Stratasys has recently announced that UPSA, a French pharmaceuticals company, will be transforming its manufacturing process by incorporating Stratsys’ 3D printer StratasysFortus 450mc™ Production.
Stratasys continues to better itself within the 3D printing industry. Whether it be through aiding the digital industry with new 3D systems or customizing 3D printed racing sleds for the 2018 Winter Games, Stratasys continues to make itself known within the 3D printing market. Stratasys is a company specialising in additive technology for various sectors such as healthcare, consumer products and education and aerospace. President of Stratasys, Andy Middleton, explains that there is quite an “increase for the demand of 3D printing and various production and replacements parts for industrial machinery.”
According to company owner Bristol-Myers Squibb, UPSA aims to “attract the next generation of technicians” by integrating 3D printing within its in-house workshop. This addition is an important step to UPSA. Project Manager, Mathieu Dumora explains, “We identified 3D printing as a possible solution to our needs and made an estimate of all the parts we could 3D print to see if we could save manufacturing costs and reduce our stock of parts.” 3D printing will have a great impact on the company’s productivity and its part weight would be reduced by 70%.
StratasysFortus 450mc™ Production
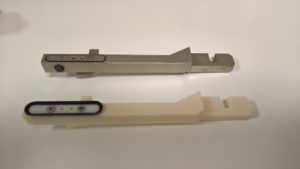
The printer is said to be much safer than the current print machine being used by UPSA. The company currently has a machine with a steel arm that can easily break, but with the 3D printed arm it is safer and if it breaks it would be at a minimal cost and replacing it won’t take much time. The printer will also be used to improve the closure of the Efferalgan caps for children as they’ve realised that some capsules contained particles which could potentially contaminate the medication. Additive manufacturing has given UPSA the capabilities to develop a system that removes these particles from the capsules.
StratasysFortus 450mc™ Production 3D Printer is also a time saver for UPSA. A track-and-trace code has been added to each packaging, and to ensure proper printing, cameras have been placed on each package. The printer is able to print 22 units, but before this integration, 27 units were needed. Production time and cost were significantly reduced.
Additive manufacturing continues to quickly become cost-effective for companies and manages to transform production-line challenges.
For further information about 3D Printing, follow us on our social networks and subscribe to our newsletter!
Would you like to be featured in the next issue of our digital magazine?
Send us an email at contact@3dadept.com