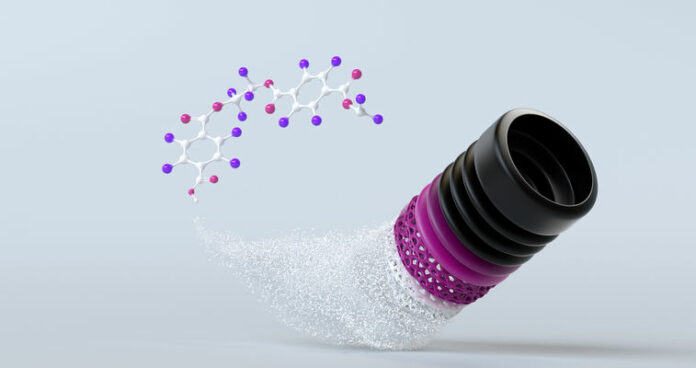
Le temps que j’ai déjà passé dans cette industrie m’a fait comprendre que la puissance d’un procédé de fabrication additive réside dans sa capacité à transformer un matériau. C’est en tout cas ce qui est généralement démontré dans presque toutes les applications mises en avant dans les différentes industries. Aujourd’hui, avec la popularité croissante de l’impression 3D pour la fabrication de toutes sortes d’articles, les producteurs de matériaux ont beaucoup de travail à faire car ils doivent faire face aux nouvelles tendances de l’industrie, à la qualification et à la certification. Nous avons rencontré le Dr Dominic Stoerkle, responsable de l’innovation dans le domaine de la croissance de la fabrication additive chez Evonik, pour discuter du développement des matériaux en fonction de ces enjeux et de leur interaction avec les applications de l’impression 3D automobile.
Plus la FA est sollicitée pour favoriser l’industrie 4.0, plus elle soulève des débats sur la façon dont les produits sont fabriqués. Dans notre industrie encore en pleine maturation, la technologie est de plus en plus porteuse de promesses d’avantages écologiques.
Par exemple, au niveau de la production, des incitants sociaux, économiques et environnementales poussent à la fabrication additive avec des matières premières locales sans avoir recours à l’usinage et à de nombreuses étapes. Au niveau du dispositif, l’objet nouvellement fabriqué offre de nouvelles propriétés et des fonctionnalités optimisées et, au niveau du matériau, l’accent est mis sur l’utilisation de la FA avec une production de déchets réduite.
Le fait est que ces avantages semblent être la voie idéale pour ceux qui fabriquent localement des produits destinés aux utilisateurs finaux. Au niveau industriel, nous sommes encore loin d’un monde idéal étant donné les différents éléments à prendre en compte. C’est en tout cas ce sur quoi le Dr Dominic Stoerkle d’Evonik attire notre attention :
« La durabilité est l’élément central pour réussir à l’avenir. Outre d’autres facteurs, tels que l’efficacité de la production ou la réutilisation des matériaux, les matières premières durables constituent également un élément important pour la fabrication additive, qui est en passe de devenir une technologie de production à l’échelle industrielle. Cependant, il est important de considérer les matières premières durables sous différents angles. Nous sélectionnons les matières premières sur la base d’une analyse complète du cycle de vie prenant en compte les réductions de dioxyde de carbone ainsi que d’autres facteurs importants tels que la consommation d’eau et l’utilisation des sols. Chez Evonik, nous suivons l’approche eCO-line : Nous travaillons avec nos chaînes de valeur pour remplacer les matières premières fossiles par des matières premières renouvelables et circulaires, comme les pneus en fin de vie, et nous utilisons des énergies renouvelables pour la production. De cette façon, l’écobilan global de nos produits peut être amélioré de manière significative le long de procédures certifiées en externe sans modifier les profils de propriétés des matériaux. »
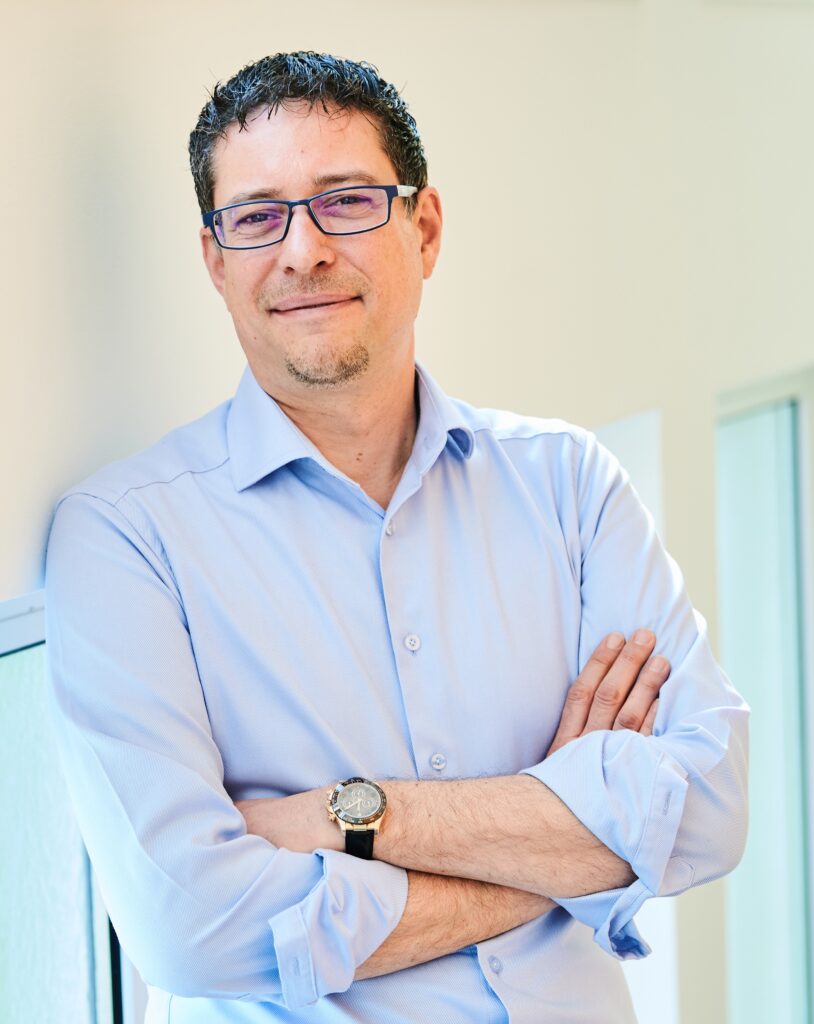
Si vous êtes un lecteur régulier de 3D ADEPT Media, vous connaissez peut-être déjà le monde des « applications infinies de l’impression 3D » que permet Evonik. L’entreprise allemande de produits chimiques spécialisés se taille continuellement une place importante dans l’industrie de la FA grâce à sa marque INFINAM® et aux investissements réalisés par sa société de capital-risque dans le secteur, Evonik Venture.
Alors que certaines des incitations susmentionnées sont prises en compte dans l’industrie automobile pour la fabrication de pièces métalliques imprimées en 3D, l’exploitation des ressources apportées par le monde des plastiques avec la FA pourrait ouvrir un nouveau champ de possibilités pour les composants automobiles. Mais c’est un autre sujet, que nous aborderons, je l’espère, dans un autre article.
Cela dit, il existe un large éventail de plastiques imprimés en 3D utilisés pour les composants automobiles. En fait, les plastiques restent les matériaux les plus utilisés dans la FA automobile. Que ce soit pour les avantages de la pré-production, la personnalisation ou l’outillage, les avantages en termes de coûts, de temps et de propriétés mécaniques des pièces méritent d’être explorés.
Actuellement, trois méthodes courantes d’impression 3D de plastiques ont gagné en popularité dans l’industrie : le frittage sélectif de couches (SLS)/la fusion laser sur lit de poudre (LPBF), le dépôt de filaments fondus (FDM) et l’impression 3D résine.
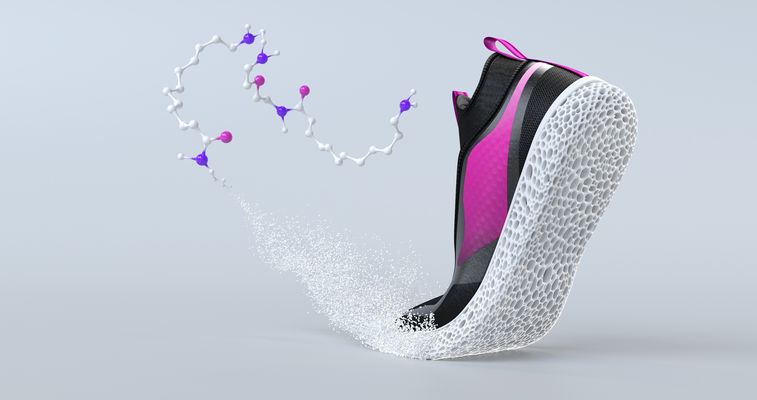
Pourquoi s’intéresser aux matériaux plastiques pour les applications automobiles ?
Ce n’est un secret pour personne que les composants mécaniques sont souvent soumis à de fortes contraintes, à des températures élevées et à un environnement corrosif, ce qui peut conduire à leur défaillance. L’intérêt pour les matériaux plastiques à haute performance prend naturellement de l’ampleur car ils peuvent répondre aux exigences de légèreté et offrir de meilleures propriétés dans les applications automobiles.
Selon une étude sur les matériaux polymères pour les applications automobiles, une grande variété de plastiques est utilisée dans les véhicules. Les fonctions de base de cette large utilisation de matériaux plastiques haute performance dans les véhicules dictent l’apparence des automobiles, leur fonctionnalité, leur économie et leur faible consommation de carburant. L’application de matériaux polymères permet une plus grande liberté de conception et environ 82 % du poids d’un véhicule moyen est recyclé. C’est, à notre avis, un élément dont la FA devrait tirer parti.
Il est intéressant de noter que si on considère les procédés de FA les plus utilisés mentionnés ci-dessus, Evonik a acquis une grande expertise dans le développement de matériaux de FA automobile pour toutes ces technologies.
« Nos matériaux polymères sont utilisés dans la fabrication additive depuis plus de 25 ans ; nous offrons à la fois la plus large gamme de technologies pour produire des poudres et une très large gamme de plateformes chimiques pour concevoir des photopolymères », souligne le représentant de la société.
L’entreprise explique que ses poudres de polyamide 12, qui ont fait leurs preuves, sont bien adaptées à la production fiable et reproductible d’un grand nombre de pièces en plastique. « Avec le polyamide 613, un matériau en poudre rigide et ductile avec une température de déflexion thermique plus élevée, nous proposons un polymère alternatif optimisé pour tous les défis des applications automobiles – avec une aussi bonne aptitude au traitement dans les imprimantes à fusion à lit de poudre que notre polyamide 12. Pour les applications qui exigent une résistance aux températures élevées et aux produits chimiques, notre filament PEEK pour la technologie FDM est le matériau de choix. En ce qui concerne nos produits photopolymères, je tiens à mentionner la résine haute résistance INFINAM® ST 6100 L, qui ressemble à du nylon chargé de verre, et INFINAM® RG 3101 L, un matériau semblable à l’ABS. Tous deux présentent des performances thermomécaniques durables et peuvent être utilisés à plus de 70°C, le matériau ST à plus de 120°C, ce qui est obligatoire pour les applications automobiles. En outre, nous avons lancé INFINAM® FL 6300 L en collaboration avec la société autrichienne Cubicure, un photopolymère élastomère à base de polyester présentant une durabilité et un comportement à la fatigue inédits », note Stoerkle.
En ce qui concerne les applications que ces matériaux peuvent susciter, le responsable du domaine de croissance de l’innovation en matière de fabrication additive explique que la variété des applications dépend directement des propriétés des matériaux mentionnés. Des composants non visibles sans exigences de sécurité peuvent être imprimés en 3D à partir de polyamide 12, de même que des couvercles et des grilles pour la climatisation, pour lesquels on dispose déjà d’une grande connaissance du post-traitement de la surface. Pour des applications plus avancées, les poudres de polyamide 613, dont la température de déflexion thermique est plus élevée, conviennent. Notre résine élastomère INFINAM® FL 6300 L, récemment introduite, est le matériau idéal pour les applications de mouillage et les supports de câbles, tandis que la résine à haute résistance INFINAM® ST 6100 L peut être utilisée pour les connecteurs et les clips.
Si on regarde à plus grande échelle, l’un des objectifs immédiats des constructeurs automobiles est d’accélérer l’électrification des véhicules électriques. On estime actuellement que 230 millions de véhicules électriques seront vendus dans le monde d’ici 2030. Si la promotion croissante de l’électrification est en partie motivée par les gouvernements qui renforcent les réglementations sur les émissions de gaz à effet de serre en vue de la neutralité carbone, il convient de noter que le défi est plus grand pour les fournisseurs de technologies de FA qui doivent fournir des solutions dédiées pour permettre des applications dans ce domaine.
La première étape pour les entreprises de FA est de comprendre que le composant central qui permettra aux véhicules électriques de se démarquer est la prochaine génération de batteries qui devraient offrir de meilleures performances et des temps de charge toujours plus courts. Pour les producteurs de matériaux, le défi consiste à développer des matériaux innovants afin d’augmenter la production à l’échelle, avec des temps et des coûts réduits, une vitesse d’assemblage et des performances accrues. Certains de ces matériaux sont actuellement développés par Evonik :
« Pour augmenter l’autonomie des voitures électriques, une plus grande efficacité des batteries est nécessaire. La prochaine génération de systèmes de refroidissement avec de nouveaux agents de refroidissement est nécessaire. Les solutions monocouches et multicouches développées par Evonik pour les tuyaux du système de refroidissement peuvent répondre à la nécessité d’une plus grande autonomie des batteries et sont performantes avec différents agents de refroidissement. De plus, nous développons un matériau qui répondra à l’une des exigences les plus élevées en matière d’e-mobilité : le retardement de flamme V0 des polymères sans compromettre les propriétés chimiques et physiques des matériaux sur une large plage de température. »
L’objectif ici est d’améliorer les batteries avec un poids et des dimensions réduits, qui ont un contrôle efficace de la température.
Parmi les autres matériaux (toutes technologies confondues) qui joueront un rôle clé dans l’amélioration de l’efficacité et des performances d’une batterie, citons les matériaux polymères de haute technologie, les polycarbonates, les adhésifs et les matériaux thermoplastiques.
Quelle suite pour Evonik ?
Parmi le large éventail de matériaux qui peuvent être exploités en FA, le type de matériau qui offre le plus grand nombre de possibilités est celui des polymères. La capacité de transformer ces matériaux en diverses formes pouvant s’adapter à la variété des processus de fabrication additive sur le marché est non seulement fascinante, mais elle nécessite également des années d’expertise en chimie des polymères. D’après les derniers commentaires de Stoerkle, c’est exactement ce qui rend Evonik exceptionnel :
« Grâce à notre force d’innovation, à nos années d’expertise dans la chimie des polymères pour la FA et à notre solide réseau de partenaires industriels, Evonik sait comment développer et fabriquer des matériaux et mettre à l’échelle des processus pour la production en série. Nous utilisons cette expertise pour le développement à long terme de nouveaux matériaux pour les applications d’impression 3D en série.
Si on considère le segment des poudres, les nouveaux procédés comme ceux développés par Evolve ou Nexa3D nécessitent de nouvelles poudres sur mesure. Pour les technologies STEP et QLS, nous développons conjointement des matériaux prêts à l’emploi à partir de notre portefeuille existant de poudres polymères, comme le polyamide 613 pour les applications à haute température ou notre élastomère INFINAM® TPA pour les pièces flexibles, afin de les adapter à ces processus très intéressants.
Enfin, [tout au long de cette année], vous verrez nos photopolymères apparaître sur un grand nombre de plateformes d’impression majeures. La validation de nos matériaux est axée sur les systèmes d’impression qui promettent de réduire le coût total de possession et de permettre une véritable production industrielle de pièces.
Nous encourageons tout le monde à nous contacter pour développer et mettre en œuvre d’autres applications de la fabrication additive. »
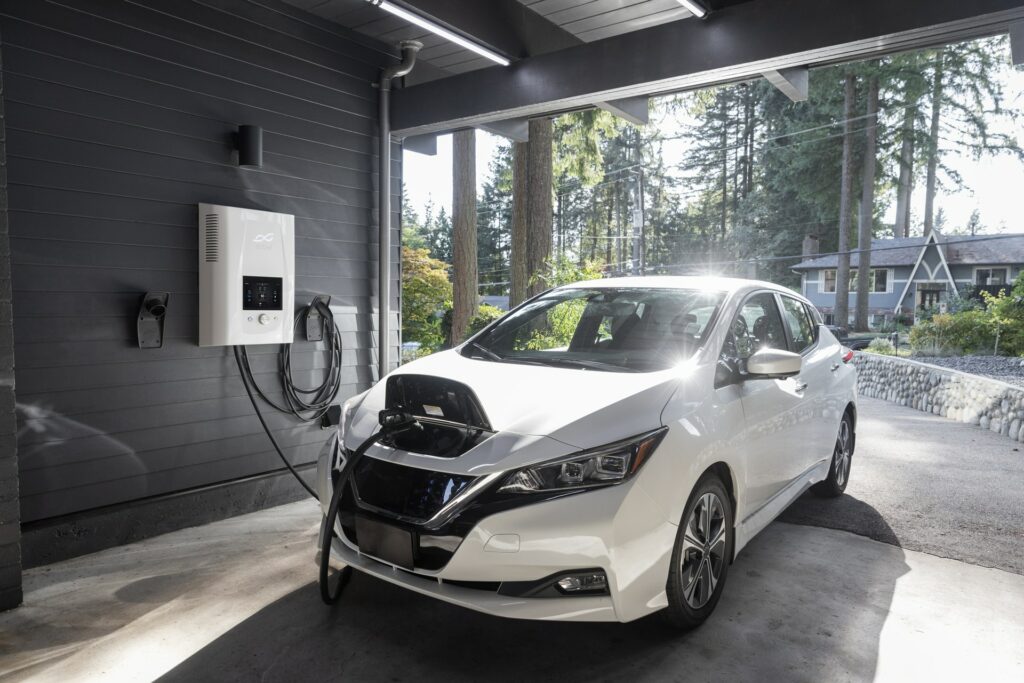
Cet article exclusif a été rédigé en collaboration avec Evonik.
Cet article a été premièrement publié dans le numéro de Mars/Avril de 3D ADEPT Mag. N’oubliez pas que vous pouvez poster gratuitement les offres d’emploi de l’industrie de la FA sur 3D ADEPT Media ou rechercher un emploi via notre tableau d’offres d’emploi. N’hésitez pas à nous suivre sur nos réseaux sociaux et à vous inscrire à notre newsletter hebdomadaire : Facebook, Twitter, LinkedIn & Instagram ! Si vous avez une innovation à partager pour le prochain numéro de notre magazine numérique ou si vous avez un article à faire connaître, n’hésitez pas à nous envoyer un email à contact@3dadept.com