The aerospace industry has always been mentioned as one of the early adopters of Additive Manufacturing. At the time (in the 2010s), being able to leverage plastic 3D printed parts for testing and simulation was already a huge achievement for aerospace companies. However, rising production needs around the world continuously impact the way the business of aerospace and defense is transacted globally. Furthermore, they lead to trade considerations that require new means of manufacturing to meet new demands of players in this sector.
Aerospace players such as Lockheed Martin, Airbus, Boeing, Northrop Grumman, and others who are at the forefront of commercial operations, may spearhead these demands, but the real heroes behind the scenes are often those who need to explore these new means of manufacturing in order to create aerospace components.
A conversation with Sintavia’s CEO Brian Neff highlights these various directions the commercial aerospace market is embracing as well as the new manufacturing strategies they require.
One of the mistakes we often make in this industry is that we consider any parts producer as a 3D printing service bureau. A 3D printing service bureau delivers its services to a wide range of industries adopting AM technologies. Yet, given its primary focus on aerospace and defense, I see Sintavia as a technology and producer partner to aerospace and defense companies.
With the founder & CEO’s roots in the aerospace industry, roots that include an extensive experience in the MRO and OEM manufacturing fields, it’s easy to understand that Sintavia seized the opportunity to build an offering that is vertically integrated with various demands within the aviation industry. Indeed, AM might be the most highlighted manufacturing process in Sintavia’s production, but to be good at this game, it’s crucial to have a solid understanding of metrology, metallurgy, machining, heat treatments, testing, etc.; in a nutshell, all sub-processes that may help you define a real manufacturing strategy around AM.
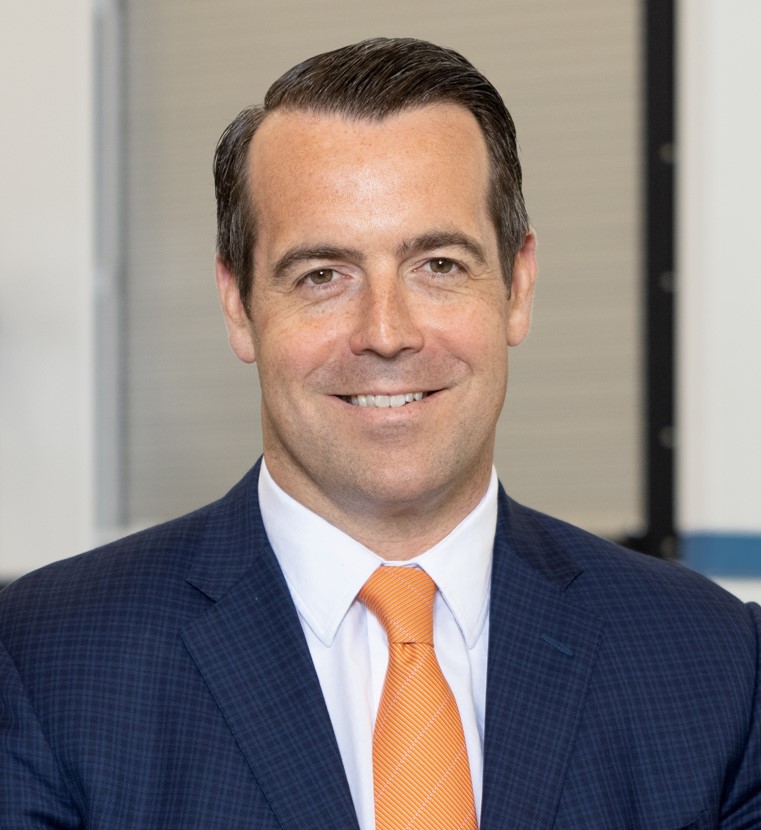
Manufacturing strategy
The Florida-based company was founded in 2015, an era that coincides with the first recognitions of AM’s potential within the aerospace industry. The thing is, despite these recognitions, the learning curve of AM was quite slow – and with good reason: companies needed to understand the ins-and-outs of the technology and this requires investment, a lot of investment.
With about 30 industrial printers in-house today, including multiple from GE Additive, TRUMPF and, obviously, EOS, including eight M400-4 quad laser printers, Sintavia decided very early to focus on “the very best way to leverage AM”.
This might seem crazy when we know that at the beginning, the aerospace AM market was not that advanced. The ROI for specific use cases of AM was not that clear.
“It can be frustrating, but to get there you have to invest in the void. It can be hard to do for some organizations because it requires a lot of money, time and dedication to see value and that’s a risk many do not want to take. When we first started, we acquired a number of different machines from various OEMs. It is essential to any company diving into this business to understand the technology and that’s what we were trying to do: understand the technology and gain a lot of hands-on experience. As time has developed, we have been able to identify which areas for which machines are the best. These 3D printers are tools we have to leverage for specific purposes and each of the various 3D printers we acquired brings a unique strength for specific areas. These areas involve for instance, the alloys that we use, the size and dimension of the parts we manufacture, the use cases of the component for manufacturing…for instance, we can meet the needs of those who want tall parts with the AMCM M4K-4 systems, we produce very good Titanium small parts on Arcam machines. In a nutshell, we try to make sure that we can meet all the different needs of our customers. Once we saw the benefits of printing very complex systems via DfAM, we said we wanted to focus on the hardest geometries possible, and it was a very smart choice. Achieving and focusing on the most complex applications is what enables us to leverage the best of these technologies”, Neff explains.
That being said, Powder-Bed Fusion (PBF-LB) remains the most widely used process in Sintavia’s portfolio.
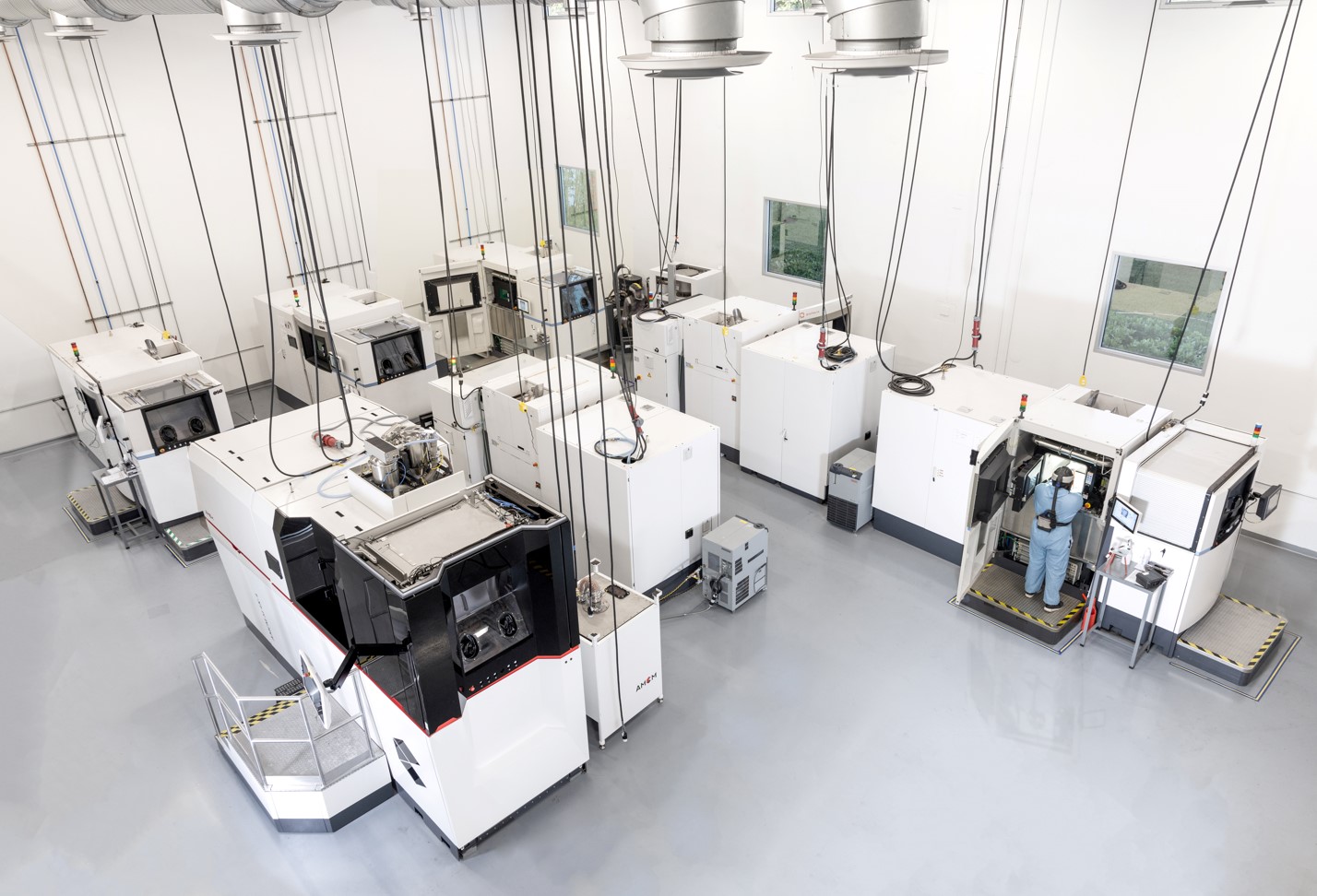
Powder-Bed Fusion yes, but an eye on other AM processes
From a regulations standpoint, the increasing use of this manufacturing process makes sense when we know that due to the conservative nature of the aerospace industry, it might now be easy to qualify parts manufactured with this technology. Remember, in January 2021, the ISO TC261 and the ASTM International committee F42 introduced a new standard which provides AM companies with qualification requirements for laser beam powder bed fusion (PBF-LB) in the aerospace industry. This standard aims to improve the ability for additively manufactured metal components to qualify for commercial, military, and civil aircrafts, as well as space flight and space propulsion.
From a manufacturing standpoint, PBF-LB would provide greater benefits for aerospace parts than other metal 3D printing processes. “The reason comes down to materials properties. In every type of manufacturing, you have to show a level of quality, and this requirement is even more stringent in aerospace manufacturing. On the other hand, it should be noted that the rigours of flying and landing can be hard in this industry because many errors could occur. Powder-bed fusion is a very sturdy type of technology that can deliver strong and durable components. The robustness of the process is demonstrated through lab analysis, microstructures, and mechanical testing. [PBF-LB] enhances a specific part, and we can demonstrate that this 3D printed part is stronger than its counterpart made via traditional manufacturing”, the expert outlines.
As AM processes use to be compared to traditional manufacturing processes, Neff draws attention to the fact that engineers should not compare PBF-LB to freeform welding. “This is not freeform welding. Freeform welding presents some weaknesses that aerospace manufacturing cannot withstand—similar to investment casting which has production variations that aerospace manufacturing does not like. At Sintavia, we use digital molds instead of physical ones and they deliver a totally repeatable process”, he adds.
Apart from the potential of PBF-LB, Sintavia’s team will keep an open mind regarding other AM processes that may deliver a significant difference in the manufacturing of aerospace parts. These manufacturing processes include for example, DED for its versatility of use and ability to deliver multi-material parts and WAAM, “which is still very underestimated, yet is interesting for some rocket applications and large structural applications”.
Investing efforts to develop the right materials parameters for the right processes
On the other hand, the “materials properties” argument goes even further as the development rate of AM depends a lot on materials. The reality is, aerospace parts producers acquired more experience on polymers (plastics) than metals because AM was first developed for polymers. However, the original structure of the aircraft makes it possible to maximize gains with metal AM, if well leveraged. These arguments lead all stakeholders involved in the aerospace industry, including parts producers to invest significant efforts to develop powders that best meet the parameters of the 3D printers they use.
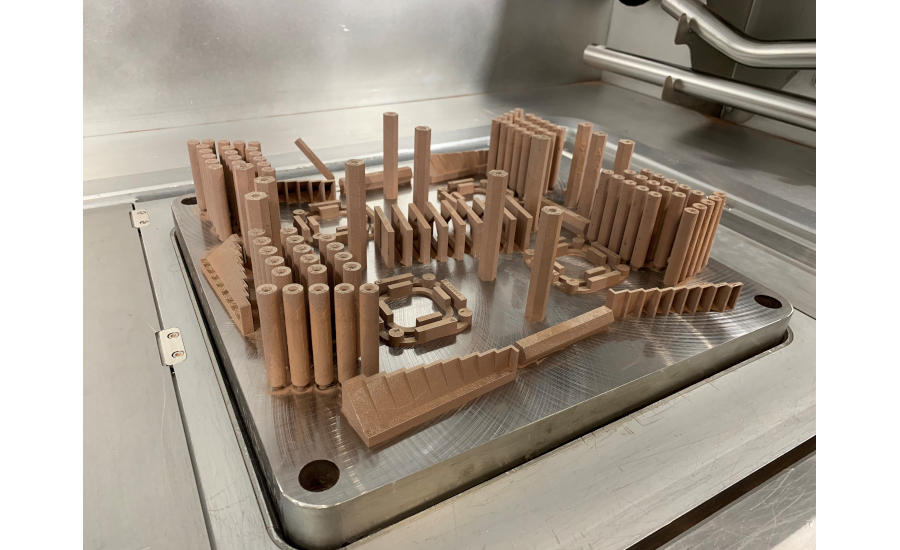
Sintavia was no exception to this rule as the company made a real splash last year with the development of a proprietary printing technology for GRCop-42, a material described as the preferred copper alloy used by NASA and private space flight companies for rocket thrust chamber assemblies.
As a reminder, the new technology is a combination of a proprietary parameter set and post-processing heat treatment. It was developed on an EOS GmbH M400-4 printer, and results in GRCop-42 components with minimum density of 99.94%, minimum tensile strength of 28.3 ksi, minimum ultimate yield strength of 52.7 ksi, and minimum elongation of 32.4%. More importantly, the technology avoids the use of a hot isostatic press in post-processing steps, thereby reducing the time, complexity, and cost of production.
The proprietary printing technology for this material is just one of many examples of properties Sintavia has developed over the years. While Neff clarifies that, they have no intention to become a powders’ producer, the ability to address the reflectivity and high thermal conductivity challenges raised by copper is a milestone the entire team was very proud to achieve.
“You have to develop your own printing parameters if you want to have the best chance to succeed. We have already developed nearly 30 proprietary material parameters. We usually don’t announce each set of parameters we develop for specific powders but copper being a unique material, we were very proud of what we achieved with this material. Other developments (with refractory powders) are in progress and will be announced soon”, the CEO comments.
Current routes the commercial aerospace market is embracing
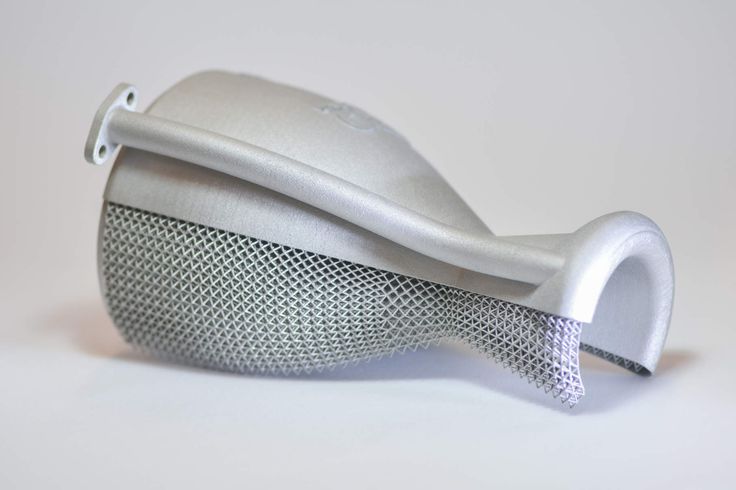
You’ve certainly heard me say this a lot, and I will reiterate it: investing in materials and processes is good, but these investments might be ineffective if they are not supported by current demands in the market you target. Surprisingly, for an industry that is described as very conservative, the aerospace market is opening up to more ambitious sub-segments that are perhaps worthy of AM's potential.
“My expertise has always kept me to more traditional aerospace applications. There has been a lot of mini-markets that have been developing lately. Three of them currently stand out from the crowd: private space launches, hypersonic flight and electric commercial flights. When I started the company in 2015, I couldn’t imagine it would explore the path to private launches”, Neff shares.
For Sintavia’s representative, the common thread to these routes is DfAM. “From a commercial standpoint, the adoption of AM in the commercial space industry urges the commercial aerospace industry to accelerate its adoption of AM – which is great to see. Moreover, there is a freedom of design when you are using AM for complex parts. In each of these paths, aerospace players are given the opportunity to create something new, something they have never done before, and AM is now giving them a myriad of possibilities to explore this potential”, he adds.
Neff’s explanations reveal that there is something appealing in rocket applications made possible via AM and the future of these applications is likely to be even more exciting. In the meantime, Sintavia’s manufacturing investments help meet the demand of customers who are looking to create advanced propulsion systems, combustion chambers for space launches, (…), optimise regenerative cooling passages and, as a result, reduce lead times and complexity.
The commercial aerospace market is really a big market. Several players are trying to find their marks here and differentiate themselves from the crowd, but I believe Sintavia is doing so as they find value in looking beyond what they can achieve today.
This exclusive feature has first been published in the January/February issue of 3D ADEPT Mag.
Remember, you can post job opportunities in the AM Industry on 3D ADEPT Media free of charge or look for a job via our job board. Make sure to follow us on our social networks and subscribe to our weekly newsletter : Facebook, Twitter, LinkedIn & Instagram ! If you want to be featured in the next issue of our digital magazine or if you hear a story that needs to be heard, make sure to send it to contact@3dadept.com