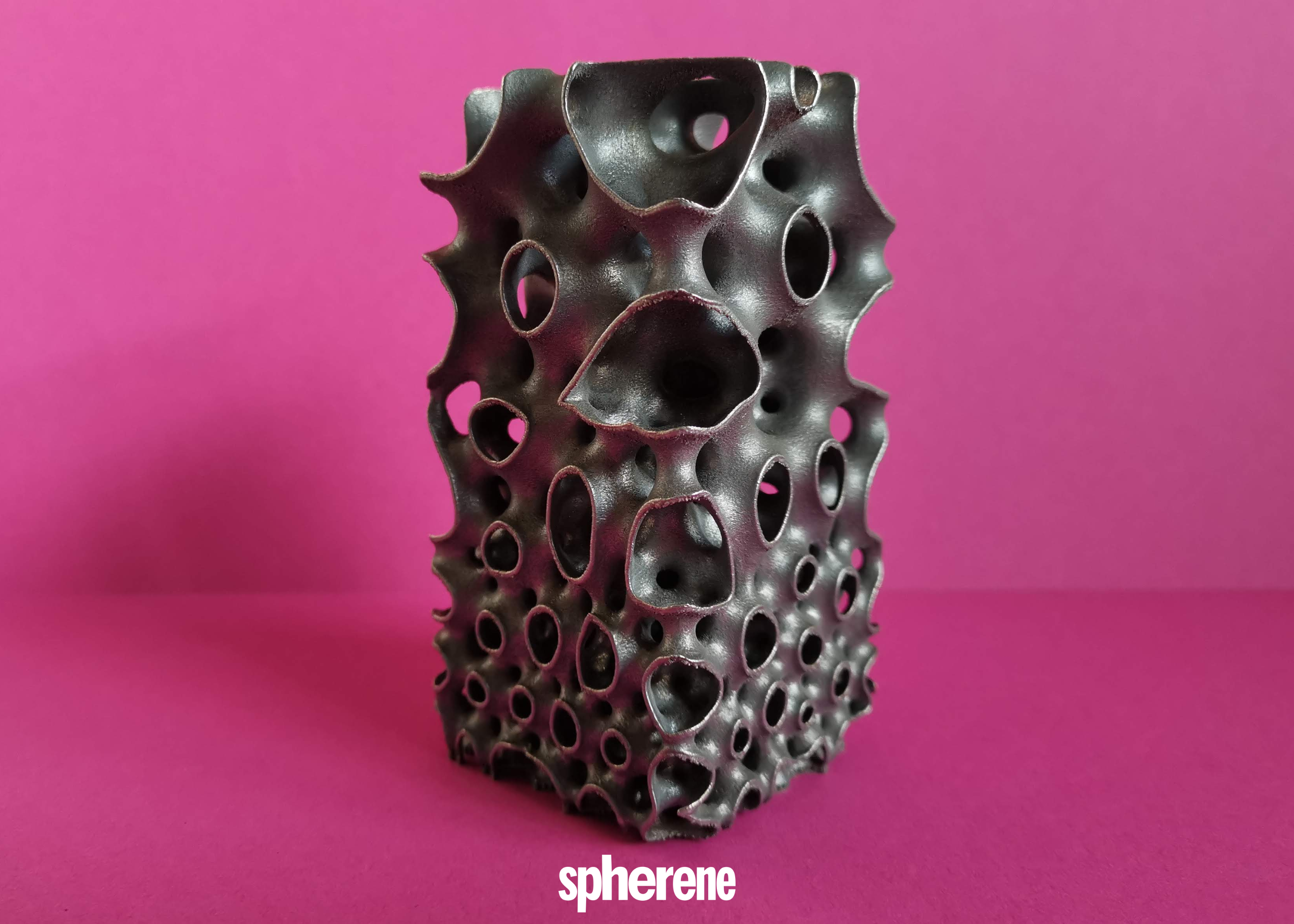
To date, Spherene licenses its software solution so that organizations can create the form they need for each material. They also provide the service to do that if the customer does not want to.
If Spherene’s solution is already ready to reach a wider audience, another approach that is worth mentioning is the AI-based design method developed by Rayne Zheng, associate professor of materials science and engineering at Berkeley Engineering and his team of engineers.
Zheng and his team used machine learning to inversely design complex mechanical behaviors of a material and engineering product that can be printed by a desktop 3D printer.
“With our method, a user can input the desired mechanical behavior described by a curve, and this data is then fed into the machine learning code to generate a design — a process that takes only a few seconds. And once that design is 3D printed, it will replicate the desired mechanical behavior,” said Zheng. “While still in its early stages, our machine learning-based design method can produce almost any type of material behavior with nearly 90% accuracy.”
To create their AI-based design approach, the researchers first had to develop and implement an integrated machine learning framework, which consists of an inverse prediction module and a forward validation module.
“The inverse module uses the desired mechanical behaviors to design the micro-structure of the material, and the designed material is passed to the forward module for the evaluation of its mechanical behaviors,” said Chansoo Ha, co-lead author of this study and formerly a postdoctoral researcher at Virginia Tech in Zheng’s lab. “This helps ensure that the desired properties are accurately reflected in the finished product.”
Next, they developed a family of cubic symmetric, strut-based cells to train the machine learning model. The cells’ lattice structure makes it possible to achieve almost any mechanical behavior and the corresponding stress-strain curve. The researchers then 3D printed the cells and tested them to generate training datasets.
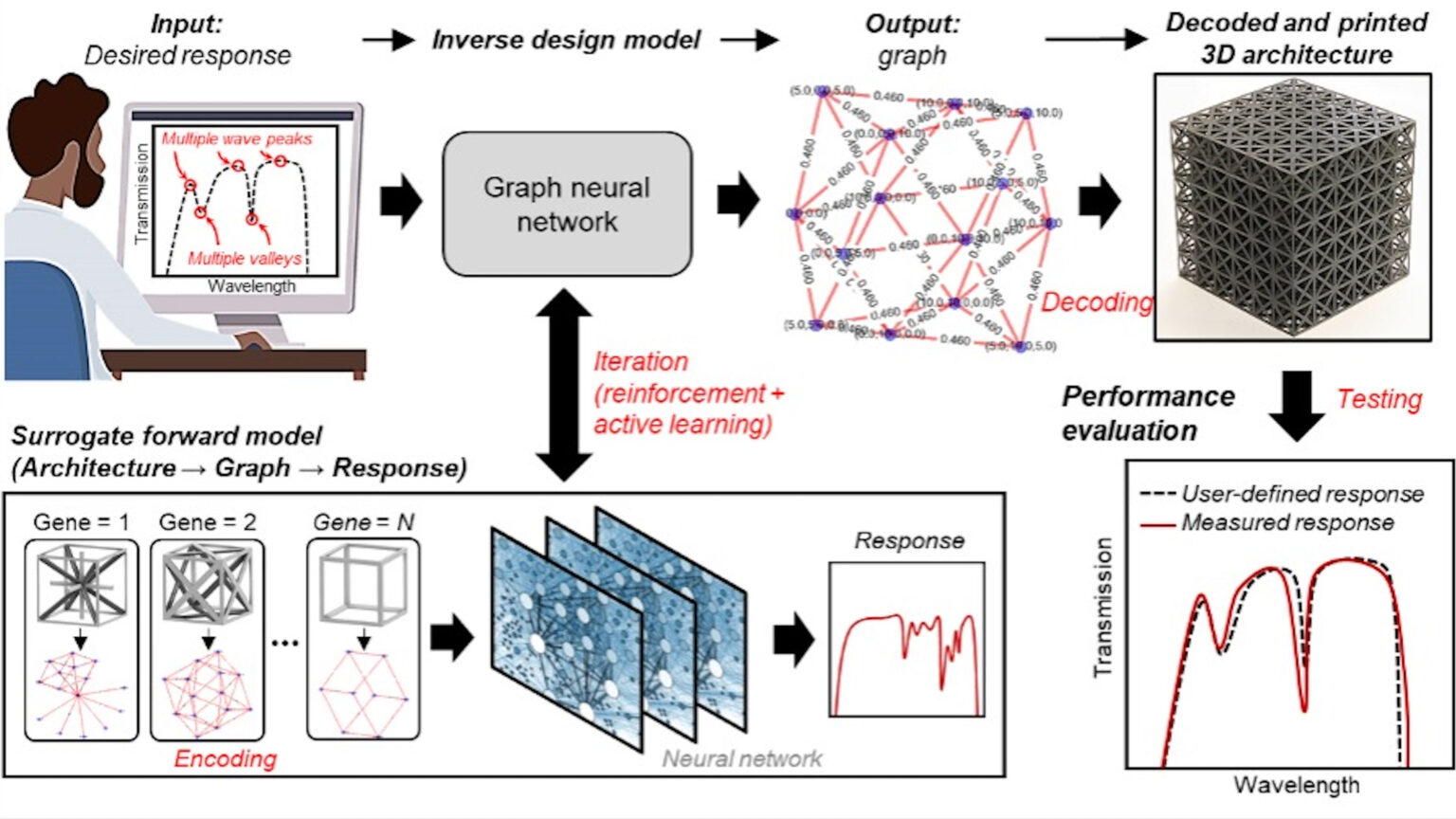
What considerations should one take into account to develop metamaterials?
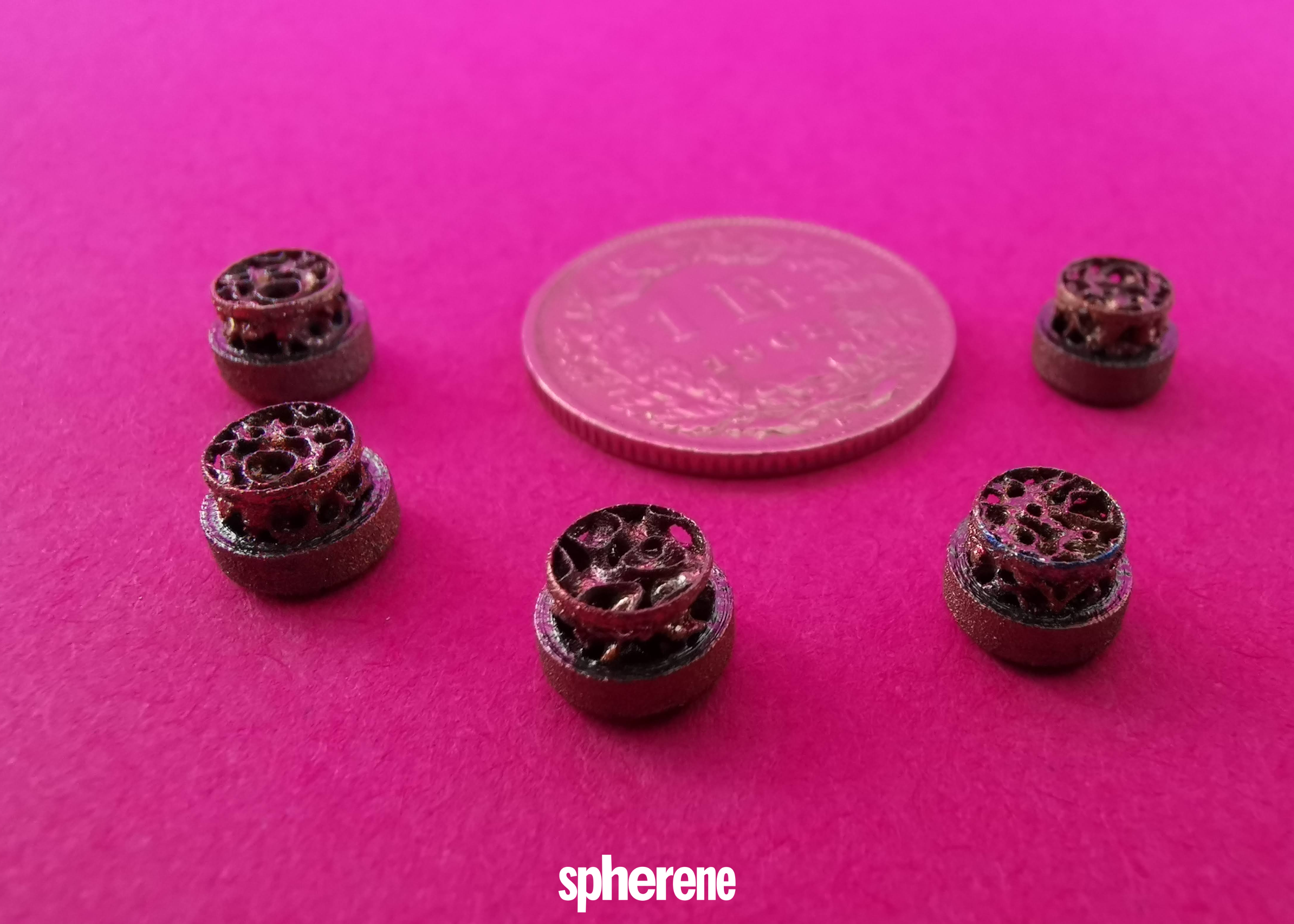
As with any new technology, the use of the Spherene API will require a learning curve. First and foremost, since “our technology is relatively new in the market. It’s crucial for the engineer to operate a shift from traditional engineering to modern engineering”, the Chief Innovation Officer says. The same argument was uttered multiple times when AM was not mature enough. Exploring the development of metamaterials requires a shift in mindset.
Secondly, it’s important to consider one’s existing workflow. Using the Spherene API makes it easy to adapt one’s workflow and to insert all the variables to test it on a 3D printer.
Thirdly, cost is a factor that could tip the balance. While they anticipate organizations might find the cost of the license quite substantial (which makes sense given the novelty of the solution), Bachmann would like to urge industrials to keep in mind the advantages they can benefit from:
- Material & time savings: newly created designs filled with the exact structures lead to materials that are rapidly processed by 3D printers which leads to time savings. Taking the example of a satellite application, Bachmann explains how in 5 minutes, they have been able to save 20 hours of engineering time;
- A self-supporting method which means one can print without supports;
- Lightweighting: the spherene metamaterial can remove bulk material regardless of its density, thereby reducing the component weight;
- Customization at the design level: the spherene geometry can be positioned alongside solid sections to seal specific areas, incorporate screw holes, or form inner voids. Gradients can also be utilized to decrease material usage, adjust the center of gravity, or manage elasticity.
Applications of metamaterials
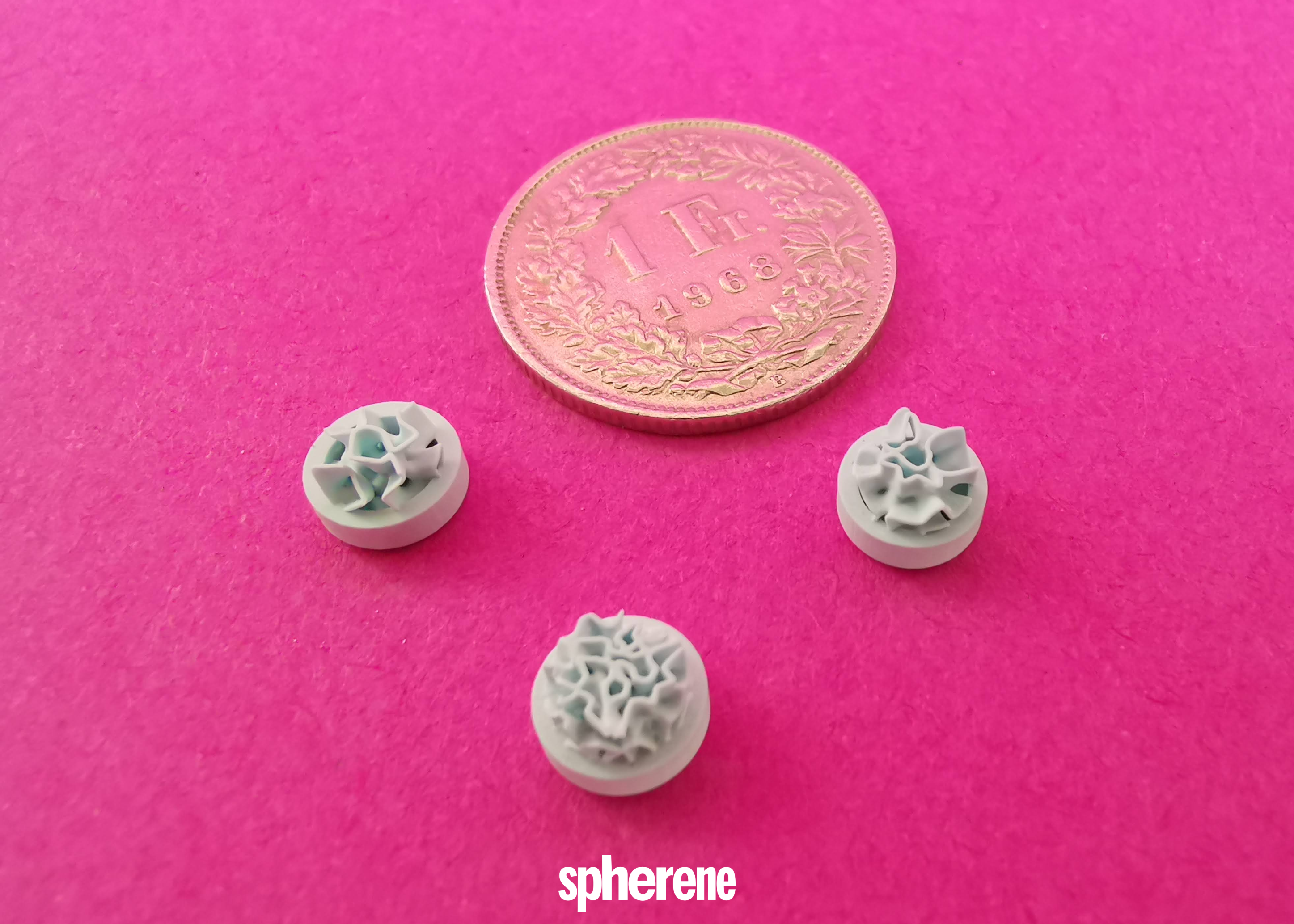
Researchers have explored the potential of metamaterials in electronics, communications, and defense applications. Among the wide range of applications that could help validate the capabilities of their technology, Spherene Ltd. counts an ESA satellite bracket, a waveguide for a communication satellite, and a bioceramic implant tested for bone ingrowth. They are currently working on testing the capabilities of their technology on shoes for diabetics.
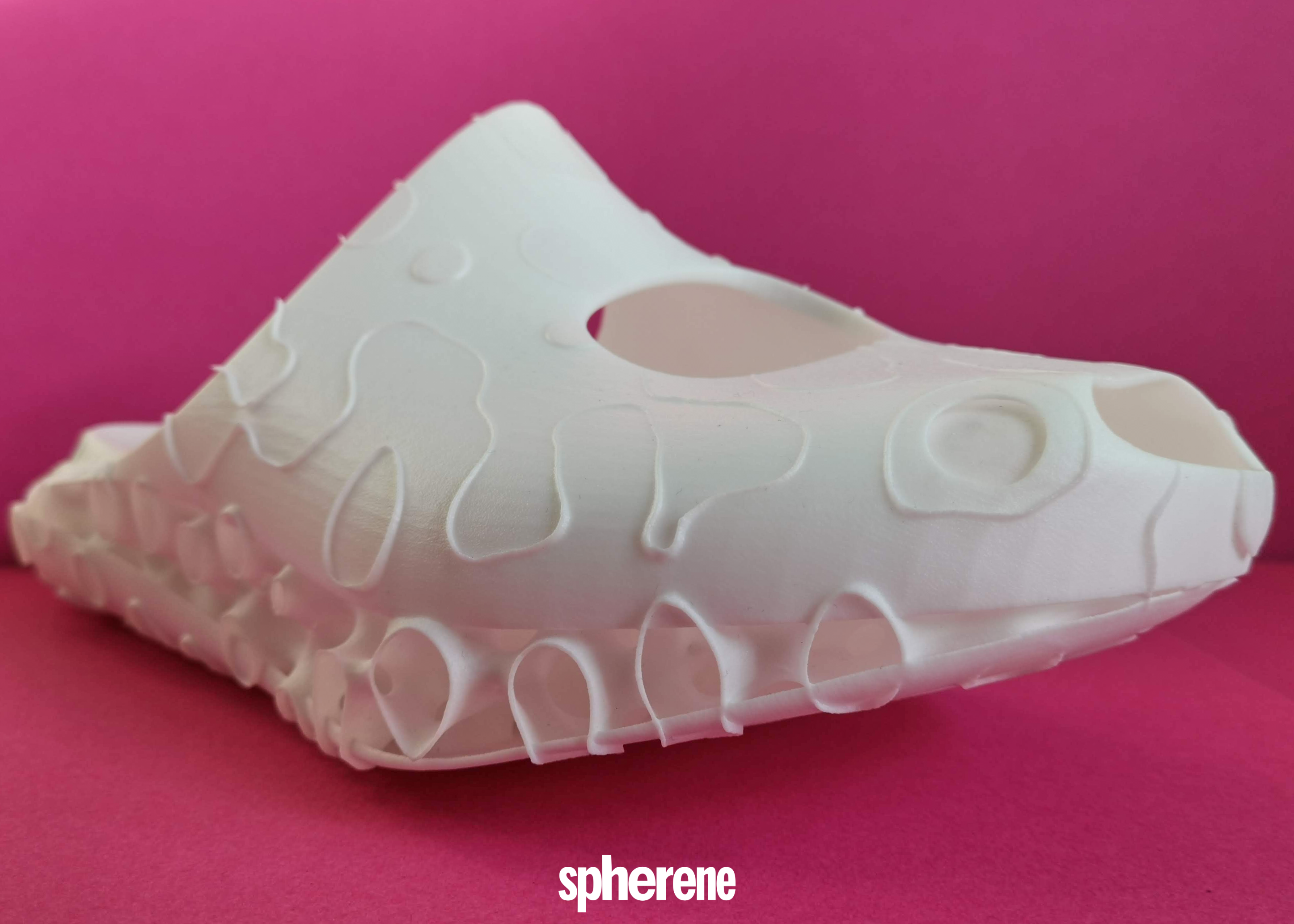
Further information about the implant can be found here.
The spherene metamaterial is set to become commercially available soon (around May), and will be available through the company’s network of resellers.
This dossier has first been published in the March – April 2024 edition of 3D ADEPT Mag.