From patient data to an end-use prosthetic device at Quorum Prosthetics
At 12, Joe Johnson lost his leg in a motorcycle accident. He faced initial challenges with a basic prosthetic until he discovered how AM could help produce a tailor-made and more comfortable 3D-printed prosthetic. Johnson’s story could have ended after he got his first prosthetic, but he didn’t see anyone willing to take the risks to help amputees. His journey therefore led him to found Quorum Prosthetics, a prosthetics company that makes prosthetic arms and legs, custom bracing, and the Quatro adjustable 3D printed sockets. Over time, the company has been continuously exploring the use of digital manufacturing technologies to give amputees the right fit. If we are talking about it today, that’s because Johnson’s experience allowed us to understand the digital manufacturing stages of 3D-printed patient-specific devices.
Quorum Prosthetics itself is a journey of resilience. We share its story today because “Additive Manufacturing is a vehicle to [its] ideas” – in the words of Johnson. However, in 1998, when the company was founded, it wasn’t. It took Johnson a lot of investment, energy and trust in engineering expertise to bring his company to where it is today – yes, because Johnson is not an engineer by training.
“I had this recipe 8 years ago of what I wanted Quorum to achieve. We wanted to standardize a good design for prosthetics as it was difficult to carefully replicate existing ones. [From conventional manufacturing techniques such as lamination resin and plaster, we took the leap to AM in 2019. Today, with a distributed manufacturing model, we can help amputees beyond our frontiers]”, the founder adds.
On a more practical note, it’s important to understand that regaining mobility hinges on having a prosthetic device that is both functional and properly fitted. A conventional manufacturing process would require the use of a plaster cast customized for the patient and lamination using carbon and resin. “The problem is, even though the final socket is comfortable, the manufacturing process is inaccurate for replication”, Johnson told 3D ADEPT Media. Not to mention that the shape and volume could change over time, causing a sort of pressure or discomfort on the wearer.
The Quatro socket from Quorum Prosthetics is based on a patented design that enables wearers to adapt the volume and compression using adjustable reels and interchangeable comfort cells. The truth is the process to get there demands a meticulous and comprehensive digital workflow. Commenting on the development of such patient-specific devices in the realm of prosthetics and orthotics, Johnson explains that each step of the digital workflow is “imperative to ensure the creation of prosthetic sockets, such as the Quatro socket, that seamlessly integrate with the patient’s anatomy, optimize comfort, and enhance functionality.”
What are these steps?
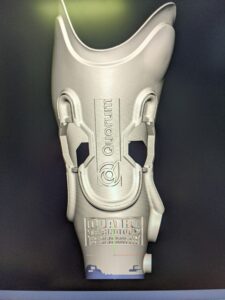
On a very technical level, the digital manufacturing stages can be gathered in 3 main steps:
- 3D scanning & digital model creation
- Print & process
- Patient fitting
At Quorum Prosthetics, the entire manufacturing process from patient assessment to outcome evaluation takes 10 steps. These steps include:
- Patient assessment: Any healthcare provider would agree with the fact that this step is obvious as it offers a better understanding of the patient’s specific needs and requirements, and helps to gather relevant medical data such as residual limb measurements, skin condition, and functional capabilities.
- 3D scanning: With this step one can capture the shape and contours of the residual limb accurately. In general, Computerized Tomography (CT) scans, Magnetic Resonance Imaging (MRI) scans, X-rays, and handheld 3D scanners can be utilized to capture the details of the patient’s anatomy. This digital representation becomes the foundation for the subsequent steps in the AM process.
Quorum uses an Artec 3D scanner to perform this task.
- Digital model creation: Thereafter, the designer uses a specific software solution to convert the 3D scan data into a digital model. Certain adjustments based on the patient’s anatomy can also be made at this stage.
-
Legend: Adjustments can be made with pinpoint accuracy. Credit: Quorum Prosthetics . Socket design: The level of sophistication in the design software is crucial here, as it dictates whether the process remains a manual craft or progresses toward partial or full automation. This digital modeling phase permits unparalleled precision, guaranteeing that the eventual prosthetic seamlessly conforms to the individual anatomy and requirements of the patient.
With the help of Geomagic Freeform, they can design the socket and integrate features such as pressure-relief areas, suspension mechanisms, and reinforcement. Johnson explained that they held a patent for the Quatro socket, which had precise design requirements, and Freeform was an ideal solution for meeting those requirements. Essentially, Freeform enables them to create custom-fitted sockets for individual patients, resulting in unique shapes for each. However, the standardized layout of adjustment lines and the entire Quatro system in Freeform streamline the design process, making it efficient and straightforward. Most importantly, through conventional methods, developing a socket design of this nature could require as much as 12 hours. Yet, the Quorum team can finalize a design in a fraction of the time, typically within four to six hours.
- Manufacturing preparation requires for instance to confirm that all digital models are within the boundaries of the print bed.
- Fabrication: Quorum relies on HP Multi-Jet Fusion to manufacture its sockets. Any other AM process could be assessed to ensure that the end part is biocompatible and that it delivers the ideal strength and weight. That being said, there are important differences at the geometry level when one compares a socket that is traditionally made and one that is fabricated with MJF. Other differences include connection points and thickness (Carbon fiber to have 6mm uniform thickness leveraging 4 layers of fiber weave and 2 bases of resin.)
-
Legend: The Quatro is strength-tested using ADAC’s metrology lab, ensuring a safe socket experience each time. Credit: Quorum Prosthetics Quality control: Beyond meeting quality standards and specifications, it’s about ensuring accuracy and comfort for the user. It should be noted that no official testing protocol exists to test socket performance. That’s why healthcare providers often rely on various testing methodologies. ISO 10328:2016 for instance specifies procedures for static and cyclic strength tests on lower limb prostheses which typically produce compound loadings by the application of a single test force. The compound loads in the test sample relate to the peak values of the components of loading which normally occur at different instants during the stance phase of walking.
- Assembly & customization: Aesthetics and functional requirements should be met at this level.
- Fitting and adjustment: After fitting the socket onto the patient’s residual limb, a couple of adjustments can still be made. When required, Quorum for instance adds comfort cells into the perforations of the flexible inner socket to provide the patient with more cushion.
- Outcome evaluation: throughout this process, the Quorum team follows up with the patient to assess the performance of the device in real-world scenarios.
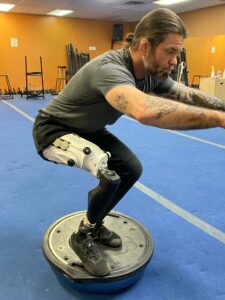
Concluding thoughts?
While healthcare providers might face labor shortages and size capacity when relying on AM, the advantages of using the technology for 3D printed prosthetics are those you might already be familiar with, if you know the technology: customization, improved comfort, reduced production time and cost-efficiency.
As a matter of fact, as regards the cost factor, Quorum’s adjustable sockets can now be covered by insurance companies under prosthetic volume adjustment.
As AM continues to evolve, it will continue to reshape the prosthetics landscape, offering newfound accessibility and improving the overall welfare of individuals in need. With more than 57.7 million people living with limb amputation due to traumatic causes worldwide, I hope to see more “Quorum Prosthetics” emerge across the world.
This article was initially published in the March/April edition of 3D ADEPT Mag.