L'industrie aérospatiale a toujours été mentionnée comme l'un des premiers adeptes de la fabrication additive. À l'époque (dans les années 2010), être en mesure de tirer parti de pièces plastiques imprimées en 3D pour les essais et la simulation était déjà une grande réussite pour les entreprises aérospatiales. Cependant, l'augmentation des besoins de production dans le monde entier a un impact continu sur la façon dont les affaires de l'aérospatiale et de la défense sont traitées à l'échelle mondiale. En outre, ils conduisent à des considérations commerciales qui nécessitent de nouveaux moyens de fabrication pour répondre aux nouvelles demandes des acteurs de ce secteur.
Les acteurs de l'aérospatiale tels que Lockheed Martin, Airbus, Boeing, Northrop Grumman et d'autres, qui sont à l'avant-garde des opérations commerciales, peuvent être le fer de lance de ces demandes, mais les véritables héros dans les coulisses sont souvent ceux qui doivent explorer ces nouveaux moyens de fabrication afin de créer des composants aérospatiaux.
Une conversation avec Brian Neff, CEO de Sintavia, met en lumière les différentes orientations que prend le marché de l'aérospatiale commerciale ainsi que les nouvelles stratégies de fabrication qu'il requiert.
L'une des erreurs que nous commettons souvent dans ce secteur est de considérer tout fabricant de pièces comme un bureau de services d'impression 3D. Un bureau de services d'impression 3D fournit ses services à un large éventail d'industries adoptant les technologies de FA. Pourtant, étant donné son orientation principale vers l'aérospatiale et la défense, je vois Sintavia comme un producteur et partenaire technologique des entreprises de l'aérospatiale et de la défense.
Avec les racines du fondateur et CEO dans l'industrie aérospatiale, racines qui incluent une expérience étendue dans les domaines de la fabrication MRO et chez des OEMs, il est facile de comprendre que Sintavia a saisi l'opportunité de construire une offre qui est verticalement intégrée avec les diverses demandes de l'industrie aéronautique. En effet, la FA est peut-être le processus de fabrication le plus mis en avant dans la production de Sintavia, mais pour être bon à ce jeu, il est crucial d'avoir une solide compréhension de la métrologie, de la métallurgie, de l'usinage, des traitements thermiques, des tests, etc. ; en bref, tous les sous-processus qui peuvent vous aider à définir une véritable stratégie de fabrication autour de la FA.
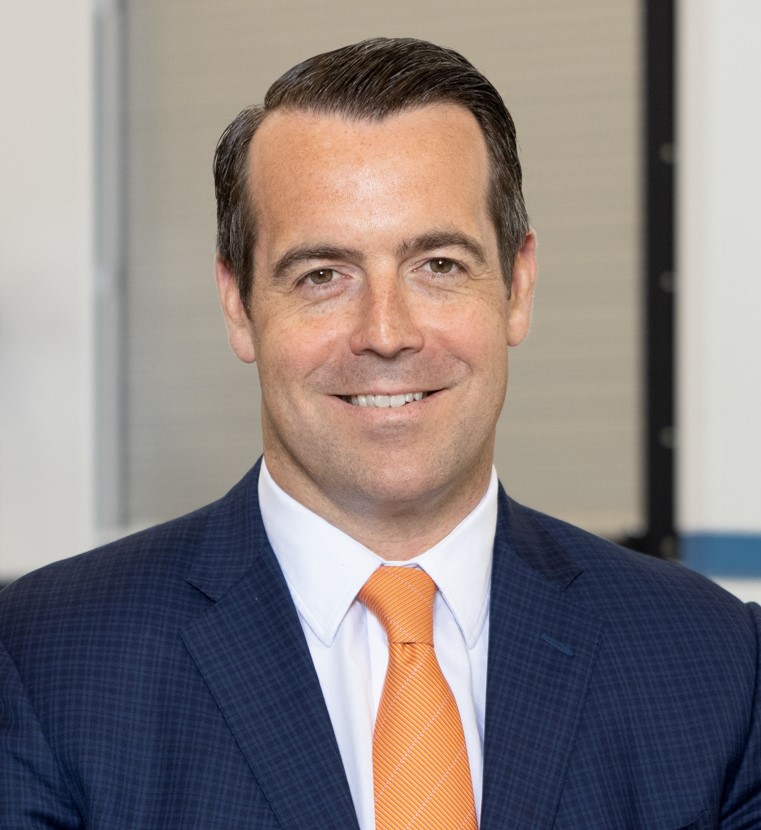
Stratégies de fabrication
L'entreprise basée en Floride a été fondée en 2015, une époque qui coïncide avec les premières reconnaissances du potentiel de la FA au sein de l'industrie aérospatiale. Le fait est que, malgré ces reconnaissances, la courbe d'apprentissage de la FA était assez lente – avec raison : les entreprises avaient besoin de comprendre les tenants et aboutissants de la technologie et cela nécessite des investissements, beaucoup d'investissements.
Avec environ 30 imprimantes industrielles en interne aujourd'hui, dont plusieurs de GE Additive, TRUMPF et, évidemment, EOS, y compris huit imprimantes laser quadruple M400-4, Sintavia a décidé très tôt de se concentrer sur « la meilleure façon de tirer son épingle du jeu. »
Cela peut sembler fou quand on sait qu'au début, le marché de la FA dans l'aérospatiale n'était pas très avancé. Le retour sur investissement pour des cas d'utilisation spécifiques de la FA n'était pas très clair.
« Cela peut être frustrant, mais pour y arriver, il faut investir dans le vide. Cela peut être difficile à faire pour certaines organisations, car il faut beaucoup d'argent, de temps et de dévouement pour en voir la valeur, et c'est un risque que beaucoup ne veulent pas prendre. Lorsque nous avons commencé, nous avons acquis un certain nombre de machines différentes auprès de divers équipementiers. Il est essentiel pour toute entreprise qui se lance dans ce secteur de comprendre la technologie et c'est ce que nous avons essayé de faire : comprendre la technologie et acquérir une grande expérience pratique. Au fil du temps, nous avons été en mesure d'identifier les domaines pour lesquels les machines sont les meilleures. Ces imprimantes 3D sont des outils que nous devons exploiter à des fins spécifiques et chacune des différentes imprimantes 3D que nous avons acquises apporte une force unique pour des domaines spécifiques. Ces domaines concernent par exemple les alliages que nous utilisons, la taille et la dimension des pièces que nous fabriquons, les cas d'utilisation du composant pour la fabrication… par exemple, nous pouvons répondre aux besoins de ceux qui veulent des pièces hautes avec les systèmes AMCM M4K-4, nous produisons de très bonnes petites pièces en titane sur les machines Arcam. En bref, nous essayons de nous assurer que nous pouvons répondre à tous les différents besoins de nos clients. Lorsque nous avons vu les avantages de l'impression de systèmes très complexes via DfAM, nous avons décidé de nous concentrer sur les géométries les plus difficiles possibles, et ce fut un choix très judicieux. Réaliser et se concentrer sur les applications les plus complexes est ce qui nous permet de tirer le meilleur parti de ces technologies », explique Neff.
Cela dit, la fusion sur lit de poudre (PBF-LB) reste le procédé le plus utilisé dans le portefeuille de Sintavia.
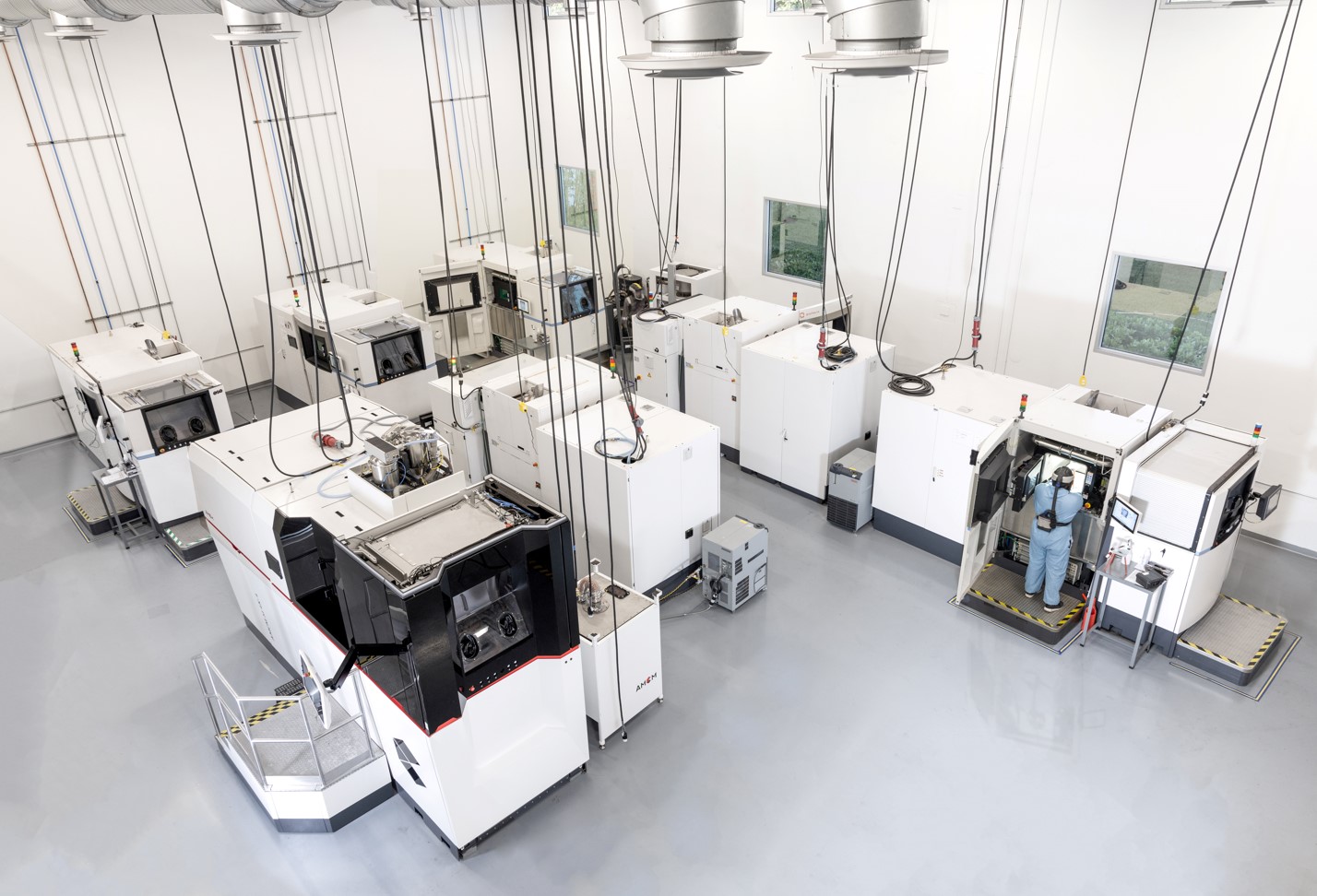
La fusion sur lit de poudre, oui, mais un œil sur les autres procédés de FA
D'un point de vue réglementaire, l'utilisation croissante de ce procédé de fabrication est logique quand on sait qu'en raison de la nature conservatrice de l'industrie aérospatiale, il pourrait désormais être facile de qualifier les pièces fabriquées avec cette technologie. Rappelons qu'en janvier 2021, l'ISO TC261 et le comité international F42 de l'ASTM ont introduit une nouvelle norme qui fournit aux entreprises de la FA des exigences de qualification pour la fusion sur lit de poudre par faisceau laser (PBF-LB) dans l'industrie aérospatiale. Cette norme vise à améliorer la capacité des composants métalliques fabriqués de manière additive à se qualifier pour les aéronefs commerciaux, militaires et civils, ainsi que pour les vols spatiaux et la propulsion spatiale.
Du point de vue de la fabrication, le PBF-LB offrirait de plus grands avantages pour les pièces aérospatiales que les autres procédés d'impression 3D de métaux. « La raison se résume aux propriétés des matériaux. Dans tout type de fabrication, vous devez faire preuve d'un certain niveau de qualité, et cette exigence est encore plus stricte dans la fabrication aérospatiale. D'autre part, il faut savoir que les rigueurs du vol et de l'atterrissage peuvent être difficiles dans cette industrie, car de nombreuses erreurs peuvent se produire. La fusion sur lit de poudre est un type de technologie très robuste qui permet d'obtenir des composants solides et durables. La robustesse du processus est démontrée par des analyses en laboratoire, des microstructures et des essais mécaniques. La [PBF-LB] améliore une pièce spécifique, et nous pouvons démontrer que cette pièce imprimée en 3D est plus solide que son homologue fabriquée de manière traditionnelle », souligne l'expert.
Étant donné que les procédés de FA sont comparés aux procédés de fabrication traditionnels, Neff attire l'attention sur le fait que les ingénieurs ne doivent pas comparer le procédé PBF-LB au soudage en forme libre. « Il ne s'agit pas de soudage en forme libre. Le soudage en forme libre présente certaines faiblesses que la fabrication aérospatiale ne peut pas supporter – tout comme le moulage à la cire perdue qui présente des variations de production que la fabrication aérospatiale n'aime pas. Chez Sintavia, nous utilisons des moules numériques au lieu de moules physiques, ce qui permet d'obtenir un processus totalement répétable », ajoute-t-il.
Outre le potentiel du PBF-LB, l'équipe de Sintavia reste ouverte à d'autres procédés de FA susceptibles de faire une différence significative dans la fabrication de pièces aérospatiales. Ces procédés de fabrication comprennent par exemple le DED pour sa polyvalence d'utilisation et sa capacité à fournir des pièces multi-matériaux et le WAAM, « qui est encore très sous-estimé, mais qui est intéressant pour certaines applications de fusées et de grandes applications structurelles ».
Investir des efforts pour développer les bons paramètres de matériaux pour les bons processus
D'autre part, l'argument des "propriétés des matériaux" va encore plus loin car le taux de développement de la FA dépend beaucoup de ceux-ci. En réalité, les producteurs de pièces aérospatiales ont acquis plus d'expérience sur les polymères (plastiques) que sur les métaux, car la FA a d'abord été développée pour les polymères. Cependant, la structure originale de l'avion permet de maximiser les gains avec la FA métal, si elle est bien exploitée. Ces arguments conduisent tous les acteurs impliqués dans l'industrie aérospatiale, y compris les producteurs de pièces, à investir des efforts importants pour développer des poudres qui répondent au mieux aux paramètres des imprimantes 3D qu'ils utilisent.
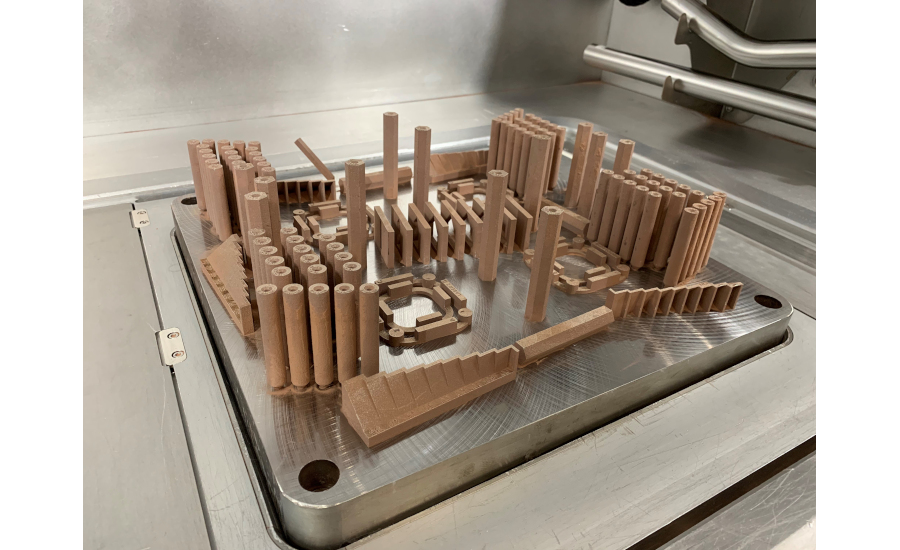
Sintavia n'a pas fait exception à la règle, puisque la société a fait fureur l'année dernière en développant une technologie d'impression propriétaire pour le GRCop-42, un matériau décrit comme l'alliage de cuivre préféré utilisé par la NASA et les compagnies privées de vol spatial pour les assemblages de chambres de poussée des fusées.
Pour rappel, la nouvelle technologie est une combinaison d'un ensemble de paramètres exclusifs et d'un traitement thermique post-traitement. Elle a été développée sur une imprimante EOS GmbH M400-4, et permet d'obtenir des composants GRCop-42 présentant une densité minimale de 99,94 %, une résistance à la traction minimale de 28,3 ksi, une limite d'élasticité minimale de 52,7 ksi et un allongement minimal de 32,4 %. Plus important encore, cette technologie évite l'utilisation d'une presse isostatique à chaud dans les étapes de post-traitement, réduisant ainsi le temps, la complexité et le coût de production.
La technologie d'impression exclusive de ce matériau n'est qu'un des nombreux exemples de propriétés que Sintavia a développées au fil des ans. Même si Neff précise que l'entreprise n'a aucunement l'intention de devenir un producteur de poudres, la capacité de relever les défis posés par la réflectivité et la haute conductivité thermique du cuivre est une étape importante que toute l'équipe est très fière d'avoir franchie.
« Vous devez développer vos propres paramètres d'impression si vous voulez avoir les meilleures chances de réussir. Nous avons déjà développé près de 30 paramètres de matériaux exclusifs. Nous n'annonçons généralement pas chaque ensemble de paramètres que nous développons pour des poudres spécifiques, mais le cuivre étant un matériau unique, nous étions très fiers de ce que nous avons réalisé avec ce matériau. D'autres développements (avec des poudres réfractaires) sont en cours et seront annoncés prochainement », commente le PDG.
Voies actuelles empruntées par le marché de l'aérospatiale commerciale
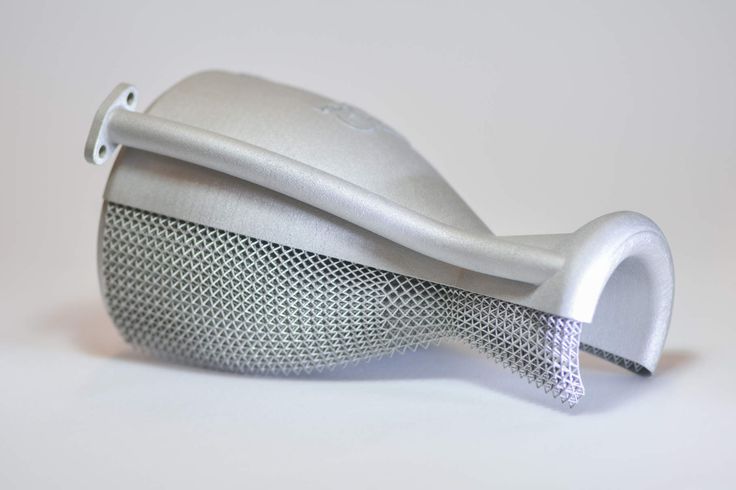
Vous m'avez certainement entendu le dire souvent, et je vais le répéter : investir dans les matériaux et les processus est une bonne chose, mais ces investissements peuvent être inefficaces s'ils ne sont pas soutenus par les demandes actuelles du marché que vous ciblez. Étonnamment, pour une industrie que l'on décrit comme très conservatrice, le marché de l'aérospatiale s'ouvre à des sous-segments plus ambitieux qui sont peut-être à la hauteur du potentiel de la FA.
« Mon expertise m'a toujours cantonné à des applications aérospatiales plus traditionnelles. De nombreux mini-marchés se sont développés ces derniers temps. Trois d'entre eux sortent actuellement du lot : les lancements spatiaux privés, les vols hypersoniques et les vols commerciaux électriques. Lorsque j'ai lancé l'entreprise en 2015, je ne pouvais pas imaginer qu'elle explorerait la voie des lancements privés », partage Neff.
Pour le représentant de Sintavia, le fil conducteur de ces voies est le DfAM (Design for Additive Manufacturing »). « D'un point de vue commercial, l'adoption de la FA dans l'industrie spatiale commerciale pousse l'industrie aérospatiale commerciale à accélérer son adoption de la FA – ce qui est formidable à voir. De plus, il y a une liberté de conception lorsque l'on utilise la FA pour des pièces complexes. Dans chacune de ces voies, les acteurs de l'aérospatiale ont la possibilité de créer quelque chose de nouveau, quelque chose qu'ils n'ont jamais fait auparavant, et la FA leur offre désormais une myriade de possibilités pour explorer ce potentiel », ajoute-t-il.
Les explications de Neff révèlent qu'il y a quelque chose d'attrayant dans les applications de fusées rendues possibles par la FA et l'avenir de ces applications est susceptible d'être encore plus passionnant. En attendant, les investissements de fabrication de Sintavia permettent de répondre à la demande des clients qui cherchent à créer des systèmes de propulsion avancés, des chambres de combustion pour les lancements spatiaux, (…), à optimiser les passages de refroidissement régénératifs et, par conséquent, à réduire les délais et la complexité.
Le marché de l'aérospatiale commerciale est vraiment un grand marché. Plusieurs acteurs tentent d'y trouver leurs marques et de se différencier, mais je crois que Sintavia y parvient car elle trouve de la valeur à regarder au-delà de ce qu'elle peut réaliser aujourd'hui.
Ce dossier exclusif a été publié initialement dans le numéro de Janvier/Février de 3D ADEPT Mag.
N’oubliez pas que vous pouvez poster gratuitement les offres d’emploi de l’industrie de la FA sur 3D ADEPT Media ou rechercher un emploi via notre tableau d’offres d’emploi. N’hésitez pas à nous suivre sur nos réseaux sociaux et à vous inscrire à notre newsletter hebdomadaire : Facebook, Twitter, LinkedIn & Instagram ! Si vous avez une innovation à partager pour le prochain numéro de notre magazine numérique ou si vous avez un article à faire connaître, n’hésitez pas à nous envoyer un email à contact@3dadept.com.